In the complex landscape of workplace safety, fire prevention and management stand out as paramount. Fire incidents can result in not just significant property damage, but also pose a grave threat to the lives of employees and visitors. Recognizing this, the Occupational Safety and Health Administration (OSHA) has set forth stringent requirements concerning fire extinguishers in the workplace. But what exactly are these standards? How do they influence workplace design, equipment maintenance, and employee training?
Welcome to our comprehensive guide on OSHA’s Fire Extinguisher Requirements. Whether you’re an employer striving for compliance, an employee aiming to understand your workplace’s safety protocols, or just someone curious about fire safety regulations, this guide is designed to illuminate every corner of the topic. From the scope and application to detailed testing and training protocols, we aim to unpack, explain, and simplify these crucial guidelines for you. So, let’s embark on this journey of understanding and ensure that safety, like a vigilant watchman, always stands guard in our workplaces.
OSHA Fire Extinguisher Requirements
The Occupational Safety and Health Administration (OSHA) is a federal agency responsible for ensuring that workplaces are safe and healthful for employees. One of its major areas of oversight is fire safety. Among the myriad of regulations that OSHA has in place, the requirements for portable fire extinguishers are specifically outlined in standard 1910.157. Let’s delve into the essential points of this standard.
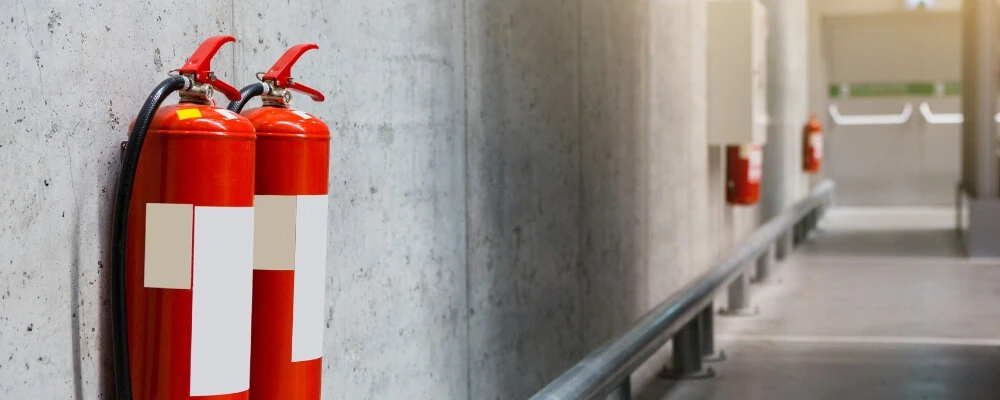
1. Scope and Application
The Occupational Safety and Health Administration’s (OSHA) standard on portable fire extinguishers predominantly centres around their proper placement, their designated use, the rigorous maintenance they undergo, and the testing methods they’re subjected to, with the main goal being the safety of employees. The overarching aim is to ensure that, should a fire emergency arise, employees have immediate and functional access to this crucial safety tool.
Placement within the Workplace: OSHA emphasizes the correct positioning of fire extinguishers. They must be placed in areas where they are easily accessible in times of emergency. The placement is not arbitrary; it follows a methodological approach based on potential fire risks in different workplace zones, ensuring that employees do not have to traverse large distances or navigate obstacles to reach them.
Extinguishers Outside Buildings or Structures: Certain conditions and exceptions for fire extinguishers are positioned outside the main workplace infrastructure, perhaps in auxiliary or open areas. These exceptions recognize the distinct fire risks and environmental conditions that might differ from those inside a building.
Extinguishers Not Primarily for Employee Use: In some cases, fire extinguishers might be present in a workplace but may not be designated for general employee use. This could be the case in areas with specialized equipment or materials, where only trained personnel are expected to handle fire emergencies. Even if these extinguishers are not intended for broad employee use, they must align with the company’s broader emergency response strategy. This means that their presence, maintenance, and accessibility should be consistent with the company’s emergency action plan (which details the steps employees should follow during emergencies) and the fire prevention plan (which outlines measures to prevent fires and maintain fire-safe conditions).
