Creating a safe workplace isn’t just about following rules—it’s about building a culture where safety is second nature. To do that, you must first recognize the risks. Hazards come in many forms: physical, chemical, ergonomic, or psychological. But how do you spot them before they cause harm?
This guide explores five proven methods for identifying hazards in the workplace—strategies that are practical, proactive, and built on real-world success. Whether you’re a safety officer, business owner, or concerned team member, these methods will help you take control and create a safer environment for everyone.
5 Ways to Identify Hazards in the Workplace
Workplace hazards don’t just endanger lives—they impact productivity, morale, and profit. According to OSHA, U.S. businesses spend nearly $1 billion per week on workers’ compensation for preventable injuries. Beyond the cost, accidents damage employee trust and can trigger legal and reputational consequences.
Identifying hazards early allows companies to implement preventive measures, reduce risks, and stay compliant with safety standards like OSHA, ISO 45001, or HSE regulations. Identifying workplace hazards is essential to ensuring employees’ safety and well-being. Here are 5 ways to identify workplace hazards:
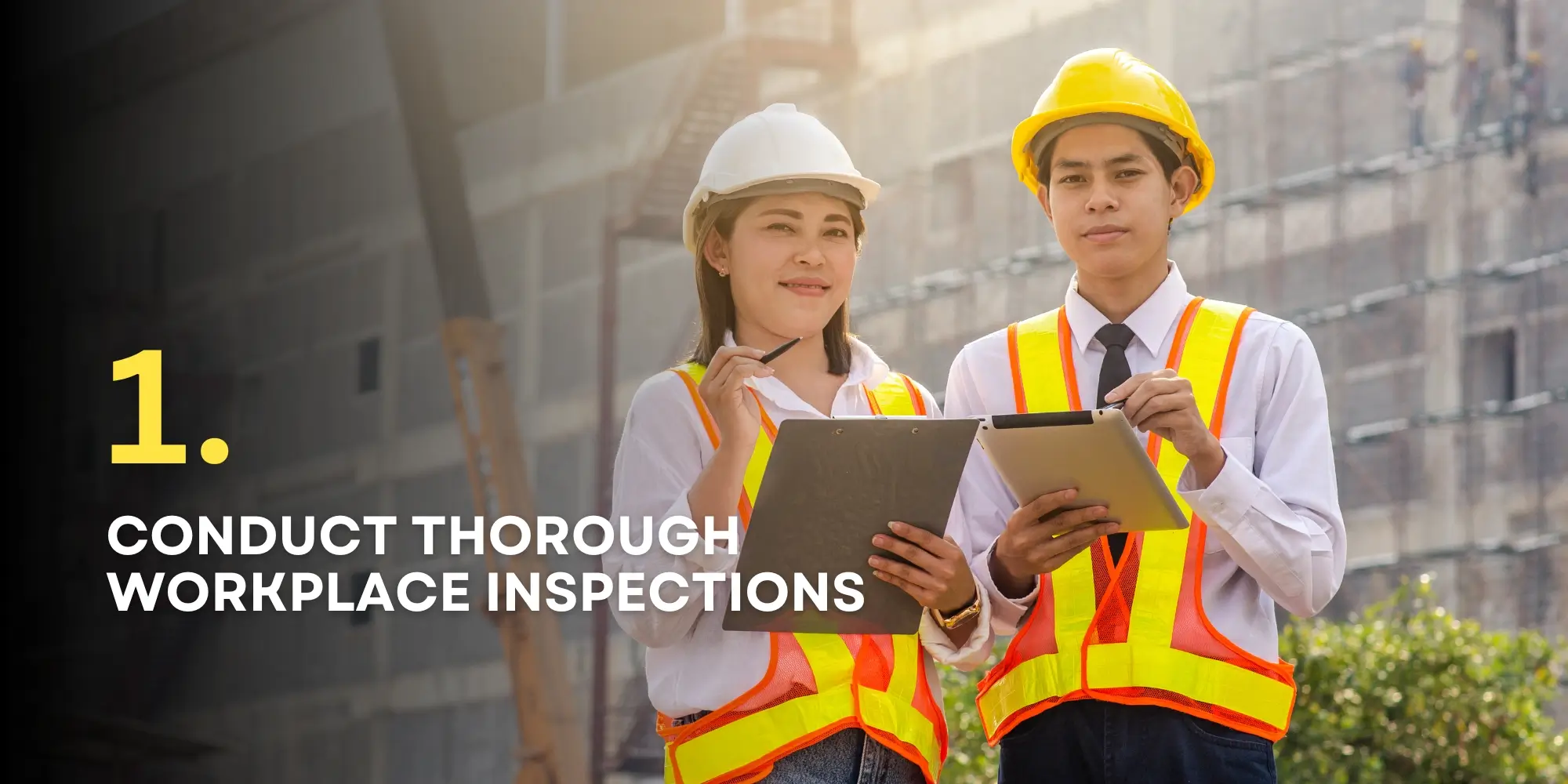
1. Conduct Thorough Workplace Inspections
Regular safety inspections are one of the most direct ways to identify existing and potential hazards. Inspections should be systematic and cover every aspect of the workplace—from machinery and walkways to storage areas and lighting.
