Working at height is one of the most hazardous activities in many industries, from construction and maintenance to telecom and warehousing. Every year, numerous accidents and fatalities occur due to falls—most of which are preventable by adhering to essential requirements for working at heights. This is where the Hierarchy of Control for Height Work comes into play.
The hierarchy is a systematic framework designed to manage risks by prioritizing the most effective safety measures. It helps employers and safety professionals minimize or eliminate fall hazards by addressing them at the root. In this comprehensive guide, we break down each level of control, offering actionable insights, examples, and best practices to keep workers safe.
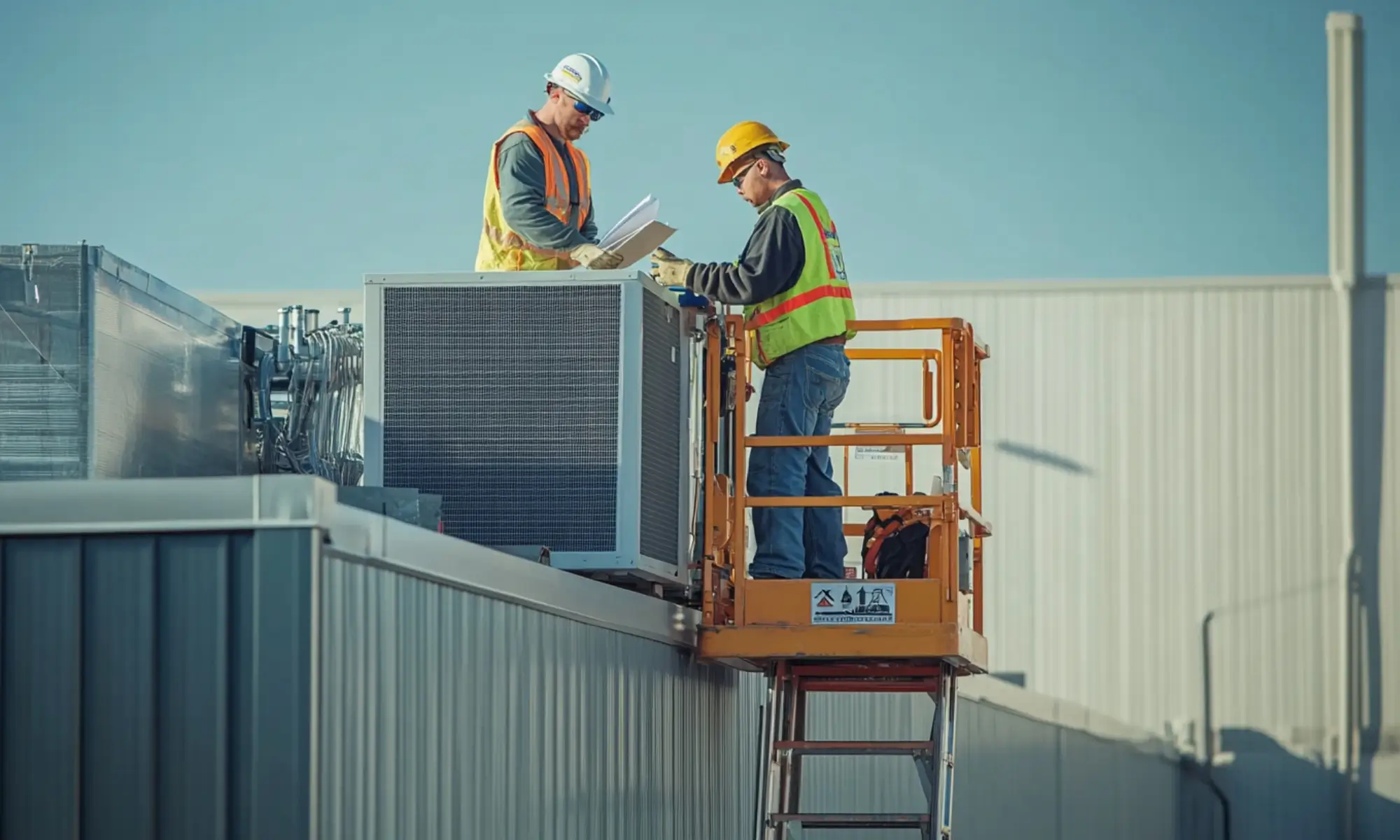
Hierarchy of Control for Height Work
The Hierarchy of Control is a structured approach to managing hazards. It ranks control measures from most to least effective and is widely endorsed by organizations like OSHA, HSE (UK), and the Canadian Centre for Occupational Health and Safety.
