Ensuring worker safety, particularly when working at heights, is a critical concern for industries that regularly use fixed ladders. Ladder safety systems play a crucial role in preventing accidents and providing continuous fall protection, making them essential for complying with safety regulations and protecting workers.
This blog will explore the different types of ladder safety systems, their key applications across various industries, and the best practices for maintaining and inspecting these systems to ensure long-term reliability and effectiveness.
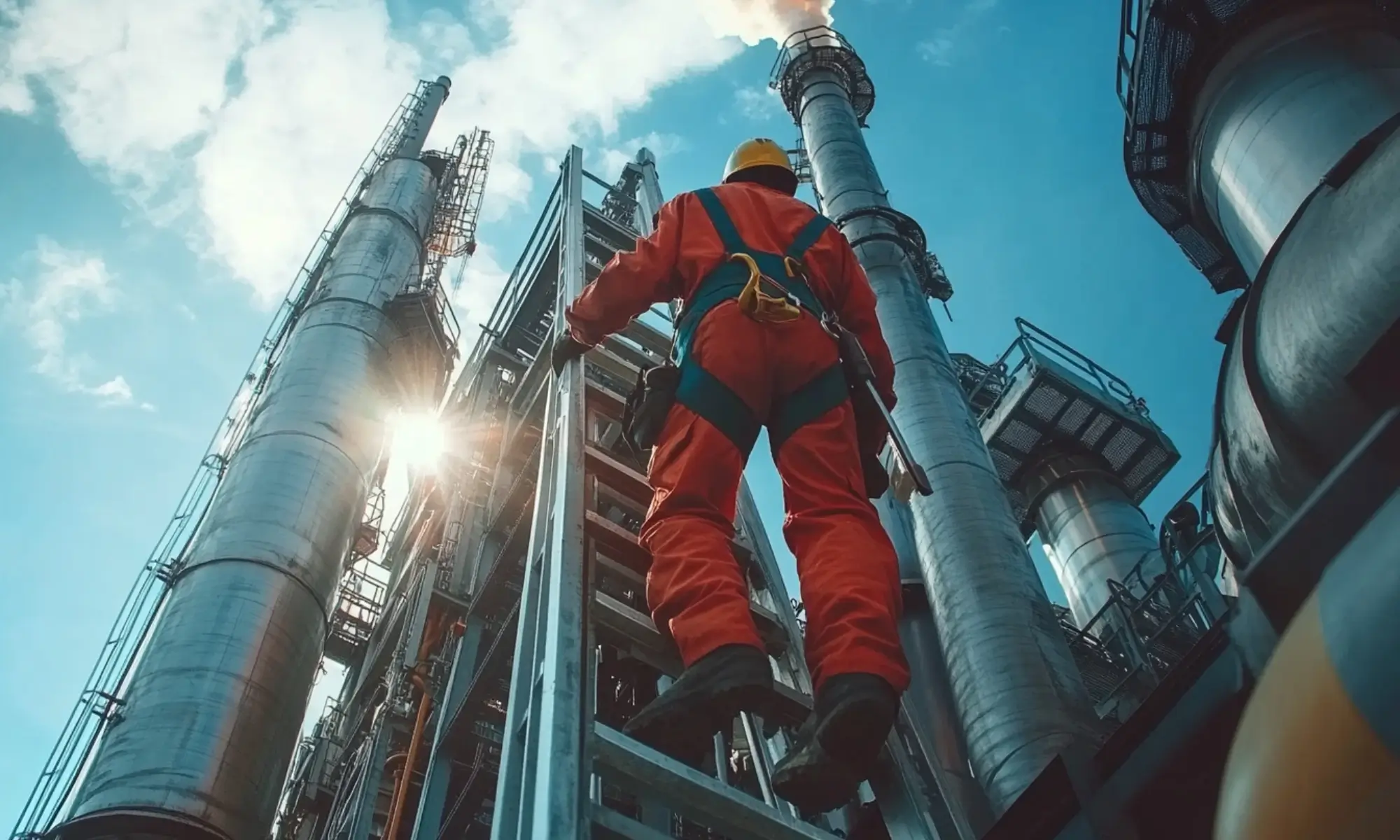
What are Ladder Safety Systems?
