In the relentless rhythm of industrial landscapes, machines with intricate parts and movements form the backbone that keeps production and processes humming. However, as essential as they are, these machines can pose serious threats to the safety of the workforce. Welcome to our latest blog post, where we dive into the world of Moving Machinery Parts Hazards & 3 Motions Of Moving Parts. This article is a must-read for anyone working in an environment with heavy machinery and for those responsible for ensuring workplace safety.
We will begin by showing the potential dangers and consequences of interacting with unguarded moving parts in machinery. In many industries, from manufacturing to food processing, the significance of understanding these hazards cannot be overstated.
Next, we’ll peel back the layers on the three primary motions of machine parts – rotating, reciprocating, and transversing. These motions, often overlooked, are central to understanding the mechanisms that can cause harm.
Finally, armed with knowledge, we will explore the safeguards and best practices to mitigate these hazards. Whether you are a safety officer, a manager, or an operator on the floor, this article is tailored to equip you with the vital knowledge needed to contribute to a safer and more productive working environment.
Hazards of Machine Moving Parts
Unguarded machines and equipment are among the biggest hazards for workers in meatpacking, poultry, and food processing. Workers’ fingers, arms, hair, and other body parts can be caught or entangled in unguarded machine parts or equipment. Protective clothing worn by most meatpacking, poultry, and food processing workers, such as gloves, frocks, aprons, and rain gear, can be caught and pulled into the machine. Finally, sanitation workers in the meatpacking, poultry, and food processing industries are also at risk when they use hoses that can be caught and pull their arms into a moving, unguarded machine.
Moving parts can pose a serious hazard to workers not properly trained to safely handle and operate them. If used incorrectly, moving parts can cause amputations, lacerations, crush injuries, and even death. Workers who are not properly trained in how to safely work with moving parts are at an increased risk of being injured by them.
There are a variety of ways that workers can be injured by moving parts. Some of the most common include:
- Amputations: Moving parts can cause amputations if they come into contact with a worker’s body.
- Lacerations: Moving parts can cause lacerations if they come into contact with a worker’s skin.
- Crush injuries: Moving parts can cause crush injuries if they collide with a worker’s body.
- Death: Moving parts can cause death if they contact a worker’s body fatally.
- Burns: Moving parts can cause burns if they come into contact with a worker’s skin.
- Shock: Moving parts can cause a shock if they come into contact with a worker’s body.
- Fractures: Moving parts can cause fractures if they come into contact with a worker’s body.
- Dislocations: Moving parts can cause dislocation of joints if they come into contact with a worker’s body.
- Sprains: Moving parts can cause sprains if they come into contact with a worker’s body.
- Strains: Moving parts can cause strains if they come into contact with a worker’s body.
Machine guards are used to prevent any contact between a machine’s moving parts and the worker. They are also used to contain fragments and particles released by a machine.
The OSHA law states the following:
“One or more methods of machine guarding shall be provided to protect the operator and other employees in the machine area from hazards such as those created by point of operation, ingoing nip points, rotating parts, flying chips, and sparks.” (29 CFR 1910.212)
Crushed hands and arms, severed fingers, blindness — the list of possible machinery-related injuries is as long as it is horrifying. There seem to be as many hazards created by moving machine parts as there are types of machines. Machine guards are essential for protecting workers from needless and preventable injuries.
A good rule to remember is Any machine part, function, or process which may cause injury must be machine guarded. When the operation of a machine or accidental contact with it can injure the operator or others in the vicinity, the hazards must be controlled or eliminated.
