Personal Protective Equipment (PPE) is a crucial element of workplace safety, designed to protect workers from injuries, illnesses, and hazardous exposures. From helmets and gloves to respirators and safety goggles, PPE acts as a barrier between workers and the physical, chemical, biological, and mechanical risks they face on the job. Despite the clear benefits of wearing PPE, many workers still avoid using it — a dangerous habit that can lead to serious accidents, long-term health issues, and even fatalities.
Understanding why workers don’t wear PPE is essential for improving compliance and building a strong safety culture. In this article, we explore the top reasons why workers neglect PPE, the consequences of non-compliance, and how employers can motivate their workforce to wear PPE consistently. By addressing these challenges, organizations can create safer work environments, protect employees from harm, and ensure compliance with safety regulations.
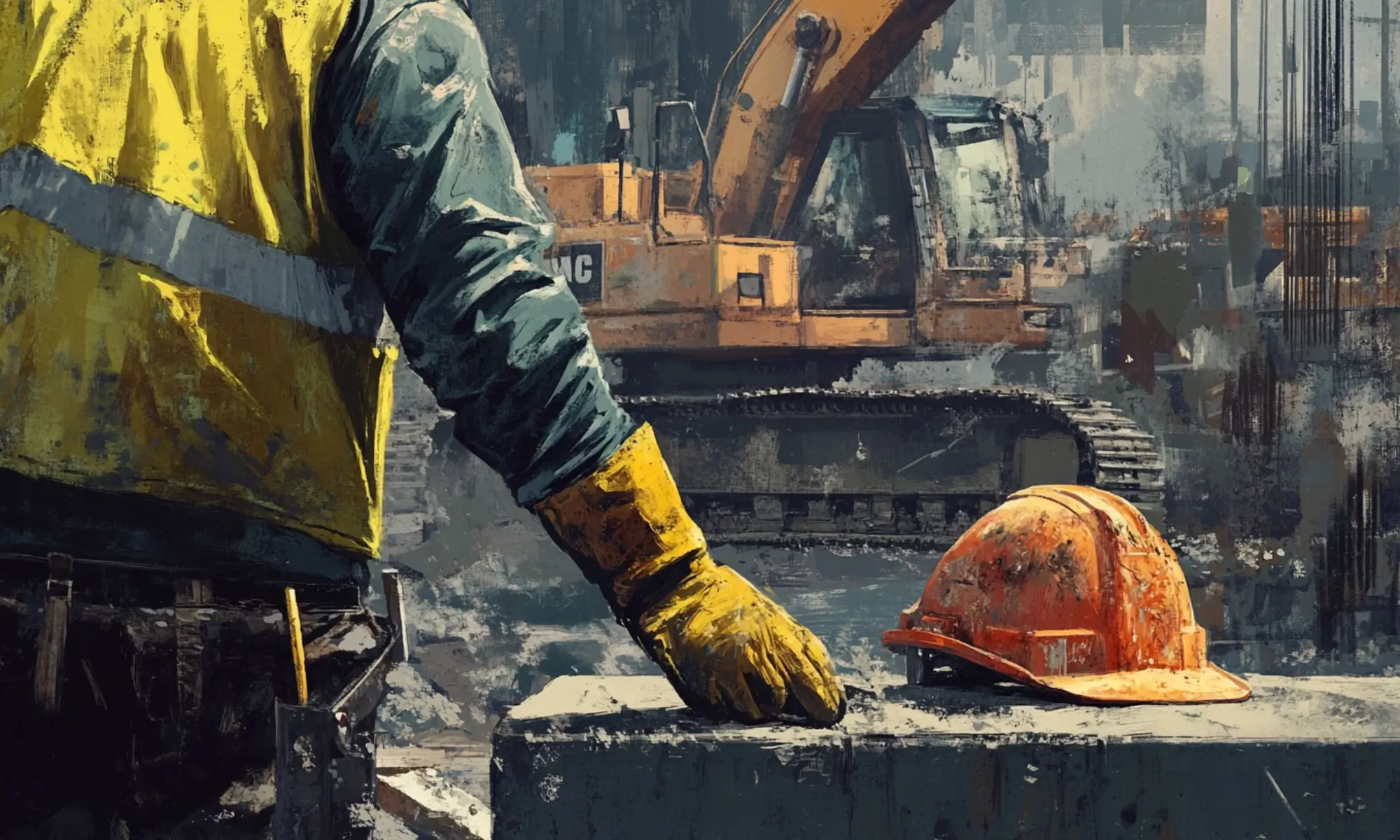
Importance Of Wearing Personal PPE
Personal Protective Equipment (PPE) refers to specialized clothing, equipment, or devices designed to protect workers from potential hazards, including physical, chemical, biological, radiological, and mechanical dangers in their work environment. PPE is essential in maintaining a safe and healthy workplace, and its importance cannot be overstated. Here are some reasons why wearing PPE is crucial:
- Protects against injuries and illnesses: PPE is a barrier between workers and potential hazards, minimizing the risk of injuries, infections, or exposure to harmful substances. It can protect the skin, eyes, respiratory system, and other body parts from various threats, including cuts, burns, chemicals, and infectious agents.
- Compliance with regulations: Employers are required by law to provide appropriate PPE and ensure that workers use it correctly. Wearing PPE is not only a best practice but also a legal requirement in many countries, with organizations like OSHA in the United States enforcing these regulations.
- Reduces downtime and associated costs: Injuries and illnesses can lead to employee absenteeism, decreased productivity, and increased workers’ compensation claims. PPE can help prevent these issues by reducing the likelihood of workplace accidents and the associated financial burdens.
