Lockout Tagout (LOTO) procedures are essential safety protocols used in industrial settings to prevent serious injuries or fatalities. LOTO procedures require that all sources of energy that can power the equipment be shut off and locked out before maintenance or repairs can begin. Unfortunately, failure to follow proper LOTO procedures can result in the unexpected startup of machinery, leading to injury or death for workers.
This blog post will explore the most common LOTO mistakes that can lead to injury or death. We will also discuss the importance of proper training, communication, and verification to ensure that LOTO procedures are followed correctly, and workers are kept safe. By understanding these common mistakes, employers can take steps to prevent incidents and keep workers safe in the workplace.
Lockout Tagout Mistakes That Can Lead To Injury Or Death
Lockout Tagout (LOTO) is a safety procedure used in industrial settings to ensure that dangerous machines or equipment are properly shut off and cannot be started up again until maintenance or repairs are complete. Failure to follow proper LOTO procedures can result in serious injury or death. Here are some common LOTO mistakes that can lead to such incidents:
1. Failure to identify all sources of energy
LOTO requires identifying all energy sources that can power the equipment, including electrical, hydraulic, pneumatic, and mechanical sources. Identifying all energy sources is crucial because failure to do so can result in unexpected startup and cause injury or death to workers performing maintenance or repairs.
For example, if a maintenance worker thinks they have locked out all electrical energy sources but fails to recognize a hydraulic energy source, the equipment can start up unexpectedly and cause serious injury. This is why it’s important to thoroughly inspect the equipment and identify all energy sources before beginning any maintenance or repair work.
In addition, it’s essential to understand that energy sources can remain hazardous even after the equipment has been shut off. Stored energy, such as electrical, hydraulic, and pneumatic pressure, can still be present even when the equipment is turned off, and it can cause the equipment to start up unexpectedly. Therefore, it’s important to properly discharge or release any stored energy before performing any maintenance or repair work.
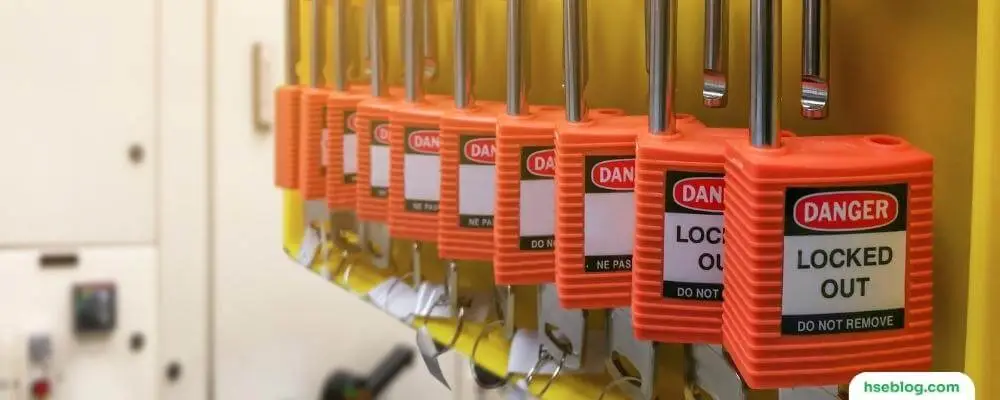
2. Failure To Drain Residues
When shutting down a piece of equipment or cutting off the power supply, it’s important to remember that the unit may not be immediately safe to handle. Energy can be stored in batteries, excess pressure can build up within a system, and machines can still be hot from their previous run. Pipes may also contain hot or toxic liquids and gases that need to be drained of residual substances. Failure to drain these residues can lead to serious injury or even death.
For example, if a worker is exposed to toxic fumes or chemicals not properly drained from pipes before maintenance work began, they can suffer from chemical burns, respiratory issues, or even death. Similarly, if a machine is still hot from its previous run and a worker comes into contact with it, they can suffer severe burns.
