In an era where electricity powers almost every aspect of our lives, safety in electrical work becomes vitally important. This is where personal protective equipment, or PPE, is an essential line of defence against potential hazards. From electricians to maintenance personnel, understanding and using the right PPE can make a life-or-death difference when interacting with electrical systems.
This blog post offers a comprehensive guide to various types of PPE that provide protection in electrical work environments. From the obvious, like insulated gloves, to the easily overlooked, such as hearing protection, we delve into each item’s function, importance, and proper usage.
Our aim is not just to educate but to underline the significance of these protective tools and inspire a safety culture in electrical work. So, whether you’re a seasoned electrical worker or someone newly venturing into this field, read on to enlighten yourself about the critical role of PPE in ensuring electrical safety.
Electricity PPE | 11 Different PPE For Electrical Safety
Personal Protective Equipment is vital for ensuring the safety of workers involved in potentially dangerous tasks, such as those dealing with electricity. Here are 11 different types of PPE for electrical safety:
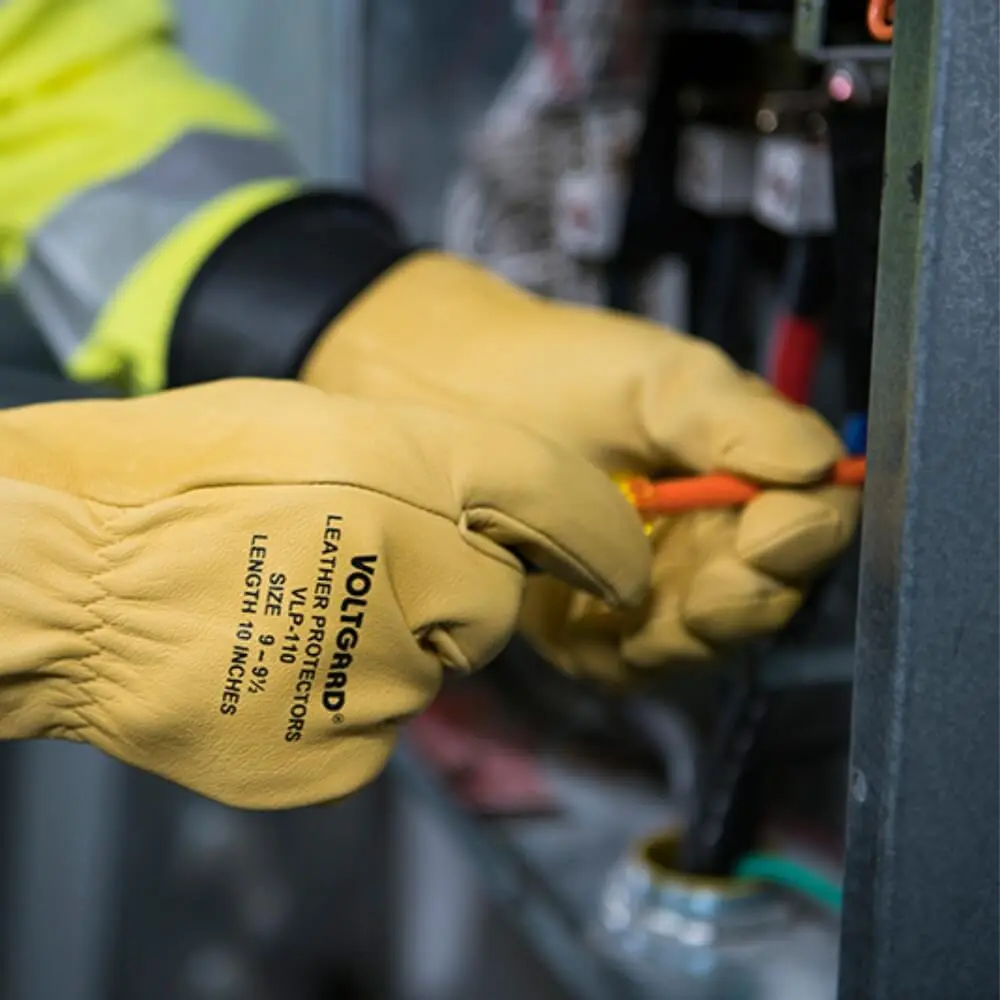
1. Insulated Gloves
Insulated gloves, commonly used in electrical work, protect the hands from electrical shocks, burns, and other potential hazards. They are typically crafted from non-conductive materials such as rubber or a similar substance, which inhibit the flow of electricity, thus providing a safe barrier between the electrical source and the person’s hands. The level of protection they offer can vary significantly, categorized by different voltage ratings that range from 500 volts for low-voltage applications up to 36,000 volts for high-voltage applications.