Ladder safety systems are fall protection solutions designed to ensure the continuous safety of workers climbing fixed ladders. These systems, typically involving a rail or cable, allow workers to securely attach themselves using a fall protection device or harness. In the event of a fall, the system automatically engages to arrest the descent, preventing serious injury or death.
Ladder safety systems are crucial for industries requiring frequent ladder use, and they comply with safety regulations like those set by OSHA to enhance worker protection and minimize risks associated with working at heights.
Key Features of Ladder Safety Systems
- Continuous Fall Protection: Workers remain securely attached to the ladder system from the bottom to the top, providing uninterrupted fall protection.
- Durable Construction: Made with high-strength stainless or galvanized steel to withstand harsh conditions and frequent use.
- Smooth Mobility: The system allows for easy movement up and down the ladder, reducing user fatigue and enhancing work efficiency.
- Ease of Installation: It is designed for a simple setup with minimal disruption, making it straightforward to retrofit onto existing ladders.
- Low Maintenance: Built for long-term use with minimal maintenance, reducing overall costs while ensuring safety.
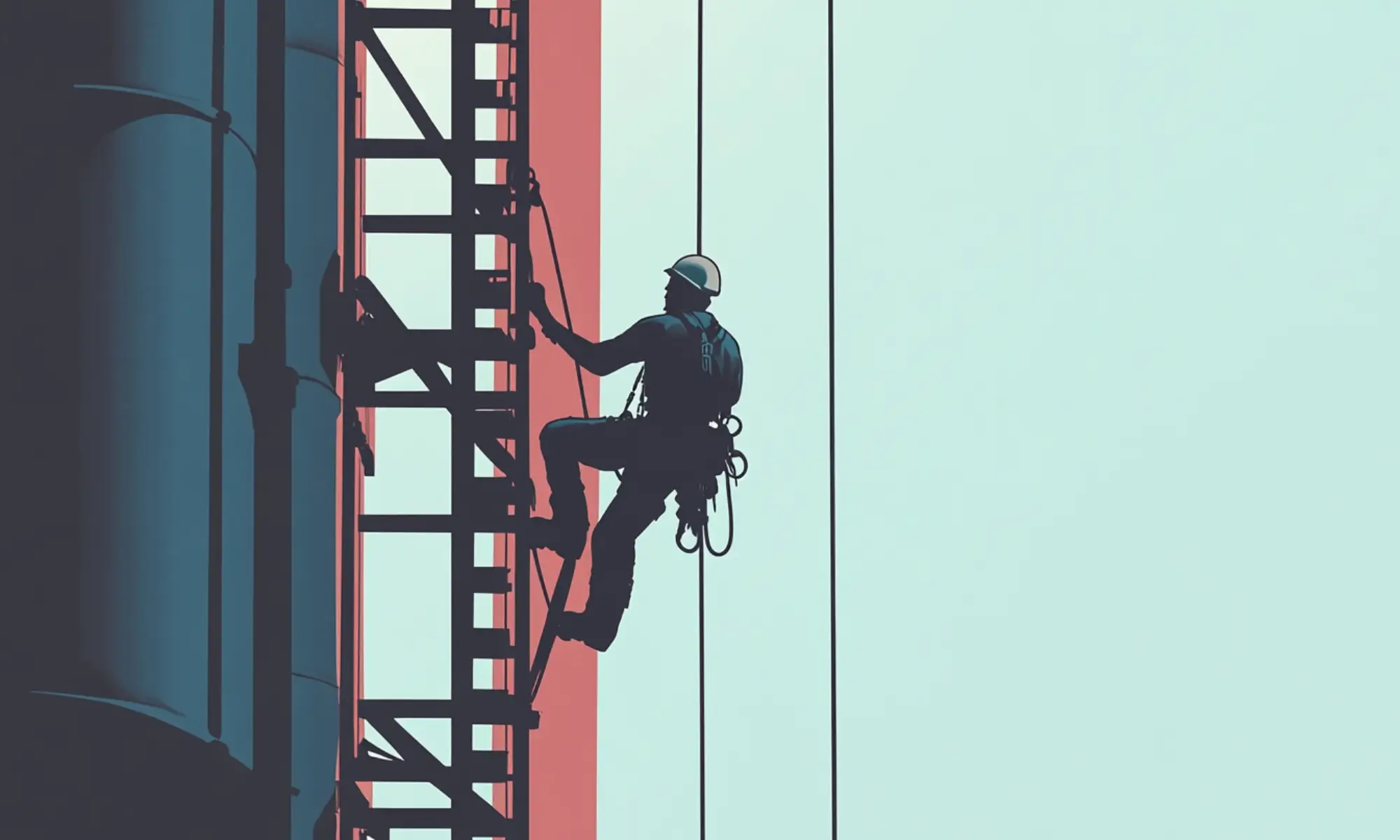
Types of Ladder Safety Systems
There are two main types of ladder safety systems: rigid rail systems and cable ladder safety systems.
1. Rigid Rail Ladder Safety System
A rigid rail system features a solid track or rail fixed to the ladder. This rail is a guide and anchor for the fall protection trolley workers attach themselves to with a body harness. In the event of a fall, the trolley locks onto the rail instantly, arresting the descent.
