Forklift accidents form an alarming part of industrial safety mishaps, often resulting in dire consequences from injury to loss of life and substantial property damage. Understanding the reasons behind these accidents and learning how to prevent them is not just a necessity but an obligation for those operating in industries where forklifts are commonplace.
In this blog post, we delve deep into the 12 most common causes of forklift accidents and, more importantly, share strategies to avoid them. From improper training to lack of maintenance, we’ll explore these hazards individually and provide practical solutions to enhance safety and efficiency within your operations.
Our objective is simple: to empower you and your team with the knowledge needed to foster a safer, more productive workplace. So, let’s equip ourselves with the insights that could prevent the next forklift accident, safeguarding people’s lives and your company’s assets.
Forklift Accidents: 12 Common Causes & Control Measures
Forklift accidents can result in serious injuries and even fatalities in the workplace. Understanding the common causes of forklift accidents and implementing control measures to prevent them is important. Here are 12 common causes of forklift accidents and some control measures to mitigate the risks:
1. Insufficient Training
The crux of many forklift accidents is insufficient or improper training. Operating a forklift is not as simple as driving a car; it demands a specialized skill set that can only be acquired through comprehensive training.
The Occupational Safety and Health Administration (OSHA) mandates this training, recognizing its crucial role in preventing accidents. Operators must be trained to understand the mechanics and characteristics of the forklift, including aspects like the centre of gravity and the stability triangle.
In a training program, operators learn crucial skills, such as:
- Safe Load Handling: This includes understanding how to correctly load and unload, the maximum load capacity, and the impact of load size, weight, and positioning on the forklift’s stability.
- Operating Principles: Trainees learn how to maneuver the forklift in various conditions, including narrow or crowded areas, ramps, and tight corners. They are also trained in safe speeds, steering, and the importance of visibility.
- Equipment Inspection: Regular pre-operation inspections are essential for spotting potential mechanical issues that could lead to accidents. Training should cover how to conduct these inspections thoroughly.
- Emergency Protocols: In an accident, operators must know how to respond quickly and appropriately. Training provides these essential emergency response skills, like the correct steps if a forklift tips over.
However, training isn’t a one-and-done affair. Refresher courses are essential because they keep operators’ knowledge up-to-date and reinforce the importance of safety. OSHA recommends refresher training at least once every three years or sooner if the operator is involved in an accident or near miss, observed operating the vehicle unsafely, or assigned to a new type of forklift.
Furthermore, the importance of training extends beyond operators. All employees working in an environment where forklifts are used should be aware of safety principles. For example, they should understand the hazards associated with forklift operations and know to never walk under raised forks.
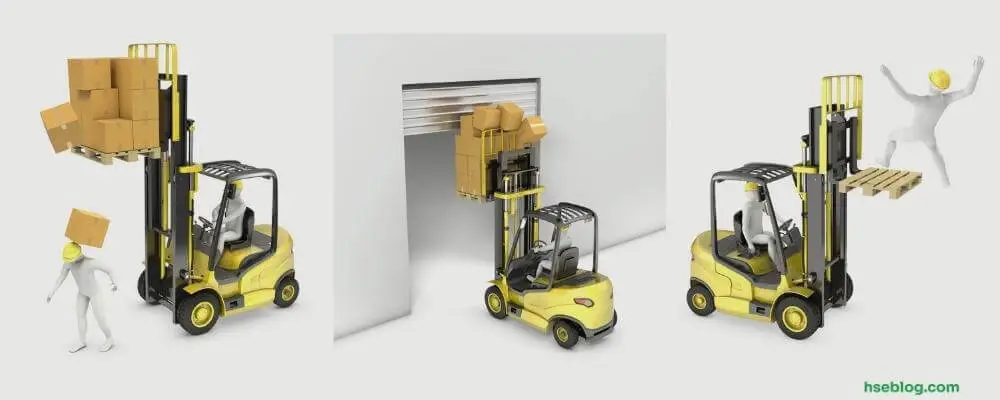
2. Speeding
Regarding forklift operations, speed doesn’t equate to productivity but poses a significant safety risk. Forklifts are designed for power and precision, not speed. They are heavy machines that can carry substantial loads, making the physics of their operation quite different from other vehicles. Their high centre of gravity and narrow wheelbase makes them susceptible to tipping over, particularly when operated at high speeds.
