A Personal Protective Equipment (PPE) hazard assessment is a crucial safety practice used to identify workplace hazards and ensure that employees are equipped with the appropriate PPE to minimize exposure to those risks. It is not just a regulatory requirement under OSHA standards (29 CFR 1910.132) but also an essential step toward creating a safe working environment.
In this article, you will learn what a PPE hazard assessment is, why it’s essential, and how to conduct one effectively. This guide provides clear, actionable steps for employers, safety managers, and employees to perform assessments that meet industry standards and regulatory compliance.
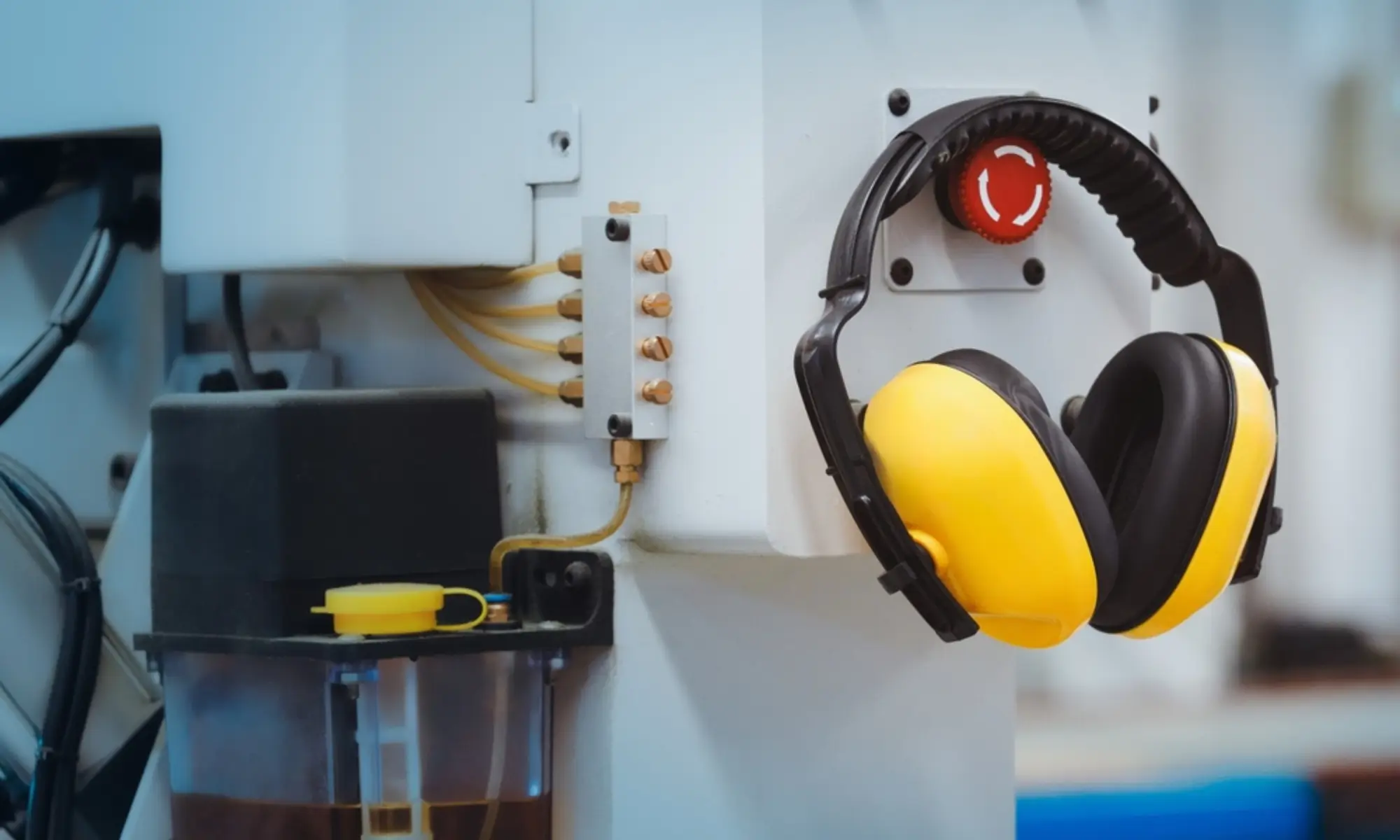
What is PPE Hazard Assessment?