The five levels in the hierarchy are:
- Elimination
- Substitution
- Engineering Controls
- Administrative Controls
- Personal Protective Equipment (PPE)
Why Following the Hierarchy Is Essential
Ignoring or skipping levels in the hierarchy increases the likelihood of incidents. A comprehensive safety program should layer controls—starting with elimination and working down to PPE—to ensure maximum protection.
By prioritizing proactive rather than reactive measures, organizations can:
- Reduce workplace injuries and fatalities
- Improve compliance with legal regulations (e.g., OSHA, HSE)
- Lower insurance costs and liability risks
- Foster a strong safety culture
Let’s examine each of these in the context of height-related work.
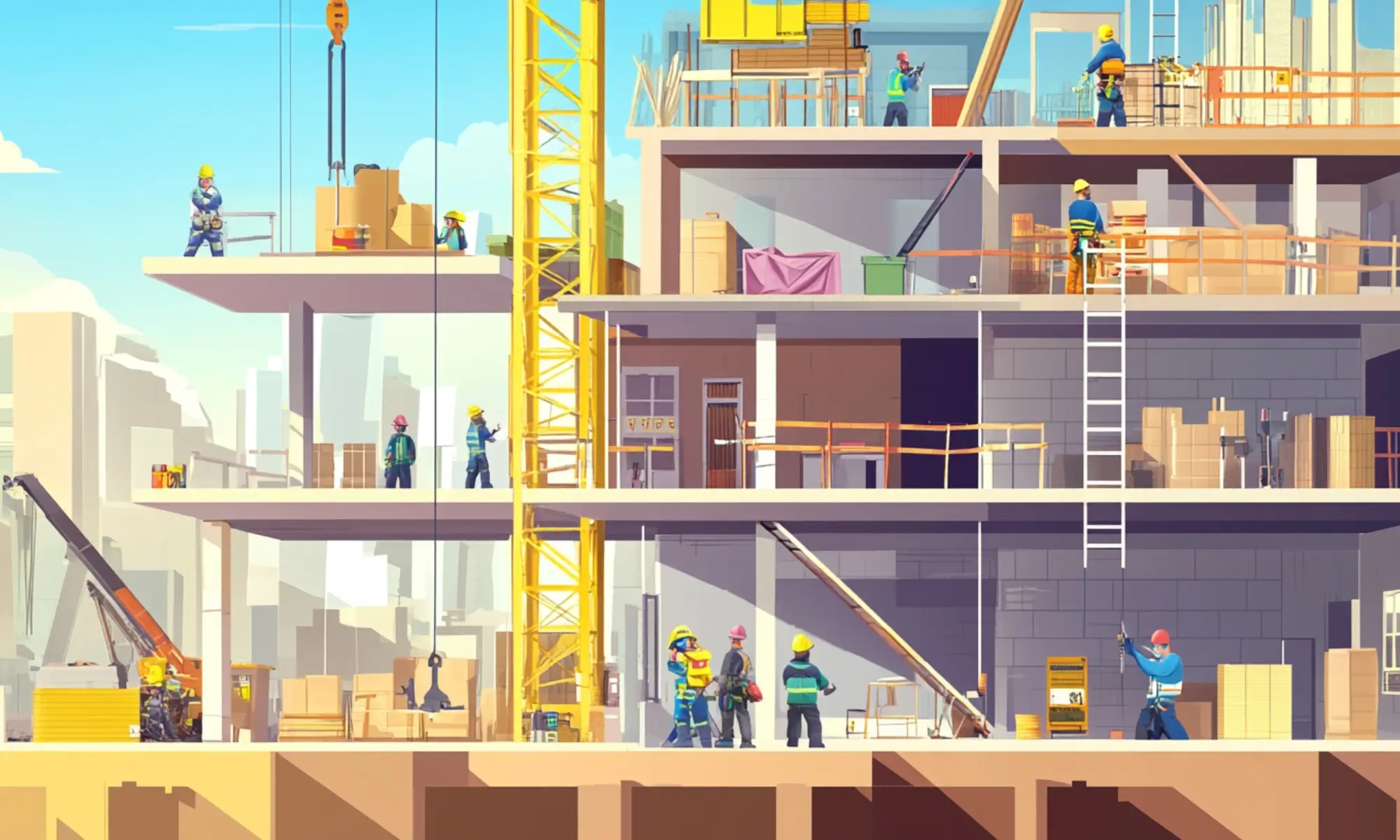
1. Elimination: Remove the Hazard Entirely
Elimination means completely removing the hazard by changing how a task is performed so that working at height is no longer needed. It focuses on redesigning the task, environment, or process to avoid exposure to the risk in the first place.