Therefore, it’s crucial to select the correct glove class for the specific task at hand. They are often colour-coded according to their class and voltage rating for easy identification. Furthermore, these gloves must be regularly tested and certified for insulating integrity to ensure ongoing safety. It’s important to mention that for optimal protection, these insulated gloves are often used in conjunction with leather over-gloves to provide mechanical protection against cuts, abrasions, and punctures.
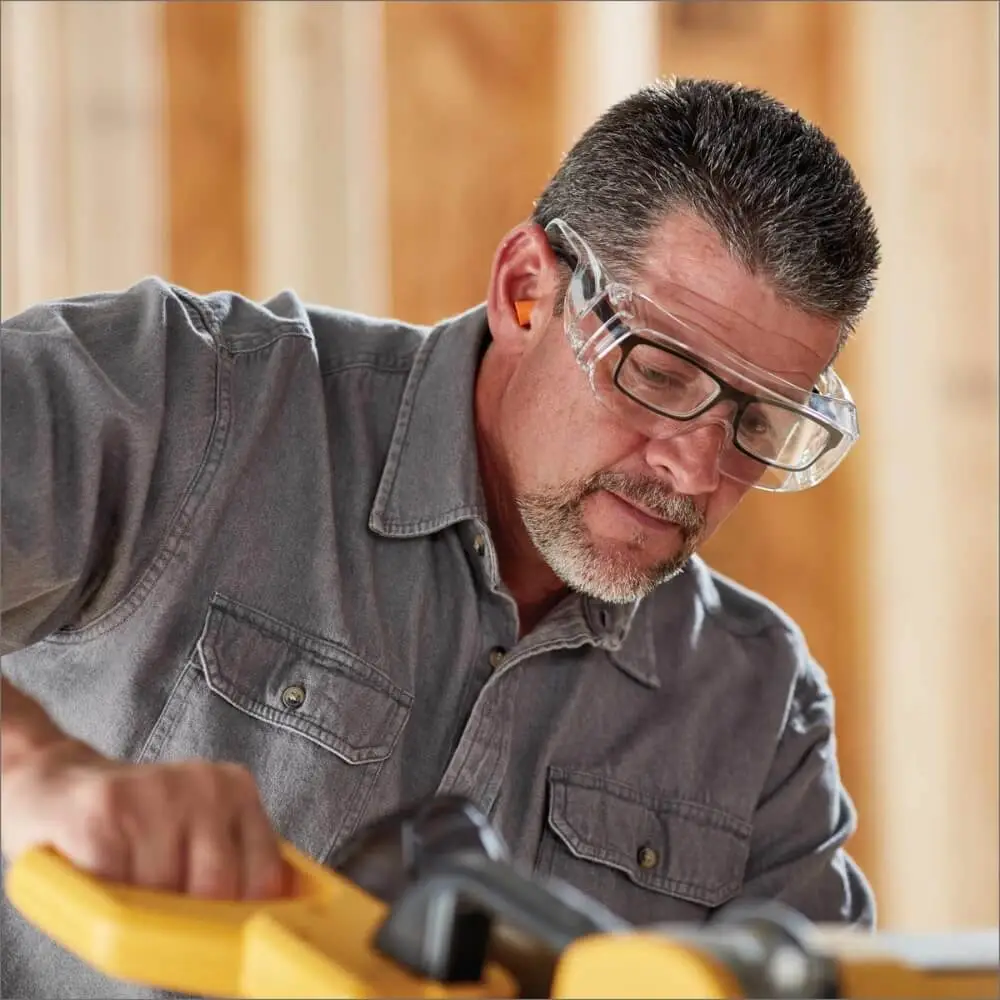
2. Safety Glasses or Goggles
Safety glasses and goggles serve a critical function in electrical safety by providing a shield for the eyes against multiple hazards that can arise in electrical work. These hazards can include flying debris and sparks, which can occur when cutting or stripping electrical wires, as well as intense light and heat from arc flashes. Properly understanding electrical signs can help workers anticipate and avoid these dangers before they happen.
Safety glasses typically have side shields made from high-impact materials that resist damage from sharp or fast-moving objects. Goggles offer a higher level of protection with a secure fit around the eyes, providing protection from all angles. Some safety glasses and goggles models are also designed with anti-fog and scratch-resistant coatings for clear vision in various working conditions.