2. Exemptions
Certain employers may be exempted from the standard OSHA requirements about fire extinguishers based on their specific fire safety strategies and workplace conditions. Here’s a deeper dive into these exemptions:
Total Evacuation Policies
Some workplaces adopt a strict policy that mandates all employees’ complete and immediate evacuation when a fire alarm sounds. This strategy is rooted in the belief that swift evacuation minimizes the risk to human life over attempting to combat the fire. If an employer has such a written fire safety policy, they might be exempt from the standard requirements of providing portable fire extinguishers for employee use. However, two critical conditions must be met:
- Emergency Action Plan (EAP): The company must have a comprehensive and effective emergency action plan. This plan outlines employees’ procedures during a fire emergency, ensuring a swift and safe evacuation process.
- Fire Prevention Plan (FPP): Alongside the EAP, a Fire Prevention Plan should focus on preventing fire incidents. It should detail potential fire hazards, the maintenance of fire safety equipment, and the measures adopted to mitigate risks.
Designated Fire Extinguisher Users
In some settings, general employees might not be trained or authorized to use fire extinguishers, but specific personnel are. For example, only trained individuals can handle fire-related emergencies in high-risk areas like chemical laboratories or specialised manufacturing zones.
In such scenarios, the broad distribution requirements of fire extinguishers—intended to be accessible to all employees—might not apply. Instead, the focus would be ensuring these designated personnel have easy access to and proper training on fire extinguishers.
It’s important to note that these exemptions don’t compromise safety; they recognize and allow for alternative strategies that best suit a workplace’s specific conditions and risks.
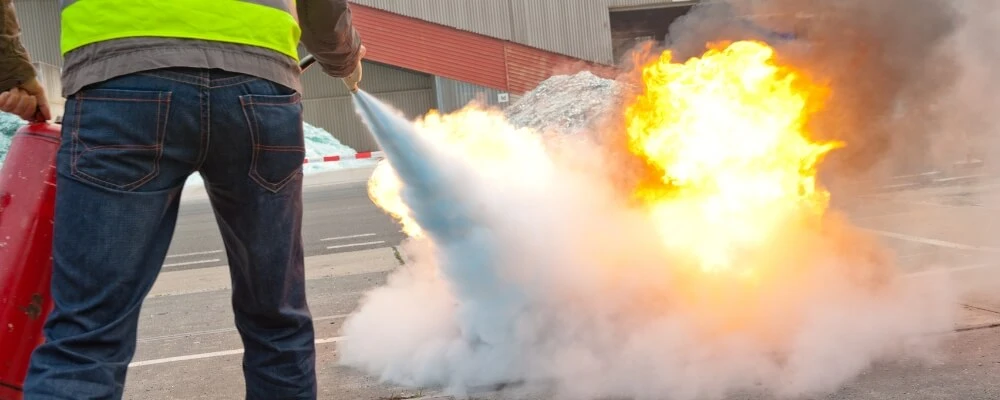
3. General Requirements
Ensuring the safety of employees during a fire emergency hinges on the right type, maintenance, and placement of fire extinguishers. Here’s a more detailed look at the general requirements set by OSHA for fire extinguishers in the workplace:
Accessibility and Safety
- Ease of Access: Fire emergencies require an immediate response. Thus, fire extinguishers must be located where employees can quickly reach them. This means they should be in open spaces, free from obstructions, and not hidden behind doors or in concealed areas.
- Safety of Placement: While accessibility is paramount, it’s also essential that the location of the extinguisher does not pose additional risks. For example, placing an extinguisher next to highly flammable materials might increase the risk of an employee trying to reach it during a fire.
Approval of Extinguishers:
- Not all extinguishers are created equal. Only those extinguishers that meet specific standards and have been tested and certified by recognized testing laboratories should be used in workplaces. This ensures their reliability and effectiveness in various fire scenarios.
Prohibited Extinguishing Agents:
- Certain chemical agents used in older fire extinguishers can be harmful or ineffective. Specifically, extinguishers that use carbon tetrachloride or chlorobromomethane are no longer permitted. These agents pose health risks upon exposure and can produce harmful by-products when used.