The high-speed operation does not just risk tipping over. Still, it can also cause operators to lose control of the vehicle, potentially leading to collisions with people, objects, or other vehicles. Quick turns or sudden stops, often outcomes of excessive speed, can result in instability and, ultimately, accidents.
Moreover, operating a forklift at high speed reduces the operator’s reaction time. If a pedestrian or another vehicle unexpectedly crosses a forklift’s path, a speeding forklift operator may not have enough time to stop safely, potentially causing a serious accident.
To address the issue of speeding:
- Establish Speed Limits: Based on the layout and operations of your warehouse, establish a reasonable and safe speed limit for forklift operations. OSHA does not specify a maximum speed limit, but a common limit is 5 miles per hour, especially in areas where pedestrians are present.
- Enforce the Rules: Simply establishing speed limits isn’t enough. They must be enforced consistently. Regular monitoring, reminders, and disciplinary measures for rule-breaking can be part of your strategy.
- Use Speed Limiting Devices: If speeding is a persistent problem, consider investing in speed-limiting devices or technology that can control the maximum speed of the forklift.
- Regular Training: As with other aspects of forklift safety, training is key. Make sure operators understand the dangers associated with speeding and the reasons for speed limits.
Remember, the goal of your forklift operation should be safety first, then efficiency. By regulating and enforcing speed limits in your warehouse or operation site, you’re taking a crucial step in preventing forklift accidents.
3. Improper Loading
Loading issues are among the most common causes of forklift accidents. Overloading, imbalanced loading, or insecure loads can destabilize the forklift, putting it at risk of tipping over. Falling loads, on the other hand, can cause severe injuries or damage to property.
Here’s how improper loading can cause accidents:
- Overloading: Every forklift has a maximum load capacity that should not be exceeded. Overloading puts excessive strain on the forklift, which can cause mechanical issues or tipping over due to a shifted centre of gravity.
- Imbalanced Loading: Even if a load is within the forklift’s weight limit, it can still be dangerous if not balanced correctly. An imbalanced load can cause the forklift to become unstable and tip over.
- Insecure Loading: If a load isn’t secured properly, it can slide off the forks, causing injury or property damage.
To avoid accidents caused by improper loading:
- Adhere to Load Capacity: Ensure operators are aware of the forklift’s load capacity and adhere to it strictly. The load capacity should be clearly marked on the forklift.
- Balanced and Secure Loading: Operators should be trained to balance loads correctly and ensure they’re secure before moving. This includes even distribution of weight and use of securing mechanisms when necessary.
- Training: Regular training can help operators understand the importance of proper loading and the risks associated with overloading or incorrect loading.
- Regular Inspections: Operators should inspect the load before moving it, checking for balance, security, and potential issues.
Understanding the correct way to load a forklift and recognizing the dangers of improper loading are key skills for any forklift operator. By enforcing rules regarding load capacity and providing regular training on safe loading practices, you can significantly reduce the risk of accidents caused by improper loading.
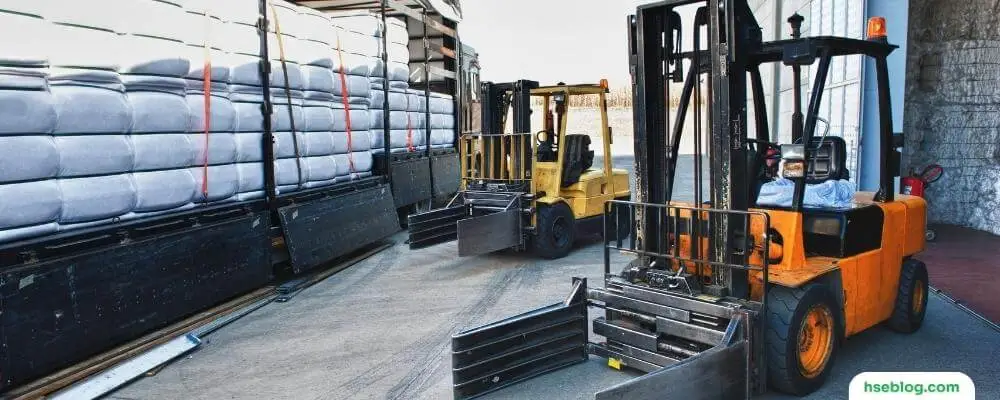
4. Poor Forklift Maintenance
Neglecting regular maintenance of forklifts can lead to critical mechanical failures, resulting in accidents or even fatalities. A well-maintained forklift is not just a safe forklift, but it’s also more efficient and has a longer lifespan.
