Job Safety Analysis (JSA) identifies and mitigates workplace hazards by breaking down a job into individual stages and analyzing the potential hazards associated with each stage. By conducting a JSA, employers can identify potential safety hazards and develop effective strategies to prevent accidents and injuries in the workplace.
This blog post will explore the six steps to successfully conducting a JSA. These steps include selecting the job to be analyzed, breaking the job down into individual stages, identifying potential hazards associated with each stage, developing preventive measures for each hazard, implementing the preventive measures, and finally reviewing and updating the JSA as needed.
By following these six steps, employers can create a safer work environment and reduce the risk of accidents and injuries for their employees. So, whether you are a safety professional, a supervisor, or an employee, understanding the process of conducting a JSA is critical to promoting a safe and healthy workplace.
What is Job Safety Analysis (JSA)
Job Safety Analysis (JSA) is a systematic process designed to identify potential hazards and recommend the safest methods for carrying out a specific task or job operation. This process integrates established safety and health principles and practices into each job stage. The primary goal of JSA is to minimize the risk of accidents and injuries in the workplace.
Some individuals prefer a more comprehensive approach, Total Job Analysis, which encompasses all aspects of a job rather than focusing solely on safety. This methodology is built on the concept that safety is an integral component of every job rather than an isolated element. However, this explanation will focus exclusively on JSA’s health and safety.
To better understand the concept of JSA, it is essential to define the terms “job” and “task.” Both terms are often used interchangeably to describe a specific work assignment, such as “operating a grinder,” “using a pressurized water extinguisher,” or “changing a flat tire.” It is important to note that JSAs are not suitable for jobs that are defined too broadly (e.g., “overhauling an engine”) or too narrowly (e.g., “positioning car jack”).
A JSA risk assessment must be developed when:
- The work activity involves a number of different tasks and hazards for which risk controls need to be planned, communicated and implemented
- Changes at the workplace occur that may impact the effectiveness of control measures.
- A Permit to Work is required
- Developing SOPs
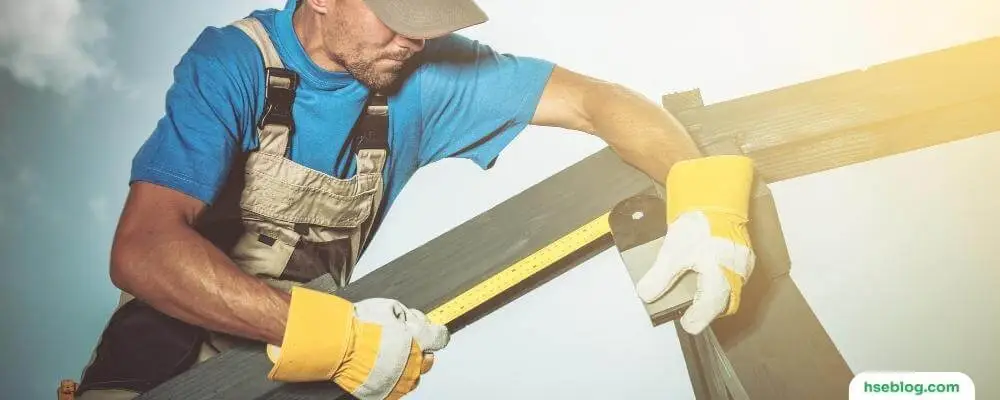
Benefits Of Doing A Job Safety Analysis (JSA)
A Job Safety Analysis (JSA) is a valuable tool for identifying and mitigating workplace hazards. The benefits of conducting a JSA are numerous and can significantly impact worker safety and organizational performance.
One of the primary advantages of conducting a JSA is that it allows organizations to identify and address potential hazards before they result in accidents or injuries. By breaking down a job or task into individual steps, organizations can systematically identify and evaluate potential hazards associated with each step. This process prompts the recognition of hazards that may have been previously overlooked, allowing organizations to develop appropriate safety measures to mitigate risks and protect workers.
Conducting a JSA also raises safety and health awareness among workers and supervisors, promoting a safety culture and encouraging communication about safe work procedures. It can also increase the job knowledge of those participating in the analysis process, enhancing their understanding of workplace hazards and the importance of implementing appropriate safety measures.