- Boosts worker morale and productivity: Employees who feel safe and protected at work are likelier to be engaged and productive. Providing and enforcing PPE demonstrates an employer’s commitment to worker safety, which can contribute to a positive work environment.
- Protects the public: In some industries, such as healthcare, properly using PPE is crucial in protecting patients or the public from infections and other hazards. By wearing PPE, workers in these settings can prevent the spread of diseases, reduce the risk of outbreaks, and improve public health.
- Supports a safety culture: When organizations prioritize safety, it fosters a culture of responsibility and care. Wearing PPE and adhering to safety protocols can help create a positive safety culture, which benefits everyone involved.
- Customization for specific hazards: PPE is designed to address specific risks in various industries, making it an effective solution for a wide range of workplace hazards. From construction to chemical laboratories, PPE can be tailored to provide the appropriate level of protection.
To ensure the effectiveness of PPE, it is essential to select the right equipment for the job, provide proper training on its use, and perform regular maintenance and inspections. By doing so, workplaces can significantly reduce the risk of injuries and illnesses, promoting a safe and healthy work environment.

Consequences Of Not Wearing Personal Protective Equipment (PPE)
Personal Protective Equipment (PPE) is designed to protect workers from injuries, illnesses, and hazardous exposures in the workplace. Failure to wear PPE increases the risk of accidents and long-term health issues, compromising worker safety and employer liability. Here are the key consequences of not wearing PPE:
1. Increased Risk of Injuries and Fatalities
PPE serves as the last line of defense against workplace hazards. Without it, workers are more vulnerable to:
- Head injuries from falling objects or impacts.
- Eye injuries from flying debris, chemicals, or dust.
- Hearing loss from exposure to loud machinery.
- Burns from chemicals, fire, or hot surfaces.
- Respiratory issues from inhaling toxic fumes or dust.
Example: A worker not wearing a helmet in a construction zone could suffer a fatal head injury from a falling object.
2. Exposure to Long-Term Health Risks
Certain hazards may not cause immediate injuries but can lead to severe health problems over time:
- Prolonged exposure to noise can result in permanent hearing loss.
- Inhalation of harmful chemicals or asbestos can lead to lung cancer or respiratory diseases.
- Contact with toxic substances can cause skin disorders and chemical burns.
Example: A welder without respiratory protection may develop lung disease after years of inhaling metal fumes.
3. Legal and Regulatory Penalties
Regulatory bodies like OSHA (Occupational Safety and Health Administration) have strict PPE requirements.
- Employers face fines, lawsuits, and penalties for not enforcing PPE use.
- Injured workers can pursue legal action for negligence.
- Violations may lead to suspension of business operations.
Example: An employer could face thousands of dollars in fines for failing to provide proper eye protection in a high-risk environment.
4. Reduced Productivity and Operational Disruption
Workplace accidents due to lack of PPE can disrupt business operations:
- Injured workers result in staff shortages and production delays.
- Investigation and compensation processes cause downtime and financial loss.
- Replacement of injured employees increases recruitment and training costs.
Example: A worker suffering a hand injury due to a lack of gloves may require weeks of medical leave, which can affect team output.
5. Increased Medical and Compensation Costs
Workplace injuries result in:
- Medical expenses for treatment, rehabilitation, and follow-ups.
- Workers’ compensation claims and increased insurance premiums.
- Costs for retraining and replacing injured workers.
Example: A back injury from a lack of a supportive harness could lead to long-term disability payments.
6. Damage to Equipment and Property
Failure to wear PPE can lead to accidents that damage machinery or facilities:
- Chemical spills due to a lack of gloves can corrode equipment.
- Improper footwear can cause slips that damage machinery or inventory.
- Fire hazards due to lack of flame-resistant clothing can destroy property.
Example: A worker’s loose clothing catching fire could damage an entire production line.
7. Reduced Employee Morale and Trust
A workplace that neglects PPE use sends a message that worker safety is not a priority:
- Injuries and accidents create a climate of fear and distrust.
- Reduced morale increases turnover and decreases employee engagement.
- Workers are less likely to follow safety rules if they feel management doesn’t value safety.
Example: Workers may feel discouraged and less motivated to work after a preventable accident.
8. Reputation Damage
Frequent workplace accidents or safety violations can harm a company’s reputation:
- Negative press can deter customers and potential employees.
- Poor safety records may lead to the loss of business contracts.
- Reputation damage may make it harder to attract skilled workers.
Example: A construction company with multiple safety violations may struggle to win new contracts.
9. Psychological and Emotional Impact
Witnessing a workplace injury or accident can have a lasting psychological effect on other workers:
- Anxiety and stress about safety can reduce focus and performance.
- Fear of injury may cause workers to avoid certain tasks or roles.
- Post-traumatic stress can lead to mental health issues.
Example: A worker may refuse to operate heavy machinery after witnessing a severe accident.
10. Loss of Business and Financial Stability
Workplace accidents due to non-compliance with PPE standards can lead to:
- Loss of contracts with clients who prioritize safety.
- Increased insurance premiums due to poor safety records.
- Business shutdown or bankruptcy if accidents lead to lawsuits or regulatory action.
Example: A manufacturing plant forced to close due to repeated OSHA violations may face permanent loss of revenue.
Not wearing PPE can have severe consequences for both workers and employers, ranging from injuries and health risks to legal penalties and business losses. To prevent these issues, employers must ensure that PPE is available, properly fitted, comfortable, and used consistently. Promoting a strong safety culture, enforcing PPE policies, and providing ongoing training can significantly reduce these risks and create a safer work environment.