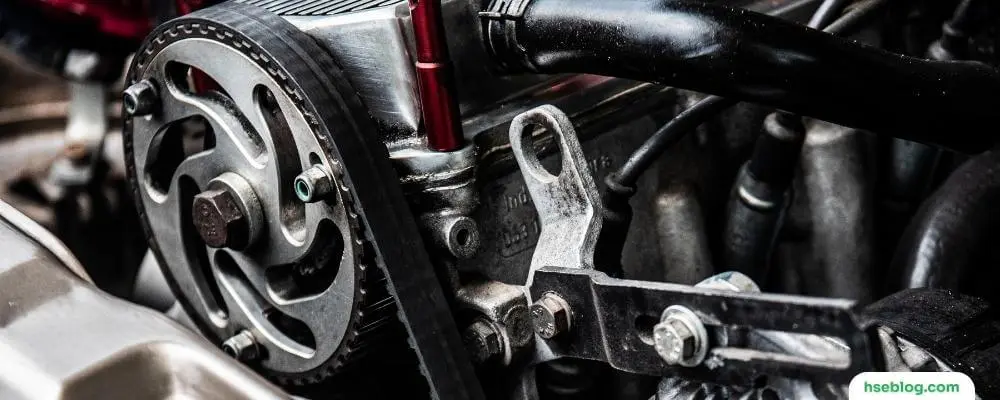
Where Mechanical Hazards Occur
Dangerous moving parts in three basic areas require machine safeguarding:
- The point of operation: the point where work is performed on the material, such as cutting, shaping, boring, or forming stock.
- Power transmission apparatus: all components of the mechanical system which transmit energy to the part of the machine performing the work. These components include flywheels, pulleys, belts, connecting rods, couplings, cams, spindles, chains, cranks, and gears. Other moving parts: all parts of the machine which move while the machine is working. These can include reciprocating, rotating, transverse moving parts, feed mechanisms, and auxiliary parts of the machine.
Hazardous Mechanical Motions and Actions
Various mechanical motions and actions may present hazards to the worker. These can include the movement of rotating members, reciprocating arms, moving belts, meshing gears, cutting teeth, and any parts that impact or shear. These different types of hazardous mechanical motions and actions are basic in varying combinations to nearly all machines, and recognizing them is the first step toward protecting workers from the danger they present.
The basic types of hazardous mechanical motions and actions are:
Motions
- Rotating (including in-running nip points)
- Reciprocating
- Transversing
Actions
- Cutting
- Punching
- Sharing
- Bending
Some general characteristics of these motions and actions present hazards, even if the machines themselves do not have any of the specific hazardous motions and actions listed above. For example, all moving parts can be hazardous if not properly guarded. Another general characteristic is that the speed of the motion can increase the hazard. For example, a fast-moving belt can cause more serious injuries than a slow-moving belt.
Three Primary Motions For Machine Moving Parts
“Rotation” is circular motion around an axis or center, such as rotating collars, couplings, cams, clutches, flywheels, shaft ends, and spindles that may grip clothing or force a body part into a dangerous location. Even smooth-surfaced rotating machine parts can be hazardous. Projections such as screws or burrs on the rotating part increase the hazard potential.
The danger increases when projections such as set screws, bolts, nicks, abrasions, and projecting keys or set screws are exposed on rotating parts, as shown in the figure to the right.
