A Health and Safety Management System (HSMS) is a structured framework that helps organizations manage occupational health and safety (OH&S) risks, improve workplace safety, and ensure compliance with regulatory requirements. Effective health and safety management protects employees from injury and illness and contributes to increased productivity, improved morale, and reduced operational costs.
The success of an HSMS hinges on two critical phases: Planning and Implementation. Careful planning ensures that all potential risks are identified, assessed, and controlled, while effective implementation ensures that safety measures and policies are integrated into the organization’s daily operations. This article provides a detailed guide on planning and implementing a robust HSMS, including key steps, best practices, and common challenges to avoid.
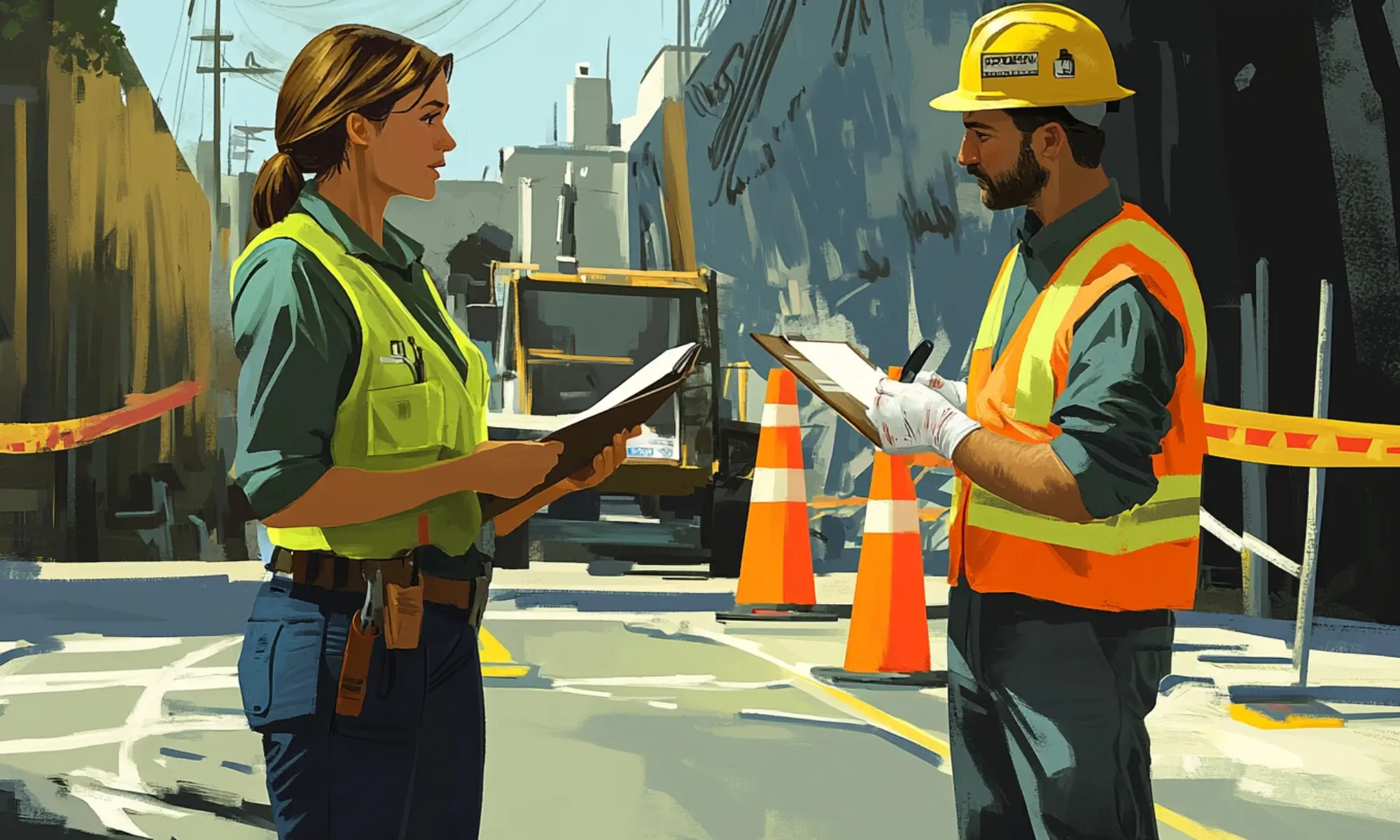
Planning a Health and Safety Management System
Planning is the foundation of an effective HSMS. It involves understanding the organization’s context, identifying hazards, setting objectives, and developing action plans. Proper planning ensures the system is tailored to the organization’s specific risks, legal requirements, and business goals.
