Hazardous chemicals are inevitable in many industries, from manufacturing and healthcare to construction and agriculture. The Occupational Safety and Health Administration (OSHA) established the Hazard Communication Standard (HAZCOM) to protect workers from chemical-related illnesses and injuries. Often referred to as the “Right-to-Know” Law, HAZCOM ensures that employees are fully aware of chemical hazards in the workplace and understand how to handle them safely.
In this comprehensive guide, we’ll explore the purpose of HAZCOM, its key components, employer responsibilities, labeling and safety data sheet (SDS) requirements, and how it aligns with the Globally Harmonized System of Classification and Labeling of Chemicals (GHS). Whether you’re an employer, safety officer, or worker, this article provides everything you need to know about HAZCOM compliance and best practices.
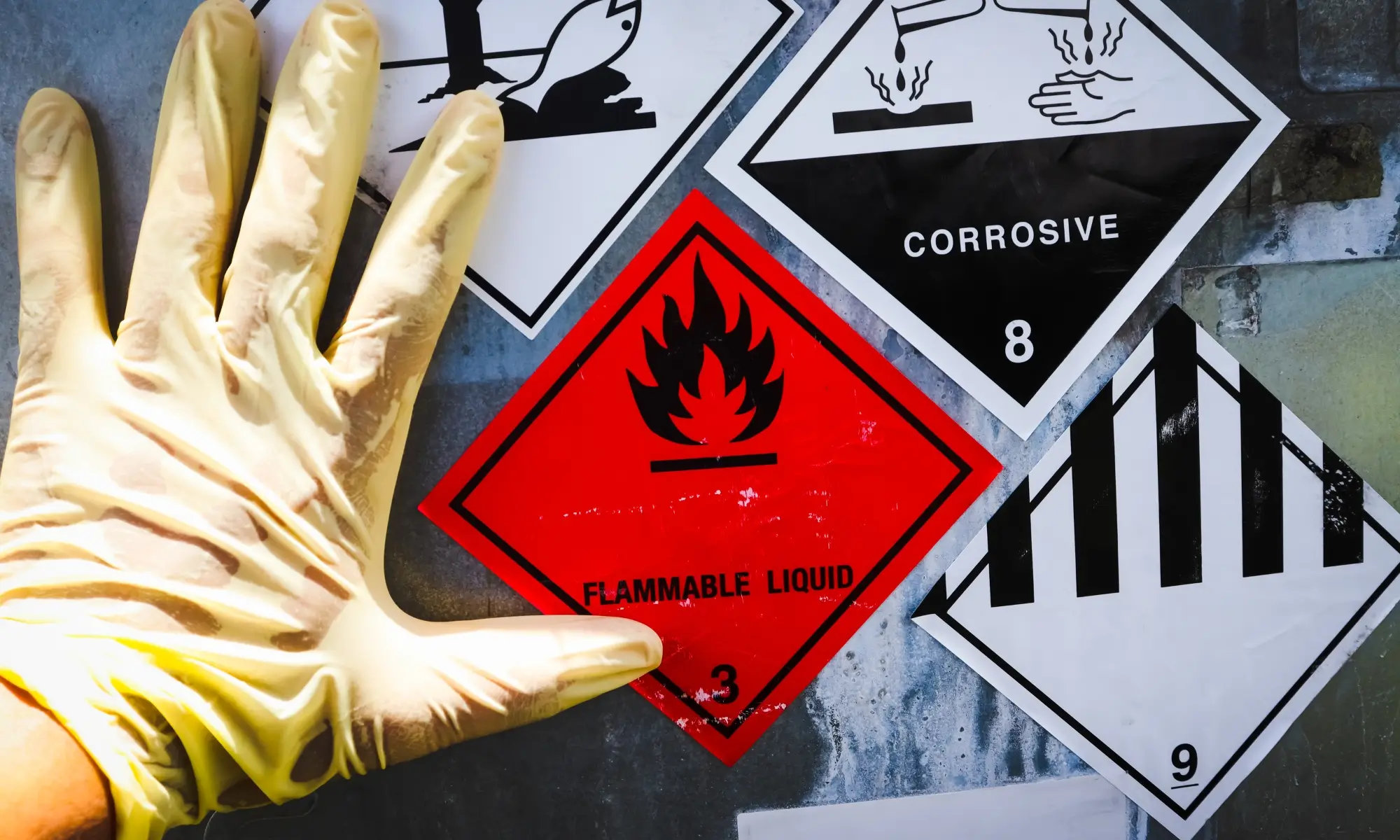
What is HAZCOM?
