In any industrial or maintenance setting, machinery can pose serious risks if it unexpectedly starts up or releases stored energy during servicing. One wrong move could result in severe injury—or worse. That’s where Lockout/Tagout (LOTO) comes in. This safety procedure is not just a regulatory requirement; it’s a critical system designed to protect workers from hazardous energy during equipment repair, inspection, or maintenance.
This blog’ll walk you through a clear and practical 6-step Lockout/Tagout procedure that every workplace should implement. Whether you’re a safety officer, technician, or site manager, understanding LOTO is essential for ensuring compliance, preventing accidents, and building a strong safety culture. From identifying energy sources to restoring equipment, this guide covers everything you need to know to implement LOTO effectively and keep your team safe.
What’s Lockout/Tagout (LOTO)?
Lockout/Tagout (LOTO) is a vital safety procedure to protect workers from the unexpected startup or release of hazardous energy during equipment servicing or maintenance. “Lockout” involves physically locking energy-isolating devices to prevent activation, while “tagout” places a warning tag to inform others that the equipment is under maintenance. These controls are essential for managing risks from electrical, mechanical, hydraulic, pneumatic, chemical, and thermal energy sources.
The core goal of LOTO is to ensure a safe working environment by completely isolating equipment from all energy sources before work begins. It prevents accidental re-energization and ensures only authorized personnel can restore power once maintenance is complete. Regulatory bodies like OSHA and HSE require businesses to implement LOTO in their safety programs.
Importance of LOTO in the Workplace
LOTO protects workers from serious injuries caused by accidental equipment startup, such as electrocution, burns, or crushing. It’s not just a best practice—it’s a legal requirement in many countries, and non-compliance can result in severe penalties and workplace accidents.
Beyond compliance, LOTO builds a stronger safety culture. When companies prioritize worker safety through proper LOTO procedures and training, they encourage employees to follow safety protocols and reduce the overall risk of incidents.
Purpose of Lockout/Tagout (LOTO)
The main purpose of LOTO is to prevent the unintended release of energy that could harm workers during servicing tasks. It ensures machines are fully shut down, isolated from power sources, and stay off until safe to operate again.
