Confined spaces present unique challenges and hazards that require specialized equipment to ensure workers’ safety and efficiency. Whether you’re dealing with air ducts, manholes, tanks, or tunnels, understanding and equipping yourself with the right tools is crucial. This comprehensive guide delves into the essential confined space equipment every job must have, ensuring compliance with OSHA standards and safeguarding your workforce.
Understanding Confined Spaces
A confined space is any enclosed area not designed for continuous human occupancy but large enough for a worker to enter and perform specialized tasks. Common examples include:
- Air Ducts
- Manholes
- Tanks
- Tunnels
- Pipelines
- Silos
- Storage Containers
According to the Occupational Safety and Health Administration (OSHA), a space is officially classified as a confined space if it meets three criteria:
- Limited Entry and Exit: The space has restricted points for entering and exiting.
- Not Intended for Continuous Occupancy: The area is not designed for people to live or work there continuously.
- Sufficient Size: The space is large enough for one person to enter and perform work.
Understanding these criteria helps identify and classify confined spaces accurately, ensuring appropriate safety measures are in place.
Dangers of Confined Space Entry
Working within a confined space exposes workers to various hazards. Recognizing these dangers is the first step in mitigating risks. Key hazards include:
1. Atmospheric Hazards
- Oxygen Deficiency or Enrichment: Low or high oxygen levels can be fatal.
- Toxic Gases: Presence of harmful gases like hydrogen sulfide or carbon monoxide.
- Mists and Fumes: Hazardous airborne substances that can impair health.
2. Chemical & Biological Exposure
- Dangerous Chemicals: Exposure to harmful substances through skin contact, ingestion, or inhalation.
- Bacteria and Pathogens: Risk of infection from biological contaminants.
3. Engulfment
- Liquid or Solid Materials: Workers can be engulfed, covered, or suffocated by materials stored in hoppers or silos.
4. Fire Hazards
- Flammable Gases and Dusts: Increased risk of fire or explosion.
- Combustible Atmospheres: Conditions that can ignite easily.
5. Mechanical & Physical Hazards
- Noise, Heat, and Vibration: Adverse environmental conditions affecting worker health.
- Structural Hazards: Risks from sloping walls, falling debris, or collapsing structures.
- Moving Parts of Equipment: Potential for entanglement, slips, or falls.
6. Rescue Hazards
- Difficult Rescues: High risk of injury or fatalities among would-be rescuers, accounting for 60% of confined space fatalities (Canadian Center for Occupational Health and Safety).
Essential Confined Space Equipment
Specific equipment is indispensable to combat the myriad hazards associated with confined spaces. Here’s a breakdown of must-have confined space tools for every job:
1. Communication Equipment
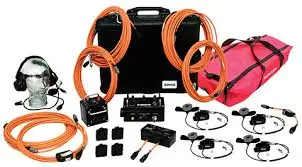
Effective communication between workers inside and outside the confined space is vital for safety and coordination.
- Confined Space Radios: Ensure clear communication even in restricted areas.
- Microphones and Speakers: Facilitate two-way communication.
- Headsets and Talk Boxes: Provide hands-free communication options.
- Head Harnesses and Carrying Cases: Ensure equipment is easily accessible and secure.
- Communication System Cables: Maintain reliable connections.
2. Descent, Rescue, and Retrieval Systems

Safe entry and exit are critical, especially during emergencies.
- Fall Arresters and Full Body Harnesses: Prevent falls and provide safety during entry and exit.
- Hoists, Winches, and Retractable Devices: Assist in lowering and raising workers safely.
- Pulleys and Rescue Systems: Enable efficient rescue operations.
- Tripods and Steadiers: Provide stable points for raising and lowering workers and equipment.
3. Medical Equipment
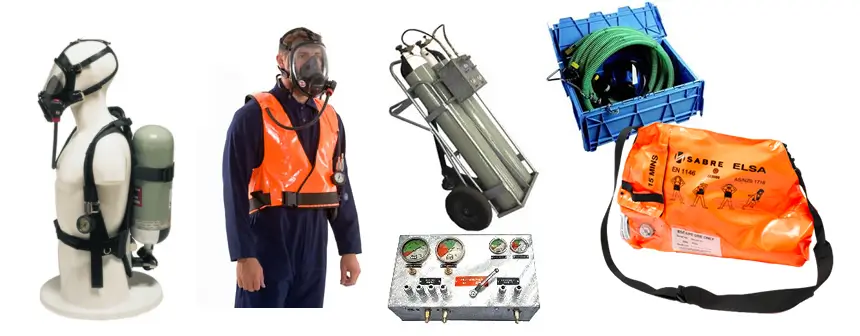
Preparedness for medical emergencies can save lives.
- Breathing Apparatuses: Provide emergency air supply.