Here’s why poor maintenance is a problem:
- Malfunctioning Parts: Wear and tear, especially on critical components like brakes, steering, transmission, or lifting systems, can cause these parts to malfunction, leading to accidents.
- Leaking Fluids: Leaks, be it hydraulic fluid or coolant, can lead to a machine malfunction or hazardous conditions like slippery surfaces.
- Reduced Visibility: A malfunctioning light or worn-out mirror can reduce visibility for the operator, increasing the risk of accidents.
Here’s how you can ensure proper forklift maintenance:
- Routine Maintenance Schedule: Implement a routine maintenance schedule as the manufacturer recommends. This can include daily checks, monthly inspections, and yearly professional servicing.
- Daily Inspections: Operators should perform daily pre-shift inspections. These inspections include checking the tires, forks, brakes, steering, warning devices, lights, and safety devices.
- Trained Personnel: Ensure that maintenance and repairs are carried out by trained personnel familiar with the specific type of forklift.
- Keep Maintenance Records: Detailed records of all inspections, repairs, and maintenance work should be kept. These records can help identify recurring problems and ensure that necessary preventative maintenance is not overlooked.
Regular maintenance is a proactive way of preventing accidents by ensuring the forklift remains safe and reliable. By strictly adhering to a routine maintenance schedule, potential issues can be detected early and rectified before they become major safety concerns.
5. Lack of Communication
In an environment where heavy machinery like forklifts is in operation, clear and effective communication is crucial for maintaining safety. Lack of communication can result in accidents, as other workers or even the forklift operators themselves may be unaware of certain risks or actions in their vicinity.
Here are the issues that may arise due to poor communication:
- Unexpected Movements: Without proper communication, workers may be caught off-guard by a forklift’s movements, leading to accidents.
- Misjudged Actions: If an operator cannot clearly signal their intentions, others in the vicinity might misjudge the actions, potentially putting themselves in harm’s way.
To improve communication and enhance safety:
- Use of Horns and Alarms: Encourage operators to use the forklift’s horn or alarm system, particularly at blind spots, intersections, entrances, and whenever reversing.
- Hand Signals: In noisy environments where horns or alarms may not be heard clearly, standardized hand signals can be a helpful tool for communication.
- Clear Markings: Clearly marked forklift zones and pathways can inform workers when they’re entering an area where forklifts operate.
- Training: Operators and other staff should understand and use their environment’s various signals, alarms, and markings.
- Communication Devices: Walkie-talkies or other communication devices can coordinate forklift movements in larger facilities.
- Effective Lighting: Good lighting enhances visibility, helping everyone see and understand what’s happening around them.
Remember, communication is a two-way street involving the sender (in this case, the forklift operator) and the receiver (other nearby workers). Everyone should understand the importance of this communication and be prepared to act accordingly. Effective communication can significantly reduce the risk of accidents and create a safer working environment.
6. Unsafe Work Environment
An unsafe or poorly organized work environment is a recipe for accidents when operating forklifts. Forklifts require clear paths and ample space to operate safely. Cluttered, narrow, or disorganized areas can impede movement, reduce visibility, and increase the risk of collisions with objects, other vehicles, or even people.
Here’s how an unsafe work environment can cause accidents:
- Blocked Vision: Clutter or disorganization can obstruct an operator’s vision, making it difficult to see potential hazards or people.
- Restricted Movement: Narrow or crowded paths can restrict the forklift’s movement, making safe maneuvering difficult and potentially leading to collisions.
To create a safer work environment:
- Regular Inspections and Cleaning: Inspect the workspace for obstructions and potential hazards. Cleaning should be a routine, ensuring that clutter is promptly removed and the aisles are always clear.
- Clear Markings: Clearly mark designated forklift routes, pedestrian pathways, and no-go areas. This will help everyone understand where forklifts are expected to be and where they need to exercise caution.
- Adequate Space: Ensure there is enough space for forklifts to operate. This includes ample room for turning and the safe stacking and unstacking of loads.
- Safety Barriers: Install safety barriers, where necessary, to protect workers from forklift traffic, especially in areas where pedestrian traffic is high.
- Good Lighting: Ensure all areas where forklifts operate are well-lit to improve visibility.
- Proper Layout: A well-thought-out layout that minimizes the need for forklifts to move through crowded or narrow spaces can significantly reduce the risk of accidents.
By prioritizing creating a safe and organized work environment, you can significantly reduce the risk of forklift accidents, thereby increasing the efficiency and productivity of your operations. A clean, organized workplace is a safer workplace.