LOTO also promotes consistency through standardized procedures—using locks, tags, and warnings to signal that equipment must not be touched. When properly implemented, LOTO reduces accidents, supports regulatory compliance, and reinforces a workplace culture focused on safety.
Lockout/Tagout (LOTO) Procedure
Lockout/tagout (LOTO) is a safety procedure used in industrial and commercial settings to ensure that machinery or equipment is safely shut off and cannot be started until maintenance or repairs are completed. The six steps of lockout/tagout are as follows:
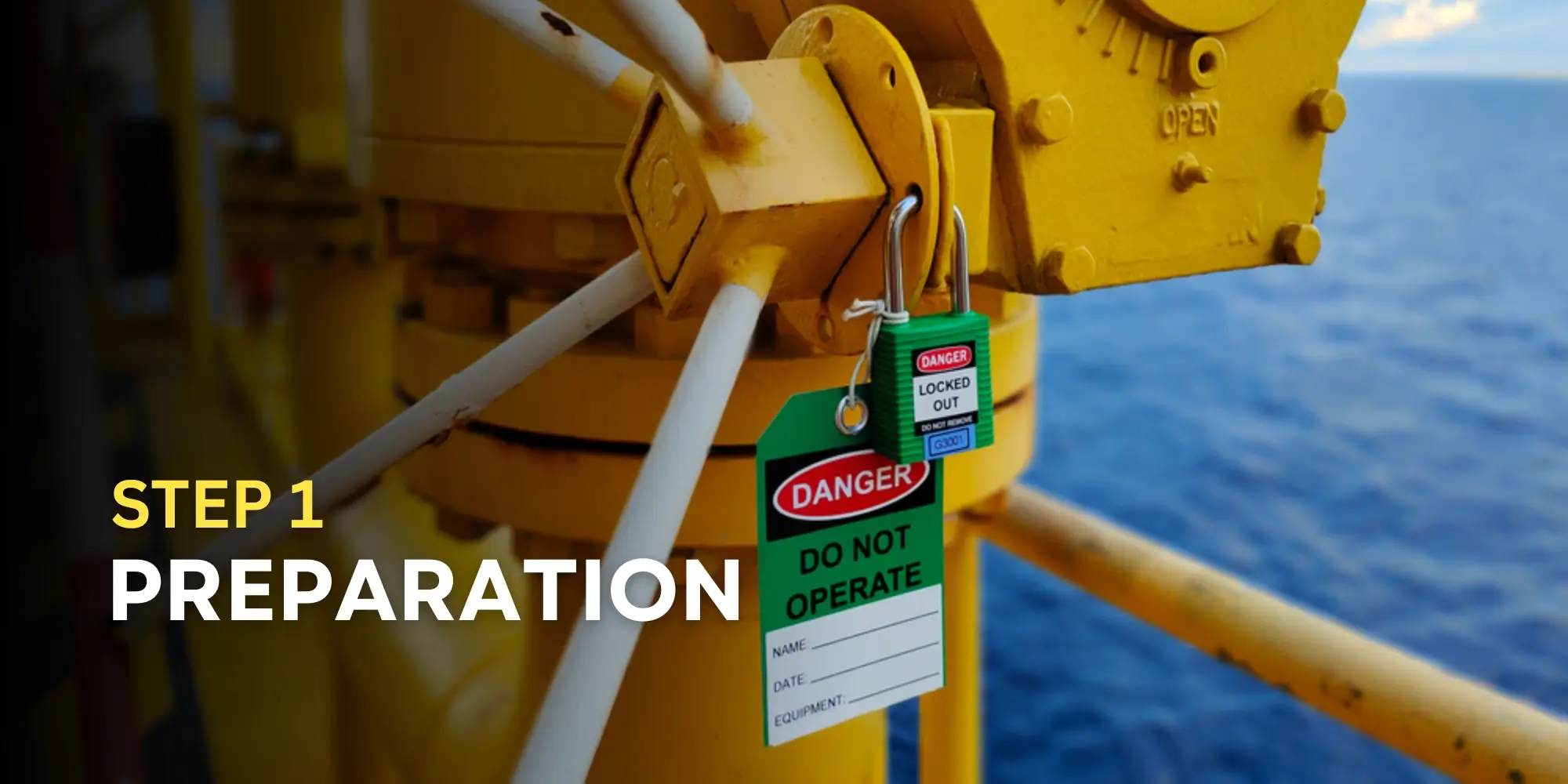
Step 1: Preparation
Preparation is the first and most crucial step in the Lockout/Tagout (LOTO) procedure. It ensures that the process is carried out safely and effectively by assessing the equipment, potential hazards, and required actions. This step is broken down into three essential parts:
Identifying Energy Sources and Hazards
Before beginning any maintenance or servicing task, you must identify all energy sources associated with the equipment. These can include:
- Electrical (power supply, circuits)
- Mechanical (moving parts, belts, gears)
- Hydraulic (pressurized fluid systems)
- Pneumatic (compressed air systems)
- Chemical (hazardous substances, reactive agents)
- Thermal (high-temperature components, steam)
- Gravitational (elevated loads that can fall)
Identifying every energy source ensures the machine is fully de-energized and safe to work on.
Gathering Necessary Tools and Equipment
Once the energy sources are known, gather the tools and devices needed to perform the lockout/tagout. These may include:
- Lockout padlocks
- Tags and identification labels
- Lockout hasps (for multiple lock usage)
- Valve lockouts or circuit breaker lockouts
- Personal protective equipment (PPE)
- Testing equipment (e.g., voltmeters)
Use only standardized, durable, and industry-approved LOTO devices to ensure effectiveness and worker safety.
Developing an Equipment-Specific LOTO Procedure
Every piece of equipment should have its own documented LOTO procedure that includes:
- Step-by-step shutdown instructions
- Methods to isolate each energy source
- Instructions for releasing stored or residual energy
- Verification steps to ensure de-energization
- Authorized personnel details and responsibilities
This written procedure should be accessible to all authorized employees and serve as a clear reference to prevent errors and maintain compliance.
