Assigned Protection Factor (APF) is a crucial concept in workplace safety, especially regarding respiratory protection. In environments where airborne contaminants or hazardous substances are present, understanding APFs helps select the right respirator, safeguard workers’ health, and ensure compliance with occupational safety standards.
This article delves into APFs, why they matter, how they’re determined, and how to use them effectively to select the most suitable respiratory protection.
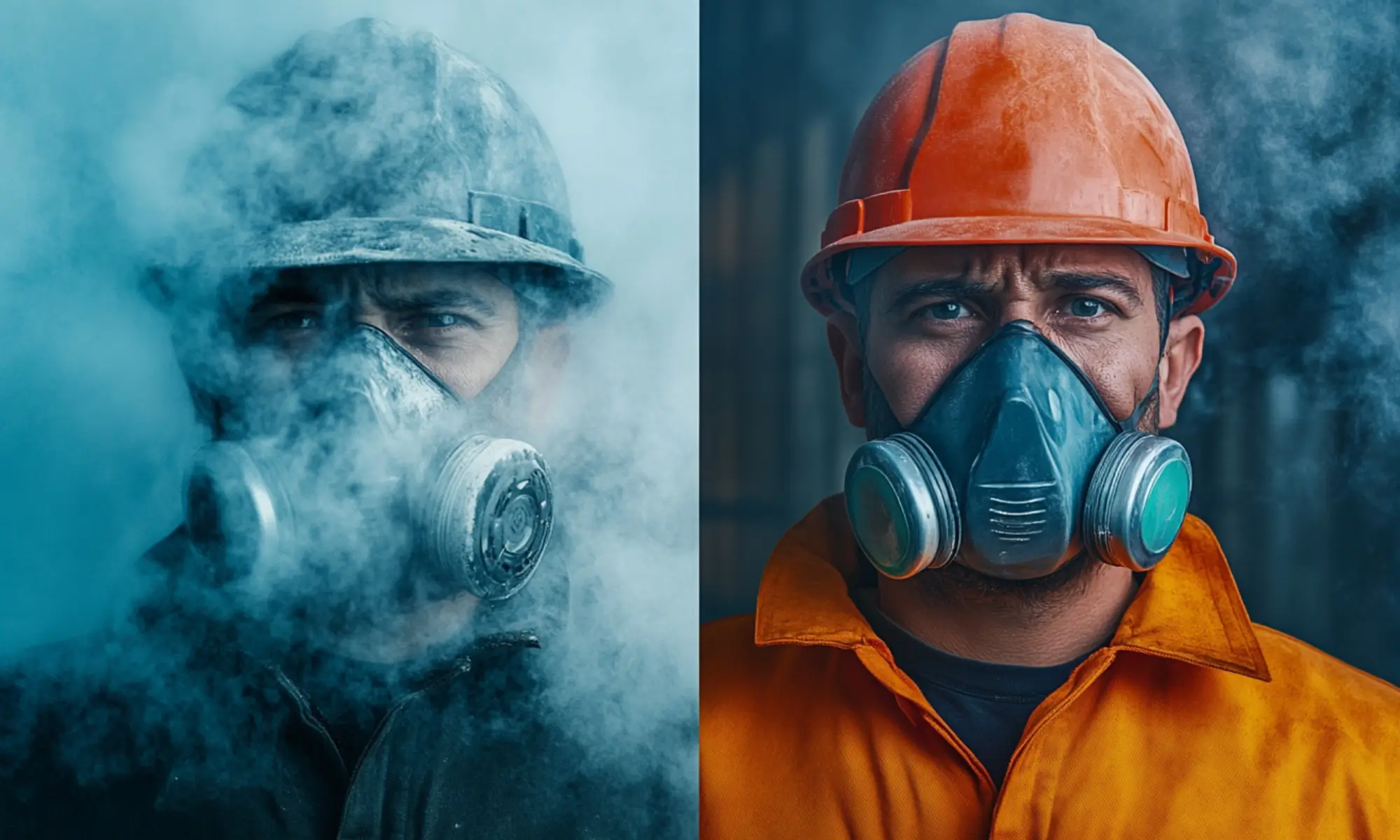
What is the Assigned Protection Factor (APF)?