Developing a written work procedure based on the JSA can serve as a teaching aid for initial job training and a briefing guide for infrequent jobs. It may also be used as a standard for health and safety inspections or observations, ensuring that safety measures are consistently applied across all tasks and jobs.
Regularly conducting JSAs can also serve as a basis for regular contact between supervisors and workers, promoting ongoing communication and feedback about workplace hazards and safety measures. In particular, a JSA can assist in completing comprehensive accident investigations by clearly understanding the sequence of events leading up to an accident and identifying any potential hazards or safety measures that may have been overlooked.
What Activities Require A Job Safety Analysis (JSA)?
A Job Safety Analysis (JSA) can be conducted for any activity, task or job that poses potential hazards to workers. However, priority should be given to certain activities with a higher risk of injury or illness or potentially resulting in fatal accidents.
Some of the activities that require a JSA include:
- Activities known for the highest injury/illness rates: This includes activities or jobs that have a history of accidents or illnesses, such as those involving heavy machinery, working at heights, working with chemicals or hazardous materials, and manual handling of heavy objects.
- Activities or jobs with no room for error require high levels of precision and attention to detail, as even a slight lapse in concentration or a mistake could lead to a fatal accident. Examples include working with electricity, in in confined spaces, and operating heavy machinery.
- New or modified activities with new procedures: Anytime new activities or modified procedures are introduced, a JSA should be conducted to identify and mitigate potential hazards.
- Complex activities requiring written instructions: Complex activities that require written instructions, such as those involving specialized equipment or procedures, should be analyzed to ensure that all potential hazards are identified and addressed.
- Any activity with the slightest potential of being fatal: All activities have some risk associated with them, but any activity with even a slight potential of being fatal should be analyzed using a JSA. This includes activities such as working with explosives or handling hazardous materials.
By prioritizing the activities that require a JSA, organizations can effectively manage potential hazards, reduce the risk of accidents and injuries, and promote a culture of safety in the workplace. The JSA process provides a systematic approach to identifying and mitigating hazards, ensuring workers can perform their tasks safely and effectively.
Job Safety Analysis (JSA) Procedure – 6 Steps to Successful JSA
As we know, Job Safety Analysis (JSA) is a process used to identify potential hazards associated with specific job tasks and develop controls to eliminate or reduce the risk of injury or illness to workers. Here are the six steps to successfully carry out a JSA:
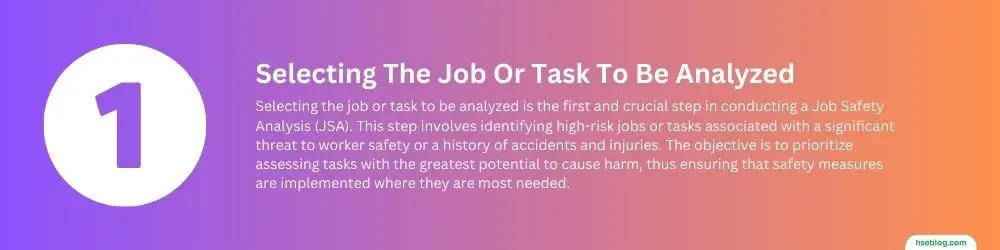
1. Selecting the job or task to be analyzed
Selecting the job or task to be analyzed is the first and crucial step in conducting a Job Safety Analysis (JSA). This step involves identifying high-risk jobs or tasks associated with a significant threat to worker safety or a history of accidents and injuries. The objective is to prioritize assessing tasks with the greatest potential to cause harm, thus ensuring that safety measures are implemented where they are most needed.
To determine which jobs or tasks require analysis, consider the following factors:
- Accident history: Review past incidents and accident records to identify tasks linked to injuries, near misses, or property damage. These tasks should be prioritized for analysis, as they have already demonstrated their potential for harm.
- Inherent risk: Some jobs or tasks inherently involve higher risks due to the nature of the work, the equipment used, or the environment in which they are performed. Examples include working at heights, handling hazardous chemicals, or operating heavy machinery. These high-risk tasks should also be prioritized for analysis.