Advantages of Rigid Rail Systems:
- Enhanced Stability: The solid connection to the ladder ensures stability, making these systems ideal for outdoor settings or high-wind environments.
- Customization for Complex Applications: Ideal for settings like tank interiors where transitioning through hatches is required.
- Durability in Harsh Environments: Stainless steel versions are recommended for corrosive settings, such as those involving potable water.
Considerations:
- Initial Cost: Higher upfront investment than cable systems, but often offset by long-term durability and reduced maintenance.
2. Cable Ladder Safety System
The cable ladder safety system comprises a flexible cable that runs the length of the ladder, with a harness and cable grab attachment. The cable is affixed to the ladder with brackets and includes a tensioner to maintain the lifeline’s stability.
Advantages of Cable Systems:
- Greater Mobility: Workers can move more freely up and down the ladder, making this system ideal for applications that require flexibility.
- Cost-Effective for Single Spans: Typically more budget-friendly for long, uninterrupted ladder sections.
- Ease of Installation: It requires only top and bottom brackets, making it simpler to install than rail systems.
Considerations:
- Wear Over Time: Lifelines may experience more wear and tear, necessitating regular inspections and potential replacements.
- Not Recommended for Certain Environments: Cable systems may not be the best choice for environments with potable water or severe corrosive exposure.
