Lockout/Tagout (LOTO) procedures are critical safety measures implemented in industries to protect workers from the unexpected energization of machinery during maintenance or repair. This blog delves into the essential components of a comprehensive LOTO training program, offers guidance on how to effectively impart this training, and highlights common pitfalls that can render such training ineffective. By understanding these facets, organizations can ensure a safer work environment, reduce accidents, and foster a culture of safety awareness and compliance.
10 Core Components Of the Lockout/Tagout Training Program
Lockout/Tagout (LOTO) is a safety procedure used in industry and research settings to ensure that dangerous machines are properly shut off and not started up again prior to the completion of maintenance or repair work. A comprehensive Lockout/Tagout training program is essential to ensure the safety of workers. Here are the 10 core components of a LOTO training program:
1. Purpose and Scope
The LOTO program is instituted to ensure the safety of workers when they are performing maintenance or service on machinery and equipment. The primary reason for the program is to prevent the unexpected energization or startup of machines, which could lead to workplace injuries or fatalities.
The scope of the program encompasses various types of equipment, from large industrial machinery to smaller devices. It’s essential in situations where the unexpected release of stored energy could cause harm or where the machine’s regular operation could endanger someone working on or near it.
2. Roles and Responsibilities
In the LOTO process, different employees have distinct roles. Authorized employees are those who lock out or tag out machines or equipment to perform servicing or maintenance. They are trained to recognize hazards and have the knowledge to effectively lock out machinery. Affected employees, on the other hand, are those who operate or use the machine being serviced.
They need to be aware of the LOTO process and understand its importance. Other employees, while not directly involved in the LOTO process, should still be familiar with the procedure and the significance of not tampering with LOTO devices.
3. Recognition of Hazardous Energy Sources
Machines and equipment can be powered by various energy sources. These include electrical currents, mechanical motions, hydraulic systems, pneumatic systems, chemical reactions, and even thermal energy.
Each of these energy sources can pose unique hazards. For instance, electrical energy can lead to shocks or electrocution, while chemical energy might result in toxic releases or explosions. Recognizing these energy sources and understanding their potential hazards is crucial for effective LOTO.
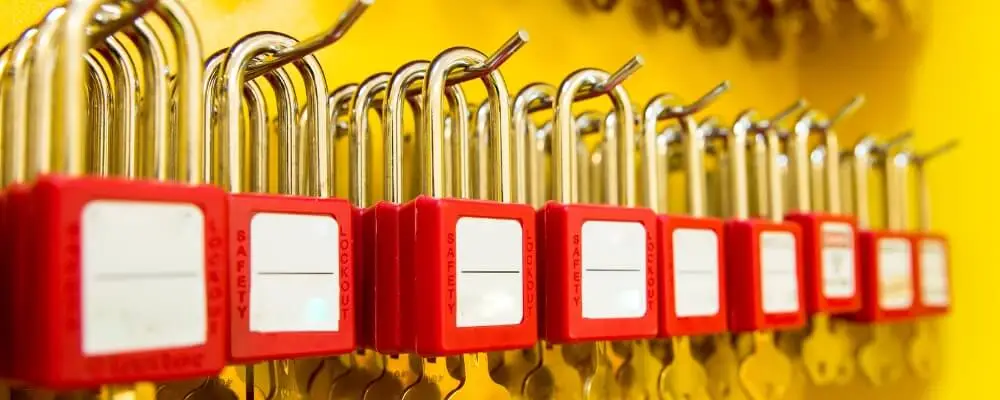
4. Types and Magnitude of Energy
Different machines have varying amounts of energy, and the potential danger they pose can differ significantly. A small battery-operated device might have minimal stored energy, while a large hydraulic press could have a significant amount. Understanding the magnitude of energy and its potential for harm helps in determining the necessary precautions and procedures for LOTO.
5. LOTO Devices and Hardware
There are various devices used in the LOTO process, including locks, tags, chains, wedges, and key blocks. These devices are designed to keep equipment in a safe or off position. Proper usage is essential to ensure they function as intended. Moreover, these devices should be stored in a manner that prevents unauthorized access and should be regularly inspected for wear and tear.
6. Shutdown Procedures
Before applying LOTO devices, machinery must be shut down correctly. This involves turning off the machine, disconnecting it from its energy source, and ensuring that all residual or stored energy is released or restrained. The procedure should be systematic and thorough to ensure no energy remains that could cause unexpected movement or activation.
7. Application of LOTO Devices
Once a machine is shut down, LOTO devices are applied to ensure it remains in an off or safe position. These devices should be placed in a manner that prevents the machine from being energized. Importantly, only the authorized individual who placed the device should remove it, ensuring continuity and responsibility in the LOTO process.