HAZCOM is a set of regulations designed to ensure employers and workers have access to critical information about hazardous chemicals in the workplace. Chemical manufacturers, importers, and employers must evaluate chemical hazards and communicate that information through labels, safety data sheets (SDSs), and training programs.
The HAZCOM standard is codified under 29 CFR 1910.1200 and applies to nearly all workplaces in the United States that manufacture, import, or use hazardous chemicals.
Why is HAZCOM Important?
- Protects Workers’ Health & Safety – Ensures employees understand chemical hazards, reducing the risk of illnesses, injuries, and fatalities.
- Promotes Workplace Transparency – Workers have the “Right-to-Know” about hazardous substances they may be exposed to.
- Prevents Workplace Accidents – Proper labeling and communication minimize chemical spills, explosions, fires, and exposure-related illnesses.
- Ensures Regulatory Compliance – Non-compliance with HAZCOM can lead to OSHA citations, fines, and legal liabilities.
- Encourages Safe Chemical Handling – Helps organizations implement proper safety procedures to prevent workplace hazards.
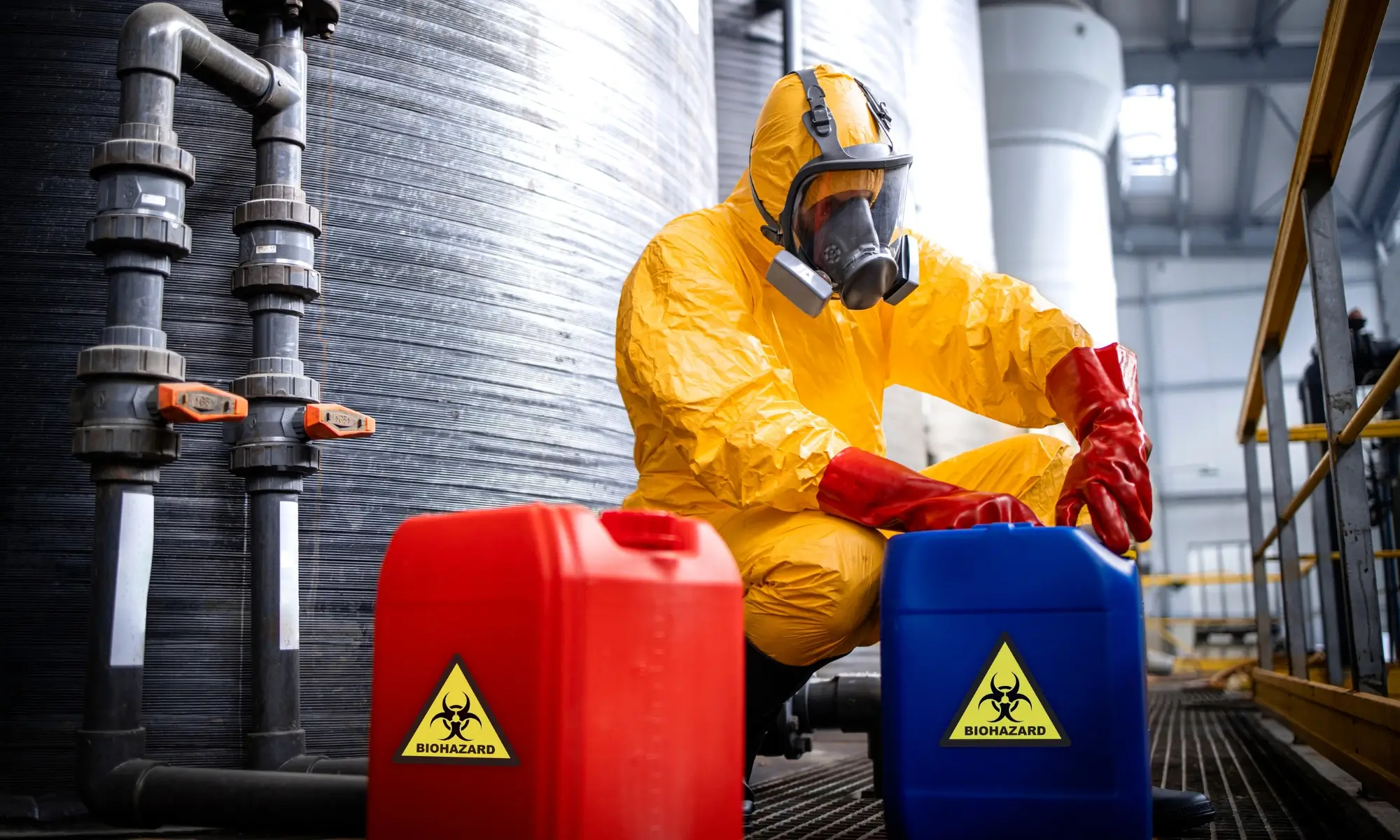
Key Components of HAZCOM
OSHA’s HAZCOM standard includes five primary elements to ensure the safe handling and use of hazardous chemicals:
1. Chemical Hazard Classification
Chemical manufacturers and importers must determine the hazards of each chemical they produce or import. These hazards fall into three main categories:
- Physical Hazards: Flammability, explosiveness, corrosiveness, etc.
- Health Hazards: Toxicity, carcinogenicity, respiratory effects, etc.
- Environmental Hazards: Impact on aquatic life, ozone layer depletion, etc.
2. Labeling Requirements