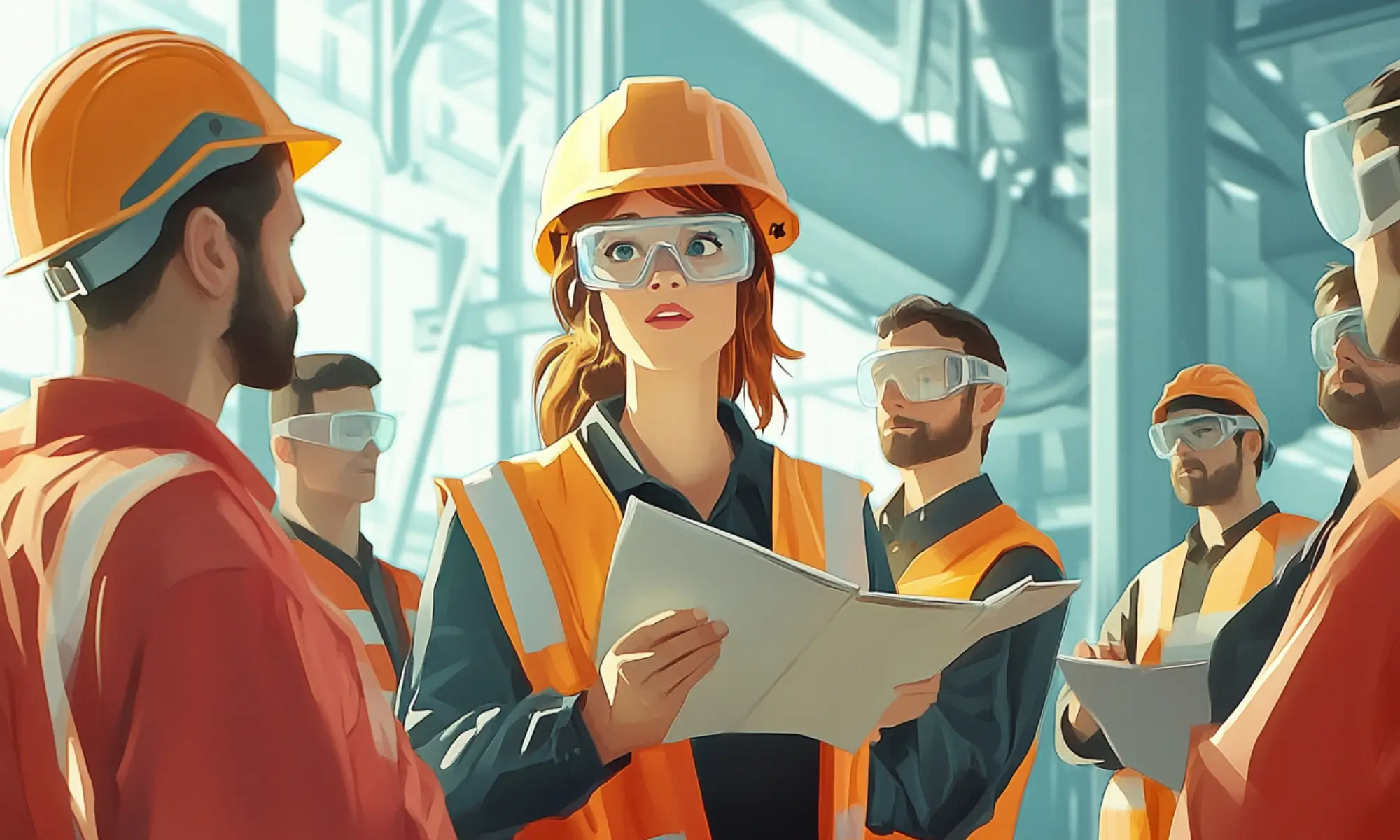
Why Workers Don’t Wear PPE And How Can You Motivate Them
Workers sometimes neglect to wear Personal Protective Equipment (PPE) for various reasons. However, addressing these concerns and motivating them to use PPE for their safety and well-being is crucial. Here are 10 common reasons why workers don’t wear PPE and suggestions for motivating them:
1. Lack Of Awareness
Lack of awareness can contribute to workers not wearing Personal Protective Equipment (PPE). Workers may be unfamiliar with the hazards they face in their work environment or the equipment designed to protect them from those hazards. This lack of awareness can stem from various reasons, such as inadequate safety training, insufficient onboarding procedures, high employee turnover, or a constantly evolving work environment.
To address this issue, it is essential to implement comprehensive safety training programs that focus on:
- Hazard identification: Teach workers how to recognize hazards in their specific work environment, including physical, chemical, biological, and ergonomic risks.
- Risk assessment: Help workers understand the potential consequences of exposure to these hazards, such as injuries, illnesses, or long-term health effects.
- PPE selection: Educate employees about the types of PPE suitable for different hazards and how to use them properly. This includes explaining the purpose, limitations, and effectiveness of each type of PPE.
- PPE care and maintenance: Train workers to inspect, clean, maintain, and store PPE to ensure its effectiveness and longevity.
- Workplace safety culture: Encourage a safety-oriented mindset by promoting open communication about safety concerns, emphasizing the importance of reporting hazards, and creating an environment where workers feel responsible for their safety and that of their colleagues.
Regular safety training sessions, such as toolbox talks or safety briefings, can help reinforce this knowledge and keep workers up-to-date with any changes in hazards or PPE requirements. By educating workers about the importance of PPE and how it can protect them from potential risks, you can increase their awareness and encourage them to wear PPE consistently.
2. Discomfort
Discomfort is a common reason workers may avoid wearing Personal Protective Equipment (PPE). Uncomfortable PPE restricts movement or causes irritation and can discourage employees from using it consistently. Employers should focus on providing ergonomic and well-fitting equipment to address this issue and encourage PPE usage. Here are some strategies to improve the comfort of PPE:
- Conduct a thorough assessment of the PPE to identify the sources of discomfort. This could involve gathering worker feedback, consulting with safety experts, or analyzing injury and discomfort reports.