- New or modified jobs/tasks: When new tasks are introduced or existing tasks are significantly modified, it’s essential to conduct a JSA to identify potential hazards and ensure that appropriate safety measures are in place.
- The complexity of the task: Jobs or tasks that involve multiple steps, require coordination between different workers, or involve specialized equipment may have a higher likelihood of hazards. Analyzing complex tasks can help identify potential risks and implement safety measures to reduce the chance of accidents.
- Regulatory requirements: Certain jobs or tasks may be subject to specific safety regulations or standards that mandate the performance of a hazard analysis. In such cases, conducting a JSA can help ensure compliance with these requirements.
- Worker feedback: Engaging workers in identifying high-risk tasks can provide valuable insights into potential hazards and areas of concern. Workers who perform the tasks daily often know firsthand the risks involved and can help prioritize tasks for analysis.
After considering these factors, create a list of jobs or tasks that require analysis, prioritizing those with the highest potential for harm. This targeted approach allows organizations to focus their resources on improving safety where it is needed most, thus reducing the likelihood of accidents and injuries in the workplace.
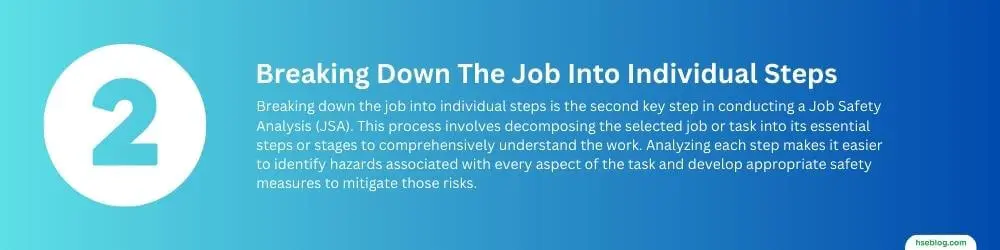
2. Breaking Down The Job Into Individual Steps
Breaking down the job into individual steps is the second key step in conducting a Job Safety Analysis (JSA). This process involves decomposing the selected job or task into its essential steps or stages to comprehensively understand the work. Analyzing each step makes it easier to identify hazards associated with every aspect of the task and develop appropriate safety measures to mitigate those risks.
To break down a job into individual steps, follow these guidelines:
- Observe the task: Begin by carefully observing the job or task being performed. This may involve watching a worker perform the task or performing the task yourself to understand the sequence of steps involved. Pay attention to the details, such as worker movement, tools, equipment, and materials.
- Consult with workers: Engage workers who regularly perform the task to gather their insights and perspectives on the steps involved. They can provide valuable information on the sequence, techniques, and potential job challenges.
- Document the steps: Write down each step of the task in a clear and concise manner. Use action verbs to describe the specific actions performed by the worker during each step, such as “lifting,” “cutting,” or “assembling.”
- Ensure a manageable number of steps: Aim to have a manageable number of steps for each JSA, typically between 5 and 15. If a task has too many steps, it might be necessary to break it down into smaller sub-tasks, each with its own JSA. Conversely, if a task has too few steps, consider combining related steps or expanding on the descriptions to provide a more detailed view of the job.
- Capture variations and non-routine tasks: Make sure to include any variations in the task, such as different methods for performing the same step or alternative tools that may be used. Also, consider non-routine tasks, such as maintenance or emergency procedures, which may introduce additional hazards.
- Review and refine: Once the steps have been documented, review them with the workers to ensure accuracy and completeness. Make any necessary adjustments based on their feedback.
Breaking down the job into individual steps makes it easier to systematically identify hazards and develop appropriate safety measures for each task step. This thorough approach helps minimize the risk of accidents and injuries by addressing potential hazards at every job stage.