All hazardous chemicals must be labeled correctly. Labels must include:
- Product Identifier (chemical name or mixture name)
- Signal Word (e.g., “Danger” or “Warning”)
- Hazard Statements (description of the chemical hazard)
- Precautionary Statements (how to handle, store, or dispose of the chemical safely)
- Pictograms (standardized symbols for quick hazard identification)
- Manufacturer’s Information (name, address, and contact details)
3. Safety Data Sheets (SDS)
Previously called Material Safety Data Sheets (MSDS), SDSs provide detailed information about each hazardous chemical. These 16-section standardized documents must include:
- Identification of the substance
- Hazard identification
- Composition and ingredient information
- First-aid measures
- Fire-fighting measures
- Accidental release measures
- Handling and storage precautions
- Exposure controls and personal protection
- Physical and chemical properties
- Stability and reactivity
- Toxicological information
- Ecological impact
- Disposal considerations
- Transport information
- Regulatory information
- Other relevant information
4. Employee Training & Right-to-Know
Employers must train employees on:
- Understanding labels and SDSs
- Identifying chemical hazards
- Using personal protective equipment (PPE)
- Responding to chemical spills and emergencies
- Safe storage, handling, and disposal of chemicals
- Understanding the Globally Harmonized System (GHS) for chemical classification
5. Written Hazard Communication Program
Every employer must develop and maintain a written HAZCOM program that includes:
- A list of all hazardous chemicals in the workplace.
- Procedures for labeling and updating SDSs.
- Employee training records.
- Protocols for handling non-routine tasks involving hazardous chemicals.