- Offer PPE in various sizes and styles to ensure a proper fit for all employees. Ill-fitting equipment can not only cause discomfort but also compromise the effectiveness of the PPE.
- Opt for lightweight and breathable materials that minimize heat buildup and reduce the risk of heat stress. This is particularly important for workers who perform tasks in hot environments or for extended periods.
- Choose PPE with adjustable features, such as straps, buckles, or fasteners, that allow workers to customize the fit and ensure optimal comfort.
- Look for PPE designed with ergonomic principles, as these products are more likely to promote comfort and ease of movement. This may include padding in high-pressure areas, curved shapes that follow the body’s natural contours, or designs that distribute weight evenly.
- Train workers on how to wear and adjust PPE properly. This can help minimize discomfort by ensuring the equipment is worn as intended.
- Monitor and regularly update PPE based on workers’ feedback and technological advances. Newer PPE models often incorporate improved designs and materials that can enhance comfort.
By providing workers with ergonomic and well-fitting PPE, employers can significantly improve comfort levels and increase the likelihood that employees will wear the equipment consistently, leading to a safer work environment.
3. Inconvenience
Inconvenience caused by PPE can discourage workers from wearing it consistently. Cumbersome, bulky, or difficult-to-use equipment can interfere with workers’ ability to perform tasks efficiently and even create additional safety risks. To address this issue, employers should opt for lightweight, easy-to-use PPE that minimizes hindrance while maintaining protection. Here are some strategies to achieve this:
- Research and invest in innovative PPE designs prioritizing protection and user convenience. Manufacturers are constantly developing new products that offer improved comfort, flexibility, and ease of use.
- Choose PPE from lightweight materials that provide adequate protection without adding unnecessary bulk. This can help reduce workers’ physical strain and increase their overall efficiency.
- Opt for modular or multi-purpose PPE when appropriate. These can offer multiple protective functions in a single piece of equipment, reducing the need for workers to wear multiple items.
- Train workers on the proper use and adjustment of PPE to minimize the time spent putting on, removing, or adjusting the equipment. This can also help workers feel more comfortable and confident while using PPE.
- Consult with workers to identify areas where PPE may hinder their efficiency, and work together to find suitable solutions that maintain protection without compromising productivity.
- Regularly evaluate and update PPE based on workers’ feedback and technological advances. As new products become available, employers can consider incorporating them into their PPE program to reduce inconvenience and improve efficiency.
- Organize the workplace to make PPE easily accessible and clearly visible. This can help ensure that workers can quickly and easily don their PPE when required without wasting time searching for the necessary equipment.
By prioritizing lightweight and easy-to-use PPE, employers can minimize the inconvenience experienced by workers while maintaining a high level of protection, ultimately encouraging consistent PPE use and fostering a safer work environment.
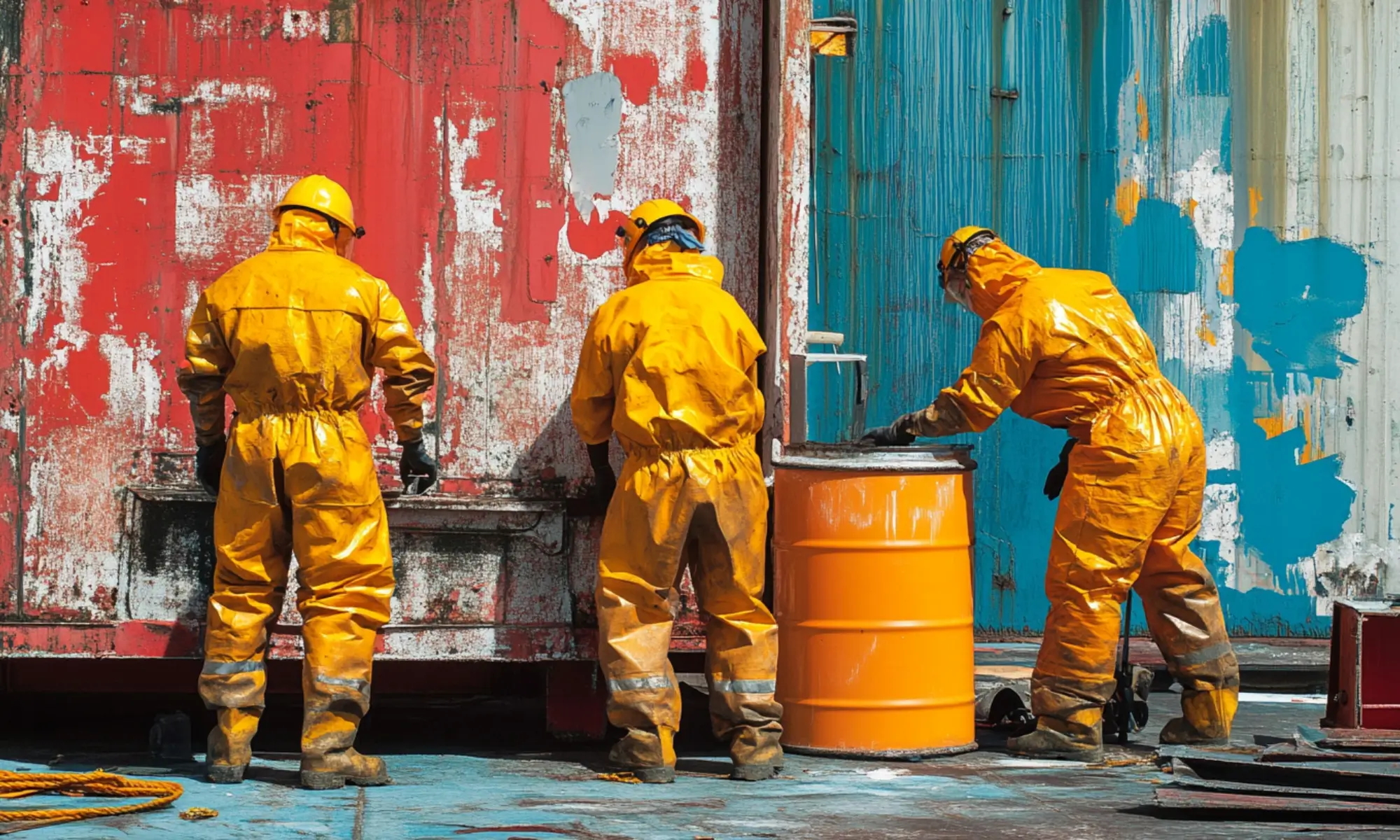
4. Lack Of Enforcement
Lack of enforcement of PPE rules can significantly impact workers’ compliance with wearing Personal Protective Equipment. When supervisors and managers do not consistently enforce PPE rules, workers may perceive that it is not necessary or important, leading to non-compliance. To address this issue, employers should implement a clear PPE policy and ensure that managers and supervisors enforce the rules consistently. Here are some steps to achieve this:
- Develop a comprehensive PPE policy: Create a written policy that outlines the specific PPE requirements for various tasks and roles, as well as the responsibilities of workers, supervisors, and management. This policy should be aligned with local regulations and industry best practices.