1. Understanding the Organizational Context
Before developing an HSMS, it is essential to understand the internal and external factors that can influence health and safety culture and performance. This includes understanding the health and safety management system’s key elements, such as policy, risk assessment, implementation, and monitoring, which form the foundation of an effective system. This includes:
- Nature of the Business: The type of industry and the associated hazards (e.g., construction, manufacturing, healthcare).
- Size and Structure: Large, complex organizations may need more detailed safety processes than smaller businesses.
- Workforce Characteristics: Employee demographics, experience levels, and language differences may affect the effectiveness of safety programs.
- Regulatory Environment: Local, national, and international health and safety laws and standards (e.g., ISO 45001, OSHA) must be considered.
Understanding these factors ensures that the HSMS is aligned with the organization’s specific needs and that potential gaps in safety management are addressed from the outset.
2. Hazard Identification and Risk Assessment (HIRA)
Identifying hazards and assessing risks is a critical step in developing an HSMS. The goal is to identify all potential sources of harm and evaluate the likelihood and severity of each risk. Steps for Hazard Identification and Risk Assessment:
Identify Hazards:
- Physical hazards (e.g., machinery, noise, heat, electricity).
- Chemical hazards (e.g., toxic substances, flammable materials).
- Biological hazards (e.g., viruses, bacteria, mold).
- Ergonomic hazards (e.g., repetitive movements, poor workstation design).
- Psychosocial hazards (e.g., work-related stress, bullying).
Evaluate Risks:
- Assess the likelihood and consequences of each hazard.
- Use a risk matrix to classify risks as low, medium, or high.
Prioritize Risks:
- Focus on high-risk hazards first.
- Develop control measures according to the hierarchy of controls (elimination, substitution, engineering controls, administrative controls, personal protective equipment).
Example: In a manufacturing plant, noise levels exceeding 85 decibels may pose a risk of hearing loss. Engineering controls (e.g., installing noise barriers), administrative controls (e.g., rotating shifts to reduce exposure), and personal protective equipment (e.g., earplugs) could be implemented to mitigate the risk.
