Health, Safety, and Environment (HSE) professionals are vital in ensuring workplace safety and preventing accidents. They are responsible for developing and implementing safety protocols, conducting risk assessments, and promoting a culture of safety in the workplace. If you’re preparing for an HSE job interview, you must be well-versed in common HSE interview questions and answers to give yourself the best chance of success.
This blog will provide a comprehensive list of HSE interview questions and answers that will help you ace your interview and land your dream job in the HSE field. Whether you’re a seasoned HSE professional or just starting your career, this guide will give you the knowledge and confidence you need to succeed in your next HSE job interview. So, let’s dive in!
HSE Interview Questions & Answers
Preparing for an HSE job interview can be nerve-wracking, especially if you’re unsure what to expect. To help you ace your HSE interview, we’ve compiled a list of common HSE interview questions and answers.
What inspired you to pursue a career in HSE?
My inspiration for pursuing a career in HSE stemmed from my interest in creating a safe and healthy work environment for all employees. I believe that a strong HSE culture promotes well-being and contributes to an organization’s overall success. Additionally, the dynamic nature of HSE regulations and standards and the opportunity to positively impact people’s lives motivated me to pursue a career in this field.
How do you ensure compliance with safety regulations?
Ensuring compliance with safety regulations involves a multi-faceted approach, which includes the following:
- Staying informed: I make it a priority to stay updated on current laws, regulations, and industry standards. This may involve attending workshops, conferences, or subscribing to relevant publications and newsletters.
- Developing and implementing policies and procedures: I work closely with the management team to develop and implement comprehensive safety policies and procedures that adhere to the applicable regulations.
- Training and education: Providing regular training and educational sessions to employees is essential for ensuring compliance. This includes training on new policies, procedures, and equipment, as well as refresher courses for existing employees.
- Regular inspections and audits: Conducting routine inspections and audits of the workplace helps identify potential non-compliance issues and hazards. These inspections also allow us to evaluate the effectiveness of our safety measures and make necessary improvements.
- Encouraging open communication: I strive to create an environment where employees feel comfortable reporting safety concerns or potential violations. This is crucial for addressing issues promptly and maintaining a strong safety culture.
- Corrective and preventive actions: When non-compliance is identified, I work with the relevant parties to develop and implement corrective actions to address the issue. Additionally, we analyze the root cause and take preventive measures to avoid similar incidents in the future.
- Documentation: Maintaining accurate and up-to-date records of all safety-related activities, such as training sessions, inspections, and incidents, is essential for demonstrating compliance during regulatory inspections or audits.
How do you identify potential safety hazards?
Identifying potential safety hazards involves a systematic and proactive approach. Here are some key steps I take to identify hazards:
- Risk assessment: Conducting regular risk assessments helps to identify hazards that may be present in the workplace. This process involves evaluating work processes, equipment, materials, and the work environment to determine potential risks.
- Inspections and audits: Regular workplace inspections and safety audits are essential for identifying hazards that might not be obvious during day-to-day operations. This involves inspecting equipment, workstations, storage areas, and other relevant aspects of the work environment.
- Employee input: Encouraging open communication and feedback from employees is crucial, as they often have first-hand knowledge of potential hazards in their work areas. Providing a reporting system where employees can anonymously report safety concerns can be helpful in identifying hazards.
- Incident and near-miss investigations: Investigating incidents and near-misses helps to identify hazards that may have contributed to the event. Thorough investigations can reveal underlying issues and prevent future incidents.
- Job hazard analysis (JHA): A JHA is a method of breaking down a job into its individual steps and then identifying the hazards associated with each step. This process helps to pinpoint potential hazards and implement appropriate control measures.
- Reviewing industry data and best practices: Analyzing accident statistics, industry trends, and best practices can provide insights into potential hazards and effective preventive measures.
- Consultation with experts: In some cases, it may be necessary to consult with external experts, such as industrial hygienists, ergonomists, or safety engineers, to identify specific hazards and recommend appropriate controls.
By combining these approaches, I can effectively identify potential safety hazards and take appropriate action to mitigate risks and protect employees.
Can you give an example of a safety project you have managed?
Certainly, I managed a safety project aimed at reducing slips, trips, and falls in a manufacturing facility. These incidents were one of the leading causes of workplace injuries at the facility. Here’s an overview of the project:
- Data collection and analysis: I began by analyzing the incident reports and injury data to identify trends and patterns. This helped me understand the most common causes and locations of slips, trips, and falls within the facility.
- Risk assessment: Next, I conducted a thorough risk assessment of the areas with the highest frequency of incidents. This included evaluating factors such as flooring materials, lighting, housekeeping practices, and the presence of trip hazards like cables or uneven surfaces.
- Employee involvement: I engaged employees through focus groups and surveys to gather their insights on potential hazards and suggestions for improvement. This helped to identify contributing factors that may not have been apparent during the risk assessment.
- Developing a plan: Based on the findings, I developed a comprehensive plan to address the identified hazards. This included installing slip-resistant flooring, improving lighting, implementing a more rigorous housekeeping schedule, and organizing cable management solutions.
- Training and communication: I organized training sessions to educate employees on the new safety measures and proper procedures to prevent slips, trips, and falls. I also developed visual aids and signage to reinforce safe behaviors and remind employees of potential hazards.
- Monitoring and evaluation: After implementing the plan, I monitored the effectiveness of the changes by tracking incident rates, conducting periodic inspections, and gathering feedback from employees. This allowed us to make any necessary adjustments and ensure that the improvements were effective in reducing slips, trips, and falls.
As a result of this project, the facility experienced a significant decrease in slip, trip, and fall-related incidents, leading to a safer work environment and reduced costs associated with workplace injuries.