PPE hazard assessment is a systematic process of identifying potential risks in the workplace that could harm employees and determining the appropriate PPE to protect against those risks. PPE is considered the last line of defense after efforts to eliminate hazards through engineering, administrative, or procedural controls.
The purpose of this assessment is twofold:
- Prevent injuries and illnesses caused by chemical, physical, biological, or ergonomic hazards.
- Ensure compliance with regulatory standards such as OSHA 29 CFR 1910.132, which mandates hazard assessments and PPE certification.
Why is PPE Hazard Assessment Essential?
Conducting a PPE hazard assessment ensures:
- Employee safety: Proper PPE minimizes injuries from falls, chemical spills, electrical hazards, and other occupational risks.
- Regulatory compliance: OSHA requires written documentation of hazard assessments, ensuring businesses meet safety standards.
- Proactive risk management: Identifying hazards early reduces the likelihood of accidents, near-miss events, and costly disruptions.
- Employee engagement and trust: Involving employees in the assessment process fosters a culture of safety and responsibility.
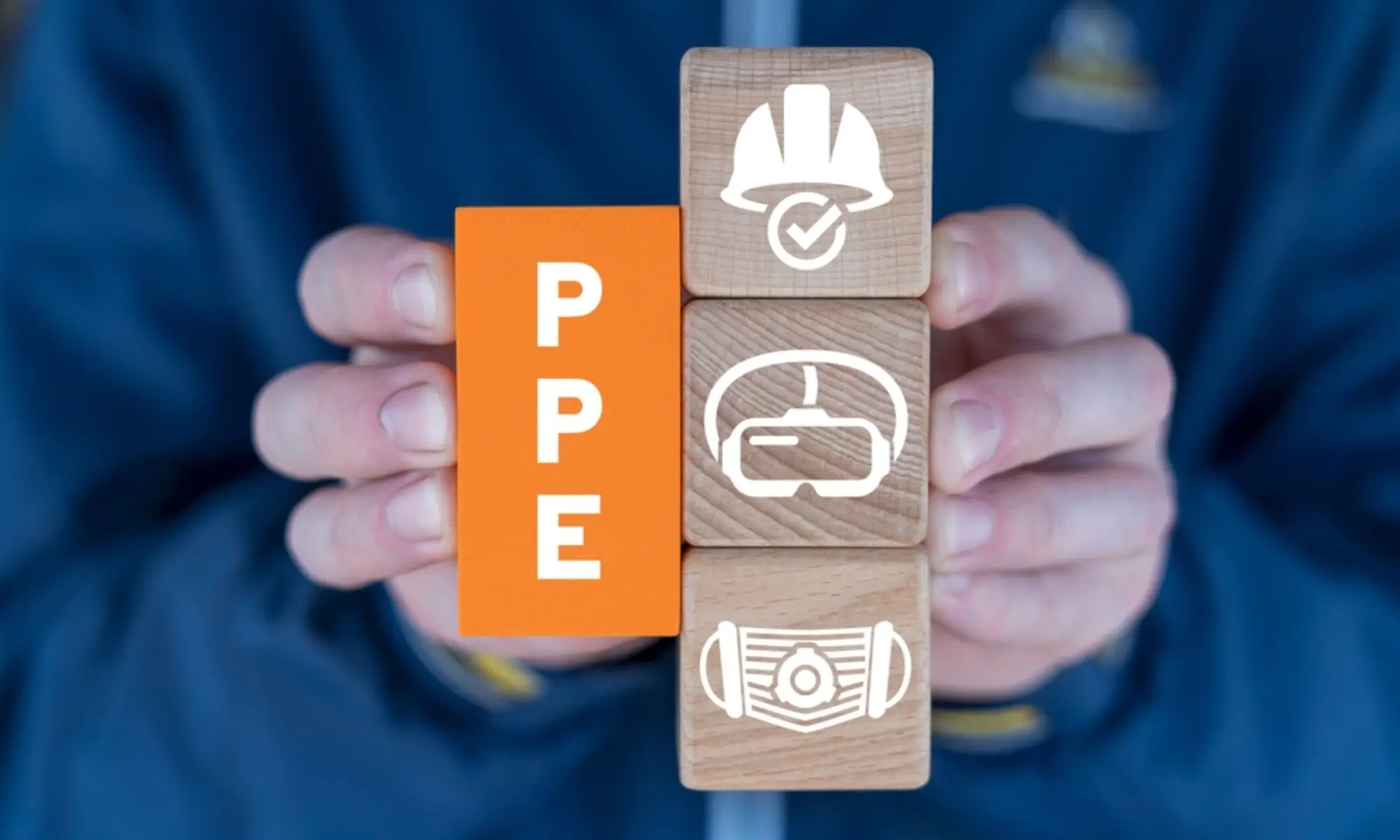
How to Conduct a PPE Hazard Assessment: A Step-by-Step Guide
Conducting a PPE hazard assessment is essential to ensure employees are protected from workplace risks. This process identifies potential hazards and determines the appropriate protective equipment needed for each task. Below is a simple, step-by-step guide to help you perform a thorough and compliant PPE hazard assessment.
1. Communicate with Employees and Establish the Scope
Before starting a PPE hazard assessment, it is essential to inform employees about the process and explain its purpose. This ensures transparency and fosters collaboration between management and workers, helping everyone understand why the assessment is being conducted and how it benefits their safety.
Involving supervisors and workers from the relevant departments is critical because they are familiar with the tasks, equipment, and potential hazards unique to their work areas. This firsthand knowledge helps identify risks more effectively and ensures that the selected PPE will meet real-world needs.
Establishing the Scope means defining the boundaries of the assessment. The scope can vary depending on the needs of the organization:
- Entire Site: If the focus is on general safety, the assessment may cover every part of the facility.
- Specific Tasks: If certain tasks involve high-risk activities, such as welding or chemical handling, the assessment will target those tasks.