An Assigned Protection Factor (APF) is a numerical rating that represents the level of respiratory protection a respirator provides to a user. APFs are assigned by regulatory and standards-setting organizations, like the U.S. Occupational Safety and Health Administration (OSHA) and the National Institute for Occupational Safety and Health (NIOSH), to indicate the degree to which a specific respirator can reduce exposure to airborne contaminants.
For example, an APF of 10 means the respirator can reduce exposure to harmful substances to 1/10th of the concentration present in the workplace environment. At the same time, an APF of 1,000 suggests it can reduce exposure to 1/1000th of the ambient contaminant concentration.
APF Formula:
Maximum Use Concentration (MUC)=APF×Permissible Exposure Limit (PEL)
Why is APF Important?
Understanding APFs is essential for the following reasons:
- Worker Protection: APFs are key to selecting respirators that adequately protect against specific workplace hazards.
- Regulatory Compliance: Adhering to APF requirements helps businesses meet OSHA regulations (29 CFR 1910.134) and avoid penalties.
- Risk Management: By using respirators with the correct APF, businesses reduce the risk of occupational illnesses and injuries.
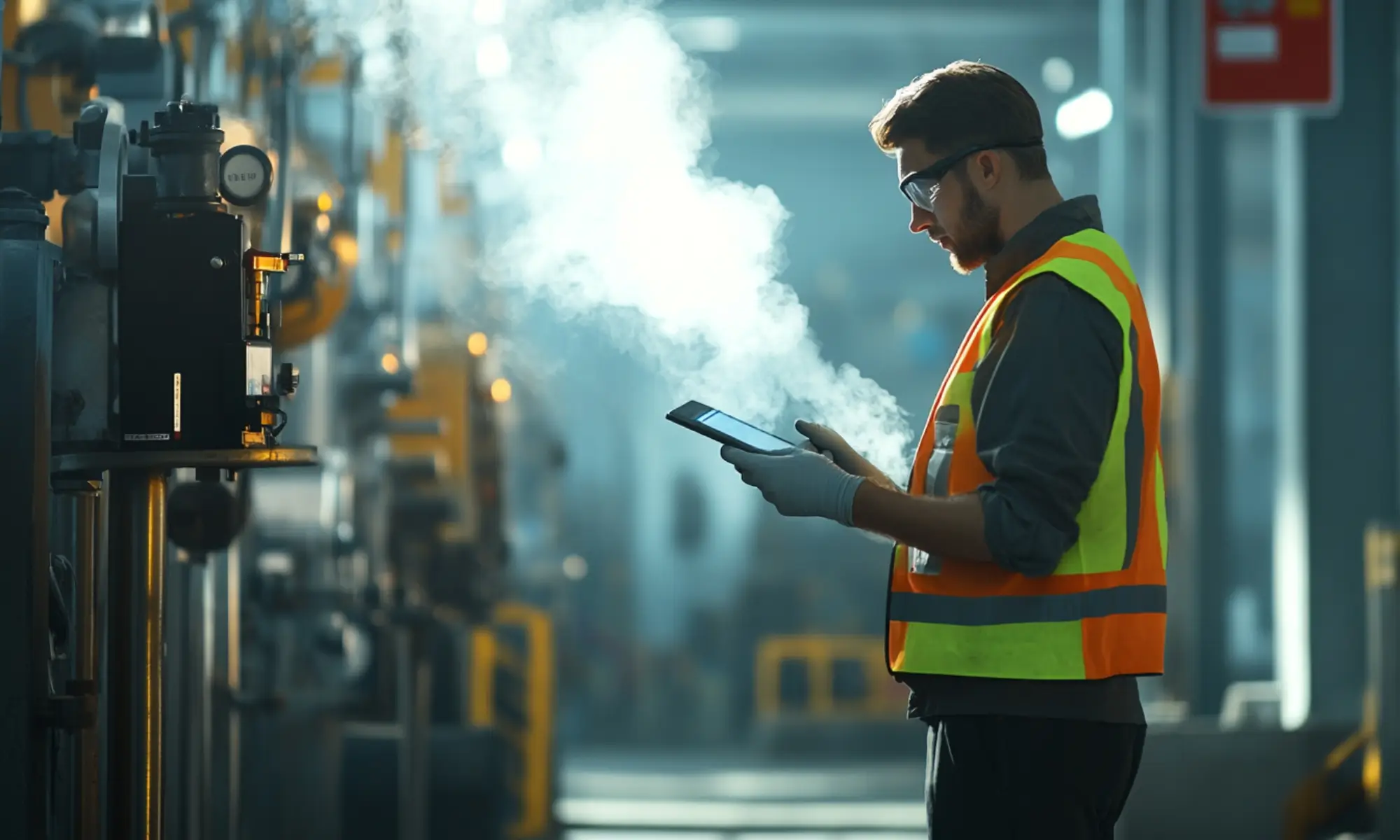
How is APF Determined?