Furthermore, for jobs with a high risk of arc flash, special arc flash-rated goggles or face shields may be necessary as they are specifically designed to withstand the extreme temperatures and radiant energy produced in such events. Remember, standard prescription glasses do not offer the same level of protection as safety glasses or goggles, so it’s important to use eyewear designed for electrical safety when performing electrical work.
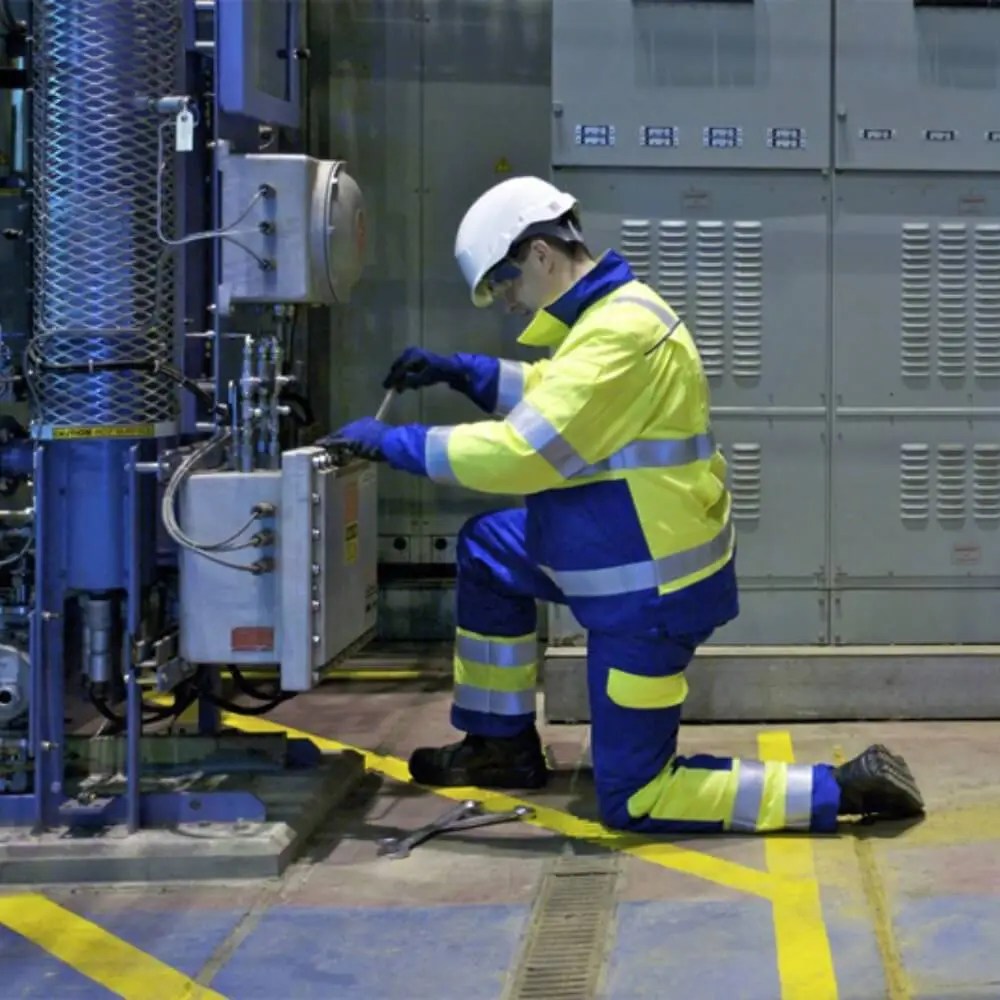
3. Flame-Resistant Clothing
Flame-resistant or arc flash clothing is a key component of electrical safety PPE, providing essential protection against intense heat and potential burns associated with electrical work. The fabric of this clothing is treated or inherently engineered to be resistant to ignition and prevent flames from spreading across the garment’s surface. Unlike regular clothing, which can catch fire and continue to burn, flame-resistant clothing is designed to self-extinguish almost immediately once the ignition source is removed. This rapid extinguishing property minimizes the wearer’s exposure to the flames and reduces the severity of burn injuries.