Maintenance and Designation:
- Regular Maintenance: A fire extinguisher is only as useful as its operational condition. Employers must ensure that extinguishers are routinely inspected, maintained, and serviced to ensure they are always in working order. This includes checking for physical damages, ensuring seals are intact, and verifying that the extinguishing agent is at the recommended level.
- Designated Locations: Extinguishers should have designated spots marked clearly in the workplace. This helps in two ways: it ensures that an extinguisher is always available where expected and aids in quick identification and access during emergencies.
Outdated Extinguisher Models:
- Fire safety technology and knowledge evolve over time. As a result, certain older models or fire extinguishers that were once considered standard may now be deemed ineffective or even hazardous. Employers should stay informed about such updates and replace prohibited or outdated extinguishers with approved models.
Adhering to these general requirements ensures that employees have the best possible tools in the event of a fire and can use them safely and effectively.
4. Selection and Distribution of Fire Extinguishers
Choosing the right fire extinguisher and its strategic placement within a workplace can be the difference between a minor incident and a major disaster. Each type of fire (classified by class) requires a specific kind of extinguisher. Here’s a detailed explanation of the selection and distribution guidelines set by OSHA:
Basis for Extinguisher Selection
- The types of fire extinguishers needed depend on the potential fire hazards present in a particular workplace. These hazards are categorized into various classes, and each class requires a specific type of extinguisher to combat them effectively.
Class A Fires
- These fires involve ordinary combustibles like wood, paper, and cloth.
- Distance Requirement: An extinguisher suitable for Class A fires should be placed so that the maximum travel distance to reach it does not exceed 75 feet. This ensures that employees can promptly address the fire before it spreads uncontrollably.
- Alternative Systems: Instead of Class A extinguishers, an establishment can opt for standpipe systems, provided these systems adhere to specific standards and requirements. Standpipe systems are a series of pipes designed to provide a readily available water supply for firefighting.
Class B Fires
- These involve flammable liquids, gases, or greases.
- Distance Requirement: Given Class B fires’ rapid spread and potential explosiveness, the maximum travel distance to a fire extinguisher should be no more than 50 feet.
Class C Fires
- These fires involve electrical equipment, where the electrical non-conductivity of the extinguishing agent is vital.
- Selection Criteria: The extinguishers for Class C hazards are not standalone. They are chosen based on their suitability for either Class A or Class B fires but with the added criterion that the extinguishing agent must be non-conductive.
Class D Fires
- Specific to combustible metals like magnesium or potassium.
- Placement: Workplaces where combustible metals are processed or used should have Class D fire extinguishers placed such that they are within 75 feet of those areas. This proximity ensures a swift response to fire from these highly reactive metals.
The strategic selection and distribution of fire extinguishers are paramount for ensuring workplace safety. Adhering to these guidelines ensures that the right tools are within reach in the event of a fire, maximizing the chances of swiftly and safely controlling the situation.
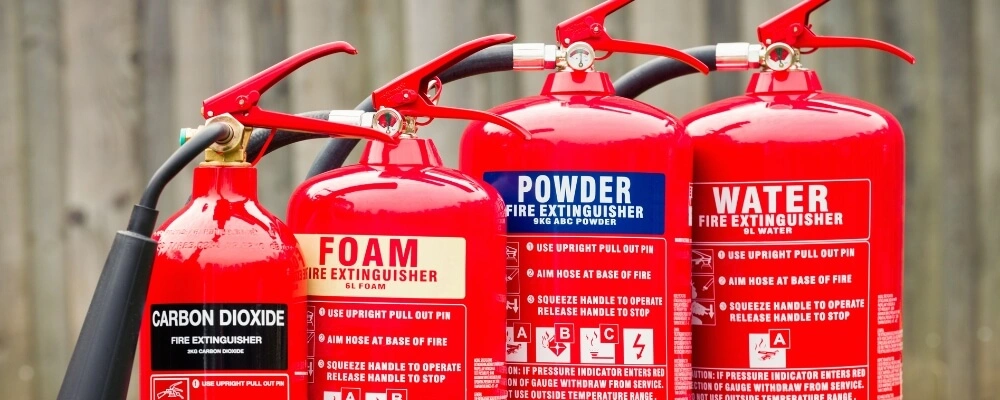
5. Inspection, Maintenance, and Testing of Fire Extinguishers
Ensuring the proper function of fire extinguishers is not just about having them in place but also about ensuring they are in operational condition when needed. Here’s an in-depth look at the obligations employers have in terms of inspection, maintenance, and testing:
Employer Responsibility
Employers are primarily responsible for upkeep all fire extinguishers within their premises. This includes regular inspection, routine maintenance, and periodic testing to guarantee their efficacy in emergencies.