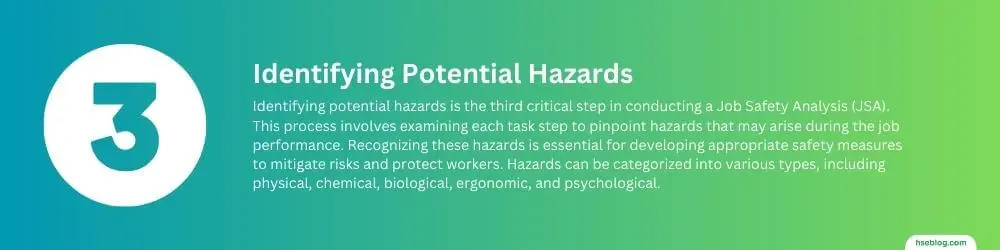
3. Identifying potential hazards
Identifying potential hazards is the third critical step in conducting a Job Safety Analysis (JSA). This process involves examining each task step to pinpoint hazards that may arise during the job performance. Recognizing these hazards is essential for developing appropriate safety measures to mitigate risks and protect workers. Hazards can be categorized into various types, including physical, chemical, biological, ergonomic, and psychological.
To identify potential hazards, consider the following approaches:
- Observation: Observe the task being performed and look for potential sources of harm during each step. Pay attention to tools and equipment, work environment, worker actions, and materials used.
- Worker input: Consult with workers who regularly perform the task to gather their insights on potential hazards. Their firsthand experience can provide valuable information on risks they encounter or have observed during the job performance.
- Hazard categories: Evaluate each step of the task against the different physical, chemical, biological, ergonomic, and psychological hazards.
- Risk assessment tools: Utilize established tools and methodologies, such as hazard checklists, risk matrices, or process hazard analyses, to systematically identify potential hazards associated with each task step.
- Accident and incident records: Review past accident and incident records to identify hazards previously linked to the task. This information can help identify recurring issues or patterns that may indicate areas of concern.
- Regulatory requirements and industry standards: Consult applicable safety regulations, industry standards, and best practices to identify hazards that may be specific to the task or industry.
Once potential hazards have been identified for each task step, it is crucial to document them clearly and concisely. This information will serve as the basis for developing appropriate safety measures to mitigate the risks associated with each hazard, ultimately enhancing worker safety and minimizing the likelihood of accidents and injuries.
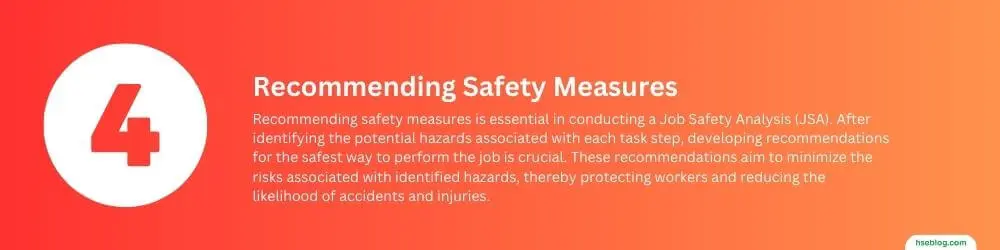
4. Recommending Safety Measures
Recommending safety measures is essential in conducting a Job Safety Analysis (JSA). After identifying the potential hazards associated with each task step, developing recommendations for the safest way to perform the job is crucial. These recommendations aim to minimize the risks associated with identified hazards, thereby protecting workers and reducing the likelihood of accidents and injuries.
To develop safety recommendations for each hazard, consider the following strategies:
- Hierarchy of controls: Apply the hierarchy of controls, a widely recognized approach to reducing risks in the workplace. This framework prioritizes safety measures based on their effectiveness, as follows:
Elimination: Remove the hazard entirely from the work process, if possible.
Substitution: Replace a hazardous substance, process, or equipment with a less hazardous alternative.
Engineering controls: Implement physical changes to the work environment, tools, or equipment to isolate or reduce exposure to the hazard.
Administrative controls: Establish policies, procedures, or work practices to minimize exposure to the hazard, such as job rotation, training, or maintenance schedules.
Personal Protective Equipment (PPE): Provide appropriate PPE to workers to protect against the hazard when other control methods are not feasible or adequate.
- Best practices and industry standards: Consult industry standards, best practices, and regulatory requirements to identify established safety measures for the specific hazards associated with the task.