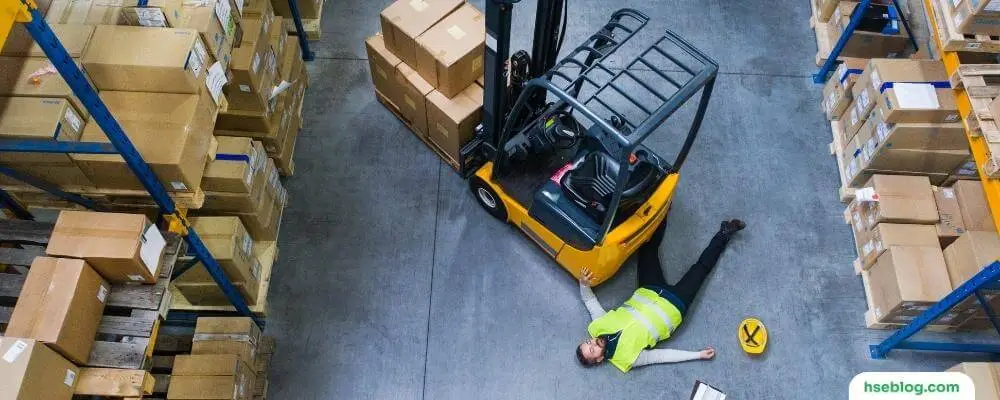
7. Neglecting Safety Rules
Despite established safety protocols, neglecting or disregarding these rules can lead to preventable accidents. Forklift safety rules are implemented to protect operators and other workers from potential hazards associated with forklift operations. Ignoring these rules can lead to accidents and violate OSHA regulations, which can result in penalties.
Some common safety rules that may be neglected include:
- Speed Limits: Operators might ignore speed limits to work faster, which can increase the risk of tipping over or collisions.
- Seatbelt Use: Not wearing a seatbelt can have serious consequences if a forklift is tipped over.
- Load Capacity: Overloading a forklift can cause it to become unstable and tip over.
- Pedestrian Right-of-Way: Failing to give pedestrians the right-of-way can lead to serious accidents.
To ensure adherence to safety rules:
- Regular Reviews: Regularly review safety guidelines with all operators. This keeps the rules fresh in their minds and emphasizes the importance of adhering to them.
- Training: Training shouldn’t just be a one-off event. Regular refresher courses are a great way to reinforce the importance of safety rules and ensure they are understood and followed.
- Enforcement: There should be consequences for not following safety rules. A culture of accountability encourages operators to adhere to the rules.
- Lead by Example: Supervisors and management should follow all safety rules and guidelines. This sets a strong example for all employees and emphasizes the importance of safety in the workplace.
Adherence to safety rules is paramount in preventing forklift accidents. By fostering a culture that values safety and strict compliance with established safety rules, you can significantly decrease the risk of forklift accidents in the workplace.
8. Inadequate Warning Systems
Forklifts, by their very nature, can pose risks to those in their vicinity. Hence, warning systems that signal a forklift’s presence or operation are critical in preventing accidents. Lack of proper warning systems such as flashing lights, backup alarms, or mirrors can lead to accidents by catching pedestrians or other workers unawares.
Here’s how inadequate warning systems can contribute to accidents:
- Unseen Forklifts: Without visible flashing lights, especially in busy or poorly lit environments, pedestrians might not notice a moving forklift until it’s too late.
- Unheard Movements: In noisy environments, the sound of a moving forklift might blend into the background noise, making backup alarms essential.
- Limited Visibility: Without mirrors at corners, operators might not see pedestrians or other forklifts, leading to collisions.
To enhance safety with adequate warning systems:
- Install Flashing Lights: Flashing lights on forklifts, especially when moving, can draw attention to their presence and operation.
- Use Backup Alarms: Backup alarms, which sound off when a forklift reverses, can warn people in the forklift’s path.
- Place Mirrors at Corners: Strategic placement of mirrors at corners and intersections can help operators see around corners, thus preventing accidents.
- Pedestrian Warning Systems: These can include floor markings, signs, or systems that alert pedestrians when entering a forklift zone.
- Regular Checks: As part of the regular maintenance schedule, ensure warning systems are functional and audible/visible enough to serve their purpose.
By implementing adequate warning systems, you enhance the visibility and audibility of forklift operations, creating safer conditions for operators and pedestrians. A well-warned workplace is indeed a safer workplace.