Visual Inspections
Monthly visual examinations are vital. These inspections identify any apparent physical damage, corrosion, leakage, or clogging. Moreover, they confirm that the pressure gauge readings are within the acceptable range and that the seals and tamper indicators are intact. Such frequent checks ensure that extinguishers are always in a ready-to-use state.
Annual Maintenance Checks
Beyond the monthly visual inspections, a comprehensive maintenance check is mandated annually. This in-depth examination is conducted to identify and rectify any issues that might impede the extinguisher’s operation. It often involves checking internal parts for signs of damage or corrosion, examining the pull-pin for ease of removal, ensuring the hose isn’t cracked or blocked, and checking the weight to ensure it’s filled correctly.
Stored Pressure Extinguishers
These extinguishers, which retain their expellant gas and extinguishing agent in the same chamber, require special attention. Their maintenance routines often involve checking for proper pressurization and ensuring that the extinguishing agent hasn’t settled or packed, which might inhibit its discharge.
Hydrostatic Testing
Hydrostatic testing involves pressurizing the extinguisher with water to check its integrity under pressure. This test is crucial because it helps identify extinguishers weakened over time and might rupture when deployed. The frequency of these tests varies based on the extinguisher’s type and material but is generally required at intervals ranging from 5 to 12 years.
In essence, the inspection, maintenance, and testing protocols serve a dual purpose: ensuring extinguishers’ readiness and their users’ safety. By adhering to these rigorous standards, employers comply with regulations and instil confidence in their workforce about their safety infrastructure.
6. Hydrostatic Testing of Fire Extinguishers
Hydrostatic testing is a crucial component of fire extinguisher maintenance, ensuring the integrity and safety of the vessel that holds the extinguishing agent. Let’s delve into the specifics:
Trained Personnel & Equipment
Hydrostatic testing must be performed by personnel who have undergone rigorous training and are well-versed in the intricacies of the process. The equipment used for this testing is designed to safely and accurately measure the strength and flexibility of the extinguisher’s cylinder. Using the right equipment ensures that tests are conducted under controlled and safe conditions.
Testing Intervals
The frequency of hydrostatic tests is determined by the material of the extinguisher and its contents. For instance, dry chemical extinguishers often need testing every 12 years, while some water-based extinguishers may require more frequent testing. These intervals are set based on exhaustive studies about the longevity and potential wear of materials used in extinguisher construction.
Conditions for Testing
It’s not just the time determining when an extinguisher should undergo hydrostatic testing. Certain visible conditions can expedite the need for a test. This includes evidence of external corrosion, mechanical damage such as dents or deformities, or any other signs that the structural integrity of the extinguisher might be compromised.
Testing Provisions & Procedures
The specifics of the hydrostatic testing process are meticulous. The equipment must be calibrated to apply a specific test pressure, often higher than the extinguisher’s normal operational pressure. This ensures the cylinder can withstand unexpected spikes in internal pressure.
During testing, the extinguisher is filled with water, pressurized to the specified test pressure, and observed for any deformities or leaks. This process evaluates the cylinder’s ability to safely hold its contents under operational conditions.
Handling Failed Extinguishers
If an extinguisher doesn’t pass the hydrostatic test, it signifies a compromise in its structural integrity. Such extinguishers are deemed unsafe for use. Detailed provisions exist for handling these extinguishers, which typically involve removing them from service, rendering them unusable to prevent accidental deployment, and disposing of them in an environmentally safe manner.