- Communicate the policy: Ensure all employees know the PPE policy’s requirements and responsibilities. This can be achieved through training sessions, written materials, or visual aids like posters and signage.
- Train supervisors and managers: Provide training on the PPE policy, the importance of enforcing PPE rules, and the potential consequences of non-compliance. This training should emphasize the role of supervisors and managers in fostering a safety culture and leading by example.
- Establish clear consequences: Define the consequences for workers who fail to comply with PPE requirements, such as verbal warnings, written warnings, or even disciplinary action. These consequences should be clearly communicated to all employees.
- Monitor compliance: Regularly assess workers’ compliance with PPE requirements through inspections, audits, or observations. This can help identify areas where enforcement may be lacking and allow for corrective action to be taken.
- Hold supervisors and managers accountable: Ensure that supervisors and managers are held accountable for enforcing PPE rules and addressing non-compliance. This may include performance evaluations, feedback, or even disciplinary measures if necessary.
- Encourage reporting: Create an environment where workers feel comfortable reporting PPE non-compliance or concerns without fear of retaliation. This can help identify issues and provide opportunities for improvement.
- Provide ongoing support: Offer resources and guidance to supervisors and managers as they enforce PPE rules. This may include access to safety experts, refresher training, or regular safety meetings to discuss challenges and best practices.
Employers can create a safety culture that encourages workers to wear PPE consistently by implementing a clear PPE policy and ensuring consistent enforcement by supervisors and managers. This will lead to a safer and more productive work environment.
5. Perception Of Invincibility
Perception of invincibility is a common cognitive bias where workers may feel immune to the hazards in their work environment. This belief can lead to PPE non-compliance, as workers may underestimate their risks and the consequences of not using proper protection. To address this issue, employers can use various strategies to emphasize the importance of PPE in preventing accidents and injuries:
- Share real-life stories: Presenting case studies, testimonials, or stories of accidents and injuries due to PPE non-compliance can help workers better understand the potential consequences of not wearing PPE. These stories can be more relatable and impactful than mere statistics, as they humanize the risks involved.
- Provide relevant statistics: Share industry-specific data on accidents, injuries, and fatalities related to PPE non-compliance. This information can help workers grasp the prevalence and severity of hazards in their work environment and the importance of using PPE to mitigate these risks.
- Conduct hazard demonstrations: Demonstrating the potential hazards and risks through practical exercises or simulations can help workers visualize and experience the dangers firsthand, making the need for PPE more evident.
- Invite guest speakers: Bring safety experts, industry professionals, or individuals who have experienced accidents or injuries due to PPE non-compliance to share their knowledge and experiences with your workers. Hearing firsthand accounts can help break down the perception of invincibility.
- Encourage open communication: Create a culture where workers feel comfortable discussing safety concerns, sharing experiences, and learning from each other. This can help dispel misconceptions and foster a greater appreciation for the importance of PPE.
- Highlight the benefits of PPE: In addition to focusing on the potential consequences of not wearing PPE, emphasize the benefits of proper PPE use, such as reduced injury rates, increased productivity, and improved overall well-being.
- Lead by example: Supervisors and managers should consistently wear PPE and follow safety guidelines, demonstrating their commitment to safety and reinforcing the importance of PPE to their workers.
By sharing real-life stories, statistics, and experiences, employers can help dispel workers’ perceptions of invincibility and emphasize the critical role of PPE in preventing accidents and injuries, ultimately fostering a safer work environment.
6. Peer Pressure
Peer pressure can significantly impact workers’ compliance with PPE usage. If workers see their coworkers not wearing PPE, they may feel less inclined to use it themselves. To combat this issue, employers should encourage a safety culture where everyone is responsible for their safety and that of their colleagues. Here are some strategies to promote a positive safety culture and address the impact of peer pressure:
- Lead by example: Ensure supervisors, managers, and team leaders consistently wear PPE and follow safety guidelines. This will set a standard for workers to follow and show that safety is a priority at all levels of the organization.
- Offer regular safety training: Provide ongoing safety training emphasizing the importance of PPE, the workplace’s potential hazards, and the workers’ responsibilities to protect themselves and their colleagues.
- Establish a buddy system: Pair workers together to act as safety partners, encouraging them to watch for each other’s safety and hold each other accountable for wearing PPE.