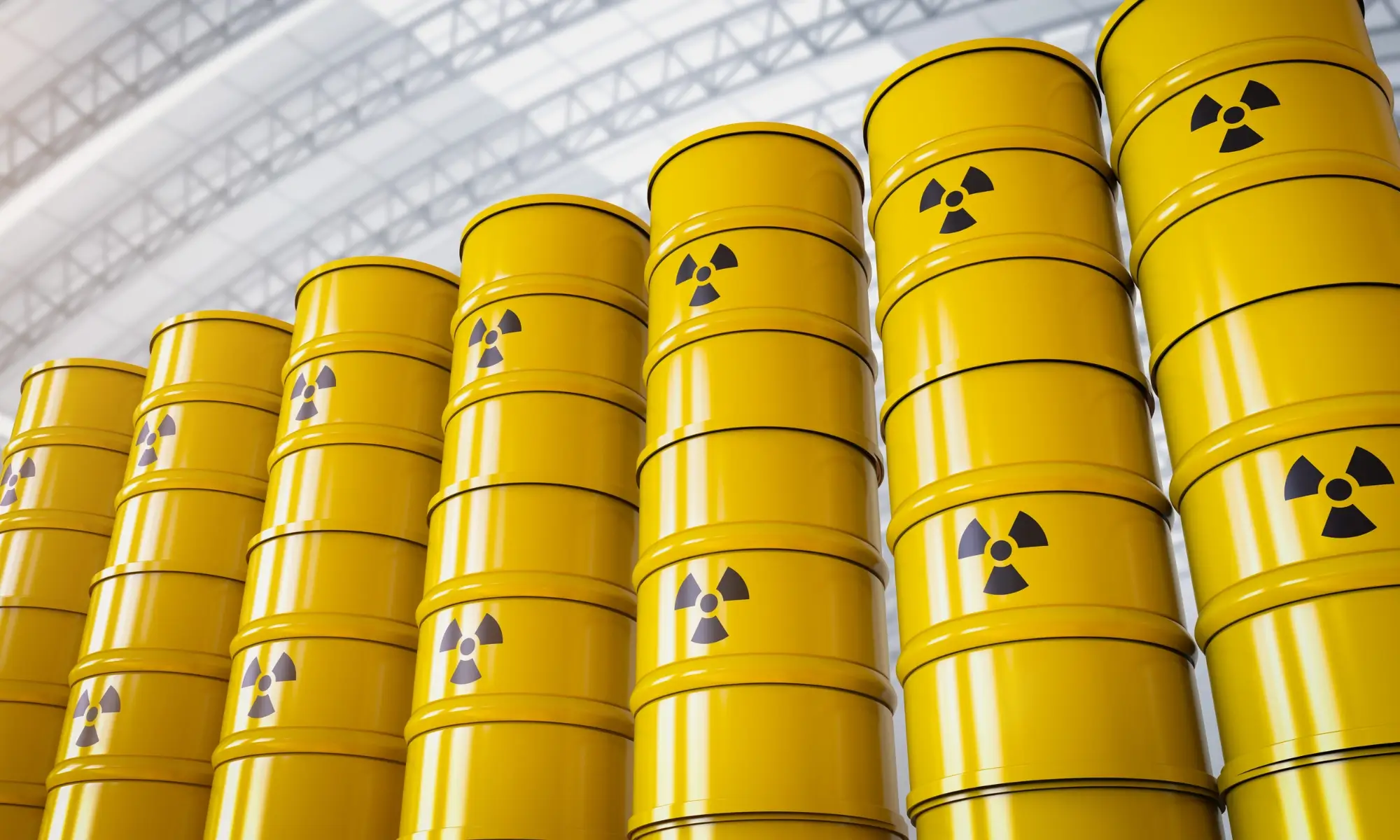
HAZCOM & The Globally Harmonized System (GHS)
To create a universal system for chemical hazard communication, OSHA aligned HAZCOM with the Globally Harmonized System of Classification and Labeling of Chemicals (GHS) in 2012. This ensures:
- Standardized hazard classification across countries.
- Consistent labeling and pictograms for easier recognition.
- A uniform SDS format that improves accessibility and comprehension.