To prevent such incidents, it’s essential to ensure all residual substances have been properly drained before beginning maintenance or repair work. This includes draining fluids and gases from pipes, discharging excess pressure, and allowing machines to cool down before handling them.
Additionally, it’s important to use appropriate personal protective equipment (PPE) when working with potentially hazardous substances. This may include gloves, goggles, respirators, or other equipment to protect workers from exposure to toxic substances or extreme temperatures.
3. Inadequate training
Employers must ensure that their employees are properly trained on LOTO procedures to prevent injuries or deaths from occurring. Employees need to be trained in recognizing energy sources and safely isolating them before performing maintenance or repair work. This includes understanding the types of locks, tags, and other devices used to isolate energy sources and knowing when and how to use them.
Training should also include information on the hazards associated with working with the equipment and the consequences of failing to follow proper LOTO procedures. Employees should understand the importance of following the procedures exactly as they are laid out and the potential risks of taking shortcuts or skipping steps.
Moreover, employees should also be trained to recognize the limitations of LOTO procedures and understand when additional measures may be necessary to ensure worker safety. For example, employees should understand that some equipment may require special LOTO procedures or that some types of energy may be more difficult to isolate and require additional steps.
Lastly, training should be ongoing to ensure employees are updated on any changes or updates to LOTO procedures or equipment. It’s essential that employers provide regular refresher training to ensure that employees continue to follow the correct procedures and remain aware of potential hazards.
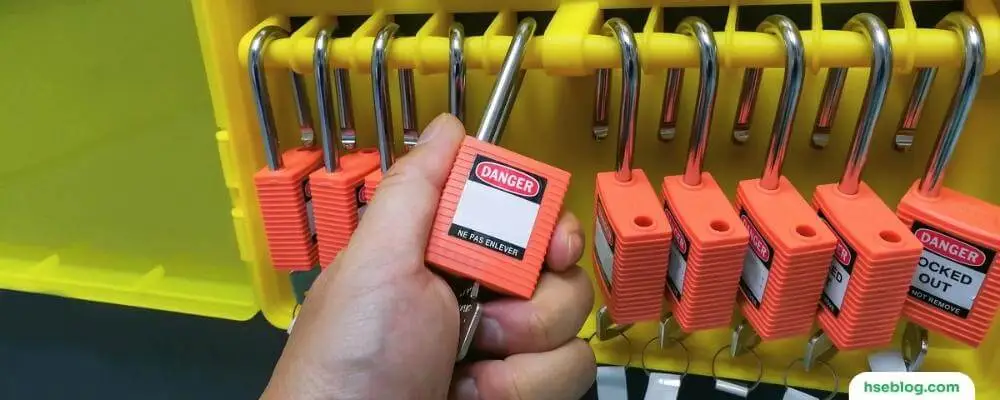
4. Use Of Duplicates/Master Keys/Shared Locks
Lockout Tagout (LOTO) procedures are designed to ensure workers are safe while performing maintenance or repair work. To ensure that LOTO procedures are followed correctly, it’s important to use appropriate locks and tags specific to each energy source, which can only be opened with a unique key.
However, some workers may try to take shortcuts by using duplicate or master keys or by sharing locks with other workers. This can lead to serious safety issues, as other workers may unknowingly attempt to start the equipment while it is still locked out.
Using duplicates or master keys can also make it difficult to trace accountability and responsibility, as it may not be clear which worker performed which lockout procedure. This can lead to confusion and make it difficult to determine who is responsible in the event of an incident.
Similarly, sharing locks can lead to dangerous consequences. If multiple workers use the same lock, knowing who has the key and whether the equipment has been properly locked out can be difficult. This can lead to unexpected equipment startup, causing serious injury or death.
To prevent such incidents, it’s essential to ensure that each technician holds their tagged lockout devices with a single key. Duplicate or master keys should not be used, and sharing locks should be avoided. Additionally, it’s important to ensure that all workers know the proper LOTO procedures and the consequences of not following them.