What to look for:
- Slippery surfaces or loose floor tiles
- Faulty electrical systems or exposed wires
- Worn-out tools or malfunctioning machinery
- Improper chemical storage or labeling
How to do it right:
- Create a checklist tailored to your industry
- Involve supervisors and workers during walkthroughs
- Document findings with photos and notes
- Assign deadlines for corrective actions
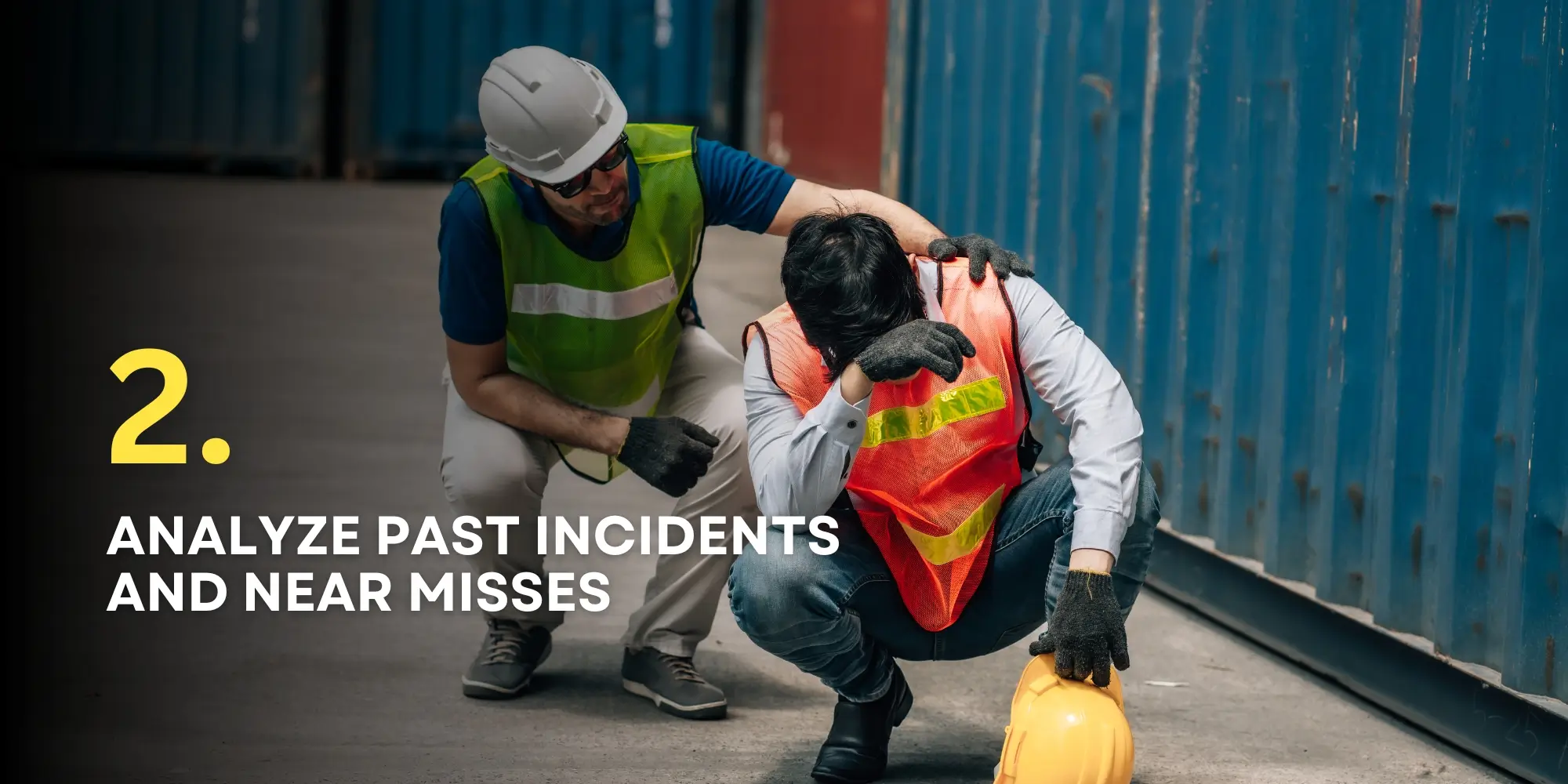
2. Analyze Past Incidents and Near Misses
Your best teacher might be your own history. Reviewing incident reports helps identify trends and recurring risks. Even “close calls” are goldmines of insight—if someone almost got hurt, something needs fixing.
Steps to implement:
- Collect all incident and near-miss reports
- Categorize them by type (e.g., trips, machinery failures)