APFs are established through rigorous laboratory and field testing. In the U.S., OSHA requires respirator manufacturers to prove that their products meet or exceed specific protection levels, often through Workplace Protection Factor (WPF) or Simulated Workplace Protection Factor (SWPF) studies.
In these studies, the effectiveness of respirators is measured under controlled conditions and in real-world environments to determine the ratio of the contaminant concentration outside the respirator to the concentration inside it. Based on these tests, OSHA assigns APFs to different types of respirators.
Types of Respirators and Their APFs
Respirators vary widely in their design and capability to protect against airborne contaminants, and each type is assigned an Assigned Protection Factor (APF) by OSHA based on the level of protection it offers. Here’s a breakdown of common respirator types, their APFs, and suitable usage scenarios:
1. Filtering Facepiece Respirator (e.g., N95 mask) – APF of 10
These are single-use respirators, often called “dust masks” or filtering facepiece respirators (FFRs). The N95 is one of the most recognized types, filtering out at least 95% of airborne particles.
- Protection Level: With an APF of 10, they reduce the user’s exposure to contaminants to 1/10th of the concentration in the surrounding air.
- Best For: Low-to-moderate levels of airborne contaminants, especially in non-life-threatening situations. They’re commonly used in healthcare and light industrial applications.
2. Half Mask Respirator (Elastomeric Facepiece) – APF of 10
These are reusable respirators with a flexible elastomeric facepiece designed to form a seal around the nose and mouth. They use replaceable filters or cartridges to purify air.
- Protection Level: Similar to filtering facepiece respirators, they also have an APF of 10.
- Best For: Environments with similar exposure levels as filtering facepiece respirators but where a more durable, reusable option is preferred. These respirators are often used in construction, painting, and manufacturing.
3. Full-Facepiece Respirator (Air-Purifying) – APF of 50
Full-face respirators cover the entire face, including eyes, nose, and mouth, providing both respiratory and eye protection. They use replaceable filters or cartridges, which may be for particulate, chemical, or combined protection.
- Protection Level: With an APF of 50, they are more protective than half-mask or filtering facepiece respirators, reducing contaminant exposure to 1/50th of the ambient concentration.
- Best For: Moderate to high levels of airborne contaminants, where eye protection is also needed. Full facepiece respirators are suitable for tasks in industries like chemical handling, pharmaceutical production, and pesticide application.
4. Powered Air-Purifying Respirators (PAPR) – APF of 25-1,000
PAPRs use a battery-powered fan to pull air through a filter, supplying clean air to the wearer’s face or head. They come in various configurations, including loose hoods, helmets, and tight-fitting facepieces.
- Protection Level: The APF of PAPRs varies widely, from 25 for loose-fitting facepieces to 1,000 for certain helmet or hood configurations.
- Best For: Situations requiring extended wear time or a higher comfort level. They are common in healthcare settings, laboratories, and industrial environments with a range of contaminants, including asbestos, silica, and biological hazards.
5. Supplied-Air Respirators (SAR) – APF of up to 10,000
SARs deliver clean air from an external source, such as an air compressor, through a hose to the user’s facepiece. They are used in both continuous flow and positive-pressure modes, with configurations like full-face masks and hoods.