GHS Pictograms Required by OSHA
Pictogram | Hazard Category |
---|---|
Flame | Flammable materials |
Exploding Bomb | Explosives, self-reactive substances |
Health Hazard | Carcinogens, mutagens |
Skull & Crossbones | Toxic or fatal substances |
Exclamation Mark | Skin and eye irritants |
Gas Cylinder | Compressed gases |
Corrosion | Skin burns, eye damage |
Environment | Environmental toxicity |
Flame Over Circle | Oxidizers |
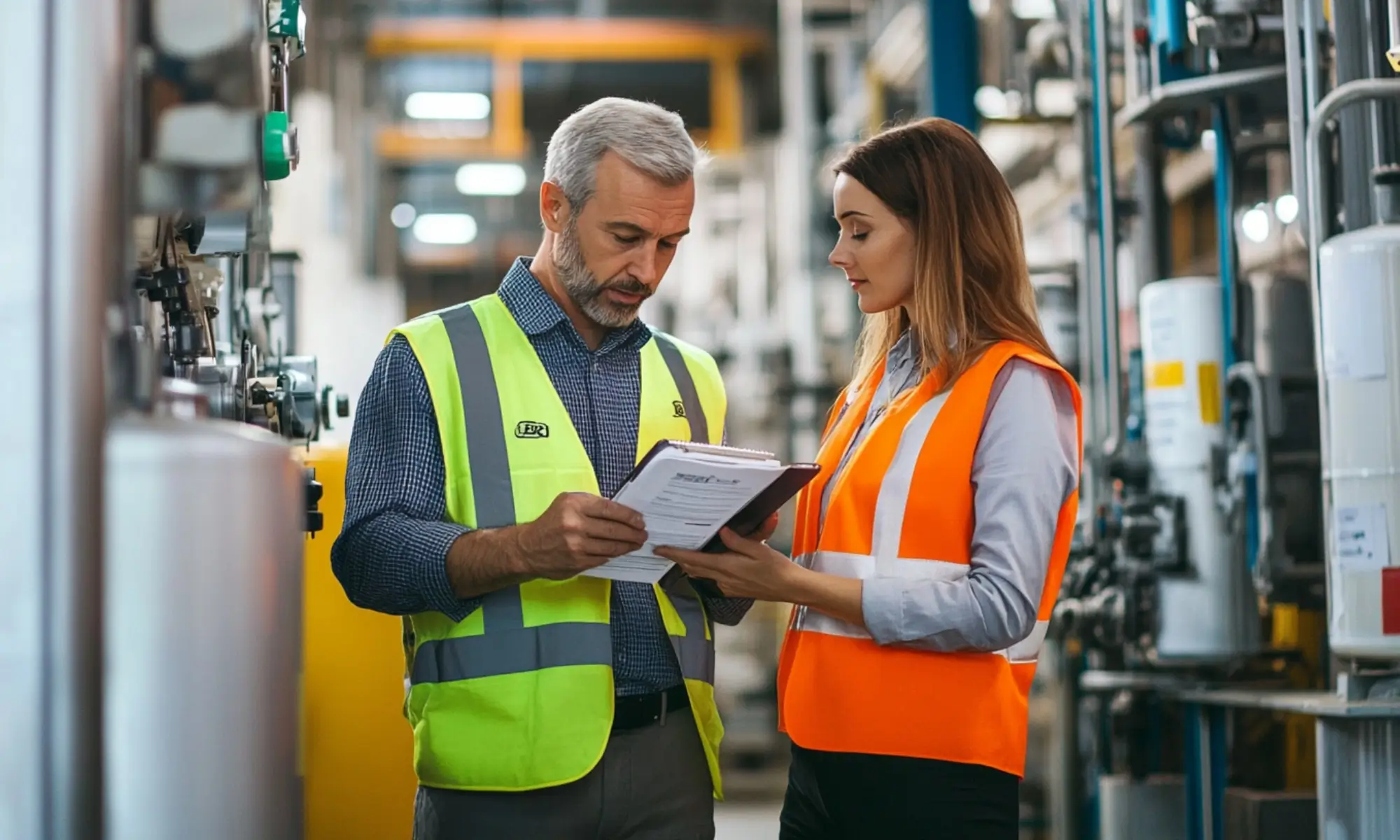
Employer Responsibilities Under HAZCOM
Under OSHA’s Hazard Communication Standard (HAZCOM), employers have a legal responsibility to ensure that hazardous chemicals in the workplace are properly managed, labeled, and communicated to employees. The goal is to protect workers from chemical-related injuries and illnesses by providing them with clear, accurate, and accessible hazard information. Key Employer Responsibilities Under HAZCOM:
1. Maintain a Chemical Inventory
Employers must:
- Identify and list all hazardous chemicals present in the workplace.