- Look for patterns in time, location, or cause
- Involve frontline workers in root-cause analysis
Pro Tip: Don’t ignore minor injuries—they often signal bigger hazards waiting to happen.
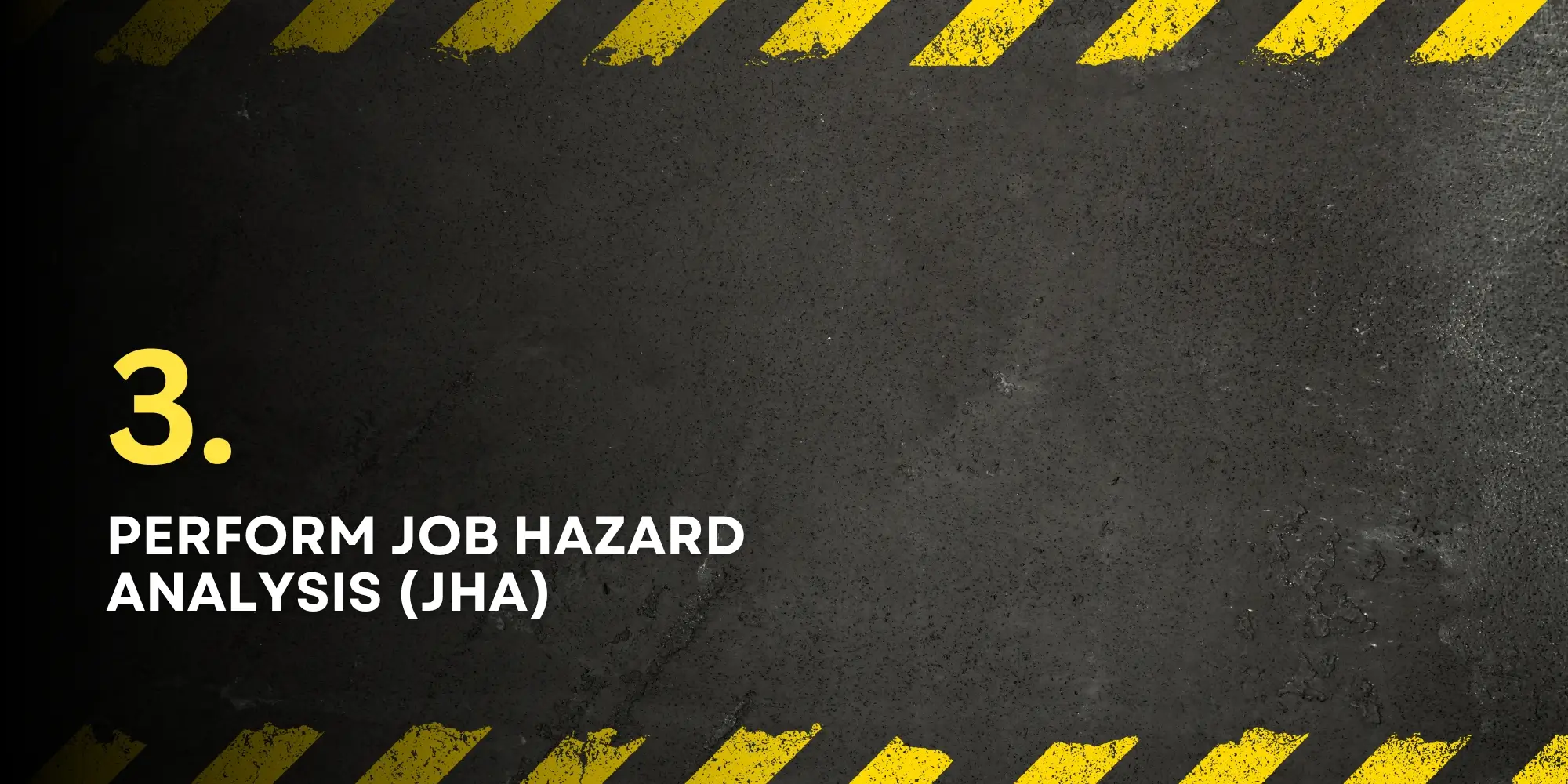
3. Perform Job Hazard Analysis (JHA)
A Job Hazard Analysis (JHA) breaks down individual tasks to examine the hazards within them. This proactive method is ideal for high-risk jobs like maintenance, machine operation, or chemical handling.
How JHA works:
- Select high-risk or frequently performed tasks
- Break down each task step by step
- Identify potential hazards in each step
- Recommend controls: engineering, administrative, or PPE
Example: For a task like operating a table saw:
- Step: Aligning wood → Hazard: hand injury → Control: use push stick + training
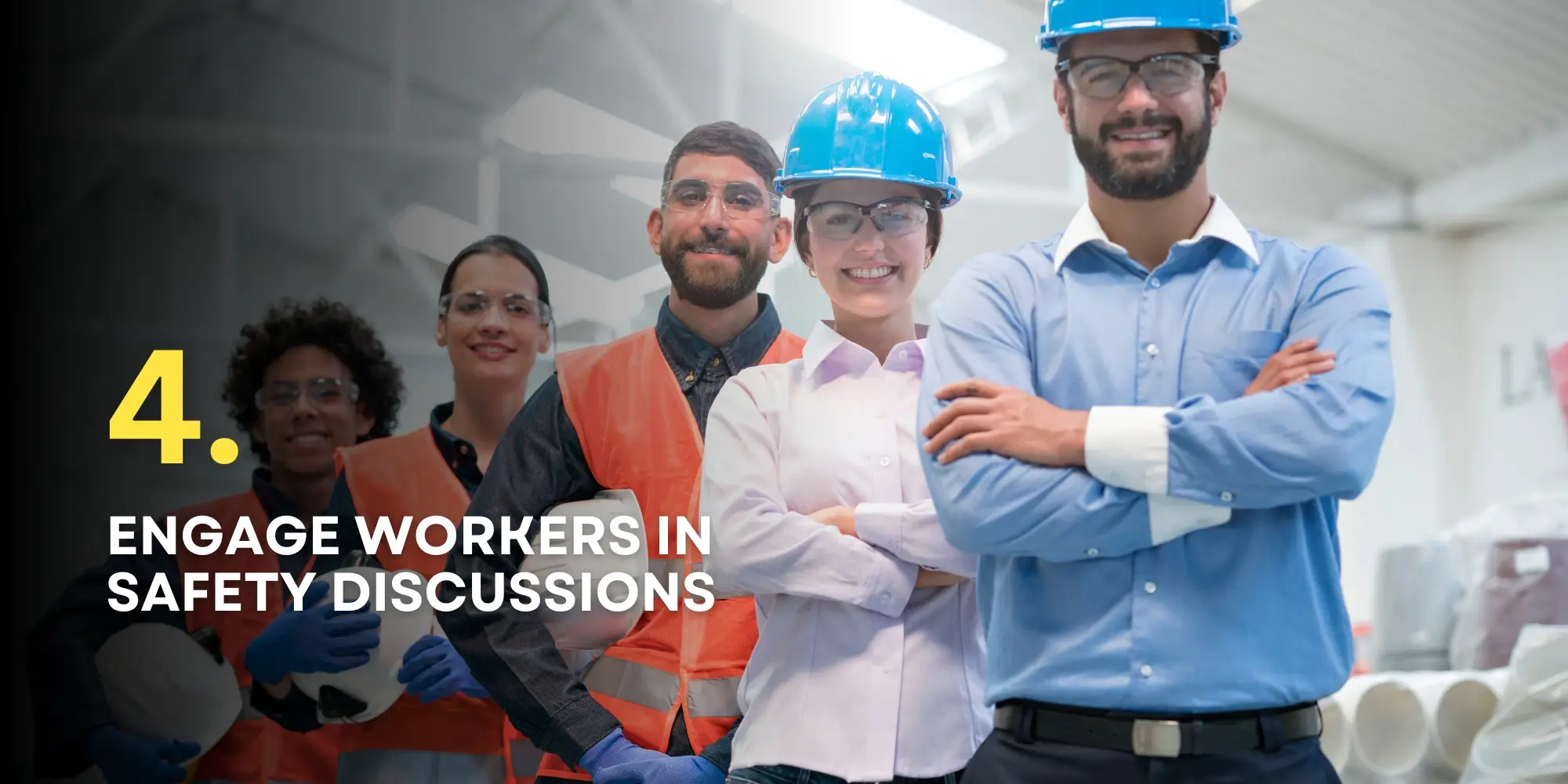