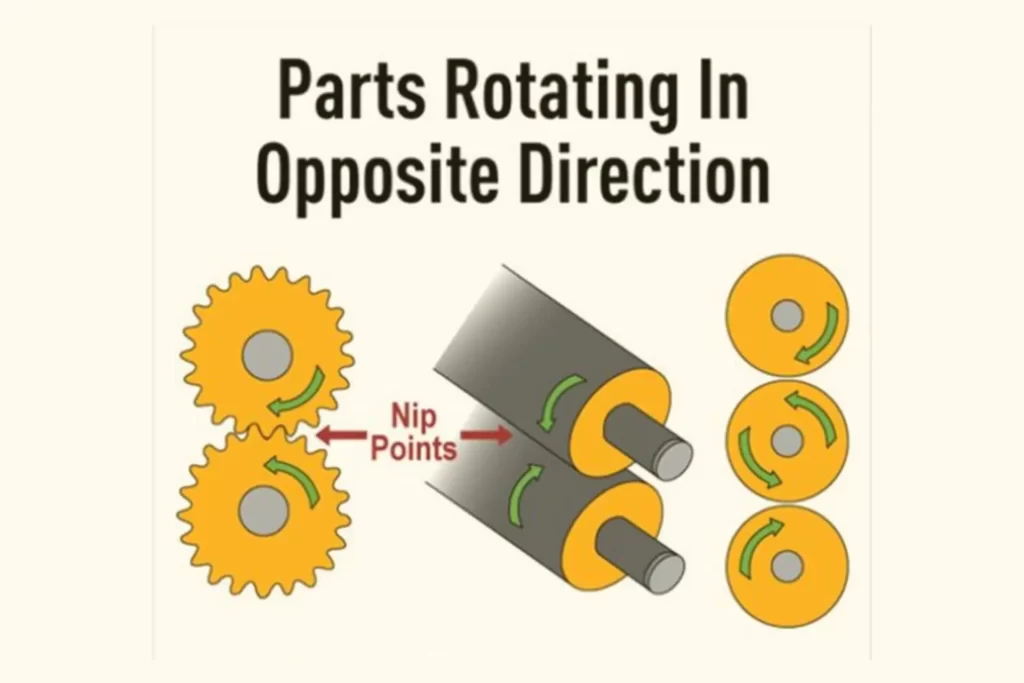
1. In-running Nip Points
In-running nip point hazards are caused by rotating parts on machinery. There are three main types of in-running nips.
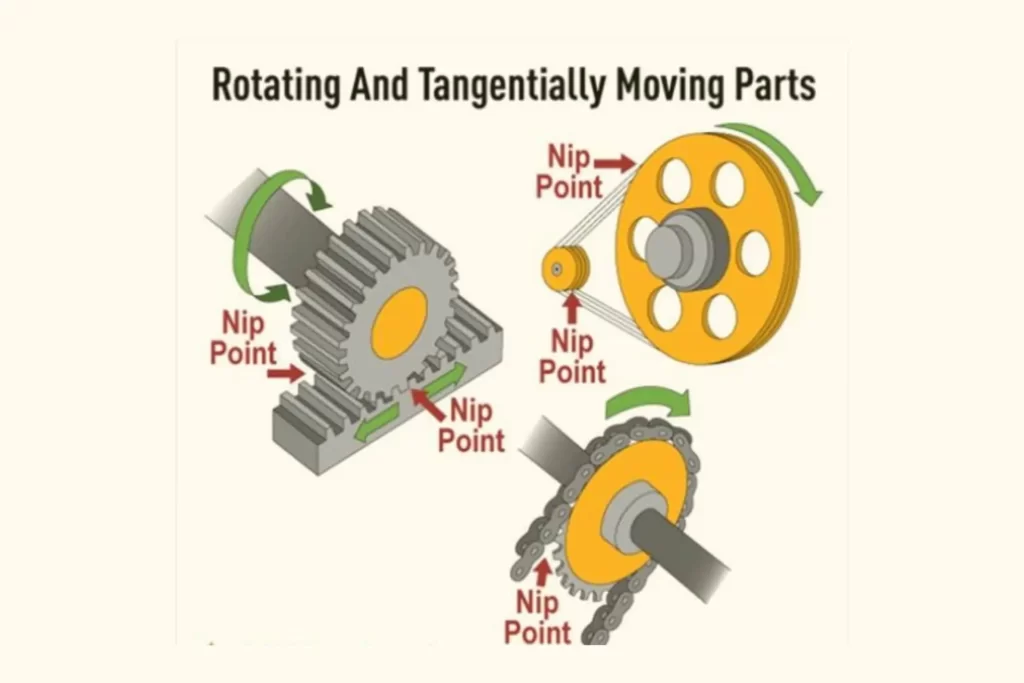
- Parallel rotating parts: Parts can rotate in opposite directions while their axes are parallel. These parts may be in contact, producing nip points. Stock fed between the rolls may also produce nip points. This danger is common on machines with intermeshing gears, rolling mills, and calenders.