Flame-resistant clothing comes in several forms, including shirts, pants, coveralls, jackets, and even full-body suits. The level of protection required depends on the potential heat energy (measured in cal/cm2) that a worker could be exposed to in an electrical arc flash event. This potential energy level, the Arc Thermal Performance Value (ATPV), is often listed on garment labels, and appropriate clothing should be selected based on this rating.
Additional features of flame-resistant clothing include high-visibility stripes for improved visibility and safety in low-light conditions. Proper care and maintenance are essential to preserve the protective properties of flame-resistant clothing, and it’s important to follow the manufacturer’s care instructions to ensure the garments maintain their effectiveness.
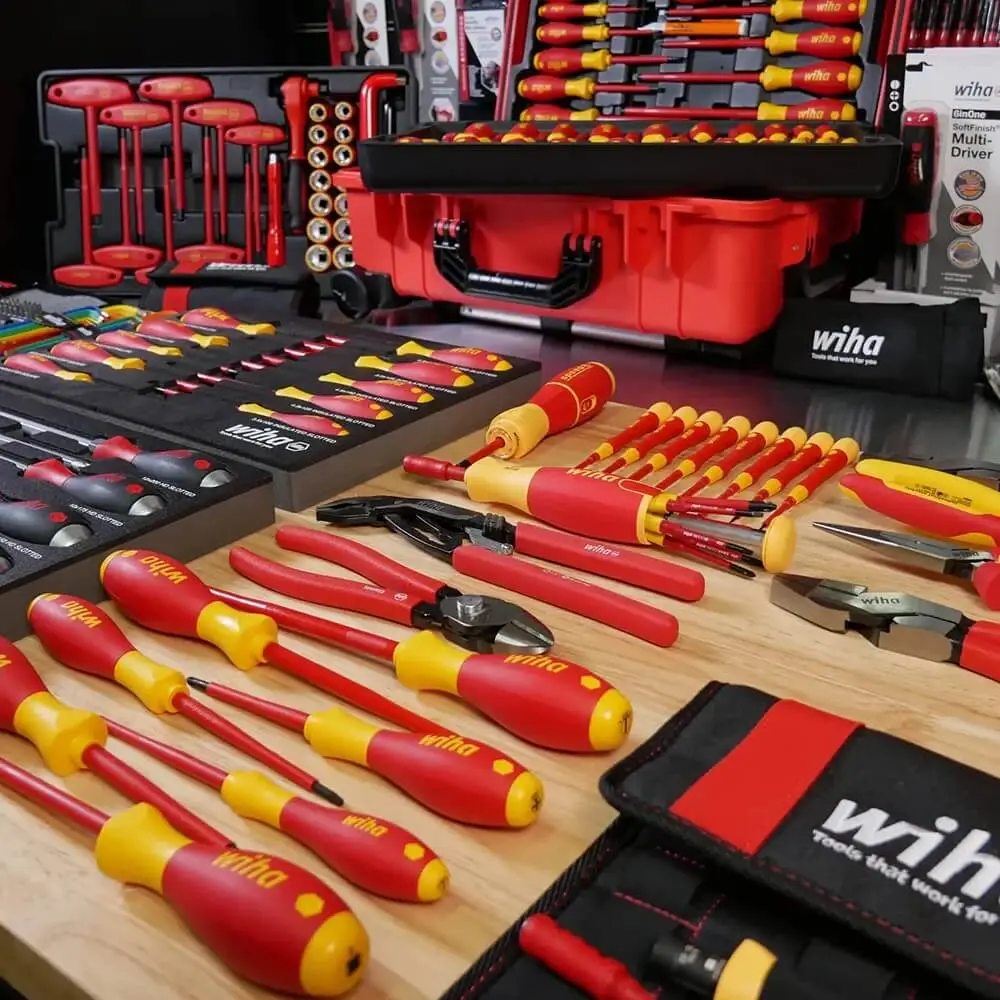
4. Insulated Tools
Insulated tools are a crucial part of an electrician’s safety arsenal, specifically designed to reduce the risk of electrical shock when working with energized electrical systems. These tools have insulating material, typically a specially formulated plastic or rubber, covering their conductive parts, except for the area needed for performing work, like the tip of a screwdriver or pliers’ jaws. This insulating layer acts as a barrier between the electrician and the electricity, helping prevent the unintentional flow of electrical current if the tool accidentally contacts an energized conductor.
It’s important to note that the insulating material used is not only resistant to electricity but is also designed to withstand the harsh conditions and heavy usage that tools often endure. Insulated tools come in various types, including screwdrivers, pliers, wrenches, and wire cutters. They must meet specific standards and be clearly marked with their rating, indicating the maximum voltage they can safely withstand.