- Protection Level: With an APF of up to 10,000, they offer the highest level of protection among respirators.
- Best For: Extremely hazardous environments or confined spaces where contaminants are at levels that exceed the protective capacity of air-purifying respirators. SARs are often used in environments with toxic gases or vapors, and in rescue or emergency response situations.
Each respirator type provides varying degrees of protection, and selecting the right APF level ensures safety based on the contaminant concentration in the work environment. Proper fit testing, user training, and following a respiratory protection program are also essential to achieving the designated APF for each respirator.
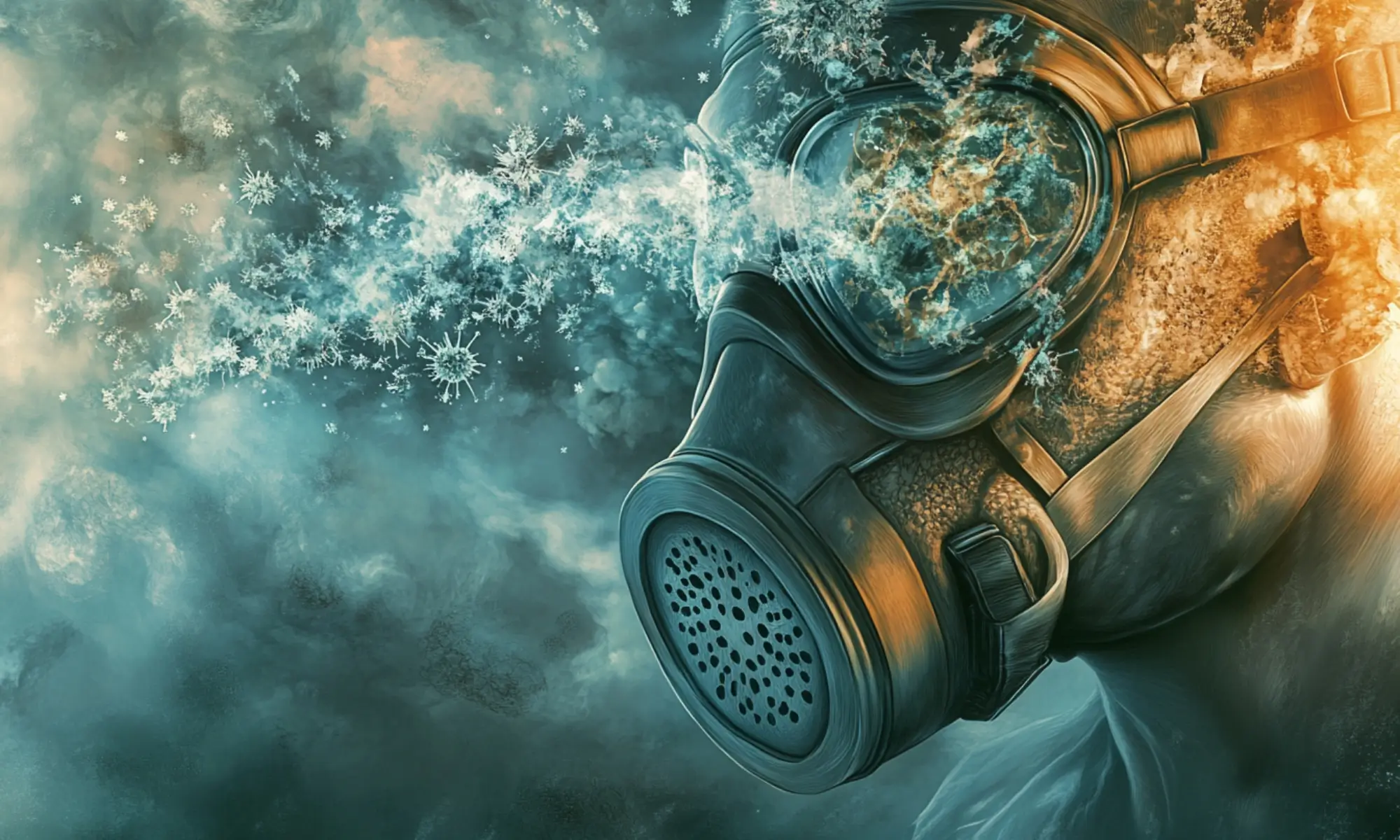
How to Use APF for Selecting Respiratory Protection
Selecting the right respiratory protection using the Assigned Protection Factor (APF) requires understanding the level of contamination, calculating safe limits, and ensuring a proper fit. Here’s a step-by-step guide to effectively use APF when choosing respirators:
Step 1: Assess the Workplace Hazard
Before choosing a respirator, it’s essential to understand the contaminants present in the work environment:
- Identify the contaminants: Determine the specific types of airborne hazards, such as dust, fumes, gases, or vapors.