How do you motivate employees to prioritize safety?
Motivating employees to prioritize safety requires a combination of strategies that create a strong safety culture and encourage individual responsibility. Here are some ways I motivate employees to prioritize safety:
- Leadership commitment: Demonstrating management’s commitment to safety is crucial in setting the tone for the entire organization. By consistently prioritizing safety in decision-making and communicating its importance, employees are more likely to follow suit.
- Training and education: Providing regular, engaging, and relevant safety training helps employees understand the importance of safety, learn best practices, and develop the skills needed to work safely.
- Open communication: Encouraging open communication and feedback channels allows employees to express their concerns, report hazards, and suggest improvements. This helps them feel more involved in the safety process and reinforces the importance of their contributions.
- Positive reinforcement: Recognizing and rewarding employees who demonstrate safe behaviors, report hazards, or contribute to safety improvements can be a powerful motivator. This can include verbal recognition, awards, or incentives such as bonuses or gift cards.
- Employee involvement: Involving employees in safety committees, risk assessments, or improvement projects helps them feel a sense of ownership in the safety program and motivates them to prioritize safety in their daily tasks.
- Clear expectations and accountability: Establishing clear safety expectations and holding employees accountable for their actions helps create a culture of responsibility. This can be achieved through regular performance reviews, addressing unsafe behaviors, and celebrating successes.
- Sharing success stories and lessons learned: Communicating the results of safety initiatives, as well as lessons learned from incidents or near-misses, helps employees understand the impact of their efforts and the importance of continued vigilance.
- Personalizing safety: Encouraging employees to consider the personal consequences of unsafe behaviors, such as the potential impact on their families and loved ones, can be a powerful motivator for prioritizing safety.
By implementing these strategies, I strive to create a culture where employees understand the importance of safety, feel empowered to contribute to a safer workplace, and are motivated to prioritize safety in their daily work.
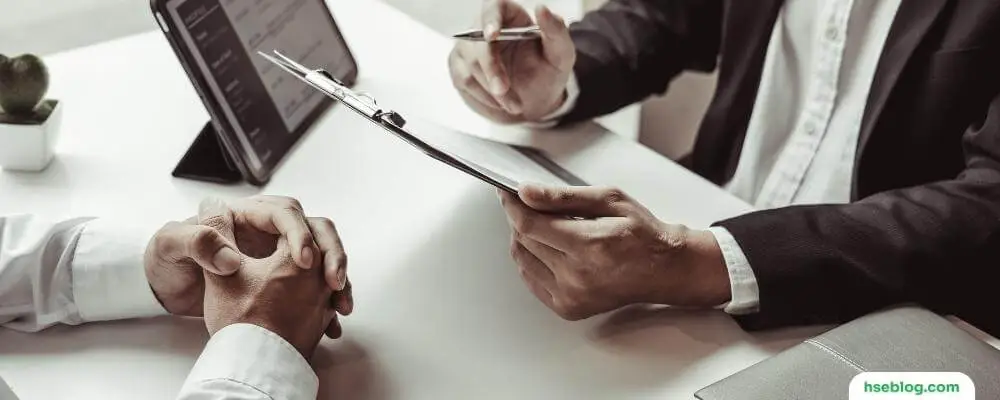
How do you handle safety incidents and emergencies?
Handling safety incidents and emergencies requires a well-prepared and structured approach to ensure an effective response, minimize the impact, and prevent future occurrences. Here are the steps I take to handle such situations:
- Preparation and planning: Developing and maintaining an Emergency Response Plan (ERP) is essential for handling emergencies effectively. This plan outlines the procedures, roles, and responsibilities of all parties involved in responding to various types of emergencies.
- Immediate response: When an incident or emergency occurs, the first priority is to ensure the safety of all individuals involved. This may include administering first aid, evacuating the area, or activating emergency systems such as fire alarms or emergency shut-off valves.
- Incident stabilization: Once the immediate threats have been addressed, the next step is to stabilize the situation to prevent further damage or injuries. This may involve isolating the affected area, shutting down equipment, or engaging emergency response teams such as firefighters or hazardous material teams.
- Notification and communication: It’s crucial to notify the appropriate internal and external parties, including management, employees, emergency responders, and regulatory agencies, as required by law. Clear communication and coordination are essential during this phase.
- Investigation: Conducting a thorough investigation is necessary to determine the root cause of the incident or emergency. This involves collecting evidence, interviewing witnesses, and analyzing the contributing factors. The findings from the investigation will help identify areas for improvement and prevent future occurrences.
- Corrective actions: Based on the investigation findings, I work with the relevant parties to develop and implement corrective actions to address the root causes of the incident. This may involve revising policies and procedures, updating equipment, or providing additional training to employees.
- Follow-up and evaluation: After implementing corrective actions, I monitor their effectiveness and make any necessary adjustments to ensure the incident does not recur. This may involve conducting additional audits, inspections, or employee feedback sessions.
- Continuous improvement: The learnings from safety incidents and emergencies are used as opportunities for continuous improvement in the organization’s safety program. This helps to build a strong safety culture and prevent similar incidents in the future.
By following these steps, I can effectively handle safety incidents and emergencies, minimize their impact, and use them as opportunities to improve the overall safety performance of the organization.
How do you stay up-to-date with safety regulations and best practices?
Staying up-to-date with safety regulations and best practices is essential for ensuring a safe work environment and maintaining compliance. Here are some ways I keep myself informed:
- Professional associations and organizations: I am an active member of professional associations related to HSE, such as the American Society of Safety Professionals (ASSP) or the National Safety Council (NSC). These organizations offer resources, webinars, and updates on regulatory changes and best practices.
- Conferences and workshops: Attending industry conferences, workshops, and seminars allows me to learn from experts, network with other professionals, and stay informed about the latest trends and best practices in the HSE field.