Additionally, while insulated tools add a layer of protection, they are not a guarantee against shock and should be used as part of a comprehensive safety approach, which includes de-energizing circuits before working on them whenever possible. Lastly, regular inspection of insulated tools is necessary to ensure the integrity of the insulation isn’t compromised, as even small cracks or wear can reduce their protective capacity.
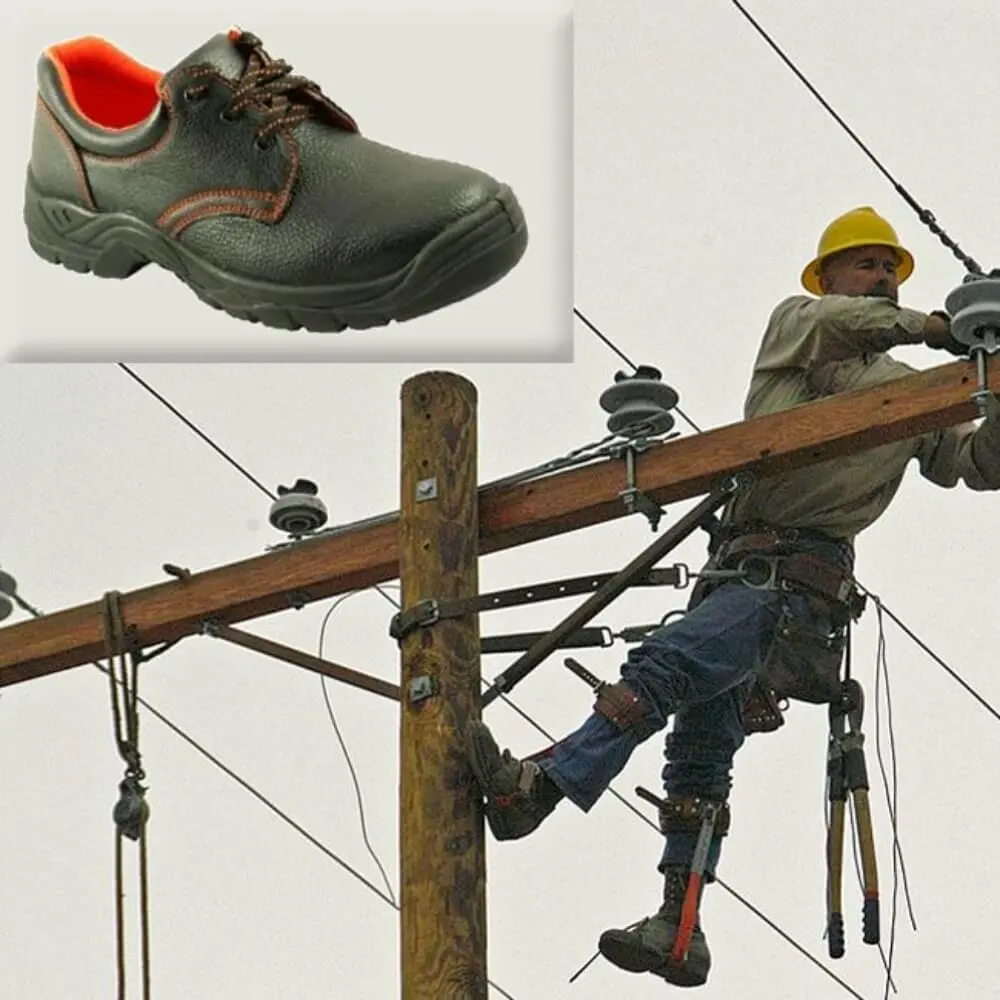
5. Electrical Safety Shoes
Electrical safety shoes, or dielectric footwear, are fundamental to personal protective equipment in electrical work. They are designed to provide protection from electrical hazards and decrease the risk of electric shocks. The construction of these shoes typically involves using non-conductive materials, such as rubber or leather, to prevent electrical conduction from the ground to the body, thereby acting as an insulating barrier. They are also designed to resist the penetration of sharp objects which may be present in a work environment.
In addition to insulating properties, electrical safety shoes often incorporate composite toe caps made from non-metallic materials such as Kevlar, plastic, or carbon fibre. These toe caps provide similar levels of protection as traditional steel toe caps against impact and crushing injuries but without the risk of conducting electricity. The soles of these shoes are often resistant to heat and certain chemicals and provide additional benefits like slip resistance. Like all PPE, safety shoes must meet specific safety standards and be properly maintained.