- Keep an updated inventory of these chemicals.
- Ensure that every hazardous chemical has a Safety Data Sheet (SDS) available for employees.
Tip: Keep an organized Hazardous Chemical List that includes the product name, manufacturer, SDS location, and hazard classification.
2. Ensure Proper Labeling of Hazardous Chemicals
Employers must ensure that all containers of hazardous chemicals are properly labeled in accordance with GHS labeling requirements.
Labels must include:
- Product Identifier (chemical name or mixture name)
- Signal Word (e.g., “Danger” or “Warning”)
- Hazard Statements (e.g., “Causes severe burns”)
- Precautionary Statements (e.g., “Wear protective gloves”)
- Pictograms (standardized hazard symbols)
- Manufacturer’s Information (name, address, contact details)
Secondary containers (e.g., spray bottles, buckets, or transfer containers) must also be labeled with at least the product identifier and hazard warnings.
Common Mistakes to Avoid:
- Using worn-out or illegible labels.
- Not labeling secondary containers.
- Removing or defacing labels on original containers.
3. Provide Safety Data Sheets (SDS)
Employers are required to keep Safety Data Sheets (SDSs) for all hazardous chemicals in the workplace up to date. SDSs must be readily accessible to all employees during working hours and should follow the 16-section format established by OSHA’s Globally Harmonized System (GHS).
Best Practice: Keep digital and printed copies of SDSs in a central location and ensure employees know where to find them.
4. Implement a Written Hazard Communication Program
Employers must develop and maintain a written Hazard Communication Program (HCP) that includes:
- A list of all hazardous chemicals present in the workplace.
- Details on labeling and SDS access.
- Procedures for handling non-routine tasks involving hazardous chemicals.
- Steps for informing outside contractors of potential chemical hazards.
- Employee training requirements.
The HCP must be reviewed and updated annually or whenever new hazardous chemicals are introduced into the workplace.
5. Conduct Employee Training on Hazard Communication
Employers must train employees on:
- How to read and interpret chemical labels and SDSs.
- The health and physical hazards associated with hazardous chemicals.
- The proper use of Personal Protective Equipment (PPE) when handling chemicals.
- Emergency procedures for chemical spills, leaks, and exposure.
- Safe handling, storage, and disposal of chemicals.
Training must be provided:
- Before an employee begins work with hazardous chemicals.
- Whenever new hazardous chemicals are introduced.
- At least once a year as a refresher.
Best Practice: Keep training records for each employee to ensure OSHA compliance and facilitate future refresher sessions.
6. Communicate Chemical Hazards in Multi-Employer Worksites
If contractors or subcontractors are working on-site, the employer must:
- Inform them about hazardous chemicals present in the work area.
- Share SDSs and labeling information.
- Provide precautionary measures they should take to stay safe.
Example: If a construction site has paint removers with hazardous fumes, the main contractor must warn subcontractors and provide SDSs.
7. Prepare for Non-Routine Tasks and Emergencies
Employers must have procedures in place for handling non-routine tasks involving hazardous chemicals.
Employees must be trained on:
- How to safely perform special tasks (e.g., cleaning confined spaces, maintenance work).
- How to handle chemical spills, leaks, and emergencies.
- Proper PPE and first-aid measures in case of exposure.
Best Practice: Conduct emergency response drills to ensure employees know how to react in real-world situations.