4. Engage Workers in Safety Discussions
Employees are often the first to notice hazards, and they’re usually affected by them. By creating open channels for reporting and discussion, you can identify issues early and build trust.
How to involve your team:
- Hold regular safety meetings or toolbox talks
- Use anonymous hazard reporting systems
- Offer incentives for proactive hazard spotting
- Train employees to identify and communicate risks
Why this works: Employees feel empowered, leading to greater safety ownership and better reporting accuracy.
Example: A worker notices a frequently wet hallway. Without a reporting process, that puddle stays. With one, it becomes a resolved hazard.
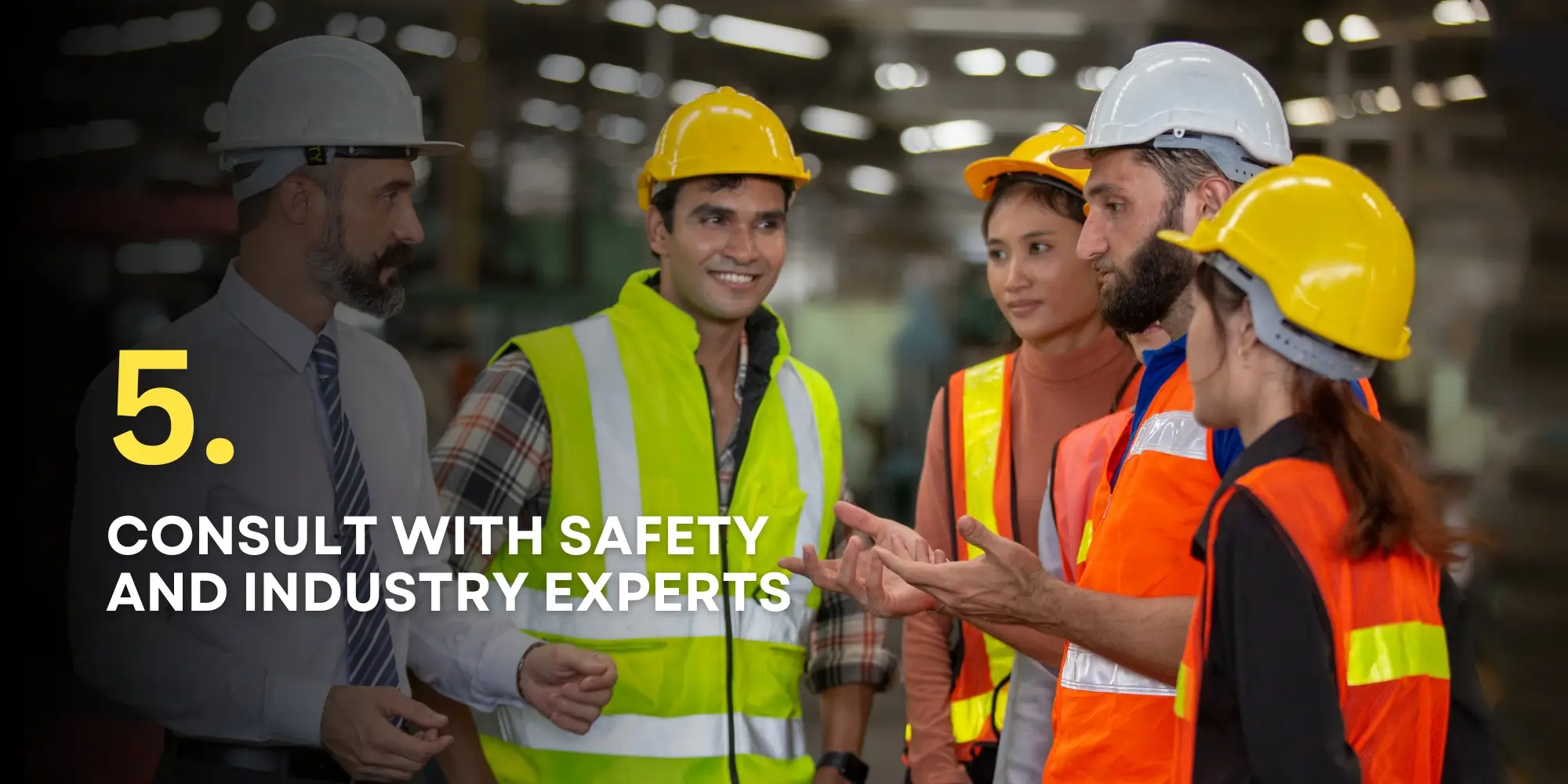
5. Consult with Safety and Industry Experts