- Measure concentration levels: Check the concentration of each contaminant in the air, often using air quality assessments or monitoring equipment.
- Review Safety Data Sheets (SDS): SDS sheets provide valuable information on safe exposure levels and potential health hazards for chemical contaminants.
This assessment helps establish the level of protection needed and sets a foundation for choosing the appropriate APF.
Step 2: Calculate the Maximum Use Concentration (MUC)
Once workplace hazards and contaminants are identified, the APF calculates maximum use concentration (MUC). MUC is the highest level of contamination a respirator can handle while protecting the user.
The formula to calculate MUC is:
MUC=APF×Permissible Exposure Limit (PEL)
- APF: The assigned protection factor of the respirator is being considered.
- PEL: The OSHA-set Permissible Exposure Limit for the contaminant.
Example Calculation:
Suppose the APF of a respirator is 50, and the PEL of a contaminant is 10 parts per million (ppm). The MUC would be:
50×10=500 ppm
This calculation means that the chosen respirator (with an APF of 50) would suit environments where the contaminant concentration does not exceed 500 ppm.
Step 3: Consider Fit Testing and Program Requirements
Even with the right APF and MUC calculations, it’s critical to ensure that the respirator is correctly fitted and maintained:
- Fit Testing: Conduct fit testing for each user to confirm that the respirator forms a proper seal on the wearer’s face. This is essential for tight-fitting respirators, as leaks can compromise the protection level.
- User Training: Train workers on correctly wearing, adjusting, and caring for their respirators. They should also understand the hazards and how their respirator protects them.
- Maintenance and Compliance: Regularly inspect, clean, and replace respirator components as needed to maintain their effectiveness. A comprehensive respiratory protection program is essential to achieving the APF rating in practice and ensuring consistent protection.
By following these steps, you can effectively select and use respirators that meet the necessary APF standards, ensuring worker safety in environments with airborne contaminants.