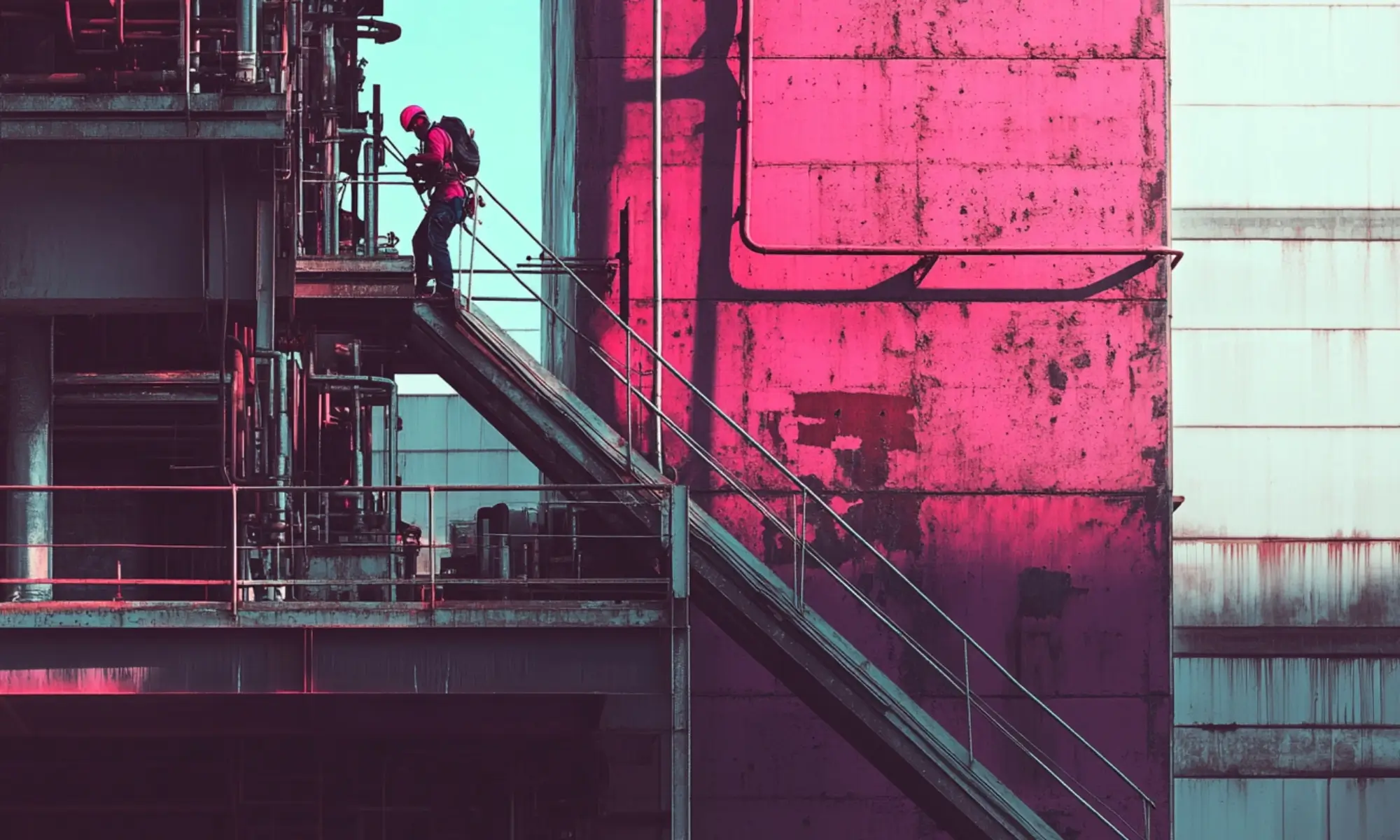
Applications of Ladder Safety Systems
Ladder safety systems are widely used across various industries to ensure worker safety during climbs. Key applications include:
Industrial Maintenance
In factories, plants, and warehouses, ladder safety systems are essential for protecting workers during maintenance tasks, ensuring their safety when accessing high or hard-to-reach areas for inspections, repairs, and servicing.
- Used for routine checks and equipment servicing
- Ensures compliance with safety regulations
- Reduces risk of falls in challenging work environments
Telecommunication Towers
Workers inspecting or maintaining telecommunication towers rely on ladder safety systems for secure ascents. These systems provide crucial fall protection while managing the heights and confined spaces of these structures.
- Provides reliable fall protection during climbs
- Facilitates safe inspections and maintenance tasks
- Enhances worker confidence and reduces accident risk
Utility Work
Ladder safety systems are vital for utility workers who need to climb poles or ladders to access electrical lines and transformers. They safeguard workers against potential falls and ensure efficient work at heights.
- Used for safe ascents during utility repairs and inspections
- Prevents falls during high-risk tasks involving power infrastructure
- Complies with safety protocols for public and worker safety
Construction
On construction sites, fixed ladders equipped with safety systems provide fall protection for workers, making climbing safer during different stages of building and ensuring adherence to safety standards.