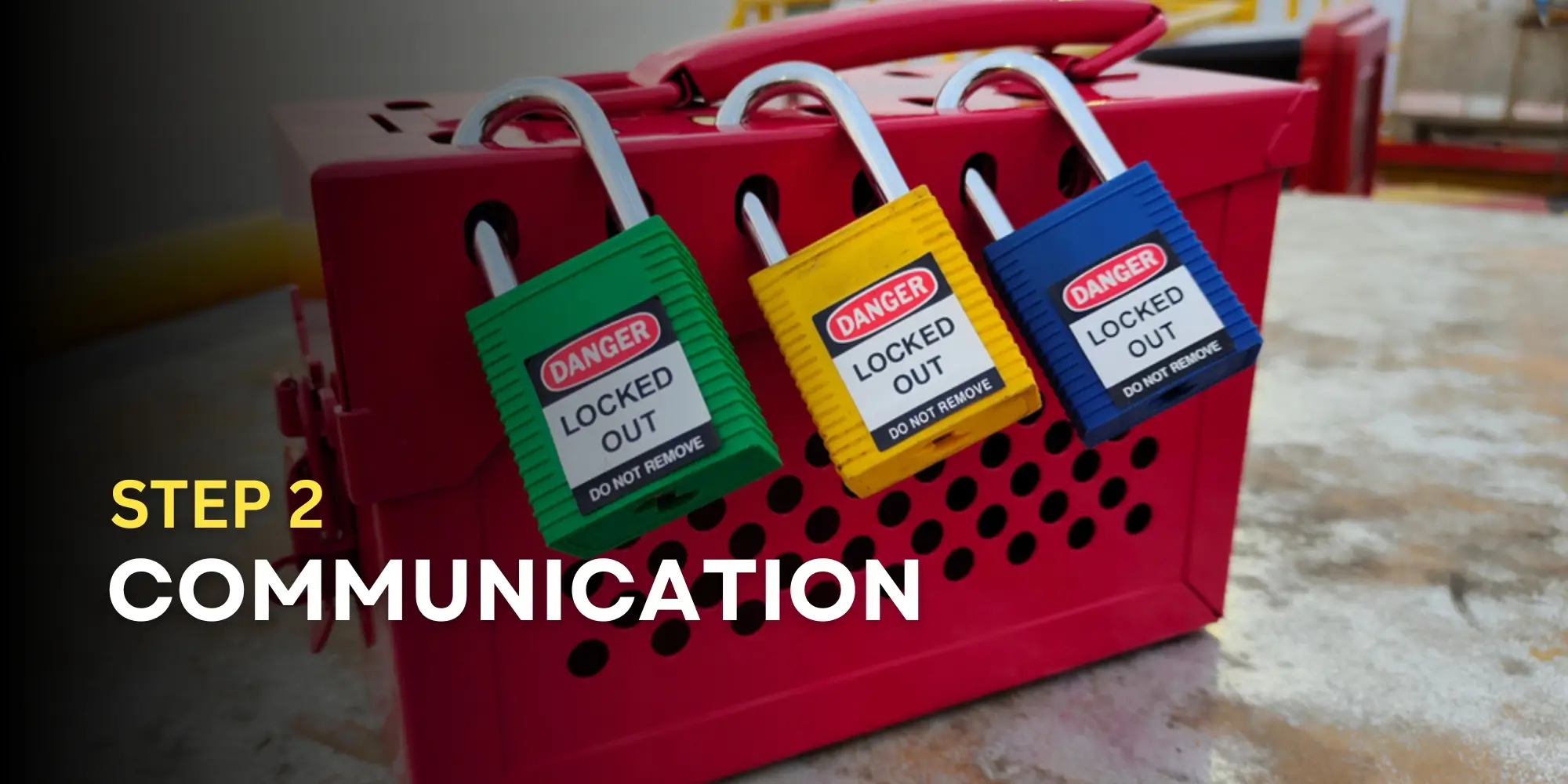
Step 2: Communication
Communication is the second key step in the Lockout/tagout (LOTO) procedure and plays a vital role in ensuring workplace safety. Before performing any lockout actions, it’s essential to inform all affected employees about the maintenance or servicing activity. This step helps prevent misunderstandings and accidental equipment use and ensures everyone is aware of potential hazards.
Notifying Affected Employees
Affected employees are those who operate the equipment or work in the area where the maintenance will take place. Communication should include:
- What equipment will be locked/tagged out
- Why the LOTO is being performed (e.g., for maintenance, repair, inspection)
- When will the procedure start, and its expected duration
- Who is responsible for performing the LOTO procedure
Clear and early communication builds awareness and ensures workers adjust their tasks accordingly.
Two-Way Communication
It’s important not just to give information but also to allow for questions or concerns from staff. This reinforces safety and ensures mutual understanding. Encourage workers to ask:
- Is there any backup system or alternate equipment available?
- What are the safety boundaries or restricted zones?
- How will they be informed when the equipment is safe to use again?