Regular inspection for wear and tear is essential, as damage to the shoe can compromise its electrical insulating properties. Despite their protective qualities, electrical safety shoes should be seen as a last line of defense and used with other safe work practices and equipment.
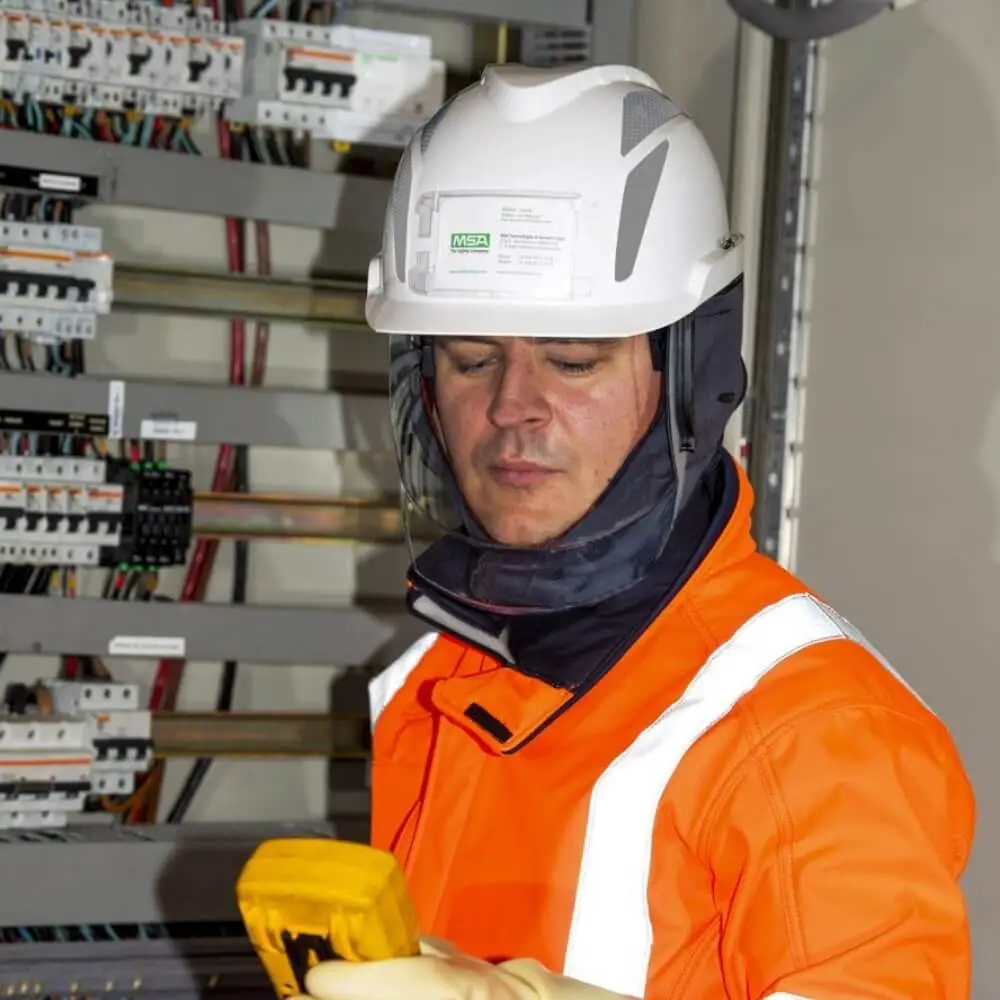
6. Hard Hats
Hard hats, or safety helmets, are essential personal protective equipment to safeguard workers from potential hazards. These include falling objects from overhead work areas, collision impacts when moving around a worksite, and electrical shocks when working with or around energized electrical systems. Made from robust materials like high-density polyethene (HDPE) or thermoplastics, hard hats are structured to provide a resilient shield for the head.
The helmet’s design often incorporates a suspension system inside the hat, creating a gap between the hat’s shell and the wearer’s head. This feature is crucial as it not only helps to distribute the force over a larger area during an impact, thereby reducing the potential for injury but also provides some space for air circulation, enhancing user comfort. For electrical work, many hard hats are designed to be electrically insulating or “Class E” (Electrical) helmets, meaning they are tested to withstand up to 20,000 volts, which helps protect the wearer from electrical shocks.