8. Release of Stored Energy
Some machines retain energy even after they are turned off. This energy can be in the form of pressurized air, hydraulic fluid, or even tension in mechanical parts. Before maintenance begins, it’s crucial to identify and safely release or restrain this stored energy to prevent unexpected movements or activations.
9. Verification of Isolation
After applying LOTO devices, it’s essential to verify that the equipment is indeed isolated from its energy sources. This can involve testing the machine’s controls to ensure it doesn’t operate. This step is crucial to confirm that the LOTO process has been effective and that it’s safe to begin maintenance or servicing.
10. Restoration to Normal Operations
Once maintenance or servicing is complete, the process of restoring the equipment to its normal operational state begins. This involves carefully removing the LOTO devices in a specific sequence to ensure safety. It’s crucial to check that all tools and parts have been cleared from the machine and that all safety guards or barriers are back in place.
Before re-energizing the equipment, affected employees should be notified. They need to be aware that the machine will be back in operation, ensuring they take the necessary precautions. Communication is key during this phase to prevent any accidental startups while someone might still be in harm’s way.
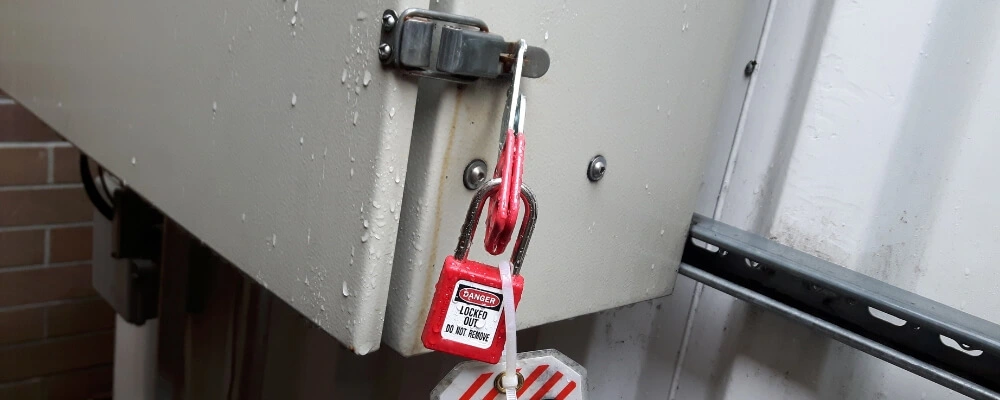
How to Deliver Effective Lockout/Tagout Training
Delivering effective Lockout/Tagout (LOTO) training is crucial to ensure the safety of employees when they are working on or around machines and equipment. Here’s a guide on how to deliver effective LOTO training:
- Understand the Audience: Recognize the varying levels of experience and knowledge among the trainees. Tailor the training to meet the needs of both new and experienced workers.
- Start with the Basics: Begin by explaining the importance of LOTO and the potential dangers of not following procedures. Use real-life examples or case studies to highlight the consequences of neglecting LOTO protocols.
- Interactive Learning: Incorporate hands-on exercises and simulations. Allow trainees to practice applying LOTO devices on mock equipment. This helps in reinforcing theoretical knowledge with practical experience.
- Use Visual Aids: Utilize diagrams, videos, and animations to explain complex concepts. Visual aids can make the training more engaging and can help illustrate the step-by-step process of LOTO.
- Clarify Roles and Responsibilities: Clearly define the roles of authorized, affected, and other employees. Emphasize the responsibilities of each role and the importance of communication among them.
- Discuss Different Energy Sources: Go in-depth about the various types of energy sources and their potential hazards. This helps employees recognize and understand the risks associated with each energy type.
- Regularly Update Training Material: As equipment, processes, or regulations change, ensure that the training material is updated accordingly. This ensures that employees are always trained on the most recent and relevant procedures.
- Encourage Questions and Discussions: Create an open environment where trainees feel comfortable asking questions or discussing concerns. This can lead to a deeper understanding of the material.
- Assess Understanding: Conduct quizzes, tests, or practical assessments to gauge the trainees’ understanding of the LOTO procedures. This helps in identifying areas that might need further emphasis or clarification.
- Provide Refresher Courses: LOTO training shouldn’t be a one-time event. Regular refresher courses ensure that employees remain familiar with the procedures and any updates or changes.
- Feedback Loop: After the training, gather feedback from the participants. This can provide insights into areas of improvement for future training sessions.
- Document Training: Keep records of all training sessions, including attendees, dates, and assessment results. This not only helps in tracking compliance but also in identifying employees who might need additional training.
- Use Real-life Incidents: If possible, discuss past incidents (without naming individuals) related to LOTO in your organization or industry. Analyzing what went wrong and how it could have been prevented can be a powerful learning tool.