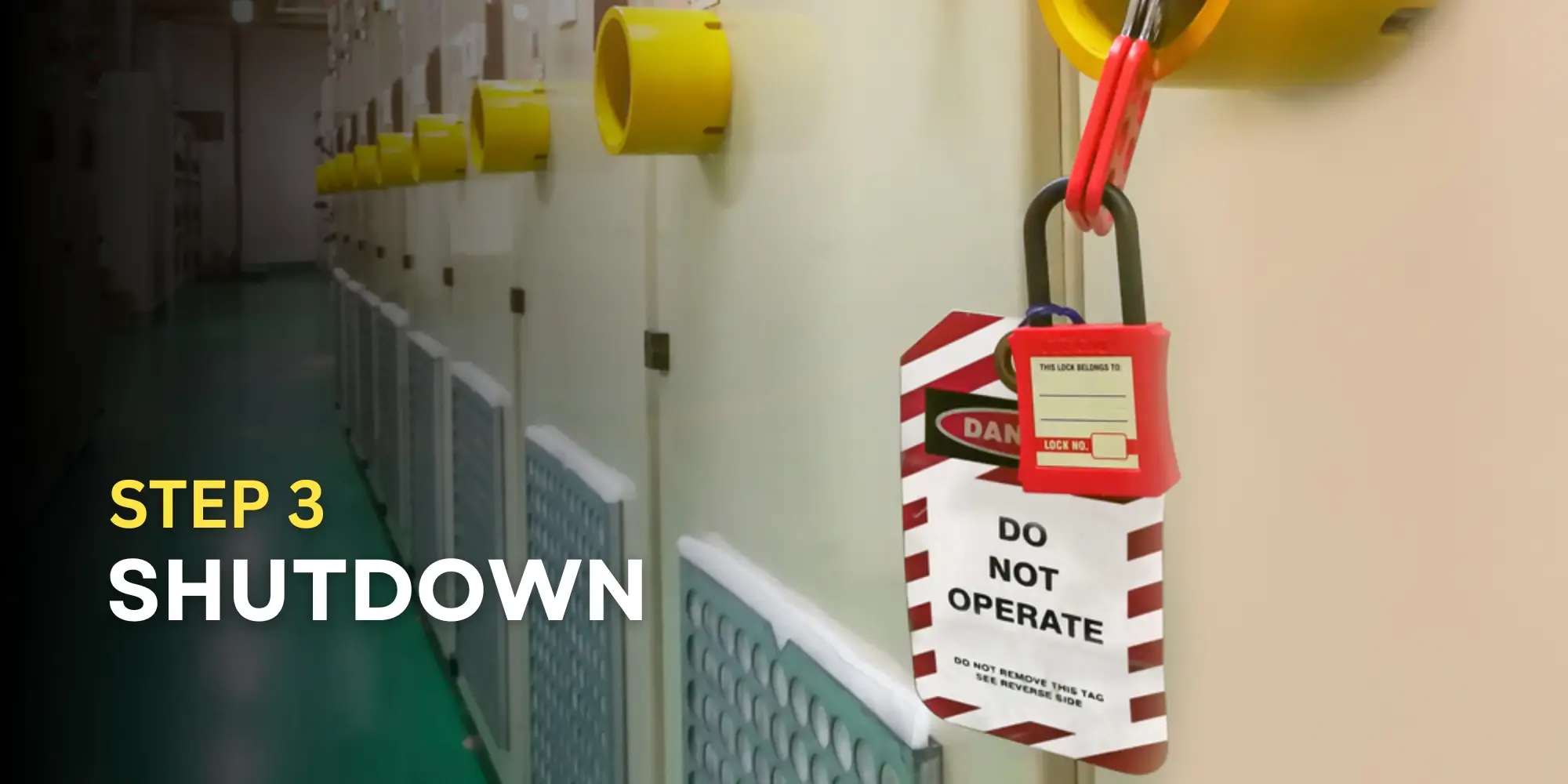
Step 3: Shutdown
The third step in the Lockout/Tagout (LOTO) procedure is shutdown, which involves safely turning off the equipment before any maintenance or servicing begins. This step must be done in accordance with the manufacturer’s guidelines or the company’s established procedures to ensure all components come to a complete stop and no energy remains active during the process.
