March marks a transition period from winter to spring, bringing new workplace safety challenges and awareness campaigns. With the changing season, employees face new hazards such as increased outdoor work, ladder safety concerns, and weather-related risks. Additionally, March is designated for several national safety observances, making it an ideal time for employers to focus on key safety initiatives.
In this comprehensive guide, we’ll cover ten essential workplace safety topics for March, providing actionable insights to help organizations foster a safer work environment.
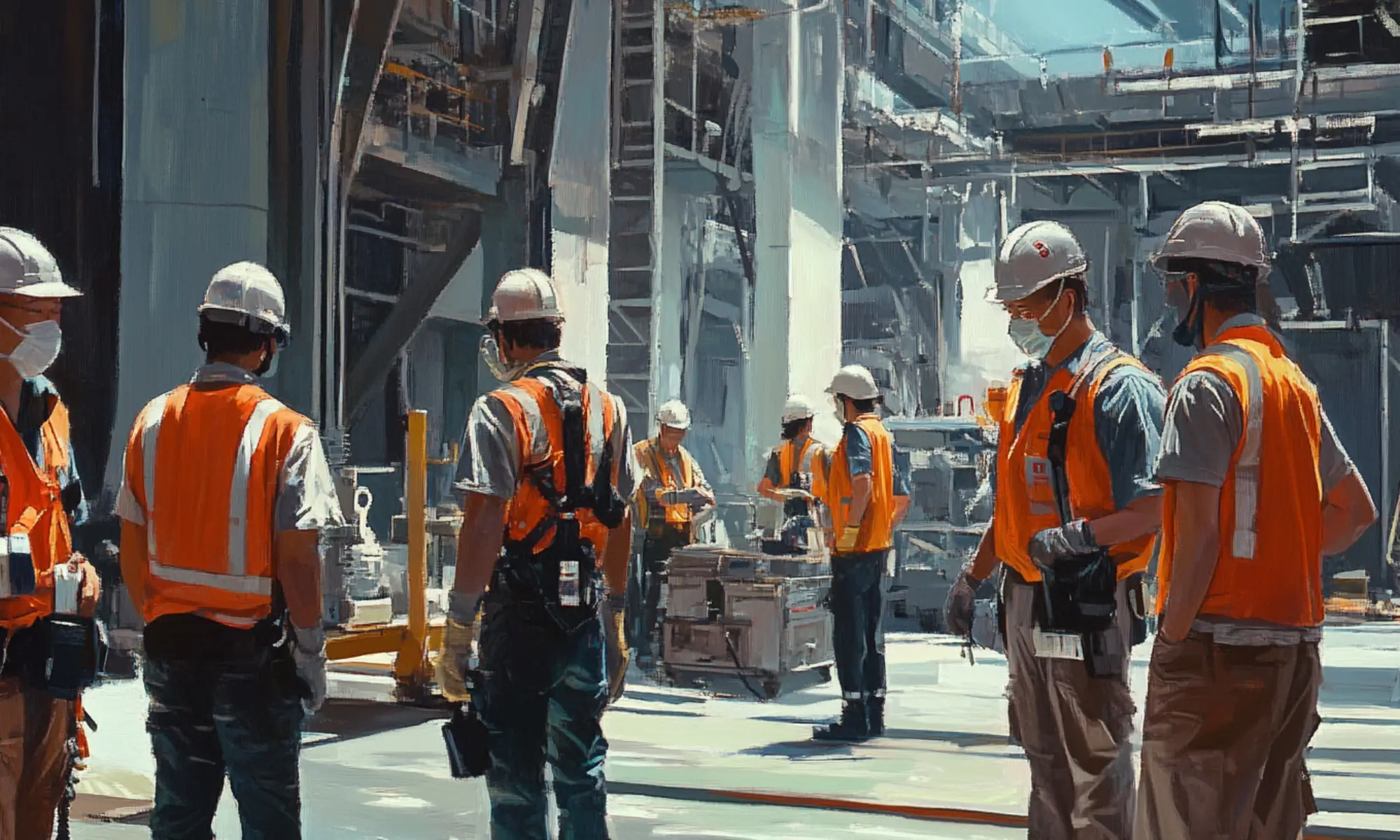
March Safety Topics: Key Workplace Safety Topics for the Month
March is a pivotal month for workplace safety, offering organizations the opportunity to focus on specific hazards and promote a culture of health and well-being. Here are key safety topics to emphasize this month:
1. Workplace Eye Wellness Month
Workplace Eye Wellness Month, led by Prevent Blindness America, focuses on the importance of eye safety and reducing workplace-related eye injuries. Whether in construction, manufacturing, healthcare, or office settings, employees are at risk of eye strain, exposure to hazardous chemicals, and physical injuries from flying debris.