- Tangentially moving parts: Tangentially moving nip points are also created between rotating and tangentially moving parts. Some examples would be the point of contact between a power transmission belt and its pulley, a chain and a sprocket, and a rack and pinion.
- Rotating and fixed parts: Nip points can occur between rotating and fixed parts, creating a shearing, crushing, or abrading action. Examples are spoked handwheels or flywheels, screw conveyors, or the periphery of an abrasive wheel and an incorrectly adjusted work rest.
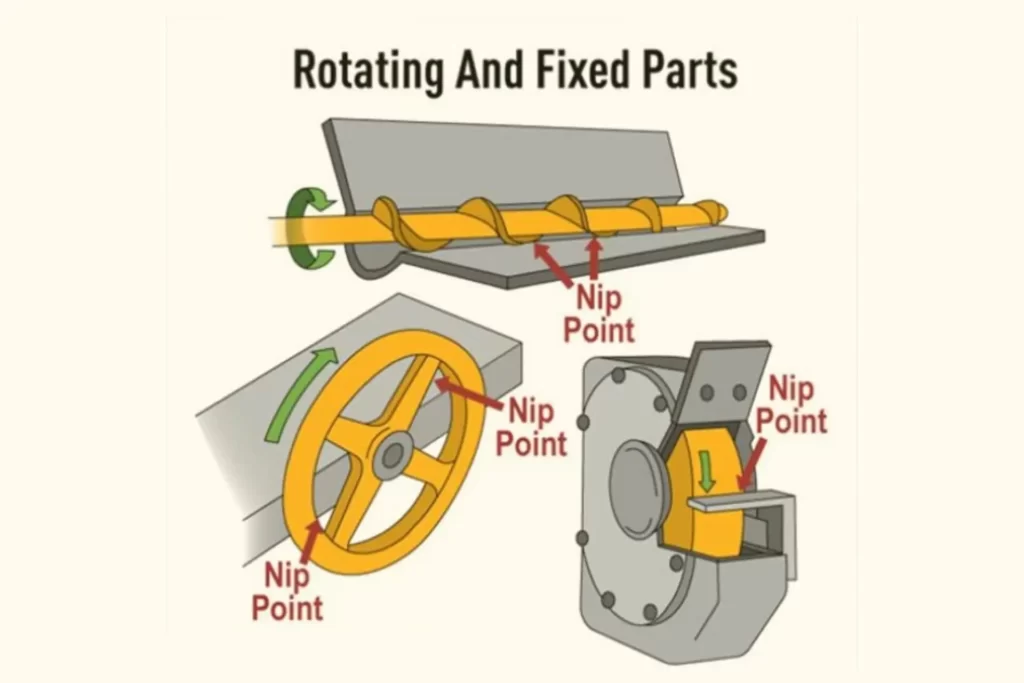
2. Reciprocating Motions
Reciprocating motions are back-and-forth or up-and-down motions that may strike or entrap an employee between a moving part and a fixed object. Reciprocating motions may be hazardous because a worker may be struck by or caught between a moving and a stationary part during the back-and-forth or up-and-down motion.