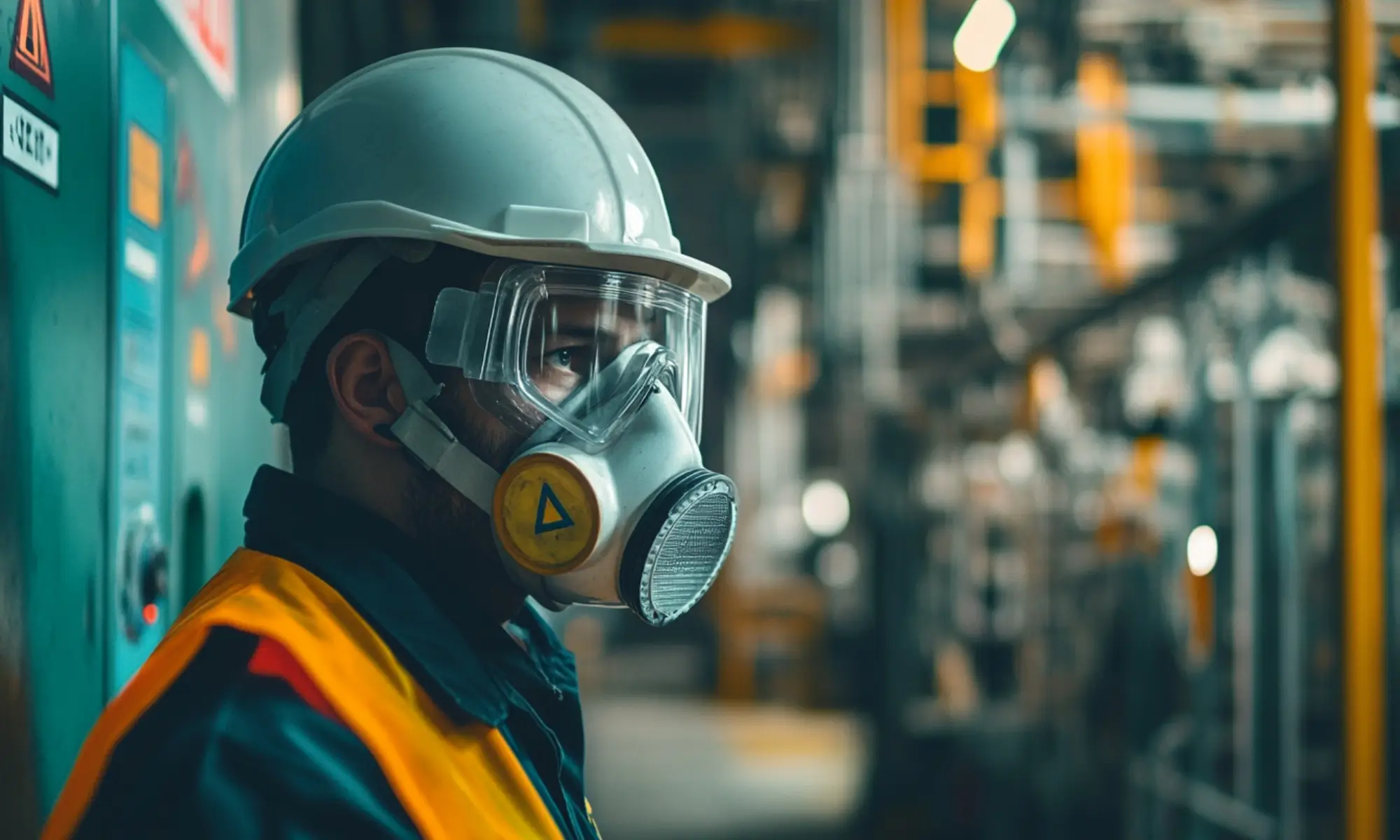
APF Limitations: What You Need to Know
Assigned Protection Factors (APFs) are critical for choosing respirators that offer the right level of protection. However, APFs have certain limitations, and understanding these is essential to ensure safety and effectiveness. Here are some key APF limitations to be aware of:
1. Proper Fit and Seal Are Essential
- The APF of a respirator assumes a tight, well-fitted seal. For tight-fitting respirators, facial hair or improper adjustments can compromise the seal, leading to leaks that reduce protection.
- Fit testing is crucial for each user to ensure the respirator achieves the expected APF. Without a proper fit, the respirator will not provide the intended level of protection.
2. Respirator Condition and Maintenance
- The APF of a respirator is valid only if the device is in good working condition. Damaged or improperly maintained respirators may have lower protection levels.
- Regular inspections, cleaning, and timely replacement of filters or cartridges are essential to maintain the respirator’s protective capabilities.
3. User Training and Proper Usage
- APFs assume that users are trained to correctly wear and use the respirator. Incorrect donning or use can significantly reduce protection.
- Training programs should cover correct donning, doffing, adjustment, and understanding of limitations for each respirator type.
4. APFs Do Not Apply in IDLH Environments
- APFs are generally not applicable in Immediately Dangerous to Life or Health (IDLH) environments. Only specific respirators, like Self-Contained Breathing Apparatus (SCBA), are rated for IDLH conditions.
- In these high-risk areas, the APF of standard air-purifying respirators may not be sufficient to provide adequate protection.
5. Assumption of Full Wear Time
- APFs assume the respirator is worn for the entire duration of exposure to hazardous contaminants. Removing or adjusting the respirator during exposure periods can allow contaminants to enter, reducing overall protection.
- Effective protection relies on continuous wear during all periods of exposure.