Why It’s Important:
- 2,000+ eye injuries occur daily in the U.S. workplace (OSHA).
- 90% of these injuries could be prevented with proper eye protection.
- Digital eye strain affects employees who work long hours on screens, leading to headaches, blurred vision, and discomfort.
Key Safety Measures:
- Use ANSI-approved safety glasses or goggles in industrial and hazardous work environments.
- Encourage the 20-20-20 rule: Every 20 minutes, look at something 20 feet away for 20 seconds to reduce screen strain.
- Ensure proper lighting to reduce glare and eye fatigue.
- Maintain and test eye wash stations regularly to ensure quick response in case of chemical exposure.
- Educate employees on the risks and prevention of eye injuries through safety training sessions.
2. National Ladder Safety Month
The American Ladder Institute (ALI) dedicates March to National Ladder Safety Month, aiming to reduce falls and injuries caused by improper ladder use. Ladders are a common workplace tool but also a leading cause of fall-related injuries and fatalities.
Why It’s Important:
- Over 300 fatalities and 20,000 injuries occur each year due to ladder-related falls.
- Falls from ladders account for 28% of all fall-related deaths in workplaces.
Key Safety Measures:
- Inspect ladders before use to check for cracks, loose rungs, or structural weaknesses.
- Follow the 3-point contact rule: Always have two hands and one foot or two feet and one hand on the ladder.
- Position ladders properly: The 4-to-1 rule means placing the base one foot away from the wall for every four feet of height.
- Never exceed the ladder’s weight limit and use the correct ladder type for the job.
- Train employees on proper ladder usage and provide fall protection equipment when working at heights.
3. National Poison Prevention Week (March 17–23, 2024)
National Poison Prevention Week raises awareness about chemical exposure hazards in workplaces, particularly in manufacturing, healthcare, janitorial services, and laboratories. Exposure to toxic substances can result in skin burns, respiratory issues, poisoning, or long-term health damage.
Why It’s Important:
- Over 2.1 million poisoning cases are reported annually to U.S. poison control centers.
- Common workplace poisons include pesticides, cleaning agents, industrial solvents, and toxic gases.
Key Safety Measures:
- Label all chemicals properly with clear hazard warnings.
- Store chemicals in designated, ventilated areas to prevent leaks and accidental exposure.
- Ensure workers have access to MSDS (Material Safety Data Sheets) for hazardous substances.
- Train employees on handling, first aid, and emergency response for chemical spills.
- Keep emergency contacts and poison control hotline (1-800-222-1222) available in case of accidental exposure.