3. Legal and Regulatory Compliance
An HSMS must meet all applicable health and safety laws and regulations. This involves:
- Identifying local and international standards (e.g., ISO 45001, OSHA, EU directives).
- Understanding reporting requirements (e.g., incident reporting, worker health monitoring).
- Ensuring that the organization’s safety policies and procedures align with regulatory guidelines.
Example: Under ISO 45001, organizations are required to document procedures for hazard identification, incident investigation, and emergency preparedness. Failure to comply can lead to legal penalties and reputational damage.
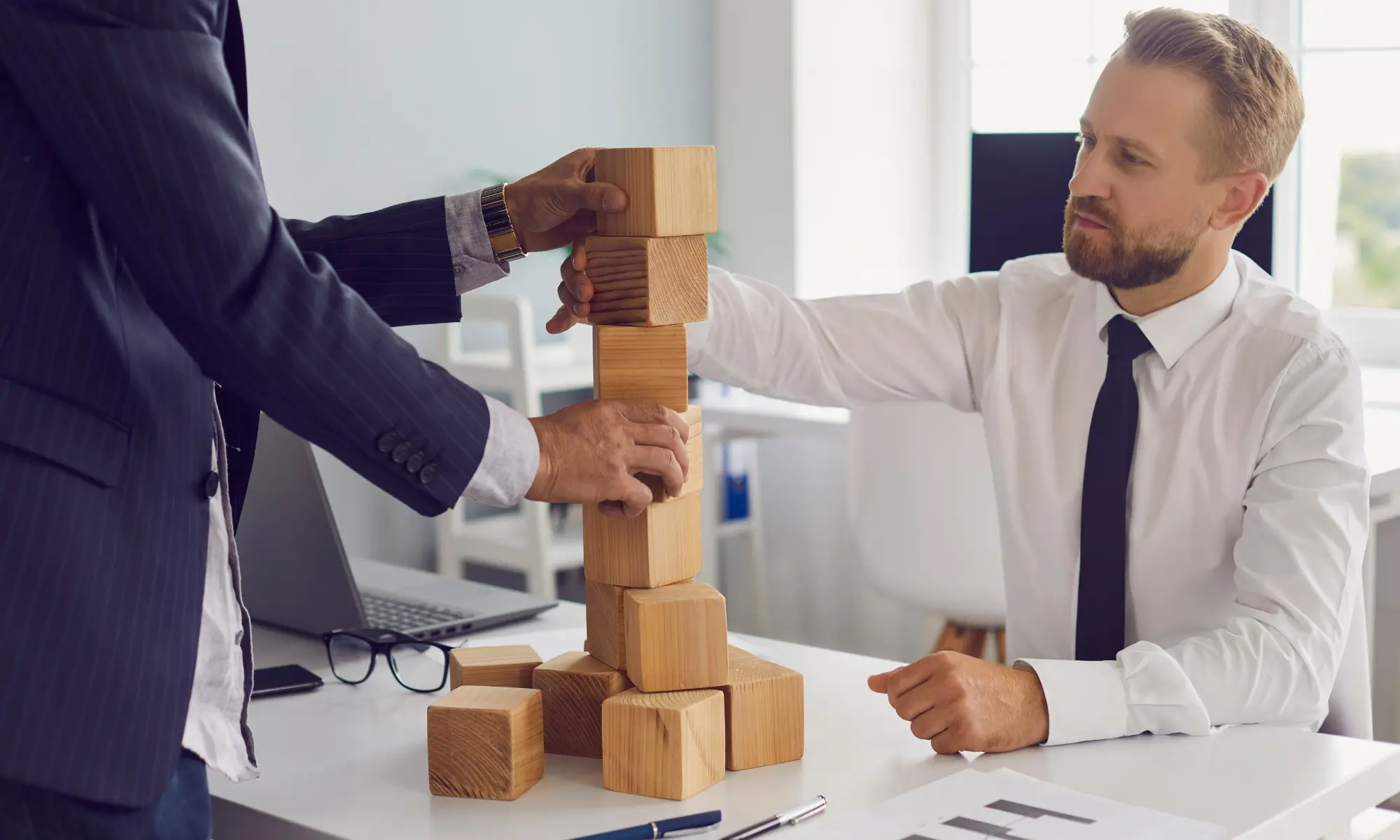
4. Setting Objectives and Performance Targets
Establishing clear health and safety objectives helps drive continuous improvement. Objectives should be:
- Specific: Clearly define the desired outcome (e.g., reduce lost-time injuries by 20%).
- Measurable: Track progress using key performance indicators (KPIs).
- Achievable: Ensure that objectives are realistic based on available resources.
- Relevant: Align objectives with the overall business goals and safety culture.
- Time-Bound: Set a deadline for achieving each objective.
Example Objectives:
- Reduce incident rate by 30% within one year.
- Provide safety training for 100% of employees by the end of the quarter.
- Implement machine guarding for all production equipment by June.
5. Developing an Action Plan
Once objectives are set, create a detailed action plan outlining the steps needed to achieve them. An effective action plan includes:
- Specific Actions: What needs to be done (e.g., conduct safety inspections, update safety training).
- Responsibilities: Who is accountable for each action (e.g., safety officer, department head).
- Resources: What tools, training, or financial support are needed.
- Timeline: When each action should be completed.
- Monitoring and Evaluation: How progress will be measured and adjusted.
Example:
Objective | Action | Responsible Person | Timeline | Resources |
---|---|---|---|---|
Reduce incidents by 30% | Introduce new PPE and conduct training | Safety Officer | Q2 | $5,000 budget |