6. Environmental and Operational Factors
- APFs are tested under specific conditions and may not fully account for challenging work environments, such as extreme heat, humidity, or high physical activity, which could affect respirator performance.
- Companies should assess these factors and may need additional safety measures or alternative respirators for difficult conditions.
While APFs provide valuable guidance on the protection levels of different respirators, these limitations highlight the importance of proper fit, maintenance, training, and situational assessment. Addressing these limitations ensures that respirators meet their expected APF levels and effectively protect workers in hazardous environments.
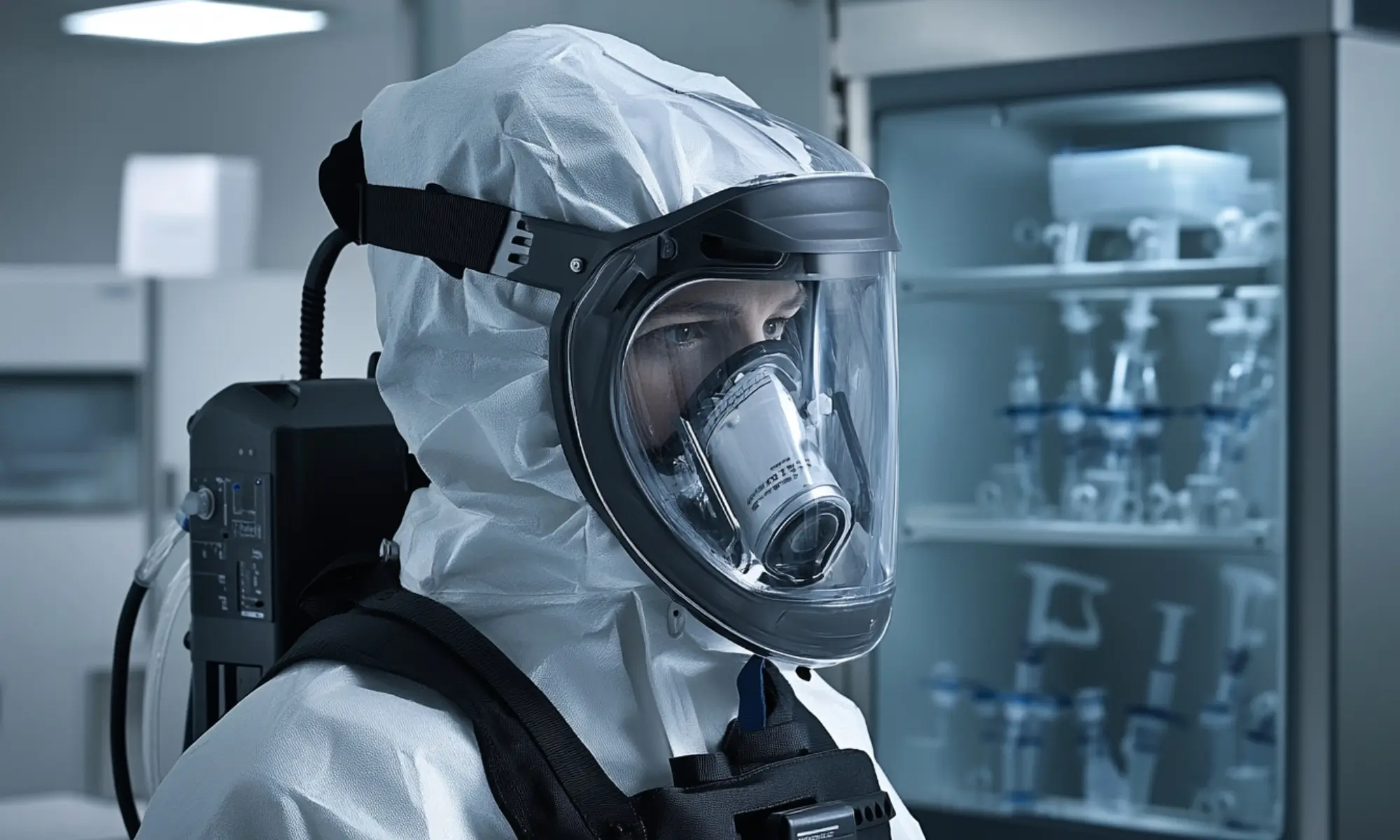
Global Variations in APF Standards
Assigned Protection Factor (APF) standards vary globally due to differences in regulatory bodies, testing methods, and workplace safety approaches. These variations can affect the selection and use of respiratory protection across different regions, especially for multinational companies. Here’s an overview of how APF standards differ worldwide and why these differences matter.