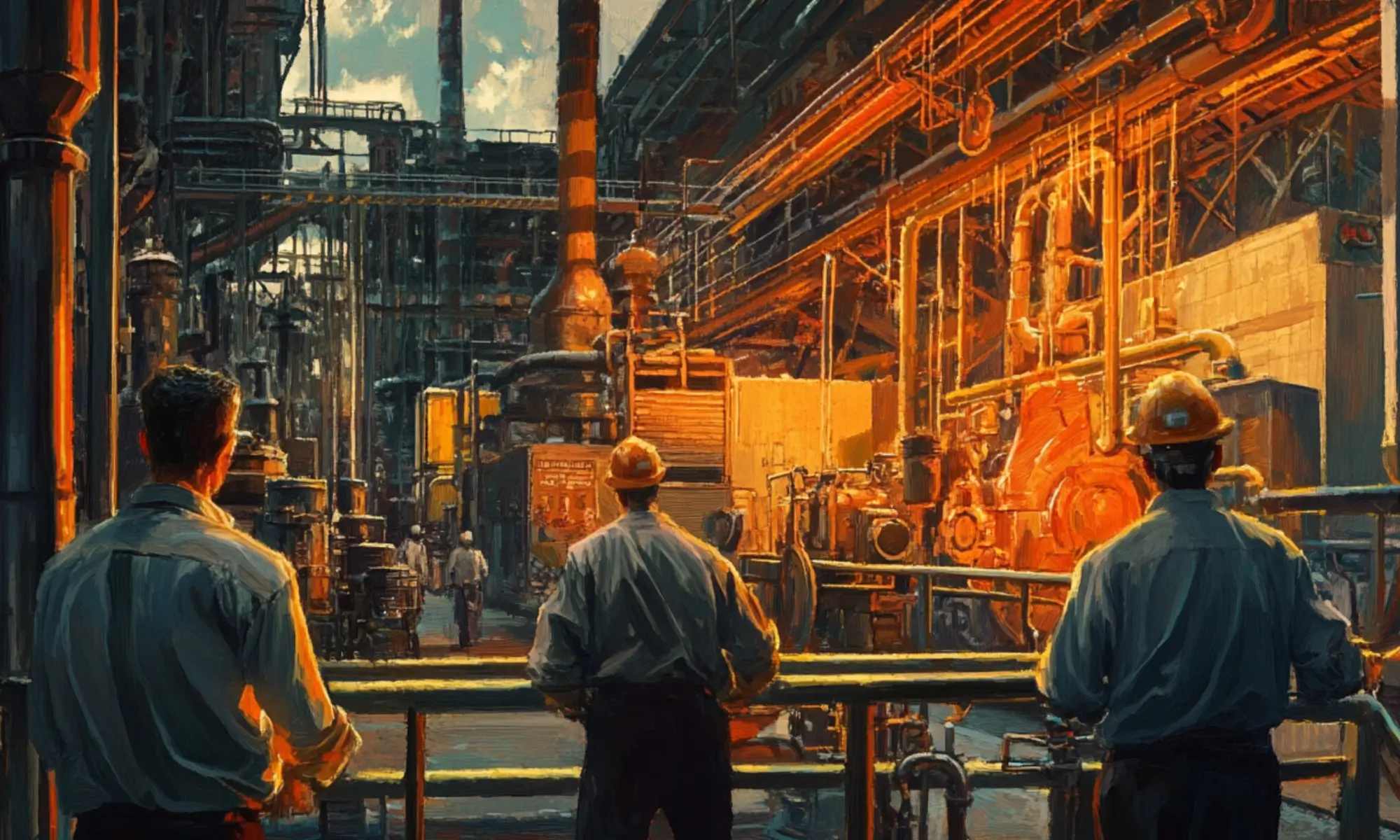
4. Brain Injury Awareness Month
March is Brain Injury Awareness Month, focusing on preventing traumatic brain injuries (TBIs) at work. Employees in construction, transportation, warehousing, and heavy machinery industries are at higher risk of falls, head impacts, and concussion injuries.
Why It’s Important:
- Every 9 seconds, someone in the U.S. sustains a brain injury.
- Falls account for nearly half of all workplace-related TBIs.
- Long-term effects of TBIs include memory loss, cognitive impairment, and chronic headaches.
Key Safety Measures:
- Require hard hats and head protection in hazardous work zones.
- Implement fall protection systems, including guardrails and harnesses, when working at heights.
- Encourage reporting of head injuries immediately and seek medical evaluation even if symptoms seem minor.
- Train workers to recognize concussion symptoms such as dizziness, nausea, and confusion.
- Conduct routine workplace audits to identify and eliminate head injury risks.
5. Sleep Awareness Week (March 14–21, 2024)
Fatigue and sleep deprivation are major causes of workplace accidents and productivity losses. Sleep Awareness Week, organized by the National Sleep Foundation, highlights the importance of rest and recovery for workplace safety and overall well-being.
Why It’s Important:
- Up to 13% of workplace injuries are linked to sleep deprivation.
- Drowsy driving and shift work contribute to thousands of transportation-related fatalities each year.
- Lack of sleep leads to slower reaction times, poor judgment, and decreased cognitive function.