- Individual Employees: In cases where roles are highly specialized, the evaluation may focus on the hazards encountered by specific employees.
Clarifying the scope ensures that the assessment is focused, efficient, and relevant, ensuring that all potential hazards are identified and addressed with appropriate PPE.
2. Review Workplace Data and Historical Records
To conduct an effective PPE hazard assessment, it’s crucial to analyze historical data from the workplace. This includes reviewing incident reports, injury logs, and near-miss events. These records offer valuable insights into recurring hazards or areas where safety procedures may have failed, indicating the need for improved protective measures.
By identifying patterns or trends—such as frequent cuts, chemical splashes, or slip-and-fall incidents—you can proactively determine where PPE is needed or whether existing PPE is insufficient. For example:
- A series of eye injuries might suggest that safety goggles need to be replaced with sealed chemical-resistant goggles.
- Repeated hand injuries could highlight the need for cut-resistant gloves during specific tasks.
This step ensures the assessment is data-driven, helping organizations focus their efforts on real-world risks and preventing similar incidents in the future through proper PPE selection.
3. Conduct a Walkthrough Survey
A walkthrough survey involves a physical inspection of the workplace to identify potential hazards that employees may encounter during their tasks. This step allows safety managers to observe work conditions firsthand, ensuring that no risks are overlooked. Here’s how to approach the survey effectively:
Physical Layout
Examine the structure of the workspace to identify hazardous areas, such as:
- Confined spaces (e.g., tanks or silos)
- Elevated platforms or unprotected edges
- Crowded or narrow pathways that could restrict movement or increase fall risks
Processes and Tasks
Observe workflows, tools, and equipment used by employees. Pay attention to:
- High-risk activities such as welding, chemical mixing, or heavy equipment operation
- Machine interaction points where workers might be exposed to pinch points or moving parts
- Material handling practices that involve repetitive motion or force
Hazard Exposure Point
Look for common workplace risks, such as:
- Dust, chemicals, or fumes that could require respiratory protection
- Sharp tools or objects that could cause cuts or punctures
- Machinery or vehicles in motion that present impact or crush hazards
By conducting a thorough walkthrough, you ensure that all potential hazards are identified and documented, forming a solid foundation for selecting appropriate PPE and improving overall workplace safety.