- Essential for high and multi-level construction tasks
- Protects workers navigating partially constructed structures
- Reduces injury risks and boosts overall site safety
Wind Energy
For wind turbine maintenance and inspections, ladder safety systems offer fall protection for workers climbing tall, confined internal ladders, supporting the safe and efficient upkeep of renewable energy structures.
- Facilitates safe navigation within turbine towers
- Ensures worker safety during maintenance checks
- Meets industry-specific safety requirements and standards
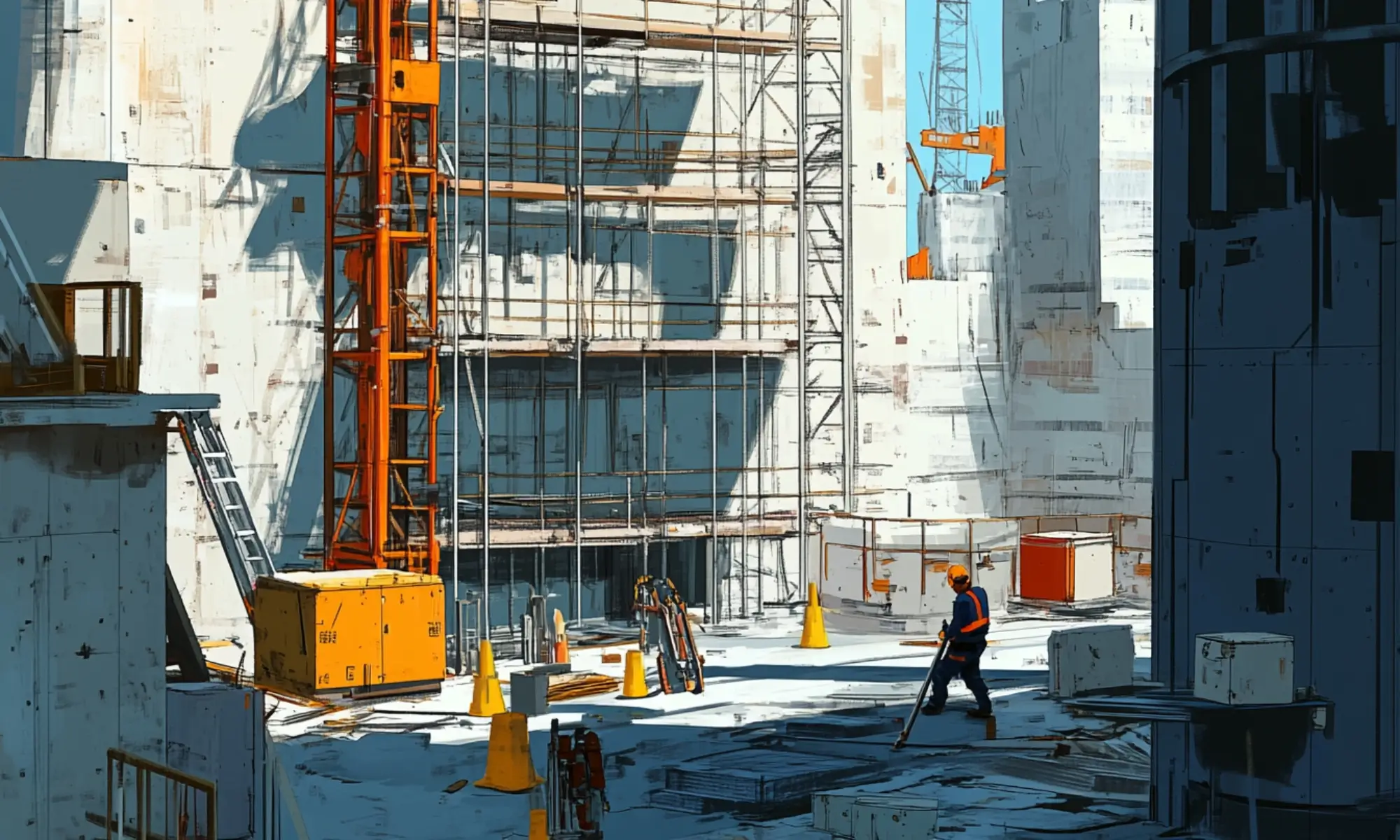
Ladder Safety and Compliance: Meeting OSHA Standards
In 2018, the Occupational Safety and Health Administration (OSHA) implemented significant changes to its fall protection standards for fixed ladders to enhance worker safety. Below, we explore the key updates and their implications for employers and industries.