- Industry publications: Subscribing to relevant industry publications, such as Safety+Health Magazine or Occupational Health & Safety, helps me stay informed about changes in regulations, new technologies, and best practices.
- Government and regulatory agency websites: I regularly visit websites of regulatory agencies, such as OSHA, EPA, and NIOSH, to stay updated on new regulations, guidelines, and recommendations.
- Online forums and social media: Joining online forums and following HSE-related social media accounts allows me to engage with other professionals, discuss industry trends, and stay informed about new developments.
- Networking and peer connections: I maintain a strong network of professional contacts in the HSE field, which helps me exchange knowledge, share experiences, and stay informed about best practices and regulatory changes.
- Continuous learning: I am committed to lifelong learning and frequently enroll in courses, certifications, or workshops to enhance my skills and stay current with the latest developments in the HSE field.
By utilizing these resources and strategies, I can stay up-to-date with safety regulations and best practices, ensuring that I can effectively manage HSE responsibilities and maintain a safe and compliant work environment.
What is Safety?
Safety refers to being protected from harm, danger, or injury. In the context of occupational health and safety, it is the condition where employees are free from hazards in the workplace that could cause injury, illness, or harm. Safety also involves implementing measures to prevent accidents or incidents and promoting a culture of safety in the workplace.
What is the accident?
An accident is an unplanned event or incident that results in damage, injury, illness, or death. In occupational health and safety, an accident is an undesired event resulting in personal injury or property damage. Accidents can occur in any environment, including the workplace, at home, on the road, and in public places. Accidents can be caused by various factors, such as human error, mechanical failure, environmental hazards, and unsafe working conditions. Preventing accidents is an essential goal of HSE programs in all industries.
What is the risk?
Risk is the probability of harm or loss due to an activity or event. In the context of occupational health and safety, the risk is the likelihood of injury or illness resulting from exposure to hazards in the workplace. Risk assessment is a critical component of HSE programs, which involves identifying hazards, evaluating the likelihood and severity of potential harm, and implementing measures to control or mitigate the risks.
What is the hazard?
A hazard is anything that has the potential to cause harm, injury, illness, or damage to property or the environment. Hazards can be physical, chemical, biological, ergonomic, or psychosocial. In occupational health and safety, hazards are typically associated with the workplace environment and can include unsafe working conditions, exposure to hazardous chemicals or substances, poor ergonomic design of equipment or workstations, and psychosocial hazards such as workplace bullying or harassment.
What is the incident?
An incident is an unplanned or undesired event that results in, or could have resulted in, harm to people, damage to property or the environment, or loss to the organization. Incidents can vary in severity, ranging from minor injuries to major disasters. In the context of Health, Safety, and Environment (HSE), an incident is any event that risks workers’ health and safety or the environment.
What is the injury?
An injury is a damage or harm caused to a person’s body, either accidentally or intentionally. In Health, Safety, and Environment (HSE), injuries can occur in the workplace due to accidents or incidents resulting in physical harm, such as cuts, burns, fractures, or sprains. Work-related injuries can also be psychological, such as stress, anxiety, or depression, resulting from workplace harassment or bullying.
How do you conduct a risk assessment?
A risk assessment typically involves the following steps:
- Identifying hazards
- Determining who might be harmed and how
- Evaluating the risks and deciding on control measures
- Recording the findings and implementing the necessary controls
- Reviewing and updating the assessment regularly or when significant changes occur
Can you explain the hierarchy of hazard controls?
The hierarchy of hazard controls is a system for prioritizing and selecting the most effective control measures to eliminate or reduce the risk of a hazard. It consists of the following levels in descending order of effectiveness:
- Elimination
- Substitution
- Engineering controls
- Administrative controls
- Personal protective equipment (PPE)
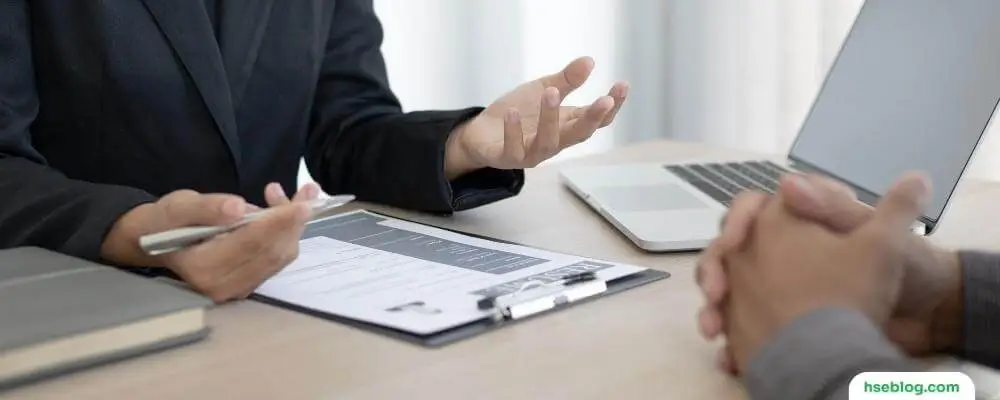
How do you promote a positive safety culture within an organization?
Promoting a positive safety culture involves:
- Demonstrating visible commitment from leadership
- Encouraging employee involvement and participation
- Providing training and resources for employees
- Establishing clear communication channels
- Recognizing and rewarding good safety performance
- Implementing a fair and consistent approach to discipline
What is a safety policy?
A safety policy is a formal statement that outlines an organization’s commitment to ensuring the health and safety of its workers, customers, and the environment. A safety policy sets out the general principles, objectives, and responsibilities for managing safety within an organization. It typically includes information on how safety risks will be identified, assessed, and controlled and procedures for reporting incidents and near misses.