- Worker input: Engage workers who regularly perform the task to gather their suggestions for improving safety. Their firsthand experience can provide valuable insights into potential solutions for mitigating hazards.
- Training and education: Ensure that workers receive proper training and education on safe work practices, hazard recognition, and the use of safety equipment. This will help ensure they are adequately prepared to safely perform the task.
- Regular inspections and maintenance: Implement regular inspections and maintenance schedules for tools, equipment, and work areas to ensure they are in good condition and functioning safely.
- Emergency preparedness: Develop emergency response plans and procedures to address potential incidents related to the identified hazards. Ensure workers are trained in these procedures and have access to necessary emergency equipment.
Once safety recommendations have been developed for each identified hazard, it is essential to document them clearly and concisely. This documentation will serve as a reference for workers, supervisors, and safety personnel to ensure appropriate measures are taken to protect worker safety and minimize the risk of accidents and injuries.
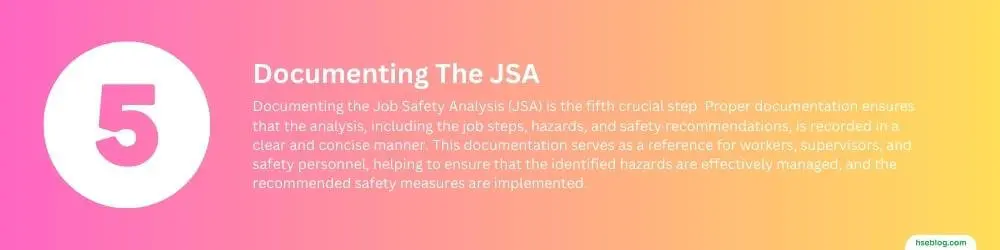
5. Documenting The JSA
Documenting the Job Safety Analysis (JSA) is the fifth crucial step. Proper documentation ensures that the analysis, including the job steps, hazards, and safety recommendations, is recorded in a clear and concise manner. This documentation serves as a reference for workers, supervisors, and safety personnel, helping to ensure that the identified hazards are effectively managed and the recommended safety measures are implemented.
To effectively document the JSA, follow these guidelines:
- Create a standard format: Develop a consistent format or template for documenting JSAs within your organization. This format should include sections for job information, job steps, identified hazards, and recommended safety measures. A consistent format makes comparing and analysing JSAs across different tasks and departments easier.
- Use clear and concise language: Write the job steps, hazards, and safety recommendations using clear and concise language. This ensures that the information is easily understood by everyone involved in the task, including workers, supervisors, and safety personnel.
- Include relevant details: Provide enough detail in the documentation to adequately describe the job steps, hazards, and safety recommendations. Include information such as the specific tools or equipment used, the worker’s body position or movement, the environmental conditions, and the exact nature of the hazard.
- Incorporate visuals: Consider using visuals, such as diagrams, flowcharts, or photographs, to supplement the written documentation. Visual aids can help clarify complex processes, illustrate equipment setup, or demonstrate proper safety procedures.
- Assign responsibility: Clearly indicate who is responsible for implementing the recommended safety measures, such as the worker, supervisor, or safety personnel. This helps ensure accountability and encourages prompt action to address the identified hazards.
- Obtain approval and signatures: Once the JSA has been documented, obtain approval and signatures from relevant parties, such as the worker, supervisor, and safety personnel. This process helps confirm that all stakeholders have reviewed and agreed upon the JSA and demonstrate a commitment to workplace safety.
- Store and organize the documentation: Store the JSA documentation in a centralized location, such as a shared electronic folder or a physical binder. Ensure the documentation is easily accessible to all relevant personnel and organised to facilitate easy retrieval and review.
Organizations can create a valuable resource for promoting workplace safety by properly documenting the JSA. This documentation serves as a reference for implementing and maintaining the identified safety measures, thereby helping to minimize the risk of accidents and injuries in the workplace.