1. Regulatory Authorities and Standards
- In the United States, APFs are defined by the Occupational Safety and Health Administration (OSHA) under standard 29 CFR 1910.134. APF values in the U.S. are based on Workplace Protection Factor (WPF) and Simulated Workplace Protection Factor (SWPF) studies that measure the level of protection under real-world conditions.
- In Europe, APFs follow standards the European Committee for Standardization (CEN) set, specifically EN 529:2005. These standards emphasize Total Inward Leakage (TIL) and Nominal Protection Factor (NPF) testing in laboratory settings, focusing on ideal conditions.
Because these standards are set by different bodies, the APF values for similar respirators may differ across regions. OSHA often sets slightly higher APFs based on practical workplace testing.
2. Testing Conditions and Methods
- U.S. APF Standards: In the U.S., APFs are based on WPF and SWPF studies that simulate real-world use in various work environments. These studies include factors like worker movement, breathing rates, and real contaminant exposure, which contribute to the practical effectiveness of a respirator.
- European APF Standards: European APFs are more laboratory-based, where respirators are tested under controlled conditions using TIL measurements. These tests assess how well respirators perform in a static, controlled setting rather than dynamic, real-world environments.
This difference in testing approach means that U.S. APFs are typically conservative for practical use, while European APFs may reflect ideal protection in a controlled setting.
3. Differences in APF Values by Respirator Type
- Filtering Facepieces (e.g., N95 in the U.S. and FFP2 in Europe): In the U.S., N95 masks have an APF of 10, while in Europe, FFP2 masks with similar filtration rates also typically receive an APF of 10. However, there can be minor differences depending on specific filter requirements in each region.
- Full-facepiece respirators: In the U.S., a full-facepiece respirator has an APF of 50, whereas in Europe, equivalent respirators’ APFs may vary based on the filter type, with an APF of 100 or more in some countries.
- Powered Air-Purifying Respirators (PAPRs): U.S. APFs for PAPRs range from 25 to 1,000 based on the respirator design, while European APFs for similar models may be capped lower. In Europe, PAPRs are classified into TH and TM categories (for loose and tight-fitting designs), each with specific APF limits.
4. Country-Specific Variations within Europe
- Within the European Union, member countries sometimes have specific national guidelines that deviate slightly from EN 529:2005, leading to further variations. For example, the United Kingdom’s Health and Safety Executive (HSE) often aligns APFs with British Standards Institute (BSI) guidelines, which may be lower or higher than the general EN values.
5. Challenges for Multinational Organizations
- For multinational companies, these differences in APF standards pose challenges when establishing respiratory protection programs that need to be consistent yet compliant in multiple regions. Companies must balance the highest APF required across all locations with local regulatory requirements to ensure safety and compliance.
6. Adapting to Regional Standards
- In countries without specific APF regulations, organizations often adopt the standards from OSHA or EN 529:2005. Many choose to use the more conservative U.S. APFs as a baseline for higher assurance of worker safety, especially in high-risk industries.
Global variations in APF standards reflect differences in regulatory approaches and testing conditions. Understanding these differences helps companies implement effective respiratory protection programs aligning with local requirements and international safety best practices. Adopting the highest applicable APF standards for companies operating across regions can ensure consistent protection for workers worldwide.
Summary
Assigned Protection Factors (APFs) are a cornerstone of respiratory protection, guiding the selection of suitable respirators based on the level of protection required in the workplace. By understanding APFs, employers and safety managers can make informed decisions to enhance worker safety and comply with regulatory standards. Whether choosing a simple N95 respirator or an advanced SCBA, the right APF ensures that workers have the necessary protection against airborne hazards, helping maintain a safer and healthier work environment.