What is a safety tag?
A safety tag is a visual communication tool used in workplaces to warn workers of potential hazards, provide instructions for safe operation, and identify equipment or areas that are currently unsafe or out of service. Safety tags are typically attached to equipment or locations using a string or wire. They may include information about the specific hazard, required personal protective equipment (PPE), and safe use or maintenance instructions. Safety tags are an important component of a comprehensive safety program and are used to help prevent accidents and injuries in the workplace.
What is a safety program?
A safety program is a comprehensive set of policies, procedures, and practices designed to ensure the safety and health of workers in a workplace. A safety program typically includes a variety of components, such as:
- Hazard identification and risk assessment: identifying potential hazards in the workplace and evaluating the risk associated with each hazard.
- Engineering controls: implementing physical measures to control or eliminate hazards, such as ventilation systems or machine guards.
- Administrative controls: establishing procedures and policies to manage hazards, such as training programs and standard operating procedures.
- Personal protective equipment (PPE): providing workers with appropriate PPE to protect them from hazards that other means cannot eliminate.
- Incident reporting and investigation: establishing procedures for reporting accidents and near misses and investigating the root causes of incidents to prevent future occurrences.
- Emergency preparedness and response: developing plans and procedures to respond to emergencies, such as natural disasters or workplace accidents.
- Ongoing monitoring and evaluation: regularly assessing the safety program’s effectiveness and making necessary adjustments to improve its performance.
A safety program is designed to create a safe and healthy work environment that protects workers from injury and illness.
What is a safety audit?
A safety audit is a systematic, objective review of a workplace’s safety management systems, policies, and practices to assess their effectiveness in preventing accidents and injuries. Safety audits are typically conducted by internal or external auditors who are trained in safety management and have expertise in identifying potential hazards and evaluating the adequacy of safety controls.
What is attitude?
Attitude refers to a person’s perspective, beliefs, and feelings toward a particular subject or situation. It encompasses the way individuals think, feel, and behave toward something, which can be influenced by their experiences, values, and personal biases. A positive attitude generally involves optimism, openness, and a willingness to learn and adapt, while a negative attitude may involve pessimism, resistance to change, and a closed-minded approach.
In an HSE context, attitude is important because it can impact safety culture and behavior, and a positive safety attitude is essential for creating a safe and healthy workplace.
What is emergency planning?
Emergency planning refers to preparing for, responding to, and recovering from an emergency or crisis. This includes identifying potential risks and hazards, developing emergency response procedures, training employees to respond to emergencies, and regularly testing and updating emergency plans.
What is work at height?
Work at height refers to any task performed at a location with a risk of falling from one level to another. This can include working on a ladder, scaffolding, roof, or other elevated surfaces. Work at height is common in many industries, including construction, maintenance, and telecommunications.
What is a work permit system?
The work permit system is a formal process that is used to control and manage high-risk activities in the workplace. It involves using written documents or permits to authorize specific work activities and ensure that they are carried out safely and in accordance with established procedures.
Under the work permit system, a permit is issued by a designated person in authority, such as a supervisor or safety officer, before any high-risk work activity is undertaken. The permit outlines the specific work to be carried out, identifies any hazards or risks associated with the work, and specifies the safety measures that must be taken to control those hazards.
What is a confined space?
A confined space is an enclosed or partially enclosed space that is not designed for continuous human occupancy and has limited means of entry or exit. Confined spaces can be found in various industries, such as construction, manufacturing, and transportation.
Examples of confined spaces include storage tanks, silos, pipelines, sewers, and manholes. Confined spaces may also have other hazards, such as hazardous gases or materials, low oxygen levels, or limited ventilation.
What is excavation?
Excavation is the process of digging, removing, or moving earth, rock, or other materials from a site to create a hole, trench, or another opening in the ground. Excavation is used in various industries, including construction, mining, and archaeology.
What is scaffolding?
Scaffolding is a temporary structure used in construction, renovation, or maintenance work to provide a platform for workers to perform their tasks at an elevated height. It is typically made up of metal tubes or poles, and wooden boards or metal planks are placed across them to create a stable and secure working surface.
What is gas cutting?
Gas cutting is cutting metal materials by heating them with oxygen and combustible gas, such as acetylene. The heat generated by the reaction between oxygen and gas melts the metal, which is then blown away by a jet of oxygen to create a clean cut.
What is sandblasting?
Sandblasting cleans or prepares a surface using compressed air to force abrasive materials against it at high speeds. Depending on the specific application, the abrasive materials used in sandblasting include sand, glass beads, aluminum oxide, or other materials.
What is welding?
Welding is a fabrication process involving joining two or more pieces of metal or other materials by applying heat, pressure, or both to fuse them. The process creates a strong, permanent bond between the materials, often essential for building structures, manufacturing machinery, and other industrial applications.
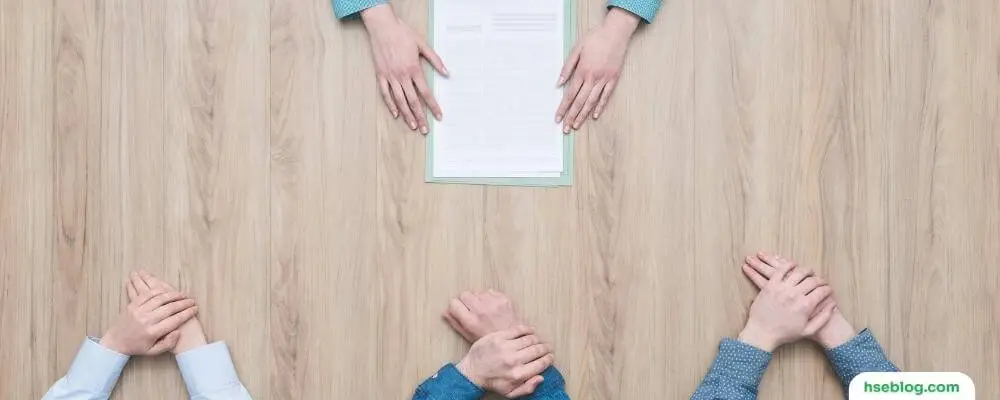
What is UEL?