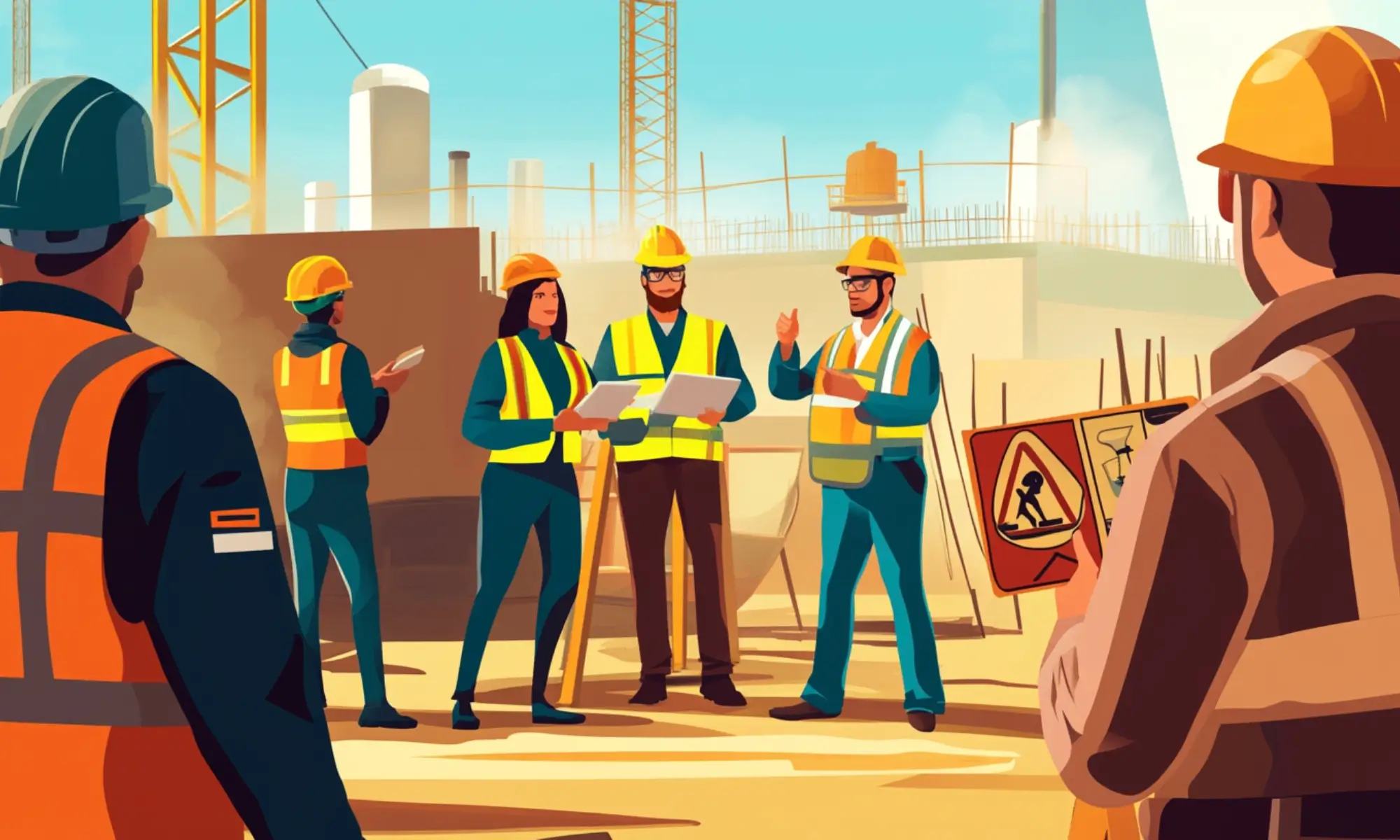
Common HAZCOM Violations and How to Avoid Them
The Hazard Communication Standard (HAZCOM) is one of OSHA’s most frequently cited workplace safety violations. Failure to comply with HAZCOM regulations can result in serious penalties, workplace accidents, and employee health risks. Below, we outline the most common HAZCOM violations and provide actionable solutions to ensure compliance. Top 5 Most Common HAZCOM Violations:
1. Failure to Provide Safety Data Sheets (SDSs) to Employees
Violation: Employers fail to maintain or provide Safety Data Sheets (SDSs) for hazardous chemicals.
Solution:
- Ensure SDSs are available for every hazardous chemical in the workplace.
- SDSs must be readily accessible to all employees during work hours.
- Store both digital and printed copies of SDSs in a central location.
- Train employees on how to find and use SDSs when handling chemicals.