- First Aid Boxes: Essential for treating injuries on-site.
- Resuscitators and Stretchers: Facilitate emergency medical response and patient transport.
4. Meters and Monitors
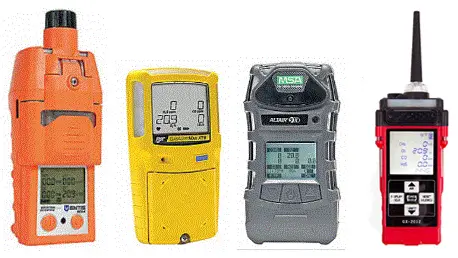
Monitoring the environment ensures safety by detecting hazardous conditions early.
- Toxic Gas Meters: Detect harmful gas concentrations.
- Oxygen Monitors: Ensure safe oxygen levels.
- Chemical Scanners: Identify specific chemical hazards in the air.
5. Personal Protective Equipment (PPE)
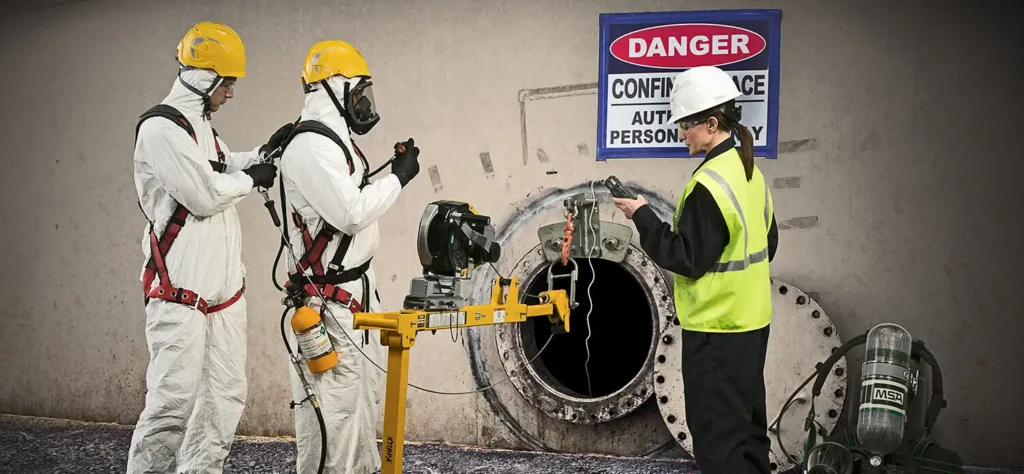
PPE is fundamental in protecting workers from various hazards.
- Appropriate Clothing: Shields against chemical and biological exposure.
- Eye and Face Protection: Guards against splashes and airborne particles.
- Gloves: Protect hands from contaminants and physical hazards.
- Hard Hats and Foot Protection: Prevent injuries from falling debris and equipment.
- Flashlights and Headlamps: Ensure visibility in dark or low-light environments.
6. Signage and Permits
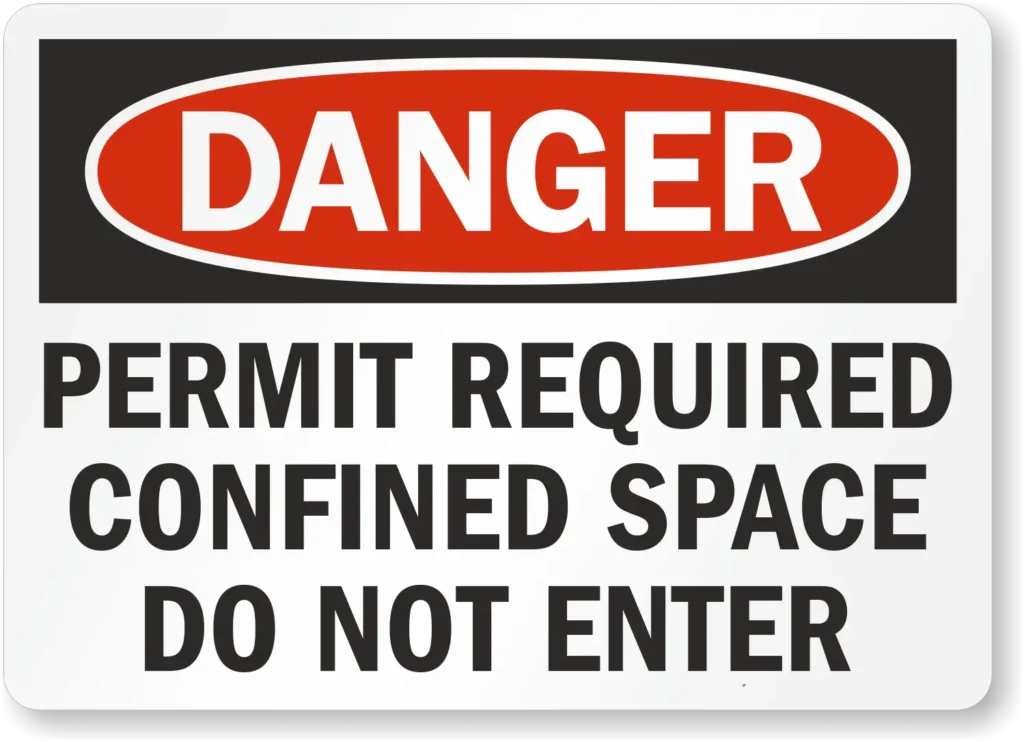
Clear signage and proper permits are essential for maintaining safety protocols.