Executing a Safe Shutdown
Authorized personnel should follow the standard operating procedures (SOPs) for shutting down each specific piece of equipment. Key actions include:
- Powering off the machine using control buttons, switches, or panels
- Ensuring all moving parts come to a complete stop
- Closing valves or disconnects related to fluid or gas systems
- Waiting for cooling or depressurization, if applicable
Do not assume that simply pressing the stop button is enough—some systems retain energy even after being switched off.
Reference Equipment Documentation
Always consult:
- The equipment’s user manual or energy control procedure
- Labels or diagrams that indicate specific shutdown steps
- Past maintenance records for known shutdown complexities
Properly shutting down the equipment is essential for preventing sudden movements or the release of hazardous energy. Skipping or rushing this step can lead to severe injuries or equipment damage.

Step 4: Isolation
Isolation is the fourth step in the Lockout/Tagout (LOTO) procedure and focuses on disconnecting the equipment from all energy sources to ensure it cannot be reactivated during maintenance or servicing. This step is critical in eliminating the risk of accidental startup or energy release that could endanger workers.
Isolate All Energy Sources
After the equipment is shut down, each energy source must be physically disconnected or blocked. Depending on the equipment, this may involve:
- Electrical: Turn off and disconnect power at the main breaker or control panel
- Mechanical: Block or restrain moving parts (e.g., gears, flywheels, belts)
- Hydraulic and Pneumatic: Shut off and bleed down pressure from lines and tanks
- Thermal: Allow equipment to cool or isolate heat sources
- Chemical: Close valves, drain lines, or neutralize substances
- Gravitational: Secure or lower suspended parts or loads
Use Isolation Devices
To ensure effective isolation, apply appropriate lockout devices to:
- Circuit breakers and switches
- Valves and actuators
- Disconnect handles
- Mechanical blocks and pins
Using a durable padlock or group lockout system, each device should be locked into the “off” or “safe” position.