Examples:
Instead of installing lighting fixtures on a high ceiling that require workers to use ladders or scaffolds, opt for:
- Wall-mounted or lower-height lighting that can be safely accessed from the ground.
Why It’s the Most Effective Control:
- No height, no risk: If there’s no need to be elevated, there’s no fall hazard to manage.
- No reliance on human behavior: Unlike PPE or administrative controls, elimination doesn’t depend on workers to act safely—it removes the risk entirely.
- Reduced maintenance risk: Not only is the installation safer, but future maintenance can also be done without climbing.
Benefits Beyond Safety:
- Often results in greater efficiency and lower long-term costs.
- Reduces the need for complex fall protection systems or extensive training.
2. Substitution: Replace the Hazard
Substitution involves replacing a high-risk task, material, or tool with a safer alternative. Unlike elimination, which removes the hazard entirely, substitution still consists in working at height or a similar task—but it significantly reduces the level of risk involved.
Examples:
Instead of climbing a ladder to clean gutters or change signage:
- Use long-handled or extendable tools that allow the work to be done from the ground.
- Replace manual roof inspections with drones or telescopic cameras to minimize the need for workers to be physically elevated.
Why It’s an Effective Control:
- Reduces exposure to risk: Tasks are modified to reduce the likelihood or severity of a fall.
- Minimizes time at height: When elevation is still required, substitution may reduce the frequency, duration, or difficulty of the task.
- Encourages innovation: Opens the door to using newer, safer technologies and methods.
Key Consideration – Avoid Introducing New Hazards:
Substituted methods or tools must be evaluated carefully:
- A heavy extendable tool might introduce ergonomic risks like muscle strain or repetitive motion injuries.
- A new material or device might create other risks (e.g., chemical, visual, or stability hazards).
Always conduct a risk assessment of the substitute before implementation.
When to Use It:
- During task planning, equipment upgrades, or maintenance reviews.
- If elimination isn’t feasible but you still want to significantly lower the risk.
Benefits Beyond Safety:
- Promotes efficiency and may reduce task time.
- Enhances worker confidence by providing safer ways to perform tasks.
- May result in cost savings from reduced PPE needs or fewer safety incidents.
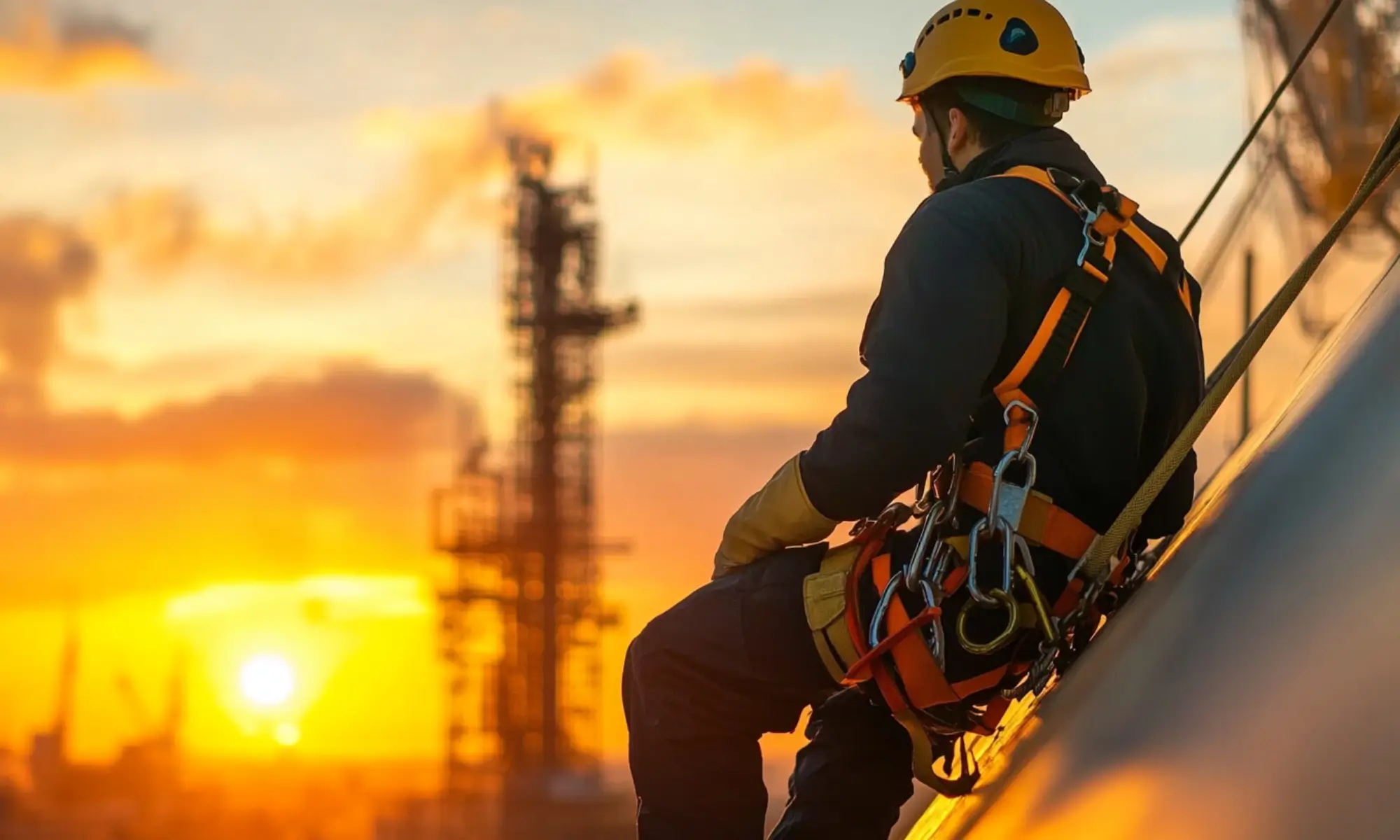
3. Engineering Controls: Isolate People from Hazards