9. Operating Near Edge Loads
Forklifts are designed to operate on flat, stable surfaces. Operating near-edge loads, such as near-loading docks or on uneven terrain, can destabilize a forklift and lead to tipping. These environments present a particular challenge because they can shift the forklift’s centre of gravity, making it more prone to accidents.
Here’s how operating near-edge loads can cause accidents:
- Tipping Over: If a forklift is too close to an edge load or if the edge load is unbalanced or insecure, the forklift can tip over, potentially causing serious injuries.
- Falling Loads: In some situations, the edge load might be unstable. If a forklift disturbs an edge load, it can cause the load to fall, damaging property or injuring people.
To prevent accidents near edge loads:
- Safe Distance: Operators should maintain a safe distance from edge loads whenever possible. This reduces the risk of tipping over or disturbing unstable loads.
- Proper Securing: Ensure edge loads are secure and stable before operating a forklift near them. This might involve additional securing measures or repositioning of the load.
- Training: Operators should receive training on safely operating near-edge loads, including recognizing potential hazards and understanding the risks.
- Safe Speeds: When operating near edge loads, operators should reduce their speed to ensure sufficient time to react to unexpected shifts or instability.
- Regular Inspections: Regularly inspect the work environment and edge loads for potential hazards, ensuring they are secure and stable.
By taking these precautions, you can minimize the risk of operating forklifts near edge loads, ensuring a safer environment for all workers. Remember, safety should always be the primary consideration in any forklift operation.
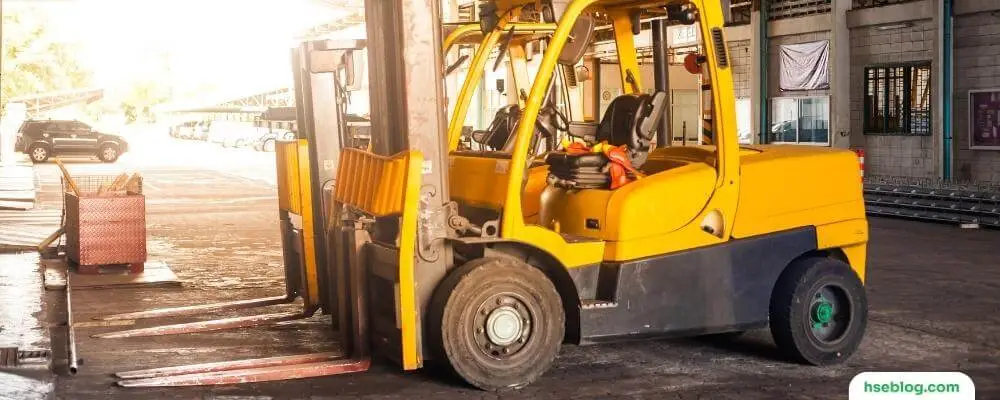
10. Driver Inattention
Operating a forklift requires a high level of concentration and attention to surroundings. Any form of distraction or inattention can lead to serious accidents, as the operator may fail to notice potential hazards or make errors in control.
Here’s how driver inattention can lead to accidents:
- Overlooking Hazards: An inattentive driver might overlook hazards such as people in the forklift’s path, low clearances, or uneven surfaces.
- Delayed Reaction Times: Distraction can lead to delayed reaction times, resulting in accidents if quick maneuvers are required.
- Incorrect Operations: Inattentive drivers may make mistakes like going too fast, turning abruptly, or improperly handling loads.
To reduce accidents caused by driver inattention:
- Zero Distraction Policy: Enforce a policy that requires operators to stay alert and focused while operating a forklift. This means no use of cell phones, no eating or drinking, or unnecessary conversation while driving.
- Regular Breaks: Fatigue can lead to inattention. Ensure operators take regular breaks to rest and recharge.
- Training: Regular safety training should stress the importance of staying alert and focused while operating a forklift.
- Proper Shift Schedules: Avoid long shifts leading to operator fatigue and inattention.
- Awareness Campaigns: Regularly remind operators about the dangers of inattention through safety meetings, posters, or messages.
Addressing driver inattention and enforcing policies that promote focus and alertness can create a safer work environment and reduce the likelihood of forklift accidents. Remember, a focused operator is a safe operator.
11. Driving Around Corners Too Quickly
Forklifts, especially when loaded, have a high center of gravity, which makes them susceptible to tipping over when taking corners too quickly. A sharp turn at high speed can shift the center of gravity outside the stability triangle (the three-point support system that a forklift has with its front two wheels and its central rear wheel), causing the forklift to tip over.