Improve incident reporting | Implement digital reporting system | IT Manager | Q3 | Software license |
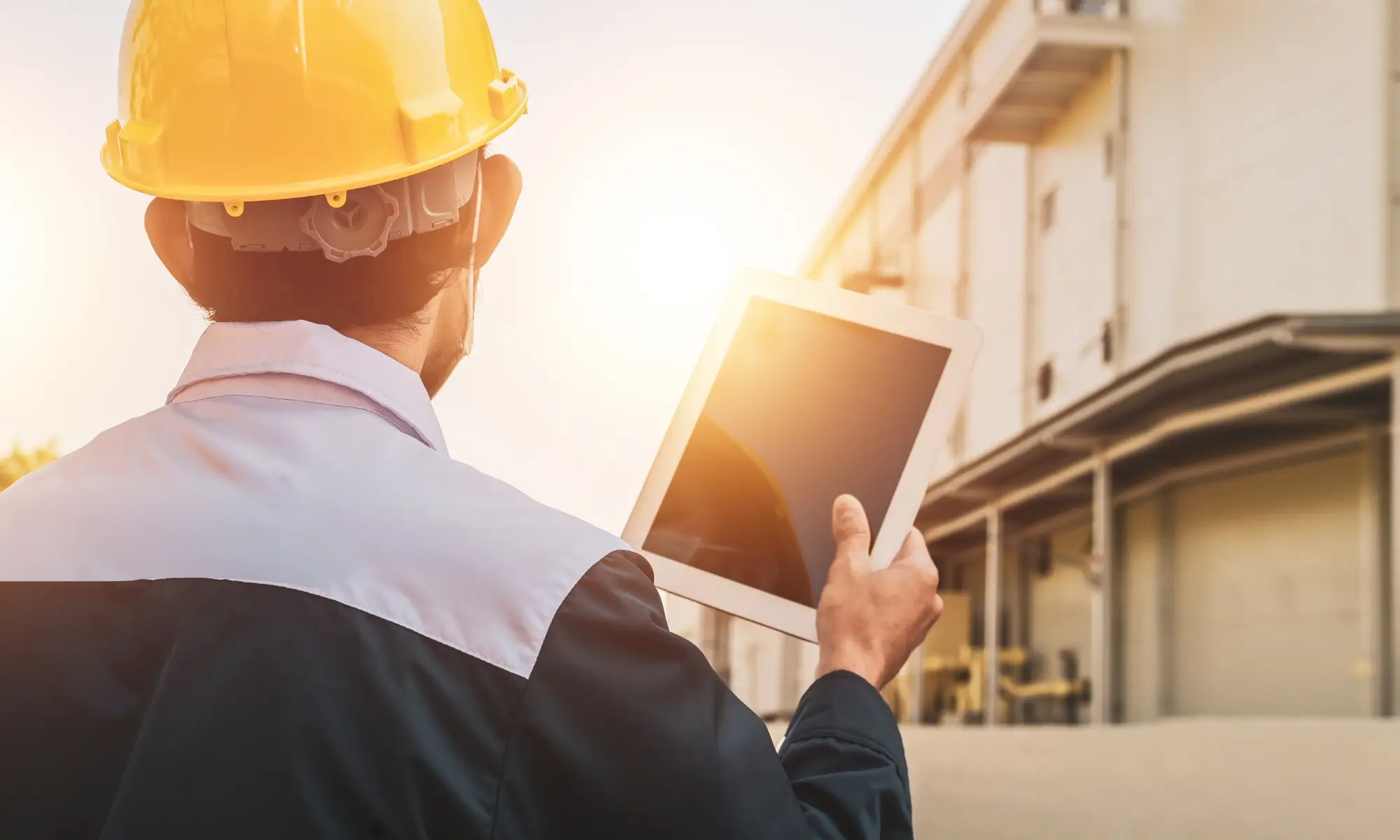
Implementing a Health and Safety Management System
Implementation involves putting the planned strategies and control measures into action. Successful implementation requires leadership commitment, employee participation, and ongoing monitoring.
1. Leadership Commitment and Responsibility
Senior management must demonstrate visible commitment to health and safety by:
- Allocating necessary resources (e.g., staffing, equipment, training).
- Actively participating in safety initiatives (e.g., attending safety meetings).
- Holding managers and supervisors accountable for health and safety performance.
Example: The CEO regularly attends safety committee meetings and provides funding for new safety equipment, reinforcing that safety is a core business priority.
2. Training and Competence
All employees should receive appropriate health and safety training to understand:
- Workplace hazards and associated risks.
- Safe work procedures and emergency protocols.
- How to use personal protective equipment (PPE).
- Incident reporting and investigation procedures.
Training should be tailored to different job roles and updated regularly. New employees must receive onboarding safety training, and refresher courses should be scheduled annually.
3. Communication and Worker Engagement
Establishing clear communication channels ensures that employees are aware of safety policies and procedures. Encourage worker participation by:
- Forming safety committees.
- Providing suggestion boxes for safety improvements.
- Encouraging workers to report hazards without fear of retaliation.
Example: A monthly safety meeting allows employees to discuss safety concerns and propose solutions.
4. Operational Controls
Operational controls ensure that safety measures are integrated into daily activities. This includes:
- Standard Operating Procedures (SOPs): Documented step-by-step guides for performing tasks safely.
- Emergency Preparedness: Conducting fire drills, first aid training, and evacuation simulations.
- Safety Inspections: Routine inspections to identify and correct hazards.
Example: A construction company may implement lockout/tagout procedures for heavy machinery to prevent accidental activation during maintenance.