Engineering controls are physical modifications to equipment, structures, or the work environment that create a barrier between the worker and the hazard. While the hazard still exists, these controls are designed to prevent direct contact or exposure, making the task safer without relying heavily on human behavior.
Examples:
Instead of requiring workers to use ladders on open edges or rooftops:
- Install permanent guardrails around elevated work areas.
- Use scaffolding with edge protection and stable platforms.
- Implement mechanical access systems such as aerial lifts or cherry pickers that offer secure workspaces at height.
Why It’s an Effective Control:
- Physical barrier = physical protection: Engineering controls don’t just reduce the risk—they actively prevent it by separating the worker from the hazard.
- More reliable than behavioral measures: Unlike training or PPE, these controls don’t rely on workers remembering to act safely.
- Standardizes safety: Consistent design features like guardrails or access systems apply to everyone who uses the space.
Key Considerations for Implementation:
- Ensure all equipment and installations comply with safety standards (e.g., OSHA, HSE, EN).
- Engineering controls should be regularly inspected and maintained to ensure continued effectiveness.
- Not all barriers are equal—choose controls based on the specific task, height, and work environment.
When to Use It:
- If elimination or substitution isn’t feasible.
- During the design or modification phase of structures, machinery, or workspaces.
- In environments where frequent work at height is required (e.g., construction, warehousing, maintenance).
Benefits Beyond Safety:
- Creates a consistent and predictable safety environment.
- Reduces the need for constant supervision or refresher training.
- Enhances worker confidence, productivity, and comfort when operating at height.
4. Administrative Controls: Change How People Work
Administrative controls focus on altering human behavior and workplace practices to reduce the risk of injury. Unlike elimination or engineering controls, these methods don’t remove the hazard, but they manage exposure to it through policies, procedures, training, and supervision.
Examples:
Instead of relying solely on physical controls:
- Develop and enforce safe work procedures for tasks performed at height.
- Implement a permit-to-work system to ensure tasks are authorized and reviewed before starting.
- Schedule work during favorable weather conditions to avoid wind, rain, or poor visibility.
- Conduct pre-task briefings and routine safety training to refresh knowledge.
Why It’s an Important Control:
- Improves awareness: Reinforces the importance of safe practices through training and supervision.