5. Failure to follow LOTO procedures
One of the most common mistakes that can lead to injuries or deaths in LOTO procedures is when employees skip steps or take shortcuts. For example, an employee may fail to disconnect all energy sources or properly tag a particular energy source. This can lead to the unexpected startup of machinery, causing injury or death.
To prevent these types of mistakes, it’s crucial to follow LOTO procedures exactly as they are laid out. This includes properly identifying all energy sources, isolating them using the appropriate locks and tags, and verifying that the equipment is completely shut off before performing any maintenance or repair work.
Employees should also be aware that LOTO procedures should be followed every time work is done on the equipment, regardless of how often they may have performed similar tasks. Employees should not take shortcuts or make assumptions about the equipment’s status, which can lead to serious injury or death.
Another important factor is to clearly understand the LOTO procedures and ensure that everyone involved is aware of the correct procedures. Any procedure or equipment changes should be communicated to all employees involved.
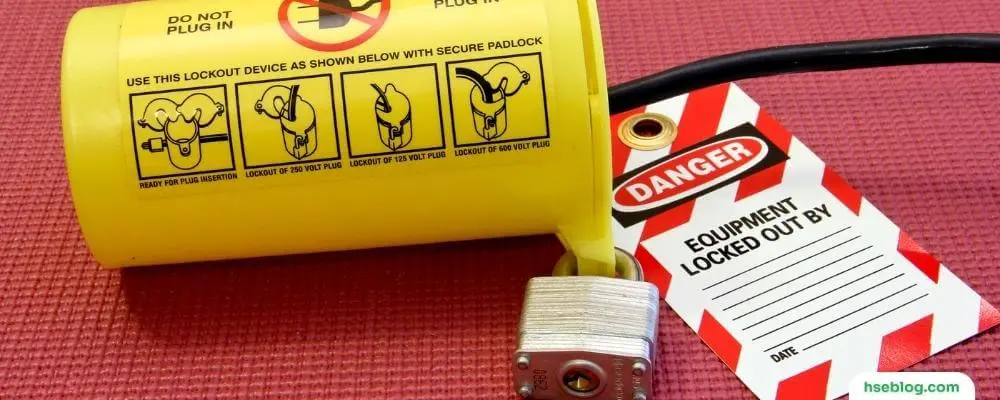
6. Improper use of locks and tags
Locks and tags are critical safety components of LOTO procedures. They isolate energy sources and ensure that the equipment cannot be started until all maintenance or repair work is complete. Improper use of locks and tags can lead to the unexpected startup of machinery, causing injury or death.
It’s important to use appropriate locks and tags for the specific equipment being worked on. This means using locks and tags of the right size and type for the isolated energy source. For example, a padlock that is too small or weak may not be able to secure the energy source properly, while a tag that is not visible or legible may not communicate the proper message to workers.
Additionally, it’s important to tag all energy sources that have been isolated, not just the primary energy source. This includes identifying backup energy sources or any other sources that could cause the equipment to start up unexpectedly.
Another important factor is ensuring that only authorized personnel can remove the locks and tags. This helps ensure that the equipment cannot be started until all maintenance or repair work is complete, reducing the risk of injury or death.
7. Failure to verify energy isolation
Before performing any maintenance or repair work, verifying that all energy sources have been properly isolated and locked out is crucial. This means ensuring that all energy sources have been identified and the appropriate locks and tags applied to each source.
To verify energy isolation, employees should conduct a visual inspection of the equipment to ensure that all energy sources have been isolated and that there are no signs of stored energy that could cause the equipment to start up unexpectedly. Additionally, employees should use appropriate testing equipment to confirm that all energy sources have been fully discharged or released.
Once energy isolation has been verified, keeping the equipment locked out and tagged until all maintenance or repair work is complete is important. During the work, monitoring the equipment to ensure no energy sources are inadvertently turned on is essential. This includes maintaining visual and auditory communication with other workers and ensuring the equipment is not started until all workers are clear.
After the work is complete, it’s important to remove all locks and tags and conduct a final inspection to ensure all energy sources have been restored to normal operating conditions. This helps ensure that the equipment is safe to use and reduces the risk of injury or death to workers.