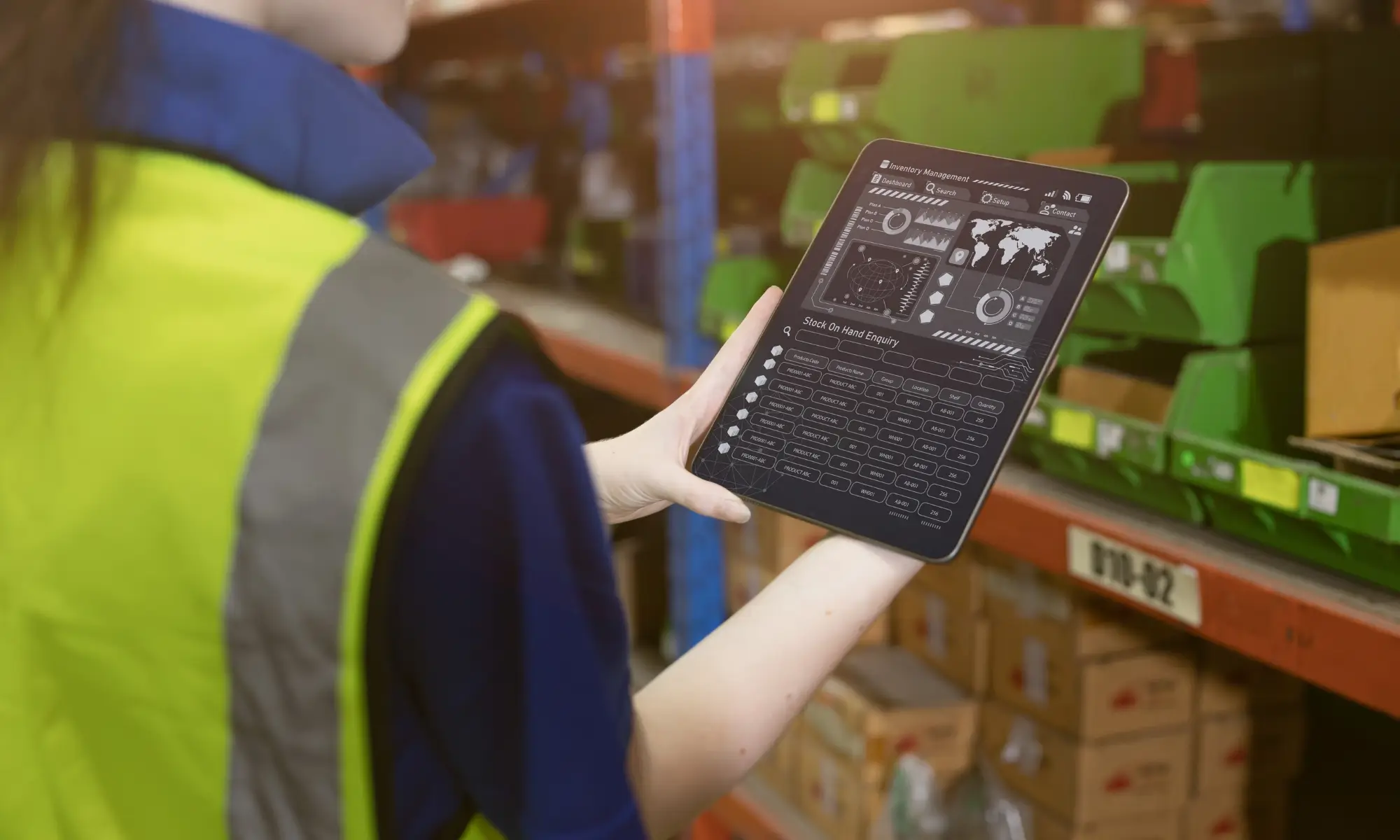
5. Incident Reporting and Investigation
Establish a formal process for reporting and investigating incidents:
- Encourage employees to report near-misses and safety concerns.
- Investigate all incidents to determine root causes.
- Implement corrective actions to prevent recurrence.
Example:
After a slip-and-fall incident, the investigation reveals that floor mats were missing. Installing slip-resistant mats prevents future accidents.
6. Monitoring and Measuring Performance
Regularly monitor safety performance using key metrics such as:
- Total Recordable Incident Rate (TRIR).
- Lost Time Injury Frequency Rate (LTIFR).
- Near-miss reporting rates.
Conduct periodic safety audits and management reviews to identify areas for improvement.
7. Continuous Improvement
The HSMS should evolve over time based on performance data, employee feedback, and industry best practices.
- Update procedures based on new regulations or incidents.
- Introduce new training programs as needed.
- Encourage innovation in safety practices.
Conclusion
A well-planned and effectively implemented Health and Safety Management System (HSMS) creates a safer work environment, reduces risks, and improves employee well-being. Organizations can protect their workforce, meet regulatory requirements, and drive continuous safety improvement plans by following a structured approach to planning and implementation.
Strong leadership, employee involvement, and continuous monitoring are the cornerstones of a successful HSMS. When health and safety become part of the organizational culture, businesses protect their employees and strengthen their overall performance and reputation.