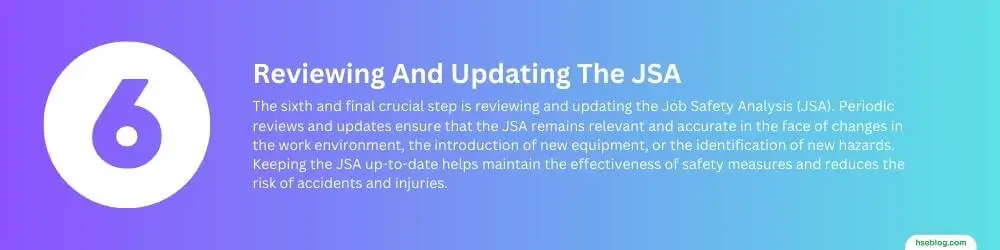
6. Reviewing And Updating The JSA
The sixth and final crucial step is reviewing and updating the Job Safety Analysis (JSA). Periodic reviews and updates ensure that the JSA remains relevant and accurate in the face of changes in the work environment, the introduction of new equipment, or the identification of new hazards. Keeping the JSA up-to-date helps maintain the effectiveness of safety measures and reduces the risk of accidents and injuries.
To review and update the JSA effectively, consider the following guidelines:
- Establish a review schedule: Set a regular schedule for reviewing JSAs within your organization. The frequency of reviews may vary depending on the nature of the job, the industry, or the organization’s specific needs. Generally, JSAs should be reviewed at least annually or more frequently for high-risk tasks or tasks subject to frequent changes.
- Monitor changes in the work environment: Keep track of any changes in the work environment, such as new processes, materials, or equipment, that may impact the safety of the task. Changes in work processes or the introduction of new equipment may necessitate a reevaluation of the existing JSA to ensure that all hazards are addressed and appropriate safety measures are in place.
- Identify new hazards: Stay informed of hazards that may be identified through incident reports, near-miss observations, worker feedback, or safety inspections. New hazards should be incorporated into the JSA to ensure that safety measures effectively address all potential risks.
- Evaluate the effectiveness of safety measures: Regularly assess the effectiveness of the safety measures recommended in the JSA. This can be done through audits, safety inspections, incident reports, and worker feedback. The JSA should include revised recommendations if safety measures are inadequate or ineffective.
- Incorporate regulatory changes: Stay informed of any changes to safety regulations, industry standards, or best practices that may impact the task. Update the JSA to ensure compliance with these changes and to incorporate any new safety measures that may be required.
- Communicate updates to workers: When the JSA is updated, communicate the changes to workers who perform the task. Provide training and information on the revised safety measures to ensure that they are properly implemented and understood by all affected workers.
- Maintain documentation: Update the JSA documentation to reflect any changes made during the review process. Ensure the updated documentation is stored in a centralized location and easily accessible to all relevant personnel.
By regularly reviewing and updating the JSA, organizations can ensure that their safety measures remain effective and relevant in the face of changing work environments, processes, and hazards. This proactive approach to workplace safety helps minimize the risk of accidents and injuries and promotes a culture of continuous improvement in safety performance.
Conclusion
a Job Safety Analysis (JSA) is a critical tool for identifying and mitigating workplace hazards. Conducting a JSA allows organizations to systematically evaluate potential hazards associated with specific tasks or jobs and develop appropriate safety measures to protect workers. By prioritizing activities known for the highest injury/illness rates, jobs with no room for error, new or modified activities, complex activities requiring written instructions, and any activity with the slightest potential of being fatal, organizations can effectively manage potential hazards, reduce the risk of accidents and injuries, and promote a culture of safety in the workplace.
The JSA process also promotes communication and feedback among workers and supervisors, raising safety and health awareness, enhancing job knowledge, and serving as a basis for regular contact between supervisors and workers. Additionally, a JSA can serve as a teaching aid for initial job training, as a briefing guide for infrequent jobs, and as a standard for health and safety inspections or observations.
Regularly conducting JSAs can assist in completing comprehensive accident investigations, ensuring that safety measures are consistently applied across all tasks and jobs, and promoting ongoing communication and feedback about workplace hazards and safety measures.
By integrating a JSA into their safety and health program, organizations can promote a safety culture and protect workers from accidents and injuries. Ultimately, the JSA process helps organizations ensure a safe and healthy work environment for all workers.