- Safety Signs: Indicate confined spaces and associated hazards with clear, visible messaging.
- Confined Space Permits: Document and control the conditions for entry, including purpose, duration, authorized personnel, atmospheric conditions, and hazard elimination measures.
- Permit Holder Signs: Inform workers about permit locations and entry requirements.
7. Ventilation Equipment
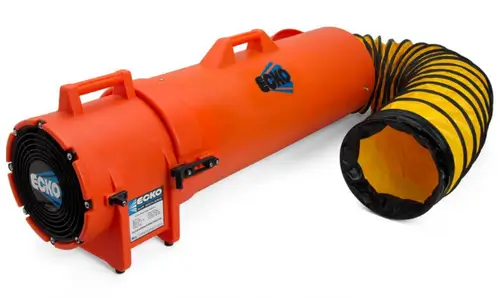
Proper ventilation mitigates atmospheric hazards by ensuring a safe, breathable environment.
- Blowers and Fans: Provide fresh air circulation.
- Ducts and Ventilation Tubes: Direct airflow into and out of confined spaces to remove contaminants.
8. Data Collection and Inspection Tools
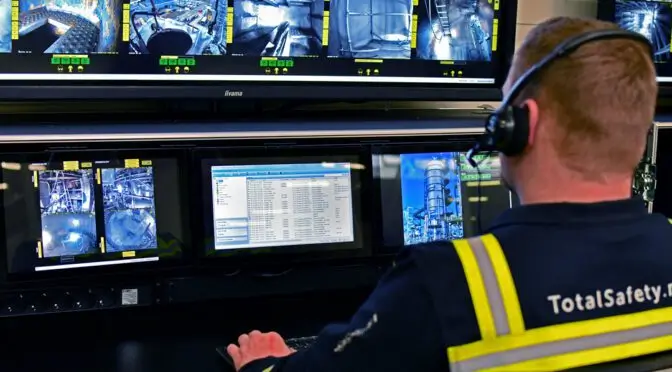
Advanced tools facilitate safe and efficient inspections and repairs without extensive human entry.
- Camera-on-a-Stick: Cost-effective solution for visual inspections.
- Crawler Robots: Ideal for inspecting long, consistent geometries like pipes and ducts.
- Snake Robots: Maneuverable tools for accessing tight or complex areas within confined spaces.
- Climber Robots: Utilize magnets to navigate vertical surfaces in metallic confined spaces.
- Drones (UAVs): Perform inspections without human entry, avoiding exposure to hazardous conditions.
Permit-Required vs. Non-Permit Confined Spaces
Permit-Required Confined Spaces
These spaces meet all three OSHA criteria and contain additional hazards such as toxic atmospheres, engulfment risks, or other significant dangers. Entry into permit-required confined spaces necessitates:
- Confined Space Permits: Ensure safety through detailed entry protocols.
- Qualified Personnel: Workers must complete safety checklists before entry.
- Continuous Monitoring: Regular checks on atmospheric conditions and worker safety.
Non-Permit Confined Spaces
These spaces do not meet all OSHA criteria or contain significant hazards, thus requiring less stringent safety measures. Examples include crawl spaces under houses, equipment closets, and ventilated tunnels. While potentially hazardous, these areas do not require permit systems but should adhere to basic safety protocols.
Implementing Confined Space Safety
Ensuring the safety of workers in confined spaces involves more than just having the right equipment. It requires:
- Comprehensive Training: Workers must be trained in using confined space equipment and emergency procedures.
- Regular Inspections: Equipment and confined spaces should be regularly inspected to ensure compliance and functionality.
- Clear Communication: Maintain open lines of communication between workers inside and outside the confined space.
- Emergency Preparedness: Develop and practice rescue plans to respond swiftly to incidents.
Conclusion
Confined spaces pose significant risks, but these dangers can be effectively managed with the right equipment and safety protocols. From communication tools and PPE to advanced robotic inspection devices, having the must-have confined space equipment for every job ensures worker safety and operational efficiency. Adhering to OSHA guidelines and continuously updating safety measures will help create a secure working environment in even the most challenging confined spaces.