Common Hazard Categories to Consider:
- Impact hazards: Falling or flying objects
- Chemical exposure: Spills, splashes, fumes
- Temperature extremes: Hot surfaces or cryogenic liquids
- Noise hazards: Loud equipment or pneumatic tools
- Electrical hazards: Exposed wiring or arc flashes
- Fall hazards: Elevated work surfaces
4. Identify Hazards and Required PPE
For each task or work area, document the hazards and match them with the appropriate PPE. Use the following chart to guide your decisions:
Body Part | Potential Hazard | Required PPE |
---|---|---|
Eyes | Flying debris, chemicals, intense light | Safety goggles, face shields |
Head/Neck | Falling objects, electrical hazards | Hard hats, bump caps, insulated helmets |
Hands/Arms | Cuts, burns, chemical exposure | Cut-resistant gloves, nitrile gloves |
Feet | Falling tools, slippery surfaces | Steel-toed boots, anti-slip soles |
Body/Torso | Chemical splashes, extreme heat | Aprons, coveralls, flame-resistant clothing |
Respiratory System | Toxic fumes, airborne particulates | N95 masks, respirators, PAPR systems |
Hearing | High-decibel machinery | Ear plugs, earmuffs |
Falls | Elevated work surfaces | Safety harnesses, lanyards |
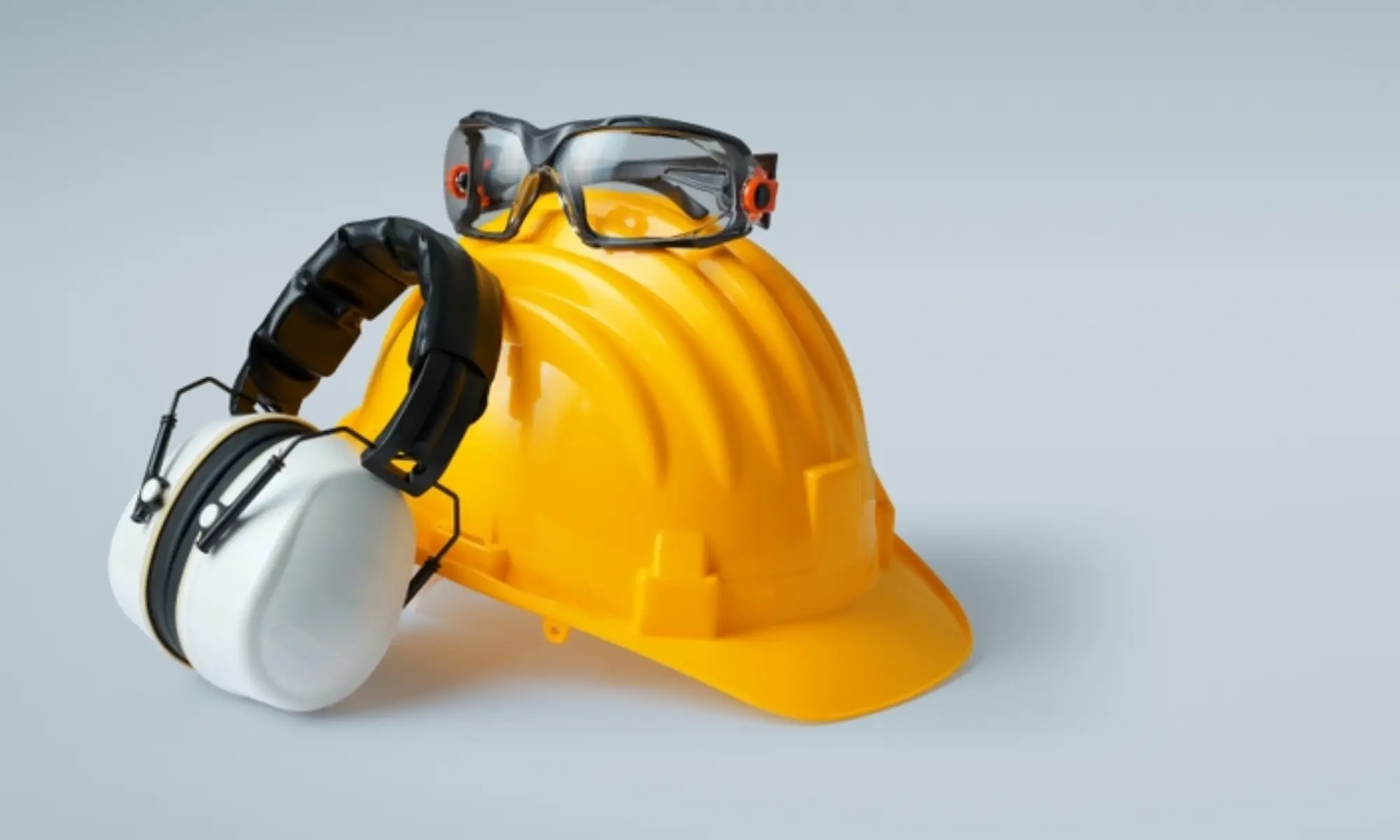
5. Select and Certify the Appropriate PPE
After identifying hazards through the assessment, the next step is to select PPE that offers the highest level of protection while ensuring it is comfortable and fits properly. Selecting the right PPE involves balancing safety with practicality, so employees are more likely to wear the equipment consistently and correctly.
Factors to Consider When Selecting PPE:
- Protection Level: Choose PPE that adequately protects against the specific hazards identified (e.g., chemical-resistant gloves for corrosive materials).
- Comfort and Fit: Ensure that the PPE fits properly and is comfortable for extended use, with appropriate sizing for different employees.
- Dexterity and Mobility: For tasks requiring precision, like assembly work, use PPE that allows for adequate movement and control (e.g., lightweight gloves).
