Machines enhance productivity and efficiency in the rapidly evolving manufacturing and industrial operations world. However, with these machines’ immense power and complexity comes an equally significant responsibility to ensure the safety of the human workforce that operates and interacts with them. Every year, countless incidents involving machinery result in injuries and, in some cases, fatalities, highlighting the critical importance of implementing effective safety measures. Machine Safeguarding Requirements is an essential read for anyone involved in manufacturing, processing, or any industry that utilizes machinery.
This comprehensive guide provides invaluable insights into the principles and practices fundamental to safeguarding employees and equipment. We will explore various topics, from the significance of risk assessments to the intricacies of various safety devices. Whether you’re an experienced plant manager, a safety officer, or someone new to the industry, understanding and implementing machine safeguarding requirements is a paramount investment in the well-being of your team and the sustainable success of your operations.
Machine Safeguarding Requirements
Machine safeguarding requirements are designed to protect workers from hazards industrial machinery poses. Such hazards include crushing, shearing, amputations, abrasions, and others. Different countries and industries may have specific requirements, but some general principles apply broadly.
In the United States, for example, the Occupational Safety and Health Administration (OSHA) sets standards for machine safeguarding. Similarly, Europe has European Union directives like the Machinery Directive. It is important to know the requirements in the specific country and industry in which you operate.
Here are some general principles that are widely applicable:
1. Risk Assessment
Risk assessment in the context of machinery involves a systematic approach to evaluate and identify potential hazards that might be present during the machine’s operation. Risk assessment aims to predict the likelihood of incidents and the severity of potential injuries by carefully analyzing the machinery’s functionality, its designed tasks, and the surrounding environment. By pinpointing areas and operations of machinery that present risks, appropriate preventive and protective measures can be implemented, thus contributing to a safer work environment.
2. Machine Guarding
This principle involves placing physical barriers or guards around machinery’s moving or hazardous parts.
- Fixed guards are permanent and are not dependent on the machine’s operation.
- Interlocked guards are connected to the machine’s power source, so the machine will automatically shut down when the guard is opened or removed.
- Adjustable guards can be adjusted manually to accommodate different sizes of material.
- Self-adjusting guards automatically adjust to the size of the material entering the danger area.
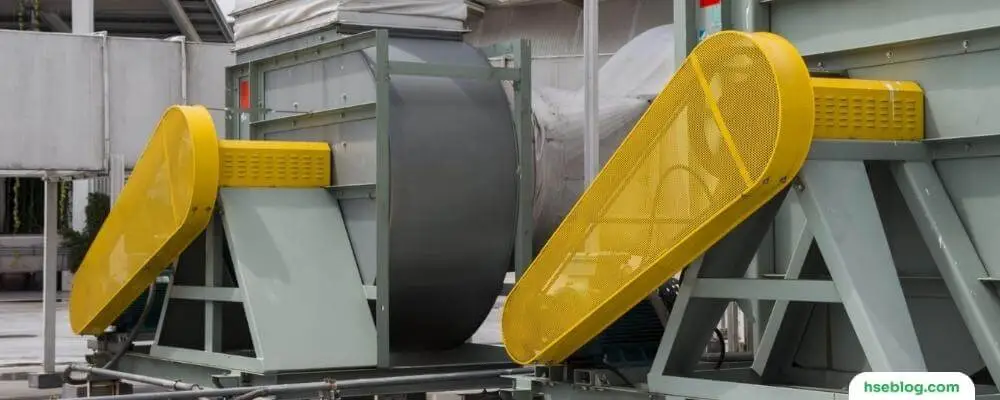
3. Safe Work Procedures and Training
Safe work procedures and training are fundamental to ensuring that machinery is operated and maintained safely. Developing safe work procedures involves creating comprehensive, step-by-step guidelines based on the manufacturer’s instructions and the findings from risk assessments. These procedures outline the best practices for operating machinery and often include information on startup and shutdown processes, handling materials, and responding to various operating conditions.
Equally crucial is the training aspect, where employees are educated and continuously trained on these procedures and using personal protective equipment and emergency response protocols. This combination of knowledge and practical skill-building is vital in fostering a safety-conscious culture, reducing accidents, and promoting efficient operations.