8. Not updating LOTO procedures
As the equipment is modified or upgraded, it’s important to ensure that the LOTO procedures are updated accordingly. Failure to update procedures can result in outdated or incorrect procedures, leading to unexpected startup and serious injury or death.
When equipment is modified or upgraded, it’s essential to review the LOTO procedures to identify any changes that need to be made. This includes identifying new energy sources, new equipment components, or changes to existing energy sources or components.
After identifying the changes, the LOTO procedures should be updated to reflect the new equipment configuration. This may include adding new locks or tags, modifying existing ones, or revising the sequence of steps in the LOTO procedure.
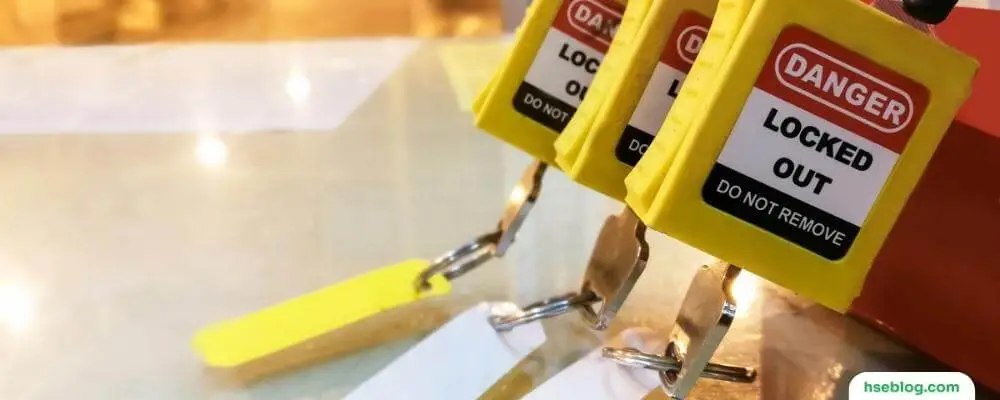
Once the new LOTO procedures have been developed, all employees should be trained on the updated procedures. This helps ensure everyone knows the changes and can follow the correct procedures to prevent injury or death.
It’s important to remember that failure to update LOTO procedures can have serious consequences. Workers may follow outdated procedures and be unaware of new hazards or risks associated with the modified or upgraded equipment. This can lead to unexpected startup and serious injury or death.
9. Lack of communication
Proper communication is essential in LOTO procedures to ensure that all employees are aware of the equipment status and the steps to isolate energy sources. This includes informing all employees involved in the work, locking out all energy sources, and ensuring that the equipment is not started until all workers are clear.
Clear communication is especially important when multiple employees are involved in the work or work in a complex or hazardous environment. Employees should be trained to communicate effectively and to ask questions if they are unclear about any aspect of the LOTO procedure.
Another important factor in communication is to use clear and visible lockout and tagout devices. This helps ensure that all workers know that the equipment is locked out and cannot be started until all maintenance or repair work is complete.
Additionally, employees should be trained to report any incidents or near-misses related to LOTO procedures. This helps identify areas where the LOTO procedures can be improved and help prevent future incidents from occurring.
Conclusion
Lockout Tagout (LOTO) procedures are critical safety protocols used in industrial settings to prevent serious injuries or fatalities. However, failure to follow proper LOTO procedures can lead to the unexpected startup of machinery, causing injury or death to workers. We have discussed the most common LOTO mistakes that can lead to such incidents, including failing to properly train workers, failing to perform proper equipment inspection, failure to use appropriate locks and tags, failure to verify energy isolation, failure to update LOTO procedures, failure to communicate effectively, failure to drain residues, failure to double-check the settings, and the use of duplicates, master keys, or shared locks.
Employers can prevent these incidents by providing proper training, equipment, and communication, performing regular equipment inspections, updating LOTO procedures, and enforcing LOTO protocols consistently. By following these steps, employers can ensure that workers are kept safe and that incidents are prevented in the workplace.