Here’s how driving around corners too quickly can cause accidents:
- Tipping Over: The most significant risk of taking corners too quickly is that the forklift can become unstable and tip over, which can cause serious injuries or even fatalities.
- Collisions: Speeding around corners can also result in collisions with pedestrians, other vehicles, or objects if the operator doesn’t have enough time to react.
- Load Spillage: High speed around corners can cause loads to shift or fall off the forks, potentially leading to damage or injury.
To prevent accidents due to high-speed cornering:
- Enforce Speed Limits: Impose and enforce speed limits in your facility, and emphasize the need for reducing speed while turning corners.
- Training: Provide proper training to operators on how to handle corners safely. This includes reducing speed before turning and not making sharp turns.
- Clear Visibility: Ensure all corners have good visibility. Consider installing mirrors at blind corners so operators can see any oncoming traffic.
- Signage: Place visible signage at corners reminding operators to slow down.
- Design Considerations: Design your facility with wide, gentle corners rather than sharp turns to improve safety.
By promoting safe cornering practices and providing a well-designed and clearly marked environment, you can significantly reduce the risk of forklift accidents in your facility.
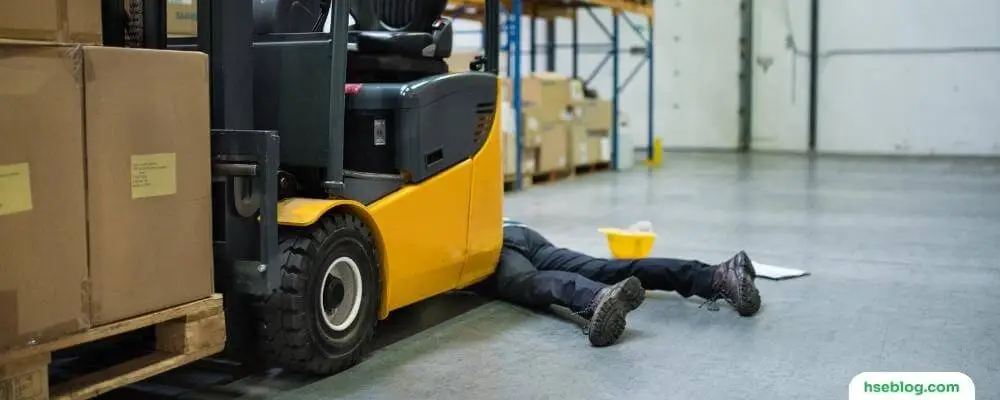
12. Driving With The Load Elevated
Driving a forklift with the load elevated can significantly increase the risk of accidents. The higher the load is lifted, the higher the centre of gravity of the forklift-load system, making it unstable and more susceptible to tipping over. This risk is even higher when going around corners, as the lateral forces acting on the forklift increase.
Here’s how driving with the load elevated can cause accidents:
- Tipping Over: As mentioned, the elevated load raises the centre of gravity and increases the risk of the forklift tipping over, especially when turning corners.
- Falling Loads: If the load is not properly secured, it can fall from an elevated position, potentially causing injury to the operator or others nearby or damage to the property.
- Collision: An elevated load can also obstruct the operator’s view, increasing the risk of collisions.
To prevent accidents due to driving with the load elevated:
- Lower the Load: Train operators always lower the load to the lowest safe level before moving the forklift.
- Training: Ensure operators receive training on safe load handling, including keeping loads low while driving, especially around corners.
- Enforce Rules: Enforce rules requiring operators to keep loads low while driving and monitor compliance.
- Regular Safety Checks: Regularly check the condition of the forklift’s load-handling attachments to ensure they are in good working order.
By adhering to these guidelines, you can reduce the risk of accidents related to driving with elevated loads, ensuring a safer environment for forklift operations. Remember, safety should always be a forklift operator’s first priority.
Conclusion
Safeguarding your workplace from forklift accidents involves operator training, adherence to safety rules, regular maintenance, and a comprehensive understanding of the working environment. This post highlighted twelve common causes of forklift accidents, providing practical mitigation strategies. However, every workplace has its unique challenges, and it is crucial to conduct regular assessments to identify and address any potential hazards. By fostering a proactive safety culture at all levels of your organization, you can comply with regulatory requirements and ensure the well-being of your most valuable asset—your employees.