4. Lockout/Tagout Procedures
Lockout/Tagout procedures are critical safety measures to prevent machinery’s accidental or unauthorized operation, particularly during maintenance or servicing when unexpected startups or energy releases can be dangerous. Lockout procedures involve using physical devices such as locks or blocking devices to keep machinery safe and non-operational.
Tagout procedures involve attaching a warning tag or sign to an energy-isolating device, clearly indicating that the machinery should not be operated until the tag is removed by authorized personnel. The combination of lockout and tagout procedures creates a multi-layered safety approach, ensuring that those working on or near the machinery are not exposed to unexpected activation or energy discharge that could lead to severe injuries or fatalities.
5. Emergency Stop Controls
Emergency Stop Controls are essential safety features on machinery that allow for the immediate cessation of operations in the event of an emergency. These controls are usually red buttons or switches prominently labeled and strategically placed within easy reach of machine operators. They override all other controls when activated, bringing the machine to a safe stop.
In situations where there is an imminent risk of injury to personnel or damage to the equipment or materials, the ability to swiftly halt the machine’s operations through Emergency Stop Controls is a vital safety measure. These controls are particularly important in cases where seconds count, such as entanglement in moving parts. This jam could cause mechanical failure or any other sudden and unforeseen hazardous situation.
6. Regular Inspection and Maintenance
Regular Inspection and Maintenance of machinery is a proactive approach to ensuring equipment longevity and safe operation. Through periodic inspections, potential issues such as wear and tear, misalignment, or parts malfunction can be identified early before they escalate into major problems. Maintenance activities might include replacing worn-out components, lubricating moving parts, and calibrating sensors.
In addition, it is imperative to check that all the guards are securely in place and that safety devices such as emergency stops or interlocks are functioning properly. Organizations can prevent accidents and injuries by maintaining machinery in optimal condition, improving productivity, and reducing downtime. The inspection and maintenance schedules must comply with the manufacturer’s recommendations and regulatory requirements.
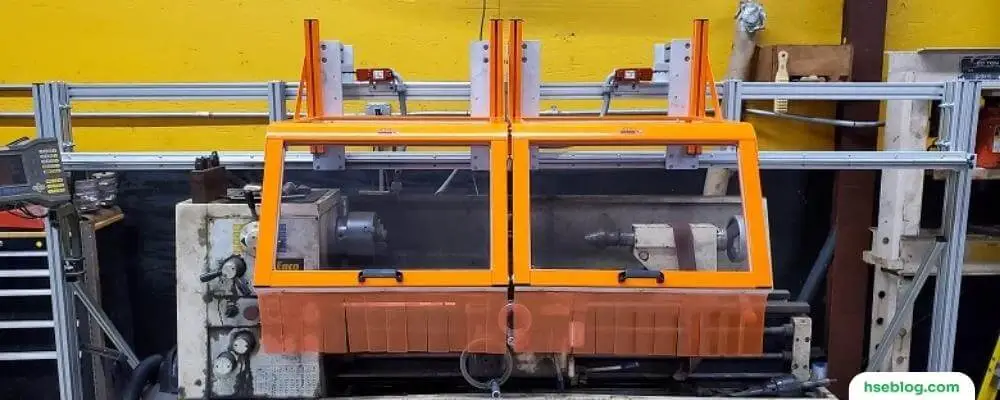
7. Safety Devices
Safety Devices are specialized equipment integrated into machinery to provide additional protection, minimizing the risks of accidents or injuries. These devices often rely on sensors and automatic controls. For instance:
- Light Curtains: These optoelectronic devices create an invisible barrier of light. When this barrier is broken, it signals that an object or person is in a hazardous area, causing the machine to immediately stop or slow down.
- Safety Mats: Placed around the perimeter of machinery, safety mats are pressure-sensitive safety surfaces that detect a person’s weight. If someone steps onto the mat, it triggers an immediate stoppage of the machine to prevent the person from accessing dangerous moving parts.
- Two-Hand Controls: Requiring an operator to use both hands to operate the machine ensures that neither hand can be in a danger zone during machine operation. This is especially useful in operations such as pressing or stamping with a risk of a hand injury.
- Presence-Sensing Devices: Similar to light curtains, these devices detect the presence of a person or object in a hazardous area near machinery. They use technologies such as lasers, infrared, or ultrasonic waves and will halt the machine if an intrusion into the danger zone is detected.