Key Safety Measures:
- Encourage employees to maintain a consistent sleep schedule to regulate their circadian rhythm.
- Provide fatigue management training, especially for shift workers and long-hour employees.
- Offer designated rest areas or power nap stations in industries where fatigue is a major risk.
- Consider alternative work schedules, such as rotating shifts and workload adjustments, to reduce sleep disruption.
- Educate employees about the effects of sleep deprivation on safety, decision-making, and productivity.
6. Slips, Trips, and Falls Prevention
As snow melts and spring rains begin, workplace floors become slippery, increasing the risk of slips, trips, and falls. These incidents are among the most reported workplace injuries according to OSHA, particularly in construction, retail, manufacturing, and healthcare environments.
Why It’s Important:
- Over 20% of workplace injuries involve slips, trips, or falls.
- Slips and trips cause 15% of all accidental deaths in the workplace.
- Wet and uneven surfaces, poor footwear, and unsecured cords are common hazards.
Key Safety Measures:
- Place non-slip mats in entryways and high-traffic areas.
- Immediately clean spills and wet floors and post warning signs.
- Require employees to wear proper footwear with slip-resistant soles.
- Conduct regular workplace hazard inspections to remove obstacles.
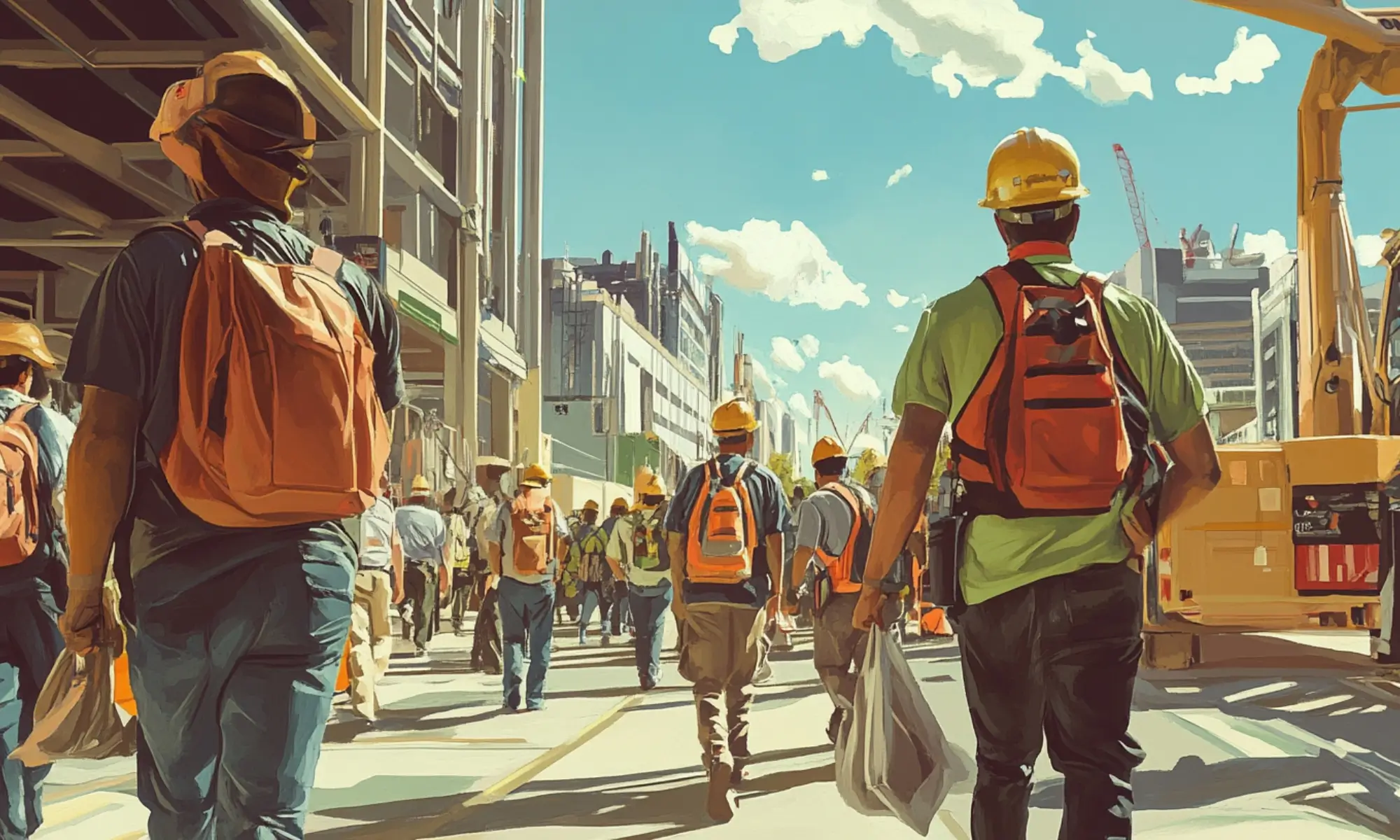
7. Severe Weather Preparedness
March is known for severe weather events, including tornadoes, heavy rains, and windstorms, which can disrupt business operations and endanger employees. Employers must ensure their workforce is prepared for emergencies.