- Promote a Safety Culture: Emphasize that safety is a shared responsibility. Encourage employees to always prioritize safety over speed or convenience and to look out for one another.
By following these guidelines and ensuring that the training is comprehensive, engaging, and up-to-date, organizations can significantly reduce the risk of accidents and injuries related to machinery and equipment.
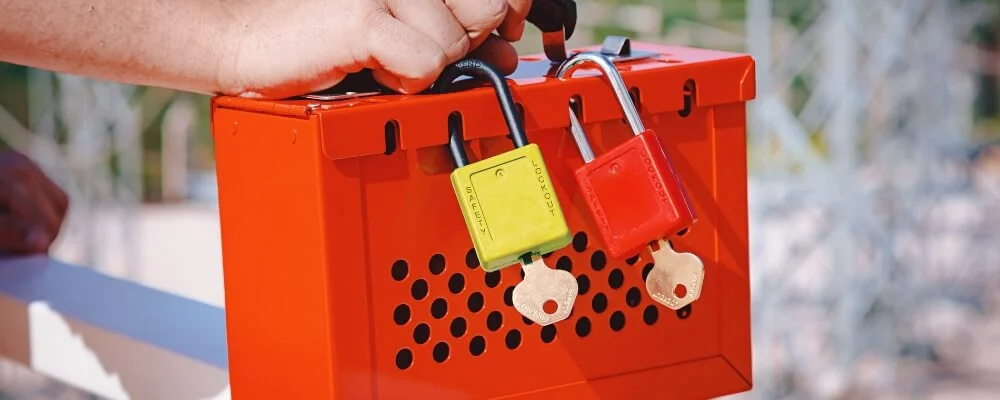
Common Reasons For Ineffective Lockout/Tagout Training
Ineffective Lockout/Tagout (LOTO) training can lead to serious safety hazards in the workplace. Understanding the common reasons for such ineffectiveness can help organizations address these issues and improve their training programs. Here are some common reasons for ineffective LOTO training:
- Lack of Management Commitment: If management doesn’t prioritize or support LOTO training, it can lead to inadequate resources, time, or emphasis being placed on the training.
- Outdated Training Material: Using old or outdated training materials that don’t reflect current equipment, processes, or regulations can lead to gaps in knowledge.
- One-Size-Fits-All Approach: Not tailoring the training to the specific needs, roles, or experience levels of the employees can result in information being too basic for some and too complex for others.
- Insufficient Hands-on Training: Relying solely on theoretical knowledge without providing practical, hands-on experience can leave employees unprepared for real-world situations.
- Lack of Regular Refresher Courses: Without periodic refresher training, employees can forget procedures or become complacent, leading to potential safety risks.
- Not Addressing Language or Cultural Barriers: If training isn’t provided in a language or format that all employees can understand, it can lead to misinterpretations or confusion.
- Overloading Information: Trying to cover too much information in a short time can overwhelm trainees, making it hard for them to retain crucial details.
- Lack of Engagement: If the training is dull or not interactive, employees might lose interest, leading to reduced retention and understanding.
- No Assessment or Feedback: Without testing or assessing employees’ understanding after training, it’s hard to identify areas of confusion or gaps in knowledge.
- Ignoring Real-life Scenarios: Not discussing real-life incidents or potential scenarios can make the training seem abstract and less relevant to employees.
- Inadequate Trainer Qualifications: If the trainer lacks experience, knowledge, or effective teaching skills, the quality of the training can suffer.
- Not Addressing Common Misconceptions: Failing to address and correct common misconceptions about LOTO can lead to persistent misunderstandings.
- Lack of Continuous Improvement: Not regularly reviewing and updating the training program based on feedback, incident reports, or changes in the workplace can lead to stagnation and ineffectiveness.
- Complacency: Over time, if there haven’t been any incidents, employees might become complacent and underestimate the importance of strict LOTO adherence.
Addressing these common pitfalls and continuously striving for improvement in the LOTO training program is essential to ensure the safety and well-being of all employees in the workplace.
Conclusion
In the realm of industrial safety, the Lockout/Tagout (LOTO) procedure stands as a paramount measure to safeguard workers from unforeseen machine activations. A robust LOTO training program is not just about compliance; it’s a commitment to the well-being of every employee. By meticulously outlining the core components of the training, ensuring its effective delivery, and being aware of potential pitfalls, organizations can significantly reduce workplace hazards.
As we’ve explored in this blog, the key lies in continuous improvement, regular updates, and fostering a culture where safety is not just a protocol but a shared responsibility. In doing so, businesses not only protect their most valuable assets – their employees – but also enhance operational efficiency and trust within their teams.