The Upper Explosive Limit (UEL) is the highest concentration of a flammable substance, such as a gas or vapor, in the air that can potentially cause an explosion if an ignition source is present. The concentration of the substance above the UEL is considered too “rich” to support an explosion, as the air-fuel mixture is too concentrated to support combustion.
What is painting?
Painting is applying a liquid or a powder coating material onto a surface to protect, decorate or enhance its appearance. It is often performed after surface preparation techniques such as sandblasting, which removes any previous coatings, rust, or dirt, to ensure proper adhesion and a smooth surface for painting.
What is LEL?
The Lower Explosive Limit (LEL) is the minimum concentration of a flammable substance, such as a gas or vapor, in the air below which combustion will not occur in the presence of an ignition source. This means the air-fuel mixture is too lean to support combustion and will not ignite even if an ignition source is present.
What is manual handling?
Manual handling is lifting, carrying, moving, or supporting objects or materials by hand or bodily force. This can include lifting, pushing, pulling, and carrying heavy or bulky objects. Manual handling is common in many industries, including construction, manufacturing, healthcare, and retail.
What is grinding?
Grinding is a material removal process that uses an abrasive wheel or belt to cut, shape, or smooth a workpiece surface. It is commonly used in manufacturing, construction, and metalworking industries.
A grinder is a machine tool used for grinding, which typically consists of a motor, a grinding wheel or belt, and a work rest to support the workpiece during the grinding process. Grinders can be powered by electricity, pneumatic power, or gasoline engines and come in various sizes and designs for different applications.
What is housekeeping?
Housekeeping keeps a workplace clean, organized, and free from clutter or hazards. It involves maintaining a clean and tidy work environment, including work surfaces, floors, and storage areas, to ensure that equipment, tools, and materials are in good condition and readily accessible.
What is personal protective equipment?
Personal protective equipment (PPE) is worn by individuals to protect themselves from potential hazards in the workplace. PPE is designed to protect the body from physical, chemical, electrical, or biological hazards that may be present in the workplace and can include items such as gloves, safety glasses, hard hats, respirators, earplugs, and safety shoes.
What is Crane?
A crane is a machine that lifts and moves heavy loads vertically and horizontally. Cranes are used in construction, manufacturing, shipping, and other industries to move heavy materials or equipment.
A typical crane consists of a base, a mast, a jib, and a hook or lifting mechanism. The crane base is typically mounted on wheels or tracks and provides stability for the machine. The mast is the vertical part of the crane that supports the jib, which is the horizontal arm that extends from the mast. The hook or lifting mechanism is attached to the jib and is used to lift and move loads.
What is a forklift truck?
A forklift truck is an industrial vehicle commonly used to lift and move heavy loads in warehouses, manufacturing plants, and other industrial settings. It is equipped with two forks or prongs at the front that can be inserted under a load and then lifted and transported to another location.
What is JSA?
JSA stands for Job Safety Analysis. It is a process to identify and analyze potential hazards associated with a particular job or task. JSA aims to develop and implement appropriate safety measures to minimize or eliminate the risks associated with the job.
During a JSA, each job step is analyzed to determine the potential hazards and the likelihood of those hazards occurring. The analysis considers the equipment and materials used, the job’s environment, and the tasks involved. Once the hazards have been identified, appropriate measures are developed and implemented to reduce the risk of injury or illness.
What are the duties of a supervisor?
The duties of a supervisor vary depending on the industry and the specific job role, but generally, a supervisor is responsible for managing and overseeing the work of a team or a group of employees. Some common duties of a supervisor include:
- Planning and organizing work: Supervisors are responsible for developing plans, setting goals, and organizing their team’s work to ensure that tasks are completed efficiently and effectively.
- Hiring and training employees: Supervisors often recruit and hire new employees and provide training and development opportunities to their team.
- Assigning tasks and delegating responsibilities: Supervisors assign tasks and delegate responsibilities to their team members to ensure that work is distributed evenly and completed on time.
- Monitoring performance: Supervisors regularly monitor the performance of their team members, provide feedback on their work, and make necessary adjustments to ensure that performance goals are met.
- Ensuring compliance with policies and procedures: Supervisors are responsible for ensuring their team members comply with company policies and procedures and relevant laws and regulations.
- Resolving conflicts: Supervisors often mediate conflicts between team members and work to resolve any issues that arise in the workplace.
- Reporting to higher management: Supervisors are responsible for reporting on their team’s performance and providing regular updates to higher management on progress and any issues that arise.
Overall, a supervisor is responsible for ensuring that their team performs their work to the best of their abilities and meets the goals and objectives set by the organization. They are crucial in ensuring the work is completed safely, efficiently, and effectively.