- Promote open communication: Create an environment where workers feel comfortable discussing safety concerns, sharing experiences, and reporting PPE non-compliance without fear of retaliation.
- Recognize and reward compliance: Acknowledge and reward workers who consistently wear PPE and are committed to safety. This can be done through informal recognition, performance evaluations, or incentive programs.
- Encourage worker involvement: Involve workers in developing and implementing safety policies and procedures, including PPE selection and training. This can help foster a sense of ownership and commitment to safety among workers.
- Create a safety committee: Establish a safety committee of workers from different levels and departments within the organization. This committee can help identify and address safety concerns, including PPE non-compliance, and serve as safety ambassadors, promoting a positive safety culture among their peers.
- Share success stories: Highlight examples of teams or individuals who have successfully implemented PPE usage and experienced positive outcomes, such as reduced injury rates or improved productivity. This can help demonstrate the benefits of PPE compliance and encourage others to follow suit.
By encouraging a safety culture where everyone is responsible for their own safety and that of their colleagues, employers can mitigate the impact of peer pressure and promote consistent PPE usage, leading to a safer and more productive work environment.
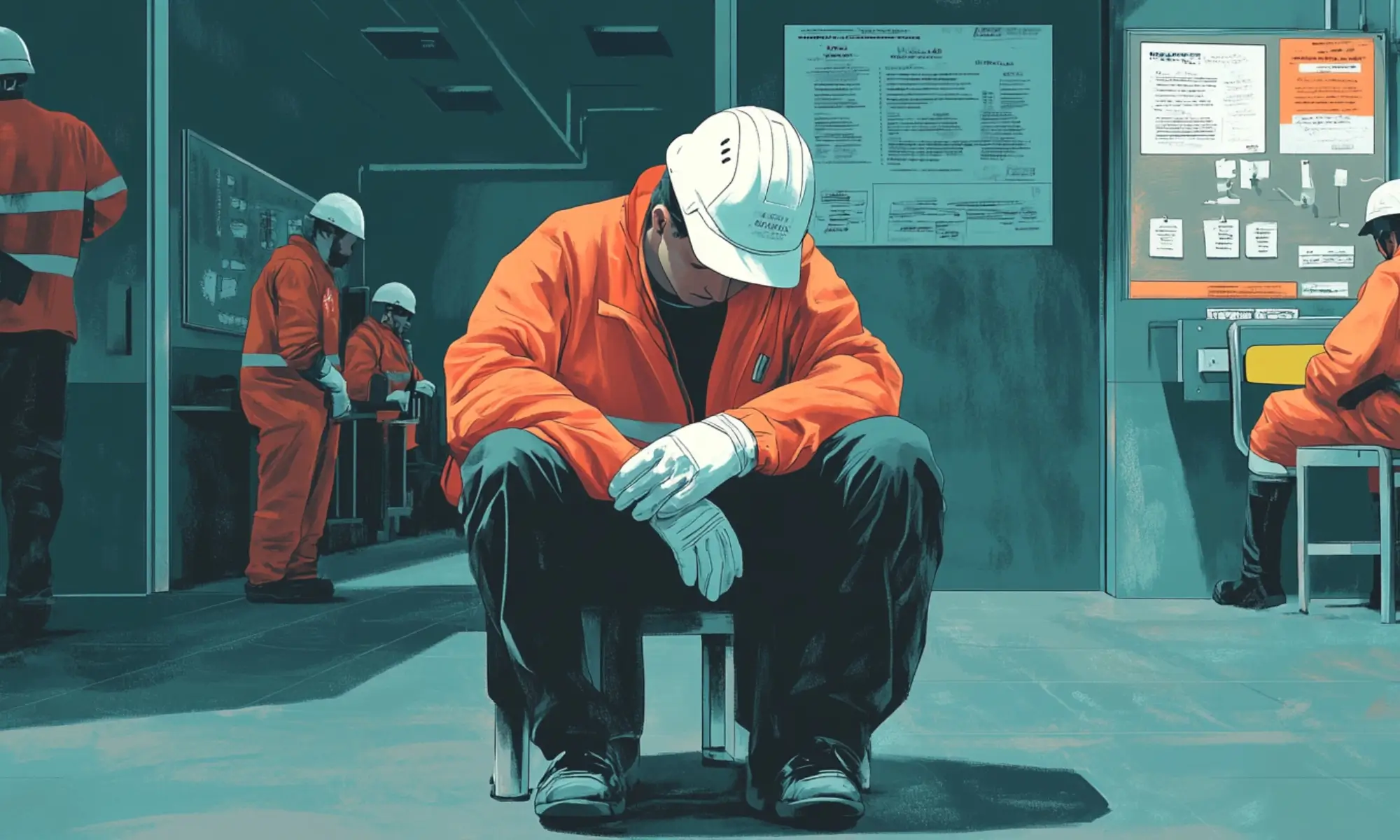
7. Limited Availability
The limited availability of PPE can be a significant barrier to workers using it consistently. If PPE is not readily available or in short supply, workers may not have access to the necessary equipment, which can lead to non-compliance. To address this issue, employers should ensure a consistent supply of high-quality equipment and make it easily accessible for all employees. Here are some steps to achieve this:
- Conduct a thorough assessment: Analyze the specific PPE needs for organizational tasks and roles, including identifying the types, quantities, and sizes of PPE required.
- Establish a reliable supply chain: Partner with reputable suppliers who consistently provide high-quality PPE that meets industry standards and regulations. Regularly review and assess suppliers’ performance to ensure they continue to meet your organization’s needs.
- Maintain adequate inventory: Keep an appropriate stock of PPE on hand to accommodate fluctuations in demand, such as changes in staffing levels, seasonal variations, or unexpected situations. Implement an inventory management system to track PPE usage and avoid shortages.