- Supports other controls: Strengthens the effectiveness of engineering or PPE by ensuring correct use.
- Flexible implementation: Can be adapted to suit different tasks, environments, and teams.
Key Considerations for Implementation:
- Must be well-documented, communicated, and enforced.
- Regular training updates and competency evaluations are critical.
- Procedures must be realistic and practical, not just written for compliance.
- Requires strong supervision and monitoring to ensure effectiveness.
When to Use It:
- As an added layer of protection when physical controls are in place.
- When elimination, substitution, or engineering solutions are not practical or fully effective.
- In dynamic work environments where conditions change frequently.
Benefits Beyond Safety:
- Promotes a strong safety culture by embedding safe practices into daily operations.
- Encourages team accountability and proactive risk identification.
- Enhances communication and coordination, especially in multi-contractor or high-risk sites.
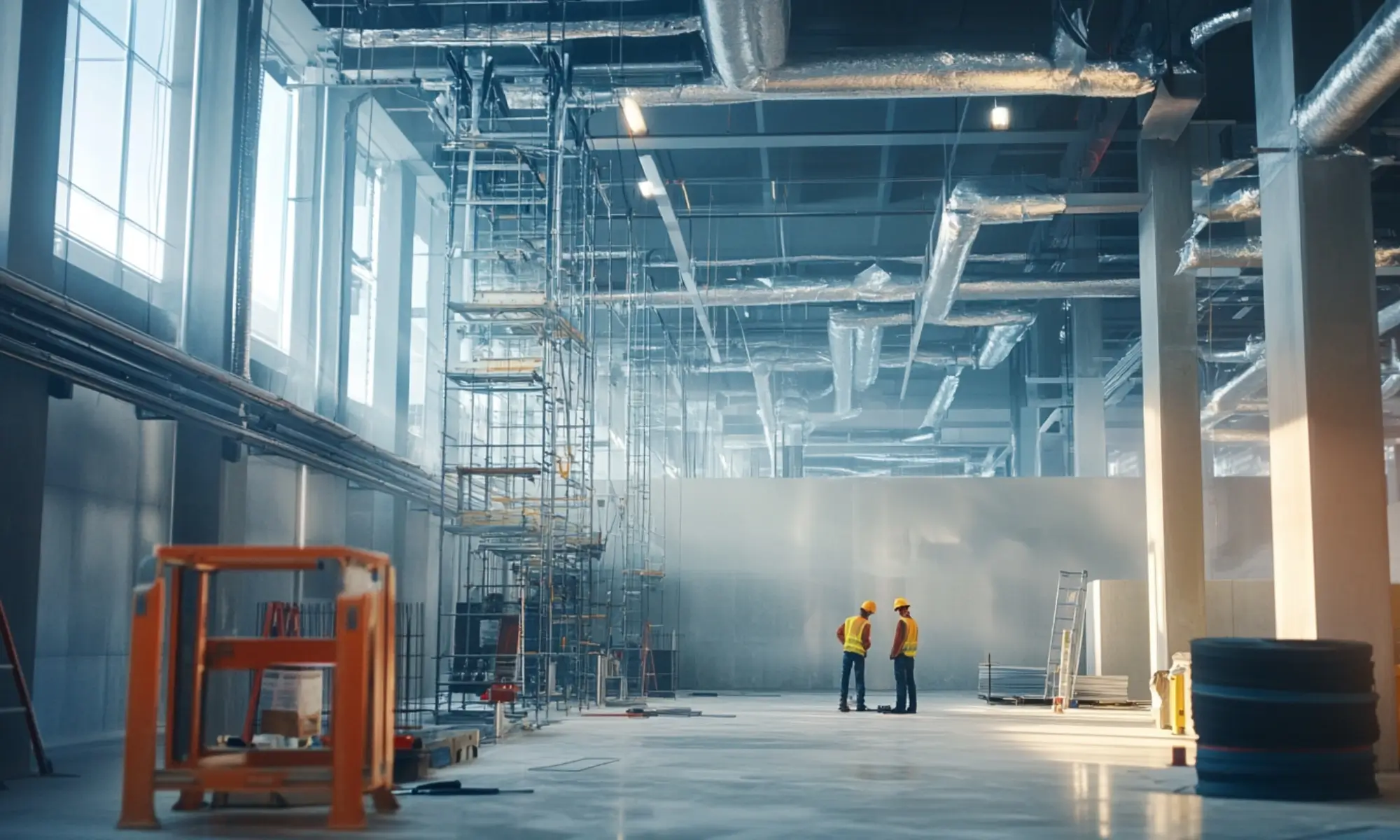
5. Personal Protective Equipment (PPE): The Last Line of Defense
Personal Protective Equipment (PPE) is used when the hazard cannot be eliminated or adequately controlled by other means. It serves as the last barrier between the worker and a potential injury. While PPE doesn’t eliminate the hazard, it reduces the severity of injury if an incident occurs.