Some models may also include accessories like face shields for additional protection against electrical arc flashes or earmuffs for noise protection. Regular inspection for damage is crucial because even a small crack can compromise the hard hat’s protective integrity, and it should be replaced immediately if any signs of wear or damage are found.
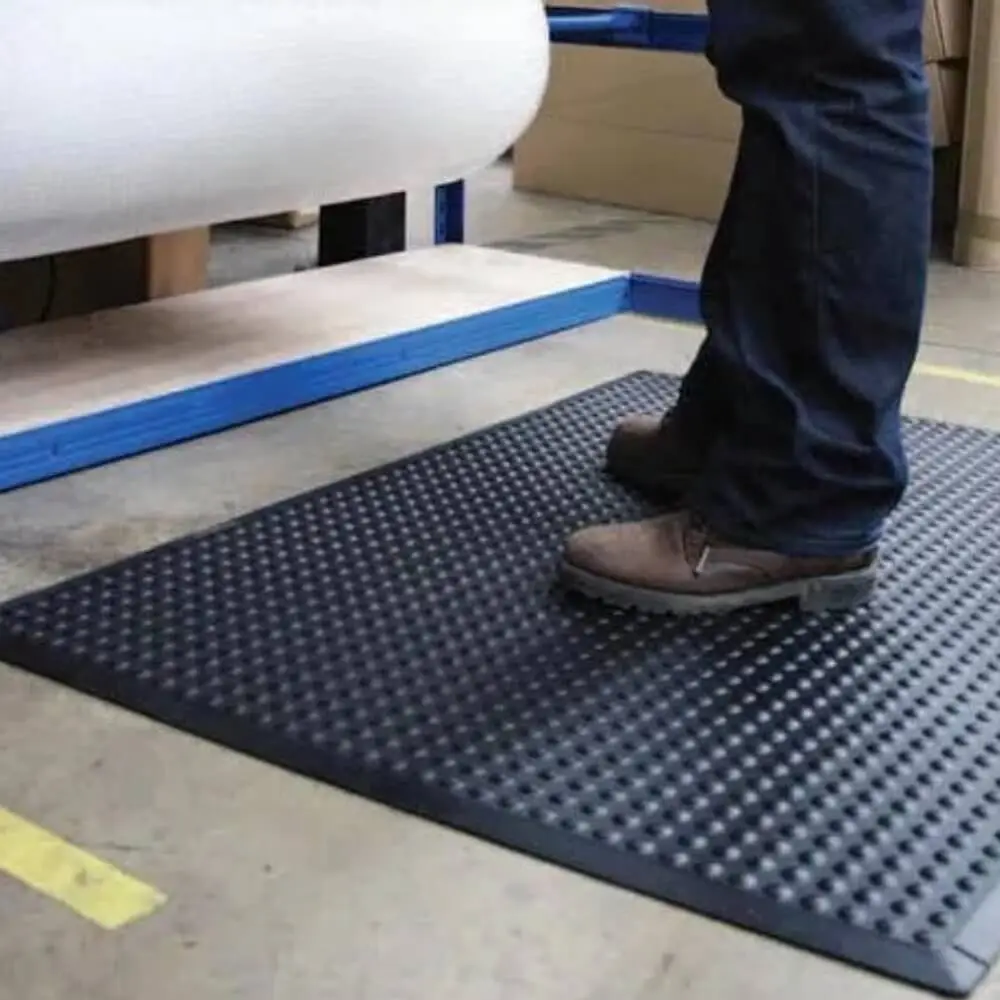
7. Insulated Mats
Insulated or dielectric mats play a crucial role in safeguarding individuals working around energized electrical systems by serving as an insulating barrier between the worker and the ground. These mats are designed to resist the flow of electrical current, reducing the risk of electrical shock if a person becomes a path to the ground for electrical energy. They are generally made from high-grade synthetic rubber or other non-conductive materials with strong electrical and mechanical resistance properties.
Depending on the specific design and material, these mats can withstand various voltage levels and must, therefore, be chosen based on the maximum voltage workers might encounter in their tasks. The surface of these mats is typically patterned to provide additional traction and reduce the risk of slipping, contributing to overall workplace safety. These mats must be placed correctly in the working area, ideally covering the potential conductive surface.
Like all safety equipment, insulated mats must be regularly inspected for any signs of wear, tear, or damage that could compromise their insulating properties. If any damage is detected, it must be replaced immediately. Insulated mats are an important part of a comprehensive electrical safety system but should be used with other personal protective equipment and safe work practices.