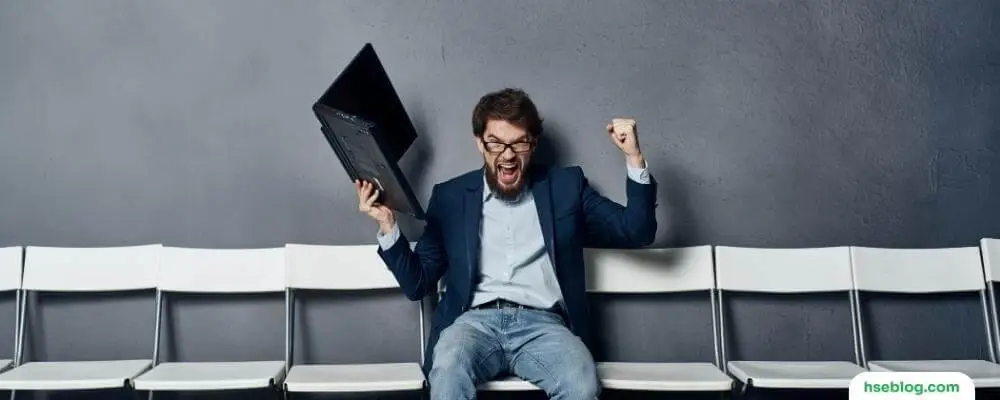
What are the duties of a safety officer?
A safety officer, also known as a health and safety officer, is responsible for promoting and maintaining safe working conditions in the workplace. Some of the key duties of a safety officer include the following:
- Conducting risk assessments: Safety officers are responsible for identifying potential hazards in the workplace and conducting risk assessments to determine the level of risk to employees.
- Developing and implementing safety policies and procedures: Safety officers develop and implement safety policies and procedures to prevent accidents and injuries in the workplace.
- Conducting safety inspections: Safety officers regularly inspect the workplace to ensure that safety policies and procedures are followed and identify potential hazards.
- Safety training: Safety officers provide safety training to employees to educate them on how to work safely and prevent accidents and injuries.
- Investigating accidents and incidents: Safety officers investigate accidents and incidents to determine the cause and make recommendations for preventing similar incidents in the future.
- Maintaining safety records: Safety officers maintain accurate records of safety inspections, incidents, and training to ensure that the organization complies with relevant regulations and standards.
- Collaborating with management and employees: Safety officers work closely with management and employees to promote a culture of safety in the workplace and ensure that everyone is aware of their role in maintaining a safe work environment.
Overall, the primary duty of a safety officer is to ensure that the workplace is safe and healthy for employees by identifying and mitigating potential hazards and promoting a safety culture.
What are the precautions for welding?
- Remove all combustion material from the place of welding.
- Clear the work area and wooden cover floor with fireproof mats. (welding mechanics should be kept within the visibility of the welders.
- Erect the fire resistance screen around the work.
- All welding cables should be thoroughly insulted.
- All welding mics shall be double-earthed.
- The welding area should be dry and free from water.
- Keep the fire extinguisher/sand.
- Use leather hand gloves, goggles, and helmets.
- Switch off the power when welding is stopped.
- Do not allow the helper to do welding.
- Do not shift the welding cable unless the electric power is switched off.
- Do not allow the helper to carry the welding. The welding cables’ terminal should be 3-cable with lugs and kept tight. Oxygen hose in black and acetylene hose in red in color as per standard.
- Welders should be adequately trained.
- Cylinders should be stored in a cold, dry place away from bottom heat and direct sunlight.
- Proper housekeeping and good ventilation in the working area.
- Smoking should be avoided in the welding area.
- Hose connection should be properly made.
- Barricade the work area and put a signboard.
- Rolling of cylinders should be avoided.
- A Flashback arrestor should be attached to each cylinder.
- Any leakage of the cylinder should be kept separately.
What are the precautions for gas cutting?
- Keep the fire extinguisher nearby.
- Keep a fire watch nearby.
- Remove all combustibles from the work area.
- Use all necessary PPE.
- Never put a welding gas cylinder inside a confined space.
- Hoses shall not be laid in pathways.
- The gas-cutting torch should have flashback arrestors.
- Gas test to be done to check for the presence of flammable gas on site.
- Good housekeeping and ventilation are necessary for the working area.
- Hose connections should be made properly.
What are the precautions for “sandblasting”?
- The compressed airline, hoses, and another fitting must install firmly without leaking the hose.
- Misuse compress should be avoided
- A fresh air hood or mask must be worn
- Housekeeping can be done periodically
- Fire extinguish her shall be kept nearby
- Dust mask ear plugs/muffs should be used
- No sandblasting shall be done on the floating roof tank in service.
- Use goggles & face shield
- The sandblasting operation must be gas-free
What is the precaution for “painting”?
- All flammable material should be cleared from the work area
- The required protective clothing and equipment must be worn
- Cartridge respirators shall always be worn
- Adequate ventilation is necessary
- Adequate washing facilities must be readily available
- Barrier cream should be applied to the skin
What are the hazards of welding?
- Eye injury
- Burn injury arc realization
- Electrical shock light arc radiation
- Heat, light, and radiation affect heat fume
- Poisonous gases chipped the price of welded metal
- Fire
- Explosion scattering
- Noise sparking
- Sparkling
- Flying sand
What are the hazards and injuries in manual handling?
- Cutting fingers due to sharp edges
- Burns, due to the handling of hot articles
- Foot injuries due to dropped articles
- Slipped disc due to improper posture in lifting the object
- Strains to wrist or fingers
- Sprains, wounds, hernias, fractures
- Cause of accidents in manual handling?