Examples:
For workers at height, typical PPE includes:
- Full-body fall arrest harnesses with lanyards and shock absorbers
- Anchorage connectors to secure the harness to a safe point
- Helmets with chin straps to protect against head injuries during falls or dropped objects
- Non-slip footwear to improve grip and stability on ladders or elevated platforms
Why It’s the Least Effective Control:
- Hazard still exists: PPE doesn’t remove or reduce the risk—it only protects the worker if something goes wrong.
- Relies on human behavior: Effectiveness depends on correct use, fit, and maintenance.
- No prevention, only mitigation: It doesn’t stop a fall—it may only reduce the injury caused by one.
Key Considerations for Implementation:
PPE must be:
- Properly selected for the specific task and environment
- Fitted to the individual worker
- Regularly inspected, cleaned, and maintained
Workers must be trained on:
- How to use PPE correctly
- How to inspect it before use
- Emergency procedures in case of equipment failure
When to Use It:
- When other controls (elimination, substitution, engineering, or administrative) cannot fully mitigate the risk.
- As a backup protection—never as the only safety measure.
- In high-risk situations where exposure to hazards is unavoidable or unpredictable.
Benefits Beyond Safety:
- Provides reassurance to workers in hazardous environments.
- Demonstrates organizational commitment to worker protection.
- Supports legal compliance with occupational safety regulations.
Real-World Example: Applying the Hierarchy on a Rooftop HVAC Installation
A company needs to install and maintain a new HVAC system on the roof of a commercial building. Here’s how each level of the hierarchy of control can be strategically applied to minimize fall hazards and ensure worker safety:
1. Elimination – Remove the Need to Work at Height
- Action Taken: Evaluate alternative system designs that can be installed at ground level or within mechanical rooms inside the building.
- Outcome: In some cases, compact or modular HVAC systems may be placed at accessible levels, eliminating the need to access the roof entirely.
2. Substitution – Use Safer Alternatives
- Action Taken: Where rooftop installation is required, use prefabricated HVAC modules that can be assembled on the ground and lifted in place using cranes.
- Outcome: Reduces the amount of on-the-job work, limiting exposure time for workers.
3. Engineering Controls – Provide Physical Protections
Action Taken:
- Install permanent guardrails and toe boards around the rooftop work area.
- Add fixed ladders with safety cages for controlled roof access.
- Use mobile elevated work platforms (MEWPs) for access and installation, where feasible.
Outcome: Workers are physically protected from fall hazards during installation and future maintenance.
4. Administrative Controls – Adjust Work Practices
Action Taken:
- Develop a site-specific safe work procedure for rooftop tasks.
- Require a permit-to-work system and pre-job risk assessments.
- Schedule work during low-wind, dry conditions to reduce weather-related risks.
- Ensure workers are trained and supervised.
Outcome: Reduces the likelihood of unsafe actions or decision-making on site.
5. Personal Protective Equipment (PPE) – Equip Workers Properly
Action Taken:
- Workers use full-body harnesses with fall arrest systems anchored to certified roof anchors.
- Wear helmets, hi-vis vests, and non-slip footwear during all rooftop operations.
Outcome: Provides protection if other controls fail or in unguarded areas (e.g., during initial setup or temporary work zones).
By layering control measures from most to least effective, the organization significantly reduces the risk of falls, protects workers at every stage of the project, and complies with relevant safety regulations. This approach also fosters a proactive safety culture and sets a benchmark for future high-risk tasks.
Conclusion
The Hierarchy of Control for Height Work isn’t just a compliance requirement—it’s a practical tool for saving lives. By applying its principles from the planning phase to daily operations, employers can build safer environments where risks are minimized and confidence is maximized.
Takeaway: Always aim for the highest level of control possible. When you can’t eliminate the risk, manage it wisely—because safety from heights is never an afterthought.