Why It’s Important:
- Tornadoes and severe storms peak in March and April.
- High winds can turn unsecured objects into projectiles, causing injuries.
- Power outages and flooding can disrupt critical operations.
Key Safety Measures:
- Review and update Emergency Action Plans (EAPs) for different weather scenarios.
- Conduct severe weather drills so employees know evacuation routes and shelter locations.
- Ensure all employees have access to emergency communication (text alerts, sirens, intercoms).
- Secure outdoor materials and structures that could become airborne during storms.
8. Fire Safety and Prevention
With electrical hazards, heating equipment, and combustible materials, workplaces need to prioritize fire safety training to prevent devastating accidents. Fires can spread quickly, causing injuries, fatalities, and extensive property damage.
Why It’s Important:
- Fire incidents cost businesses over $2.3 billion annually in damages.
- Most workplace fires result from electrical failures, heating systems, or flammable substances.
- Proper training reduces panic and ensures a coordinated evacuation.
Key Safety Measures:
- Ensure all fire extinguishers are up-to-date, properly placed, and accessible.
- Conduct monthly fire drills to test emergency evacuation plans.
- Train employees on the PASS method (Pull, Aim, Squeeze, Sweep) to operate fire extinguishers.
- Keep electrical panels clear and inspect for overheating risks.
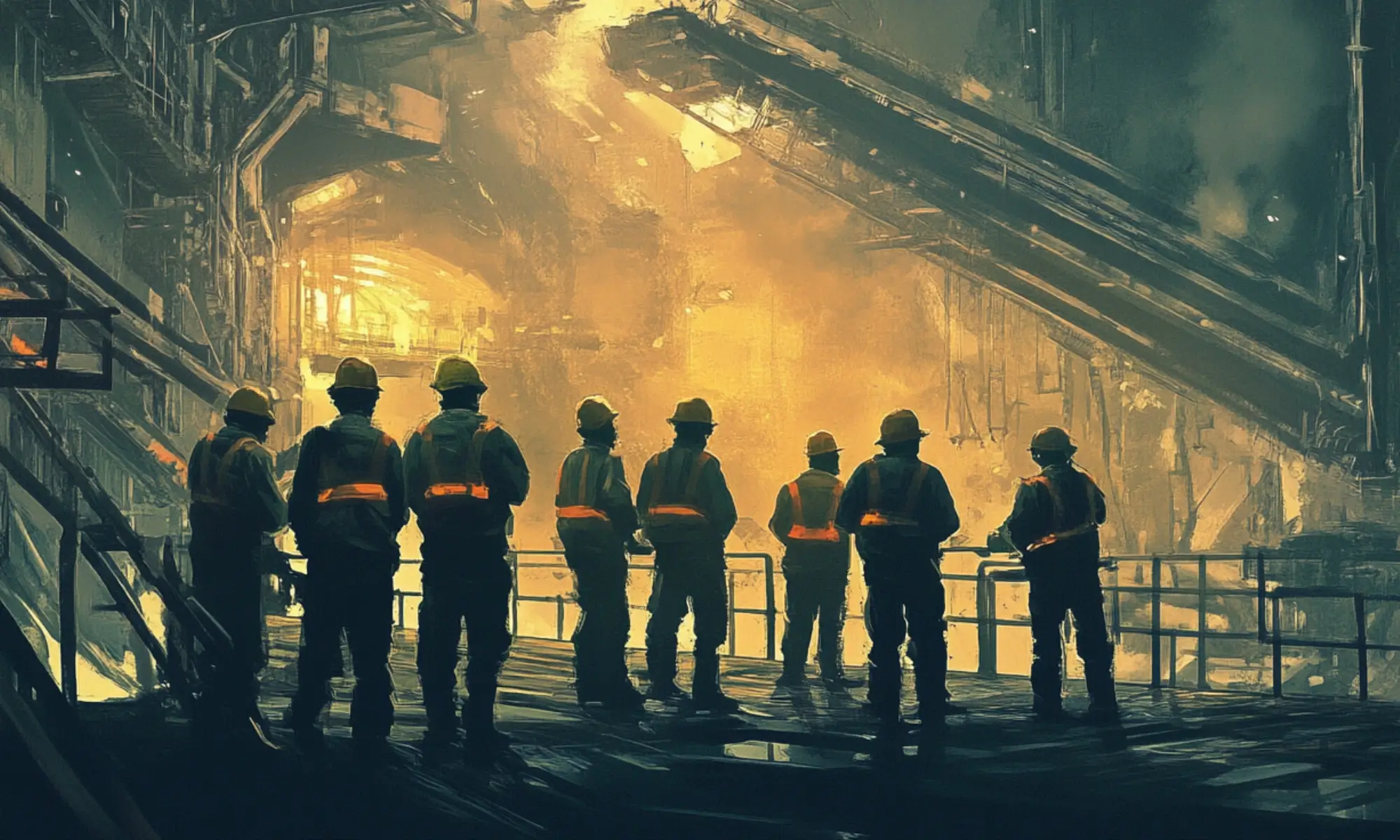
9. Electrical Safety Awareness
Electrical hazards are a major cause of shocks, burns, and electrocution in workplaces, especially in industries that rely on heavy machinery, power tools, and electrical systems. Proper training and regular inspections can prevent fatal accidents.
Why It’s Important:
- Electrical injuries result in 300+ deaths annually in the U.S.
- Overloaded circuits and damaged wiring are common hazards.
- OSHA requires Lockout/Tagout (LOTO) procedures to prevent electrocution.