Pro Tip: Use an electronic SDS management system to keep all records up to date and accessible.
2. Not Labeling Hazardous Chemicals Properly
Violation: Chemical containers lack proper labeling, making it difficult for employees to identify hazards.
Solution:
Ensure all primary and secondary containers are labeled according to GHS (Globally Harmonized System) standards.
Labels must include:
- Product Identifier (Chemical Name)
- Signal Word (“Danger” or “Warning”)
- Hazard Statements (E.g., “May cause severe burns”)
- Precautionary Statements (E.g., “Wear gloves, avoid inhalation”)
- Pictograms (OSHA-approved hazard symbols)
- Manufacturer’s Information (Name, address, contact info)
Common Mistakes to Avoid:
- Using faded, worn-out labels
- Not labeling secondary containers (e.g., spray bottles, transfer containers)
- Removing or defacing labels on original containers
Pro Tip: Use industrial-grade, waterproof labels for durability in harsh environments.
3. Lack of Employee Training on Chemical Hazards
Violation: Employees are not trained on HAZCOM, SDSs, or chemical safety procedures.
Solution:
Provide initial and annual HAZCOM training to all employees.
Training must cover:
- How to read SDSs and labels
- Safe chemical handling and storage
- Personal Protective Equipment (PPE) usage
- Emergency response for spills and exposures
- Recognizing physical and health hazards
Pro Tip: Keep detailed records of training sessions, including dates, topics covered, and employee participation.
4. No Written Hazard Communication Program (HCP)
Violation: Employers fail to develop or maintain a written Hazard Communication Program (HCP), as required by OSHA.
Solution:
Employers must create a written HCP that outlines:
- A list of all hazardous chemicals in the workplace
- Labeling and SDS management procedures
- Training requirements for employees
- Non-routine task safety procedures
- Multi-employer worksite communication guidelines
Pro Tip: OSHA often requests a written HCP during inspections—ensure yours is updated annually and easily accessible.
5. Failure to Update SDSs or Remove Outdated Information
Violation: Companies fail to update SDSs when new chemicals are introduced or when new safety information becomes available.
Solution:
Review SDSs annually and update them when:
- A new hazardous chemical is introduced
- The chemical composition of a product changes
- OSHA or the manufacturer updates safety information
Ensure outdated SDSs are replaced immediately and that employees are informed of changes.
Pro Tip: Assign a dedicated safety officer to track SDS updates and compliance.
The Consequences of HAZCOM Violations
- OSHA Fines & Citations – Penalties for non-compliance can range from thousands to hundreds of thousands of dollars.
- Workplace Accidents – Mislabeled or unidentified chemicals can lead to toxic exposures, explosions, and chemical burns.
- Legal Liability – Employers can face lawsuits from injured employees due to failure to provide proper hazard communication.
- Reputational Damage – A history of HAZCOM violations can harm company credibility and employee trust.
Fact: HAZCOM is consistently one of the top 10 most-cited OSHA violations every year due to poor chemical management practices.
Conclusion: The Importance of HAZCOM Compliance
HAZCOM is a critical safety regulation that protects workers from hazardous chemical exposure by ensuring clear communication of risks. Employers must provide proper labeling, up-to-date SDSs, comprehensive training, and a written hazard communication program to remain compliant and maintain a safe work environment.
By following OSHA’s HAZCOM standards and aligning with the GHS, businesses can minimize chemical-related risks, prevent accidents, and ensure workplace safety for all employees.
Key Takeaways
- HAZCOM is OSHA’s “Right-to-Know” Law that mandates chemical hazard communication.
- Employers must classify chemicals, provide labels & SDSs, and train workers.
- The Globally Harmonized System (GHS) standardizes labeling & SDS formats.
- A written hazard communication program is required for compliance.
- Non-compliance can result in OSHA fines, workplace injuries, and legal penalties.
By prioritizing HAZCOM compliance, businesses can enhance safety, protect workers, and avoid costly penalties. 🚧⚠️
This article was crafted following Google’s guidelines for helpful content, ensuring originality, clarity, and value while maintaining SEO best practices for optimal visibility.