Proper isolation ensures that energy sources are fully controlled and inaccessible, creating a safe environment for employees working on the equipment. Failing to isolate all energy sources can lead to severe accidents—make no assumptions and double-check every connection.
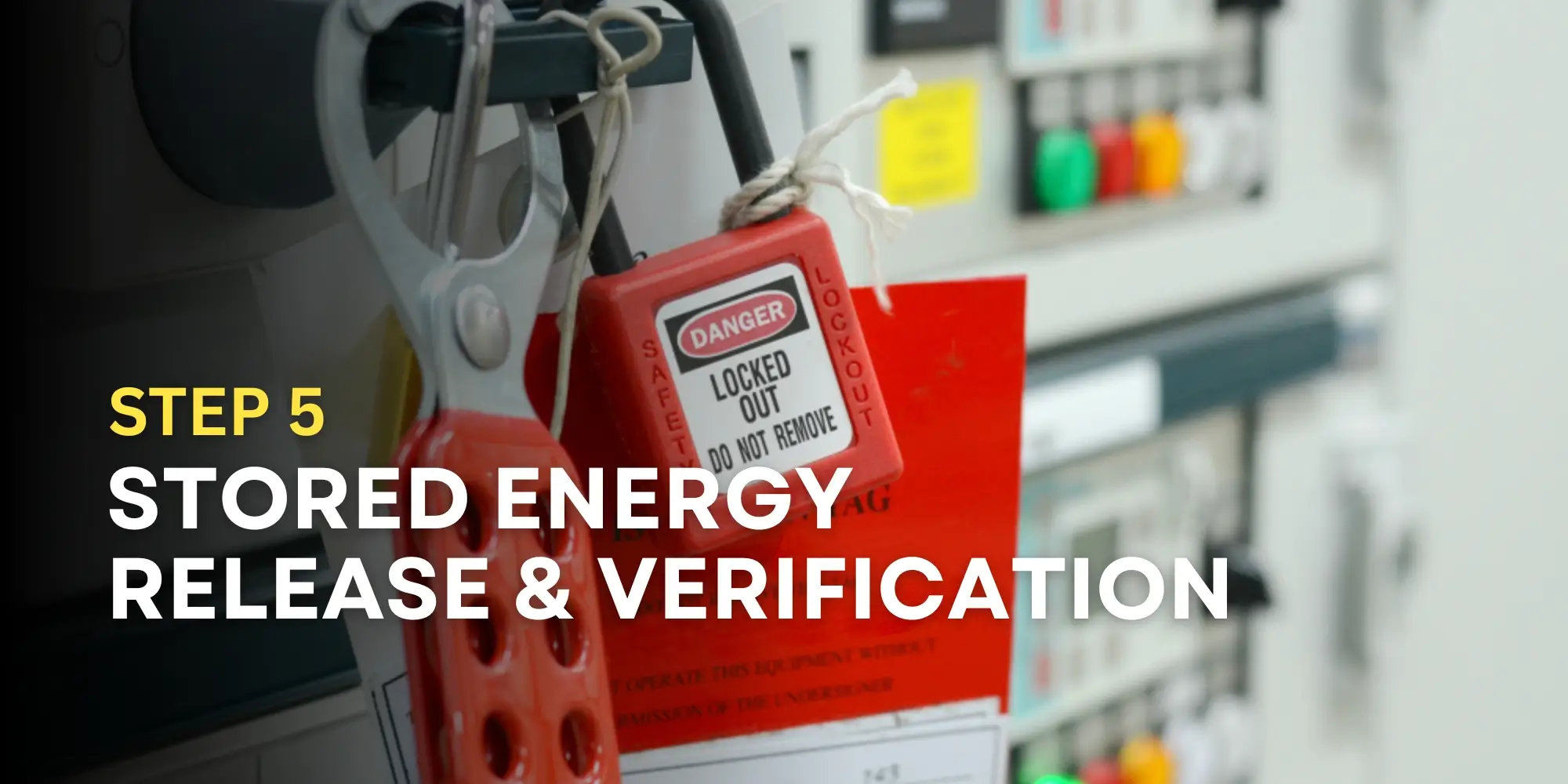
Step 5: Stored Energy Release & Verification
Once the equipment has been shut down and isolated, the next crucial step in the Lockout/Tagout (LOTO) procedure is to release any stored or residual energy and verify that the equipment is completely de-energized. Many machines retain energy even after being turned off, which can pose serious hazards if not properly discharged.
Release Stored or Residual Energy
Even after disconnection, energy can remain trapped within the system. It must be safely released or neutralized before any work begins. Common types of stored energy and methods for release include:
- Electrical: Discharge capacitors and residual current in circuits
- Mechanical: Block or restrain rotating or moving parts
- Hydraulic/Pneumatic: Drain fluid or air from cylinders, lines, and accumulators
- Thermal: Allow hot components to cool down completely
- Gravitational: Lower suspended parts to a resting position or support with blocks
Always follow equipment-specific guidelines to handle stored energy safely.
Verification of Zero Energy State
After releasing stored energy, the authorized employee must verify that all sources have been effectively isolated and de-energized. This includes:
- Attempting to start the machine using normal controls (known as a tryout)
- Using test instruments (e.g., multimeters, pressure gauges) to confirm zero energy
- Visually inspecting moving parts, gauges, or indicators
Only once verification is complete and no hazardous energy remains should maintenance or servicing begin.
Proper release and verification of stored energy is a lifesaving step in the LOTO process. Skipping this stage can lead to sudden, uncontrolled movements or energy discharges, putting workers at immediate risk. Always confirm—never assume—that the equipment is safe.
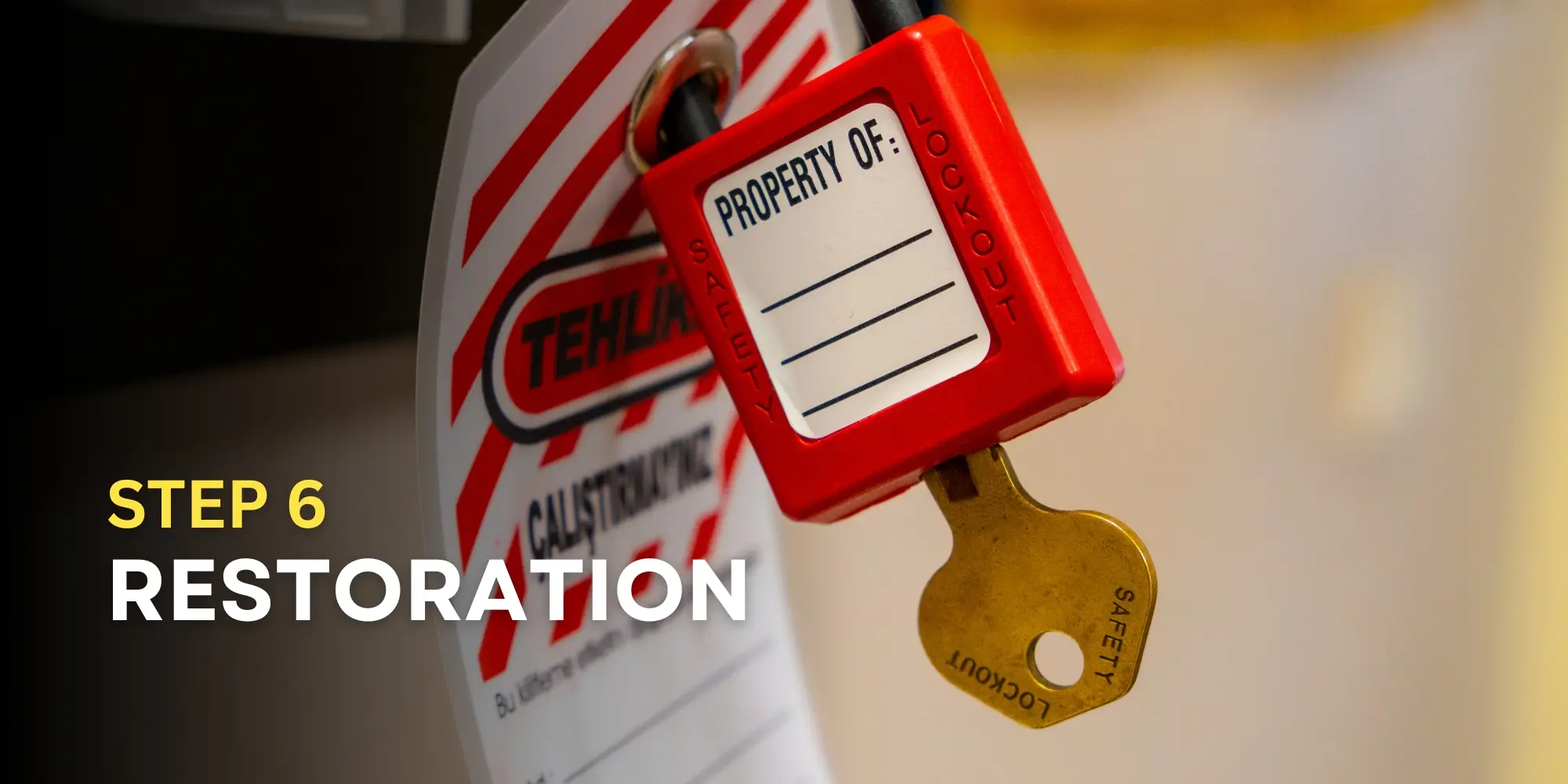
Step 6: Restoration