Sometimes, a fresh set of trained eyes is what you need. Safety consultants, occupational hygienists, or ergonomics specialists can uncover overlooked risks and validate your internal assessments.
Benefits of expert consultation:
- Objective and experienced insight
- Deep knowledge of regulatory standards
- Custom solutions based on your environment
- Advanced risk assessments like noise mapping or air quality checks
When to bring in experts:
- After repeated incidents in the same area
- When introducing new machinery or processes
- To ensure compliance with updated regulations
Conclusion
Creating a truly safe workplace goes far beyond compliance—it requires a proactive and collaborative approach to hazard identification. This guide outlines five proven strategies for identifying risks before they escalate into accidents: inspections, incident analysis, job hazard assessments, employee engagement, and expert consultation.
Each method plays a vital role in your safety strategy:
- Inspections reveal immediate, visible dangers.
- Incident reviews help you learn from the past.
- JHAs expose task-specific risks.
- Worker involvement strengthens awareness and accountability.
- Expert insights fill in knowledge gaps and ensure regulatory alignment.
By integrating these practices into your safety program, you will reduce workplace injuries and costs and build a stronger safety culture where everyone feels responsible and empowered.
Remember: Hazard identification isn’t a one-time event—it’s an ongoing process. The more consistently and thoroughly you apply these methods, the more resilient and productive your workplace will become.