- Allocate a dedicated budget: Set aside a specific PPE procurement and maintenance budget, ensuring that financial constraints do not compromise worker safety.
- Make PPE easily accessible: Store PPE in convenient and visible locations throughout the workplace, making it easy for workers to access the equipment when needed. Clearly label storage areas and use signage to indicate the types of PPE available and where they can be found.
- Monitor and update PPE: Regularly inspect PPE for signs of wear, damage, or expiration, and replace equipment as needed. Stay informed about advances in PPE technology, and consider updating your inventory to include more effective or comfortable options as they become available.
- Train workers on PPE usage: Educate workers about the proper use, care, and storage of PPE to ensure they understand the importance of consistently using the equipment and can readily access and maintain it.
- Communicate the importance of PPE availability: Encourage workers to report any shortages, damaged equipment, or other issues related to PPE availability. Address these concerns promptly to ensure workers can access the necessary equipment.
Employers can promote consistent PPE usage and create a safer work environment by ensuring a consistent supply of high-quality PPE and making it easily accessible for all employees.
8. Insufficient Training
Insufficient training can significantly hinder workers from using PPE correctly and consistently. If workers do not know how to properly use, care for, or maintain PPE, they may be less likely to wear it or may inadvertently compromise their safety. To address this issue, employers should offer comprehensive training on the correct use, care, and maintenance of PPE and provide refresher courses as necessary. Here are some strategies to ensure effective PPE training:
- Develop a tailored training program: Create a PPE training program that is specific to your organization, taking into account the unique hazards, job roles, and PPE requirements in your workplace.
- Incorporate various training methods: Combine training methods, such as classroom instruction, hands-on demonstrations, videos, and written materials, to cater to different learning styles and reinforce key concepts.
- Provide step-by-step guidance: Clearly explain the proper use, adjustment, care, and maintenance of each type of PPE. This includes information on how to put on, remove, and store the equipment and any specific precautions or limitations associated with its use.
- Conduct hands-on exercises: Allow workers to practice using PPE under supervised conditions, providing feedback and guidance as needed. This can help build confidence and competence in using the equipment correctly.
- Emphasize the importance of PPE: Help workers understand the reasons for using PPE, the potential hazards they may encounter, and the consequences of not wearing the equipment. This can help reinforce the importance of consistent and proper PPE usage.
- Offer regular refresher courses: Provide ongoing training to reinforce key concepts, address any changes in PPE requirements or technologies, and ensure workers are competent in using the equipment.
- Assess training effectiveness: Regularly evaluate the effectiveness of your PPE training program through assessments, quizzes, or practical exercises. This can help identify areas where additional training or clarification may be needed.
- Encourage open communication: Create a culture where workers feel comfortable asking questions, seeking clarification, or reporting any concerns related to PPE usage. This can help ensure workers have the information and support they need to use PPE correctly.
By offering comprehensive training on the correct use, care, and maintenance of PPE and providing refresher courses, employers can equip workers with the knowledge and skills they need to use PPE consistently and effectively, leading to a safer work environment.
9. Low Perceived Value
Workers who do not view PPE as important in their daily tasks may be less likely to use it consistently. It is crucial to communicate the benefits of using PPE and the potential consequences of not wearing it, to help workers understand its value and prioritize its use. Here are some strategies to emphasize the importance and value of PPE:
- Share success stories: Highlight instances where PPE has prevented accidents, injuries, or illnesses. Demonstrating the tangible benefits of PPE can help workers appreciate its value in protecting their health and well-being.
- Discuss potential hazards: Provide information on the hazards in your workplace and their risks to workers’ health and safety. This can help workers understand the importance of PPE in mitigating these risks.
- Communicate potential consequences: Discuss the consequences of not wearing PPE, such as injuries, illnesses, lost work time, or even fatalities. Emphasizing the potential negative outcomes can help workers grasp the importance of PPE in their daily tasks.
- Offer regular safety training: Incorporate PPE education into ongoing safety training, consistently reinforcing its importance and value in preventing accidents and injuries.
- Provide visual reminders: Posters, signs, and other visual aids throughout the workplace should remind workers of the importance of using PPE and the hazards it helps protect against.
- Encourage worker involvement: Involve workers in the selection, evaluation, and maintenance of PPE, as well as the development and implementation of safety policies and procedures. This can help foster a sense of ownership and commitment to safety among workers.
- Establish a safety culture: Promote a safety-first mindset throughout the organization, emphasizing that the health and well-being of workers are a top priority. Encourage open communication, recognize and reward safe behavior, and involve all levels of the organization in promoting safety.
- Lead by example: Ensure that supervisors, managers, and team leaders consistently wear PPE and follow safety guidelines. This will demonstrate their commitment to safety and set a standard for workers to follow.
By communicating the benefits of using PPE and the potential consequences of not wearing it, employers can help workers understand the value of PPE in their daily tasks and encourage them to prioritize its use, leading to a safer and healthier work environment.