- Durability: Select PPE that can withstand repeated use and exposure to the identified hazards (e.g., heat-resistant gear for welding).
- Compatibility: Ensure PPE works seamlessly with other equipment (e.g., safety goggles must fit comfortably under a welding helmet).
Certification of PPE Hazard Assessment
After selecting the PPE, document your choices in a hazard assessment certificate. This document serves as a formal record to show that the PPE matches the identified hazards and complies with OSHA regulations.
Sample PPE Selection Entry:
Task | Hazard | Required PPE |
---|---|---|
Welding | UV radiation, sparks | Welding helmet with shaded lens, flame-resistant gloves, leather apron |
This documentation ensures that the correct PPE is available and used, offering both accountability and traceability. The certification must be signed and dated, and stored in an accessible location for reference by employees, inspectors, or auditors.
6. Provide Employee Training
Once the appropriate PPE is selected and assigned, proper training is essential to ensure employees know how to use and maintain the equipment effectively. PPE can only protect workers if it is worn correctly, maintained properly, and understood thoroughly. Comprehensive training helps prevent misuse and ensures PPE performs as intended.
What Employee Training Should Cover:
Proper training ensures employees know how to use, maintain, and inspect their PPE effectively. This section outlines the key aspects of PPE training that employees must understand to stay safe and comply with safety regulations.
When and How to Wear PPE
- Clearly define situations and tasks where PPE is mandatory.
- Demonstrate the correct way to put on and adjust PPE to ensure a secure fit.
- Explain the importance of wearing PPE consistently and not removing it prematurely, even for short tasks.
How to Inspect PPE for Wear and Damage
- Show employees how to check for signs of wear, tear, or damage, such as cracks, fraying, or missing parts.
- Provide guidance on what to do if PPE is found to be damaged (e.g., replacing gloves with punctures or helmets with cracks).