These safety devices are integral components in machine safeguarding, and their proper implementation and maintenance are essential for creating a safe working environment. They are especially crucial when conventional guards impede functionality or visibility, or additional safety layers are necessary due to the high risks involved.
8. Ergonomics
Ergonomics is the science of designing and arranging workspaces and machinery so that they fit the people who use them. By tailoring the design of equipment, controls, and the workspace layout to the capabilities and limitations of workers, ergonomics aims to minimize physical strain, fatigue, and the risk of musculoskeletal disorders. Elements of ergonomics include ensuring adjustable chairs and work surfaces, arranging controls within comfortable reach, proper lighting, and implementing practices to reduce repetitive motions.
9. Clearance and Workspaces
This principle ensures sufficient space around machinery for safe operation and maintenance. Adequate clearance is necessary to prevent workers from being pinned between equipment and walls or other objects and to ensure they can move freely and safely. This involves considering the range of motion of moving parts, the space needed for material handling, operator movement, and maintenance activities.
10. Safety Signage and Instructions
Safety signs and instructions are crucial for communicating hazards and safe practices. Signage should be clear, easily understandable, and prominently displayed. It can include warnings of specific hazards, mandatory actions such as using personal protective equipment, and prohibitions such as not entering an area. Instructions may include safe operating procedures, emergency response protocols, and maintenance guidelines.
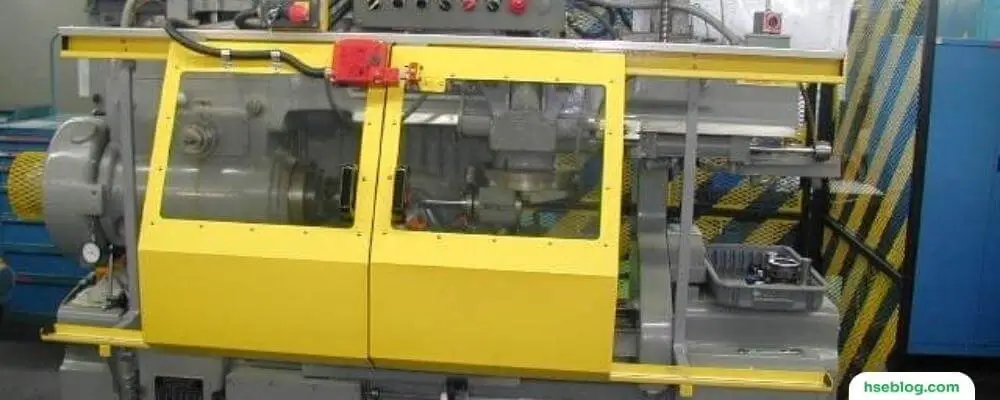
11. Compliance with Standards and Regulations
Adhering to relevant safety standards and regulations is fundamental to ensuring machinery safety. This involves complying with design criteria, safety features, and procedures stipulated by governing bodies and standards organizations such as OSHA, ANSI, or ISO. Staying up-to-date with regulatory requirements is important as they can evolve over time.
12. Reporting and Documentation
Proper record-keeping is an essential component of safety management. This involves keeping a log of machinery inspections, maintenance activities, training records, and incident reports. This documentation helps monitor the effectiveness of safety measures, identify trends or areas that need improvement, and demonstrate compliance with regulatory requirements. It’s also essential for informing risk assessments and safety training programs.
Conclusion
In conclusion, the basic requirement for machine guarding is to ensure the safety and well-being of the workforce operating or working near machinery. This entails a multifaceted approach that includes conducting thorough risk assessments to identify potential hazards, implementing physical guards and safety devices to minimize risks, and developing clear work procedures.
Ergonomic considerations must be considered to reduce physical strain and optimize worker efficiency, while sufficient clearance and workspace are necessary to enable safe operation and maintenance. Clear signage and instructions are essential for communication, and rigorous compliance with established standards and regulations is indispensable.
Moreover, comprehensive training for the workforce on safe operating procedures, coupled with an emphasis on reporting and proper documentation, solidifies the foundation of a robust machine-safeguarding program. Through diligent attention to these key principles, organizations can create a safety culture that protects employees’ well-being and enhances operational efficiency and productivity.