1. Ladder Cages Are Being Phased Out
Previously, ladder cages and wells were widely accepted as fall protection measures. However, OSHA’s updated standards found these solutions inadequate and sometimes posed additional risks. During a fall, a worker could get caught or injured by these structures, compromising safety rather than enhancing it. As a result, OSHA mandated that ladder cages would no longer be considered sufficient fall protection.
Key Points:
- Ladder cages do not adequately prevent falls.
- Workers face risks of injury from snagging or getting trapped.
- Phased-out status emphasizes the need for better safety systems.
2. Mandatory Ladder Safety Systems
To improve safety, OSHA now requires that all new fixed ladders over 24 feet must be equipped with a ladder safety system or a personal fall arrest system. These systems provide continuous fall protection and significantly lower the risk of falls and related injuries.
Key Points:
- New ladders over 24 feet must have a ladder safety or fall arrest system.
- These systems ensure continuous protection from the bottom to the top of the ladder.
- Compliance helps prevent life-threatening falls and boosts overall safety.
3. Retrofitting Requirements
OSHA’s regulations also require retrofitting existing ladders. By November 18, 2036, any fixed ladder that undergoes repairs or modifications must be upgraded to include a ladder safety system. This ensures that older ladders are brought up to current safety standards and align with the protective measures expected in the industry.
Key Points:
- Existing ladders requiring repairs or modifications must be retrofitted.
- The deadline for retrofitting compliance is November 18, 2036.
- Retrofitting brings older equipment in line with modern safety standards.
Ensuring Compliance
Employers are responsible for ensuring ladder safety systems meet OSHA’s updated regulations. By adhering to these standards, businesses not only maintain compliance but also create a safer work environment for their employees. This proactive approach helps minimize risks, prevents falls, and demonstrates a commitment to worker safety.
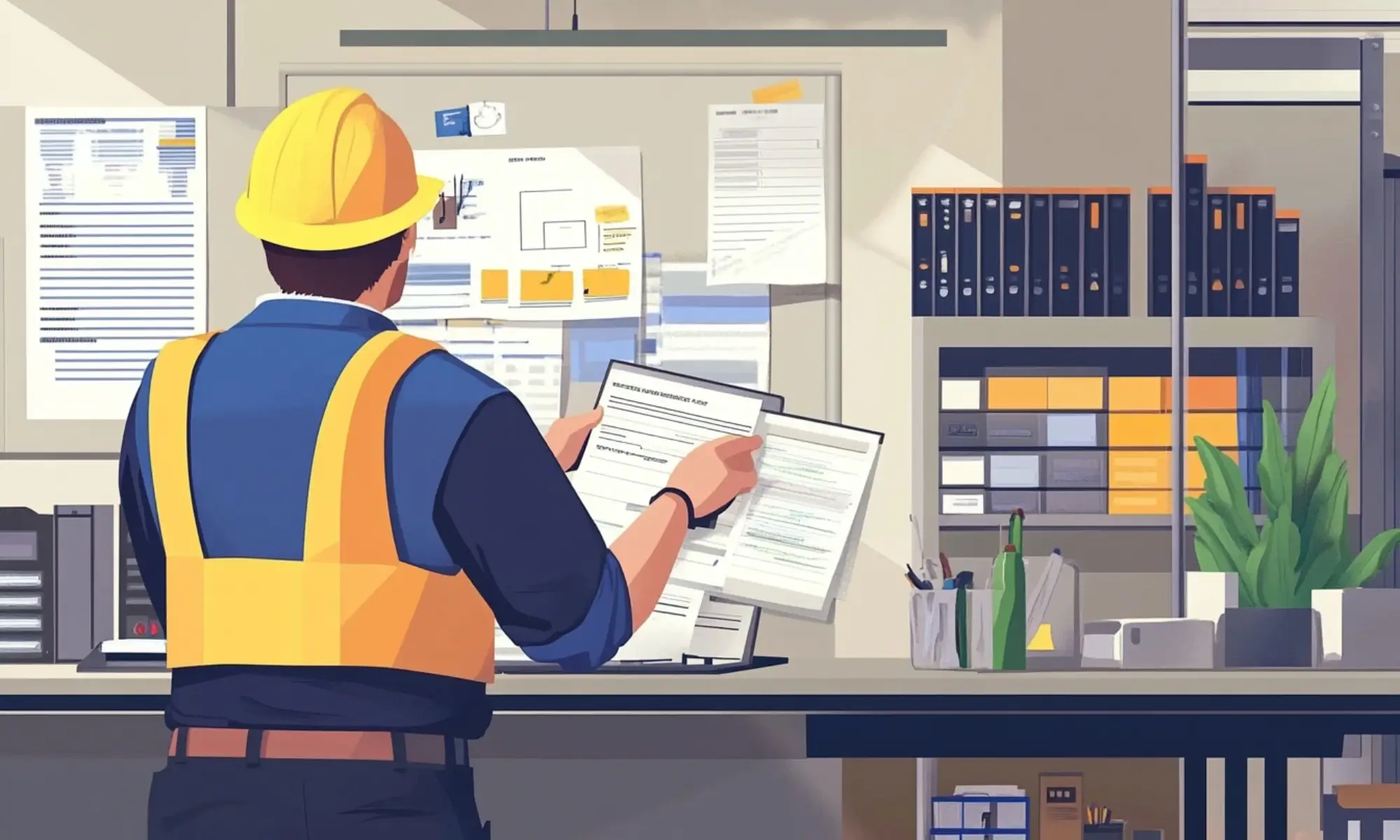
Maintenance and Inspection: Ensuring Long-Term Safety