To sum up, hydrostatic testing is essential in ensuring fire extinguishers are operational and safe. Adherence to strict guidelines and intervals ensures the reliability of these crucial fire-fighting devices.
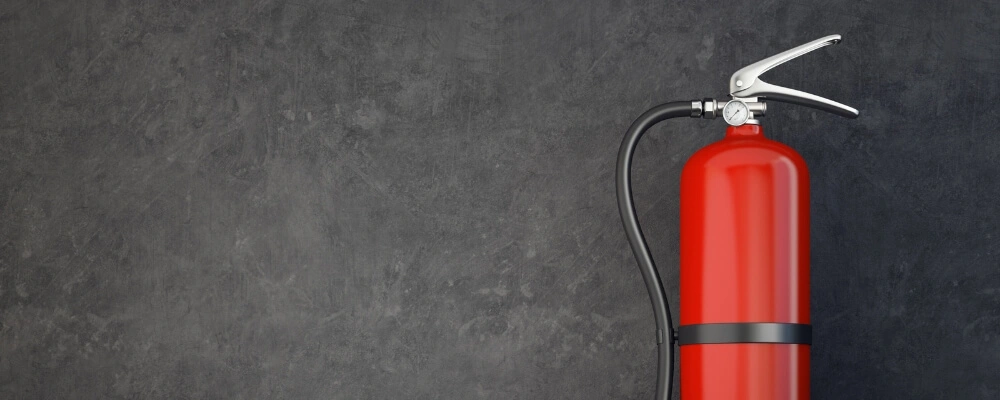
7. Comprehensive Training and Education on Fire Extinguishers
Ensuring the presence of fire extinguishers within a workplace is only part of the safety equation. Ensuring employees have the knowledge and confidence to use them effectively is equally vital. Let’s delve deeper into the requirements and nuances of training and education related to fire extinguishers:
Mandatory Familiarization for All Employees
When fire extinguishers are made available within the workplace, employers must conduct an educational program for their workforce. The primary goal isn’t necessarily to make every employee an expert in firefighting but to ensure everyone is familiar with the basic principles of using an extinguisher. This includes recognizing the device, understanding its purpose, and having a general idea of its operation.
Initial and Ongoing Training Sessions
The educational process begins the moment a new employee joins the organization. Initial training ensures that every staff member understands the role and function of fire extinguishers in the workplace from day one. However, given the gravity of fire safety and the potential for individuals to forget procedures over time, employers must refresh this education at least once a year. These annual refresher courses help reinforce key concepts, introduce new protocols or equipment, and ensure continued readiness in an emergency.
Specialized Training for Designated Firefighting Personnel
While general familiarization is crucial for all employees, there will be instances or workplaces where specific individuals are designated as the primary responders in case of a fire. These individuals may be tasked with more than just using a basic fire extinguisher; they might be responsible for coordinating evacuations, using advanced firefighting equipment, or liaising with professional firefighting teams. Consequently, their training regimen is more intensive. It goes beyond basic use and delves into advanced firefighting techniques, safety protocols, and emergency communication skills.
Providing fire extinguishers in a workspace without accompanying education is like having a library without teaching people to read. A robust training and education program ensures that if a fire does break out, panic doesn’t ensue, and employees have the requisite knowledge to respond appropriately, maximizing safety for everyone involved.
Conclusion
Ensuring workplace safety is more than just a regulatory obligation; it’s a testament to the value placed on human life and well-being. The guidelines set forth by OSHA for fire extinguisher requirements play a pivotal role in safeguarding assets and lives. As we’ve navigated through this comprehensive guide, it’s evident that OSHA’s standards are meticulously crafted to address potential fire hazards across various workplace environments.
By adhering to these requirements, employers ensure compliance and foster a culture of safety, diligence, and preparedness. Whether properly placing extinguishers, regular maintenance checks, or ensuring employees are adequately trained, each step contributes to building a safer and more resilient workspace. In closing, it’s our collective responsibility to understand, implement, and maintain these standards. The invaluable promise of safety and security for all lies in the meticulous details of these regulations.