- Improper lifting
- Carrying too heavy loads
- Improper gripping
- Failure to use PPE
- Lifting greasy, oily, and irregular objects
- Poor physique
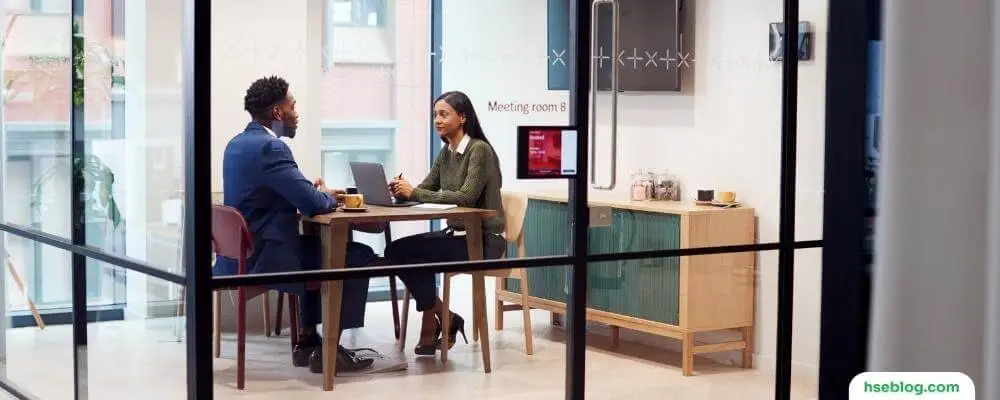
What precautions are needed to avoid the accident in manhandling
- Stand at a safe distance from the load
- Sharp edge and burns are removed before lifting a
- PPE such as safety gloves and safety shoes are to be
- If the weight is too heavy for one person to lift, he must seek assistance.
- The pathway is not blocked by obstacles while carrying the load.
- The different actions, movements, and forces are necessary while carrying the load.
- Modify the task by using hooks and crowbars.
- Mechanical equipment like cranes shall be used.
- Modify the objects
- Change the way things are used.
- Tips for manual handling?
- Plan
- Clear the path
- Move-in close to the load
- Secure your grip
- Hold your head upright
- Maintain standard curves of the spine
- Power the lift with legs and body weight
- Don’t twist
What are the causes of accidents in mechanical handling?
- The sudden failure of wire rope or a chain
- Slipping the load from the sling
- Swinging of the load at the time of lifting
- The load sometimes hits the man
What are the accidents in “poor housekeeping”?
- Men getting hit by falling from overhead
- Men slipping on greasy, wet, or dirty floor
- Men failing in open tank without a cover on the level floor
- Accidents due to poor lighting
- Fire accidents due to faulty electrical wires
What are the advantages of good housekeeping?
- It helps in the reduction of accidents, including fire accidents
- It saves the property damages
- It improves employee morale
- Better productivity
- The working area becomes presentable
- Human energy is conserved
- Visitors are very much satisfied
- The burden of the supervisor is reduced
How to care for and maintenance of hand tools?
- Tools must be kept clean and free from corrosion
- Keep metal parts lightly oiled
- Remove burrs from the edges of tools and heads of chisels.
- Tools that are not in use must be stored separately
- A good worker regularly inspects his tools
- Do not use tools without handles
How to prevent accidents of “power tools”?
- The operators should wear face shields or safety glasses
- Power tools should be placed in the storeroom after use
- Power tools should have protected by guards
- Pneumatic hoses or electric cables of power tools should not pass through passageways.
- The electrical power tools should be properly earthed
- Never horseplay with the hose of pneumatic tools
- Power tools machines should be maintained and operated correctly.
What are the causes of accidents with “hard tools”?
- Due to the wrong way of using tools.
- Due to the defective condition of tools
- Due to the failure to use the right tools for the right job
- Due to the wrong way of carrying tools
- Due to the strength of tools in Safety
What precautions are necessary for electrical work?
- All electrical installations shall be as per standard electricity rules
- Only competent persons should handle the electrical equipment.
- The equipment should be adequately earthed.
- All temporary electric lines should be drawn at least above man’s height
- The cable should be insulted entirely
- The cable should not have any joints
- Only connection for one point
- Good housekeeping in the area
- Fire protection equipment to be kept nearby
- Use rubber gloves and rubber boots
- Use good quality wire
- Power isolation close to the job
- Use a three-pin plug instead of a loose wire
- Never operate any electrical equipment with wet hands
- Never stand on wet surfaces while working on electrical equipment
- During thunderstorms, do not stand under the tree
- The proper signboard is necessary
- No person shall work on any live electrical conductor
- The switch shall only be put on by the person who switched it off
What are the hazards in construction?
- Fall of the person from the top and getting injured
- Fall of objects from the top and below person injury
- Fall of materials from the top and damage
- The person falls into the excavated pit
- The collapse of soil and below person gets an injury or may
- Damage to ug cables and sewage pipe
- The collapse of scaffolding and a person falling from a height get an injury.
- Electrical shock
- Fire and explosion
- Burn injury
- Health and lung problems
- Snakes Bite
- Poisonous gas
- Foreign body in the eye
What are the Causes of the accident in construction?
- Erection equipment failure
- Falling of persons from the height
- Electrical shocks
- Improper lighting
- Non-stop work by a worker
- Up safe work methods
- Collapsing of the earth during trench excavation
- Failure to use safety equipment
- Working a height without a safety belt
What are the General safety precautions in construction?
- Adequate first aid equipment should be kept ready.
- Adequate fire fighting equipment should be available
- All general electrical rules should be followed
- Suitable lighting arrangements should be necessary at night work
- Workmen at height should be wearing safety belts
- Workmen handling cement should be provided with goggles, rubber gloves, and rubber boots with nose masks.
- The moving parts of grinding machines used on the construction site should be covered with guards.
- The moving parts of grinding machines used on the construction site should be covered with guards.