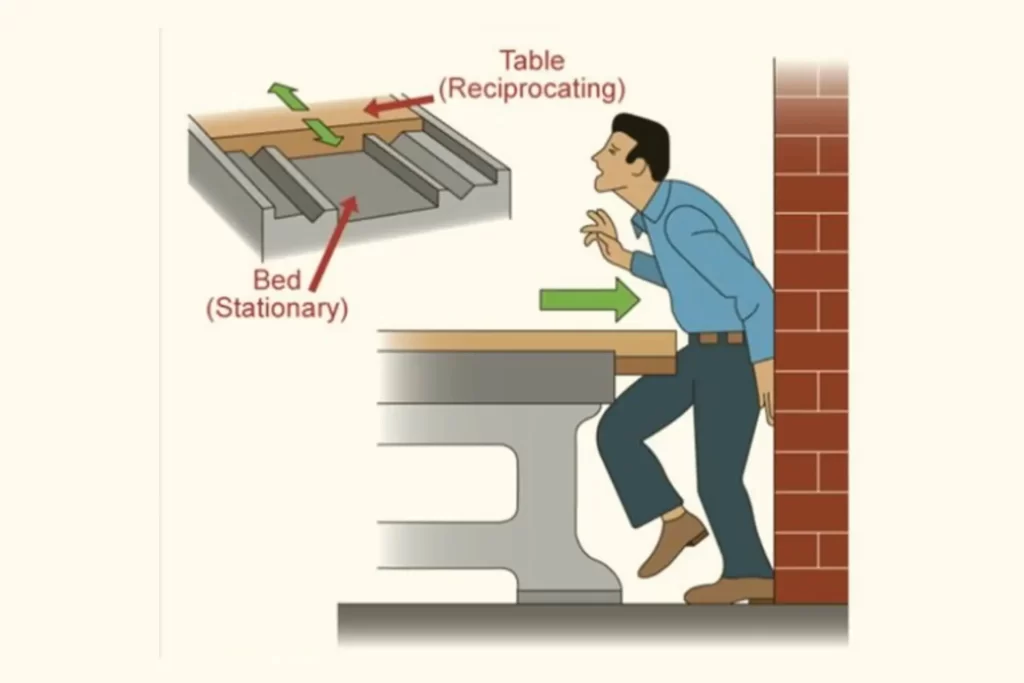
3. Transverse Motions
A transverse motion occurs in a straight, continuous line that may strike or catch an employee in a pinch or shear point created by the moving part and a fixed object. Transverse motion (movement in a straight, continuous line) creates a hazard because the moving part may strike or catch a worker in a pinch or shear point.
Rotating Shafts
Warning: Exposure to rotating shafts is the most dangerous machine safeguarding hazard. It is so dangerous we wanted to mention it again before moving on to other topics. There have been numerous accidents due to exposure to rotating shafts, and, unfortunately, most of these accidents result in a fatality.
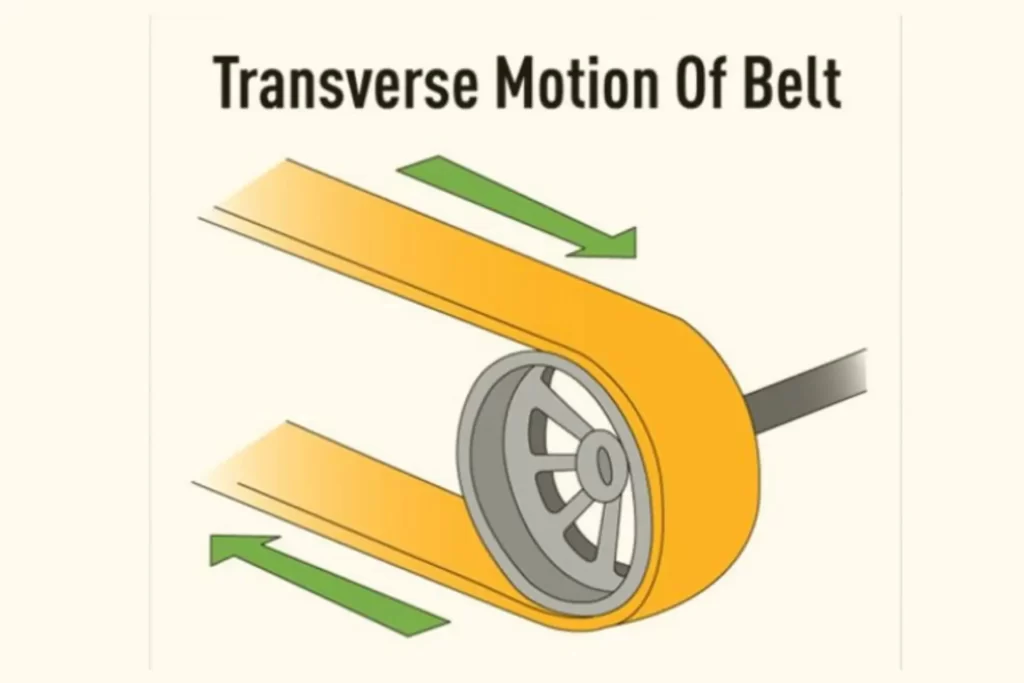
The danger of exposure to rotating shafts increases when projections such as set screws, bolts, nicks, abrasions, and projecting keys or set screws are exposed on rotating parts (see image below on the left). The image below on the right shows what can happen when a worker gets caught on a rotating shaft. In this case, massive internal injuries resulted in a tragic fatality. You should consider exposure to rotating parts as an “imminent danger” situation that must be corrected immediately.