How to Store and Clean PPE Properly
- Explain the proper storage methods to protect PPE from contamination or damage (e.g., hanging respirators in a dry place or storing gloves in sealed bags).
- Demonstrate cleaning techniques appropriate for specific types of PPE, such as using disinfectants for face shields or wiping goggles with anti-fog wipes.
- Highlight which PPE is disposable and when it should be discarded after use.
Understanding the Limitations of PPE
- Ensure employees know that PPE is the last line of defense and should be used in conjunction with other safety measures.
- Discuss situations where PPE may not fully protect against a hazard, and emphasize the need to stay vigilant despite wearing protective gear.
- Teach employees how to recognize when PPE is insufficient and when to report safety concerns.
Why PPE Training Matters
- Increases compliance: Well-trained employees are more likely to use PPE consistently and correctly.
- Reduces injuries: Proper training ensures PPE is used as intended, minimizing the risk of workplace accidents.
- Ensures regulatory compliance: OSHA requires employers to provide PPE training under 29 CFR 1910.132, and proper documentation of training ensures compliance during audits.
After training, it’s essential to document employee participation to ensure accountability and track who has been trained. Refresher courses should be conducted regularly or whenever new PPE is introduced or updated.
7. Make the Hazard Assessment Accessible
Once the PPE hazard assessment is completed and certified, it must be stored in a location that is easily accessible to both employees and inspectors. Accessibility ensures that workers can refer to the document when needed, and safety inspectors or auditors can verify compliance with regulations.
Best Practices for Storing the Assessment:
Proper storage of the PPE hazard assessment ensures that it is easily accessible for employees and inspectors, promotes accountability, and supports compliance with safety regulations. Below are best practices for organizing and maintaining these records effectively.
Electronic Storage
- Upload the hazard assessment certificate to a centralized digital platform, such as a shared drive or safety management system.
- Ensure that all employees have access to the document, with permissions set to maintain version control and prevent accidental modifications.
- Use backup systems to avoid data loss.
Physical Copies in Safety Binders
- Place hard copies in safety binders or folders kept in designated locations, such as break rooms, safety stations, or the HR office.
- Label the binders clearly with sections organized by task, department, or work area for quick reference.
- Keep the documents up-to-date and replace outdated versions immediately.
Why Accessibility is Important:
- Promotes Awareness: Easy access allows employees to review PPE requirements regularly and stay informed about workplace safety protocols.
- Facilitates Compliance: Safety inspectors can quickly verify documentation during audits, reducing the risk of non-compliance penalties.
- Supports Training and Refreshers: Supervisors can use the assessment as a training tool to reinforce safety protocols during team meetings.
Ensuring that the hazard assessment is easily available reinforces a culture of safety, making PPE protocols part of daily operations and empowering employees to take ownership of their well-being.
8. Regularly Update and Reassess the Workplace
A PPE hazard assessment is not a one-time task; it needs regular updates to ensure it reflects current workplace conditions. Changes in equipment, processes, or materials can introduce new hazards that require additional protective measures.
When to Update the PPE Hazard Assessment:
- New Equipment or Processes: If new tools or machinery are introduced, they may present risks that weren’t previously identified (e.g., increased noise levels or exposure to chemicals).
- Changes in Tasks or Materials: Modifying work procedures or switching to different materials can introduce new safety challenges, requiring different PPE.
- Accidents or Near-Miss Events: Any incident, whether it results in injury or not, signals a need to reassess the effectiveness of current PPE and safety protocols.
- Annual Reviews: Regular reviews help ensure the assessment stays relevant, aligns with OSHA requirements, and incorporates the latest safety practices.
By reassessing the workplace frequently and proactively, businesses can address hazards before they lead to accidents, maintain compliance, and ensure that employees remain safe at all times.
Conclusion
A well-conducted PPE hazard assessment ensures businesses meet OSHA requirements while providing a safe working environment. PPE serves as the last line of defense, meaning every effort should be made to eliminate or control hazards through other means. By involving employees in the assessment, selecting appropriate PPE, and providing proper training, organizations can foster a culture of safety that protects employees and enhances productivity.