- Excavated material should not be kept near the excavated
- For the concise duration of work, red flags must be hoisted, and for more period, red banners must be stretched
- Defective tools should not be used
- The worker should not carry tools in his hands when climbing a ladder
- Excavation should be guarded by suitable fencing
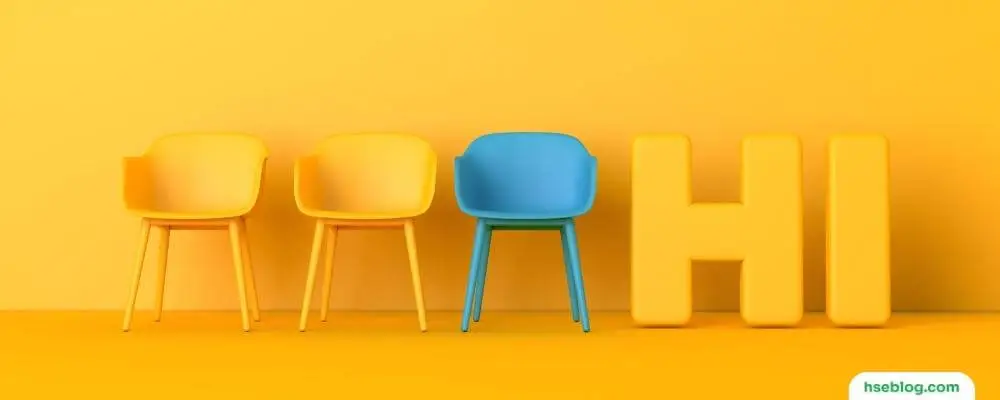
How to erect scaffolding?
- It should be erected on levels of firm ground
- It erected by a trained/skilled person
- It is constructed using metal pipes and wooden boards
- It should be designed and built from the excellent and sound material
- Not to be erected on loose earth
- Clamps should be fixed
- Properly bracing
- The sole plate is necessary for the base of the vertical pipe
- Safety precaution of scaffold?
- Wooden boards not be painted.
- The wooden board should not to any cracks.
- Check for rust in pipes/clamps
- Clamps should be fixed and good quality
- The boards thickness should be 3.4 cms, and no bending
- The construction must be rigid, properly based
- Use of good and sound materials
- The wooden bellies have no joint.
- Vertical poles should not be more than 6 feet
- Chains and ropes used for the suspension of scaffoldings
- Never throw any materials from a height
- Use a safety harness while working at above 6 feet
- Properly ties to be an arrangement
What control measures are necessary for confined space?
- Enter with airline bar sets
- Use 24v flameproof hand lamps
- A hole watch is to be kept near the manhole
- Keep firefighting equipment ready
- Gas test is to be done to check for oxygen level
- Provide blowers
- Don’t smoke in a confined space
- Use ropes and harness
- The spaces clean before entry
- Use non-sparking tools if there is any risk of flammable vapors being present.
Safety rules when using ladders?
- The footwear is not greasy, oily, or muddy and has a good grip on the rungs.
- When climbing or coming down, a ladder should face the ladder side and have both hands.
- Carry light tools in pockets in a shoulder bag.
- Hold on with at least a new hand if using both hands, then use a safety belt.
- Never climb higher than the third rung from the top on straight or second tired from the top of the extension ladder.
- The stepladder must be fully open and the divider locked.
- The metal ladder shall not be used near electrical equipment.
- The metal ladder shall not be placed on firm footing and at an angle of 75
- Any ladder found with a defect in any way should be marked Do not use
- The ladder shall not be placed in a box or drum.
- Rubber protection on the head and heel of a ladder is necessary.
Safety rules ensuring oxygen cylinders?
- Oxygen cylinders should not be kept near combustible materials.
- Oxygen cylinders should not be handled with grassy hands or gloves.
- Oxygen cylinders and their fittings should not be tested with oil-based soap solutions.
- Oxygen cylinders and other combustible gas cylinders should not be stored together.
- The top cover of the cylinder should be kept in position and screwed safely when not in use.
- Cylinders should not be used as rollers for moving materials.
- Oxygen must not be used for ventilating confined spaces.
Tips To Pass Health and Safety Interview
To successfully pass a health and safety interview, consider these tips to help you stand out as a knowledgeable and dedicated candidate:
- Research the company: Familiarize yourself with the company’s industry, size, and safety culture. Understanding the organization’s specific safety challenges will help you tailor your answers and demonstrate how your skills and experience can contribute to a safer work environment.
- Review regulations and standards: Be well-versed in the applicable safety regulations and standards for the company’s industry. This will showcase your expertise and commitment to staying informed about regulatory requirements.
- Prepare for common interview questions: Practice answering common HSE interview questions like the ones provided earlier in this conversation. Be ready to provide specific examples of your experience in managing safety projects, handling incidents, and implementing safety improvements.
- Use the STAR method: When answering behavioral questions, use the STAR (Situation, Task, Action, and Result) method to structure your responses. This helps you provide a clear and concise account of your experiences and the outcomes of your actions.
- Highlight your qualifications and certifications: Mention relevant HSE qualifications and certifications, such as OSHA training, Certified Safety Professional (CSP), or NEBOSH qualifications. This demonstrates your commitment to professional development and expertise in the field.
- Show your passion for safety: Throughout the interview, convey your enthusiasm for creating a safe work environment and your dedication to promoting a strong safety culture.
- Ask insightful questions: Prepare some thoughtful questions to ask the interviewer about the company’s safety culture, challenges, or recent safety initiatives. This shows your interest in the organization and your commitment to making a positive impact.
- Be professional and confident: Dress professionally, arrive on time, and maintain good eye contact and body language throughout the interview. Confidence in your abilities and expertise will help leave a positive impression on the interviewer.
- Follow up with a thank-you note: After the interview, send a thank-you note to the interviewer, expressing your gratitude for the opportunity and reiterating your interest in the role. This demonstrates your professionalism and eagerness to contribute to the company’s safety culture.
By following these tips, you can effectively showcase your skills, knowledge, and dedication to health and safety, increasing your chances of acing the interview and securing the position.