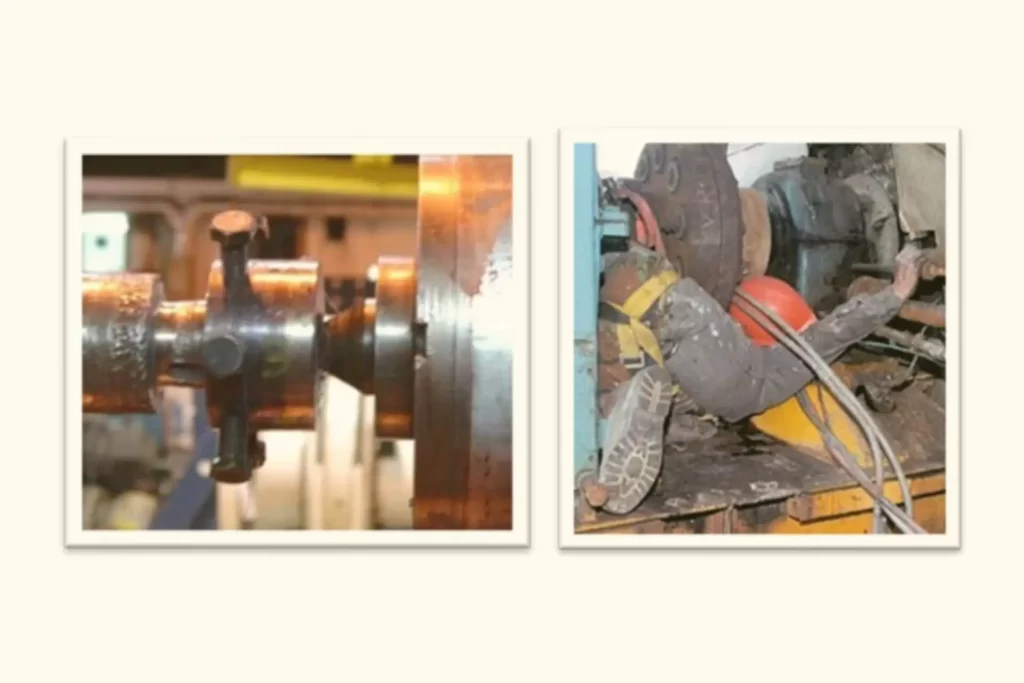
The best way to protect workers from this hazard is to install guards for each machine that requires a rotating shaft. Guards should be secured in place and regularly maintained. If you must work on machinery with unprotected rotating parts, use special tools designed for the purpose, such as coupling pulls and wrenches. Never use your hands or feet when working on machinery with unprotected rotating parts.
Finally, always be aware that exposed rotating parts can be dangerous and cause serious injury or death if left unguarded. Take the time to inspect all machinery for potential hazards and ensure guards are in a place where necessary. Properly guarded machinery is essential for a safe and productive workplace.
Conclusion
In conclusion, the moving parts of machinery, with their rotating, reciprocating, and transversing motions, hold the potential to be both the lifeblood of industries and the harbinger of severe injuries or fatalities. It is imperative to recognize and respect the inherent dangers and equip oneself and the workforce with the knowledge and tools necessary for protection. By employing robust machine guarding, adhering to safety protocols, and fostering a culture of safety vigilance, we can harness the immense power of machines while safeguarding the invaluable human lives that operate them.