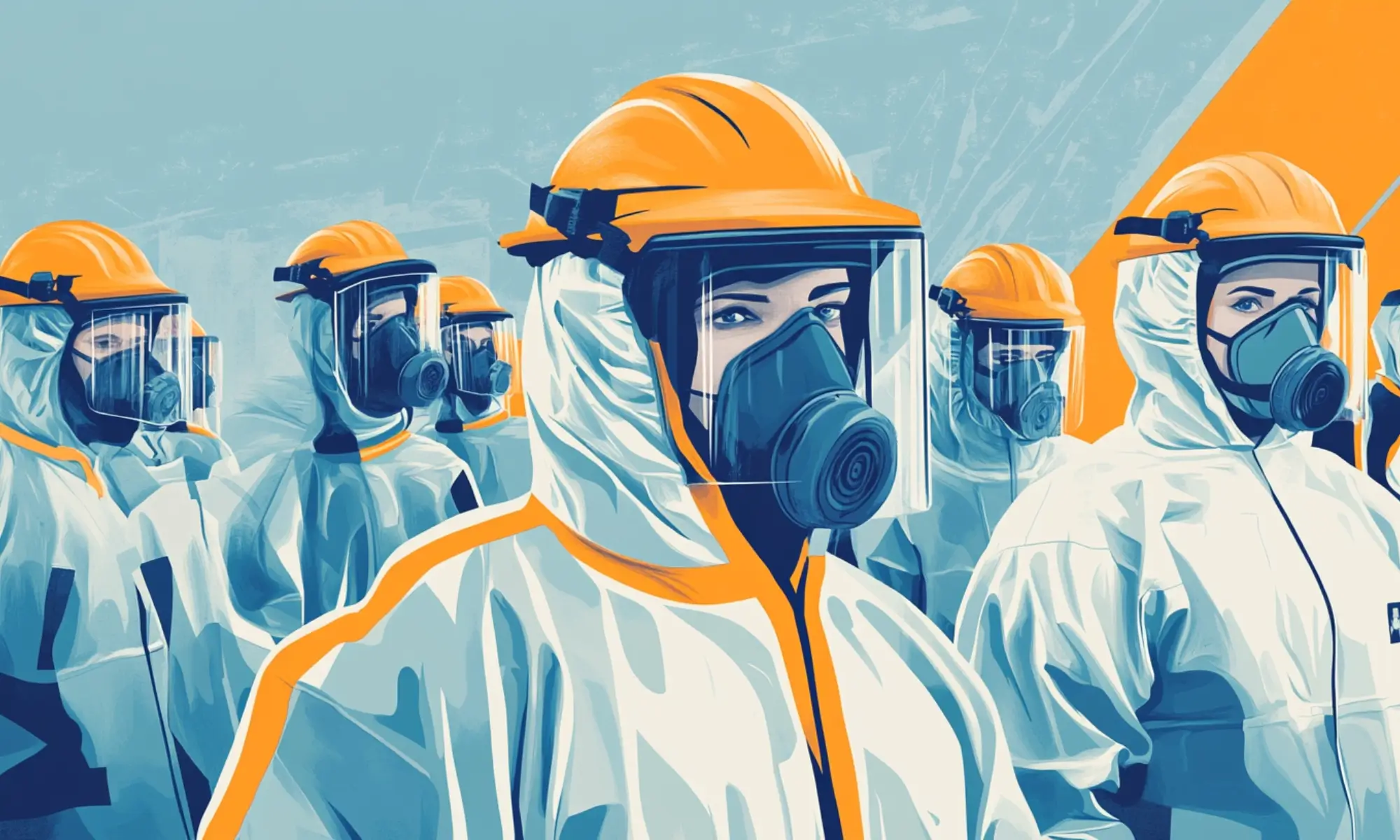
10. Refusal On Religious Or Other Grounds
Refusal to wear PPE on religious or other grounds can pose challenges for employers responsible for ensuring their workforce’s safety. The Personal Protective Equipment at Work Regulations 1992 contains no exemptions for wearing PPE based on religious, medical, or other grounds, except for turban-wearing Sikhs on construction sites.
In cases where workers refuse to wear required PPE, employers should take the following steps to address the issue:
- Communicate the importance of PPE: Clearly explain the reasons for PPE requirements and the potential consequences of not wearing it. Ensure workers understand the hazards and importance of PPE in protecting their health and safety.
- Engage in open dialogue: Discuss the workers’ concerns and try to understand the reasons for their refusal. Encourage open communication and be respectful of their beliefs while emphasizing the importance of safety in the workplace.
- Explore alternative PPE options: If possible, identify alternative PPE options that may be more compatible with the workers’ beliefs or needs without compromising their safety or the safety of others. Consult with PPE suppliers or safety experts to identify suitable alternatives.
- Re-deploy or reassign workers: If workers continue to refuse PPE and no suitable alternatives can be found, consider re-deploying or reassigning them to a less dangerous job or area where PPE requirements are unnecessary or less stringent.
- Implement disciplinary actions: If necessary, enforce disciplinary actions for workers who refuse to follow safety instructions in accordance with your organization’s policies and procedures. Contractual terms and conditions should treat failure to follow reasonable Health & Safety instructions as potential gross misconduct.
- Provide education and training: Offer ongoing safety training to reinforce the importance of PPE and address any misconceptions or concerns related to its use.
- Review and update policies: Regularly review and update your organization’s safety policies and procedures to ensure they remain relevant and effective in addressing PPE compliance issues, including those related to religious or other grounds.
Employers can address PPE refusal issues and maintain a safe and productive work environment by taking a balanced approach that respects workers’ beliefs while prioritizing safety.
Conclusion
Wearing Personal Protective Equipment (PPE) is essential for safeguarding workers against injuries, health hazards, and dangerous exposures in the workplace. Despite its importance, many workers still avoid using PPE due to discomfort, lack of training, overconfidence, peer pressure, and other factors. This increases the risk of accidents and long-term health issues and exposes employers to legal, financial, and reputational consequences.
To address this challenge, employers must prioritize providing high-quality, comfortable PPE, ensure proper training, and foster a strong safety culture where compliance is the norm. Consistent enforcement of PPE policies, open communication, and involving workers in selecting and improving PPE can significantly boost compliance. When workers understand the importance of PPE and feel supported in using it, they are more likely to wear it consistently — leading to a safer, healthier, and more productive work environment.