Restoration is the final step in the Lockout/Tagout (LOTO) procedure. Once maintenance or servicing is complete, it’s essential to safely restore the equipment to normal operating condition. This step involves systematically removing lockout/tagout devices, re-energizing equipment, and notifying affected employees—all while ensuring no one is at risk.
Remove LOTO Devices
Only the authorized employee who applied the lock and tag should remove them. Before doing so:
- Ensure all tools and parts are cleared from the work area
- Confirm that guards and safety covers are reinstalled
- Verify that all personnel are safely positioned away from the equipment
Important: Never attempt to remove someone else’s lock or tag without following proper protocol, which typically involves written authorization and supervisor approval.
Re-Energize and Test Equipment
After removing all LOTO devices:
- Reconnect energy sources (e.g., turn on breakers, open valves, reconnect air or power lines)
- Carefully restart the equipment following standard operating procedures
- Conduct a test run to ensure the system is functioning correctly and safely
Notify Affected Employees
Finally, inform all affected employees that:
- The maintenance work is complete
- The equipment has been returned to service
- It is now safe to resume normal operations
By following a controlled and careful restoration process, you ensure the equipment returns to service without exposing workers to hazards. This final step completes the LOTO procedure and reinforces your workplace’s commitment to safety and compliance.
Conclusion
Lockout/Tagout (LOTO) is more than just a procedural checklist—it’s a vital safeguard against workplace injuries and fatalities. By following the six-step LOTO procedure—preparation, communication, shutdown, isolation, stored energy release and verification, and restoration—you create a structured, reliable system that protects workers and keeps operations compliant with safety regulations.
When properly implemented, LOTO prevents accidents and promotes a culture of safety, accountability, and awareness across your organization. Investing in training, standardized procedures, and proper equipment today ensures your team can work confidently tomorrow. Make LOTO a core part of your safety program and treat it as the life-saving protocol it truly is.