Maintaining and regularly inspecting ladder safety systems is essential for ensuring their effectiveness and the safety of workers. Proper care and diligence in this area help identify and address potential issues before they compromise safety. Below are best practices for maintaining and inspecting ladder safety systems:
1. Routine Checks
Perform thorough inspections before each use to identify any signs of wear, corrosion, or damage. Key components to check include:
- Rails: Look for bends, rust, or structural damage.
- Cables: Inspect for fraying or slack that may indicate weakening.
- Brackets and Connectors: Ensure they are securely fastened and free from damage or deterioration.
2. Scheduled Maintenance
Adhere to the manufacturer’s guidelines for periodic maintenance to keep the system in top working condition. This includes:
- Replacing Worn-Out Parts: Swap out any components that show signs of wear or damage to prevent failures.
- Lubrication and Cleaning: Lubricate and clean moving parts to ensure smooth operation and reduce the impact of environmental factors like moisture and debris.
3. Record-Keeping
Maintain comprehensive records of all inspections, maintenance activities, and repairs. Proper documentation helps:
- Compliance: Demonstrates adherence to safety regulations and standards.
- Safety Audits: Provides evidence during inspections by regulatory bodies.
- Tracking Maintenance: Helps keep track of maintenance schedules and historical issues for better future planning.
By implementing these best practices, employers can ensure the long-term reliability of ladder safety systems and maintain a safer workplace for their employees.
Conclusion
Ladder safety systems are essential in safeguarding workers as they perform tasks at heights. Choosing between a rigid rail or cable system depends on your specific application, budget, and environmental conditions. By understanding the unique benefits of each system and ensuring compliance with OSHA regulations, you can create a safer work environment that protects your workforce and meets industry standards.
Investing in a ladder safety system is not just a regulatory requirement but a commitment to your employees’ well-being. By making informed decisions and prioritizing regular inspections, you can build a culture of safety that supports productivity and peace of mind.