Key Safety Measures:
- Inspect power cords and outlets for frays, exposed wires, and damage.
- Never overload power strips or circuits, as overheating can lead to fires.
- Follow Lockout/Tagout (LOTO) procedures when servicing electrical equipment.
- Require Personal Protective Equipment (PPE) like insulated gloves for high-voltage work.
10. Ergonomics and Workplace Safety
Poor ergonomics can lead to musculoskeletal disorders (MSDs), which cause chronic pain, injuries, and reduced productivity. Whether in office environments or physically demanding jobs, proper ergonomics can improve employee health and efficiency.
Why It’s Important:
- Work-related MSDs cost employers $50 billion per year in medical costs and lost productivity.
- Repetitive strain injuries (RSIs) make up 30% of all workplace injuries.
- Ergonomic adjustments can boost productivity by 25%.
Key Safety Measures:
- Adjust workstations for proper posture, ensuring monitors are at eye level.
- Encourage micro-breaks to prevent strain from prolonged sitting or repetitive tasks.
- Train employees on proper lifting techniques to avoid back injuries.
- Invest in ergonomic chairs, keyboards, and tools to reduce repetitive strain injuries.
Final Thoughts
March presents an opportunity for organizations to promote key safety initiatives that align with national awareness campaigns. By addressing these ten workplace safety topics, employers can ensure a safer, healthier, and more productive work environment for their teams.
Key Takeaways:
- Raise awareness about eye safety, ladder safety, and chemical exposure.
- Implement fatigue management and ergonomic programs.
- Prepare for severe weather and fire safety emergencies.
- Reduce risks of slips, trips, and falls with preventative measures.
- Prioritize employee training and regular safety audits.
By taking proactive steps this month, companies can foster a culture of safety that extends beyond March and into the rest of the year.