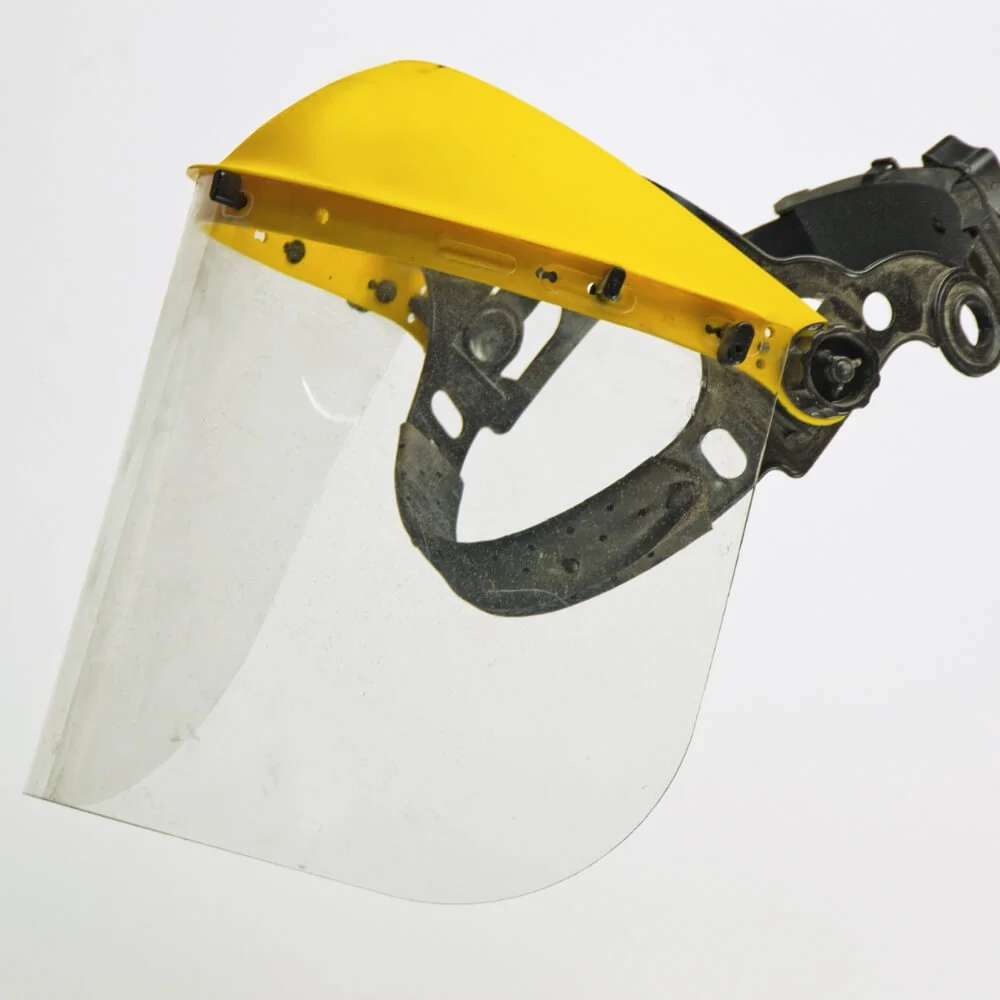
8. Face Shields
Face shields serve as an important line of defence in providing facial protection for individuals working with or around potentially hazardous electrical environments, offering additional safeguarding against burns from sparks, flash fires, and especially arc flashes. An arc flash, an electrical explosion, can produce intense heat, potentially causing severe burn injuries. Face shields are designed to cover the entire face, extending beyond the coverage of safety glasses or goggles, thus protecting the eyes and the skin on the face and neck. They are typically constructed from high-impact, heat-resistant materials and are often treated with anti-fog and scratch-resistant coatings for clear visibility under various working conditions.
Some face shields are rated for specific incident energy levels, measured in cal/cm^2, which represents the amount of thermal energy that could be delivered to a point in the event of an arc flash. This rating helps workers select the appropriate face shield based on the energy level they could potentially be exposed to.
It’s important to note that face shields should be used with safety glasses or goggles for complete eye protection, as face shields alone do not provide sufficient impact protection. Like all PPE, face shields should be regularly inspected for any damage and replaced if necessary. Face shields are one part of a comprehensive approach to safety that includes safe work practices and other protective equipment.
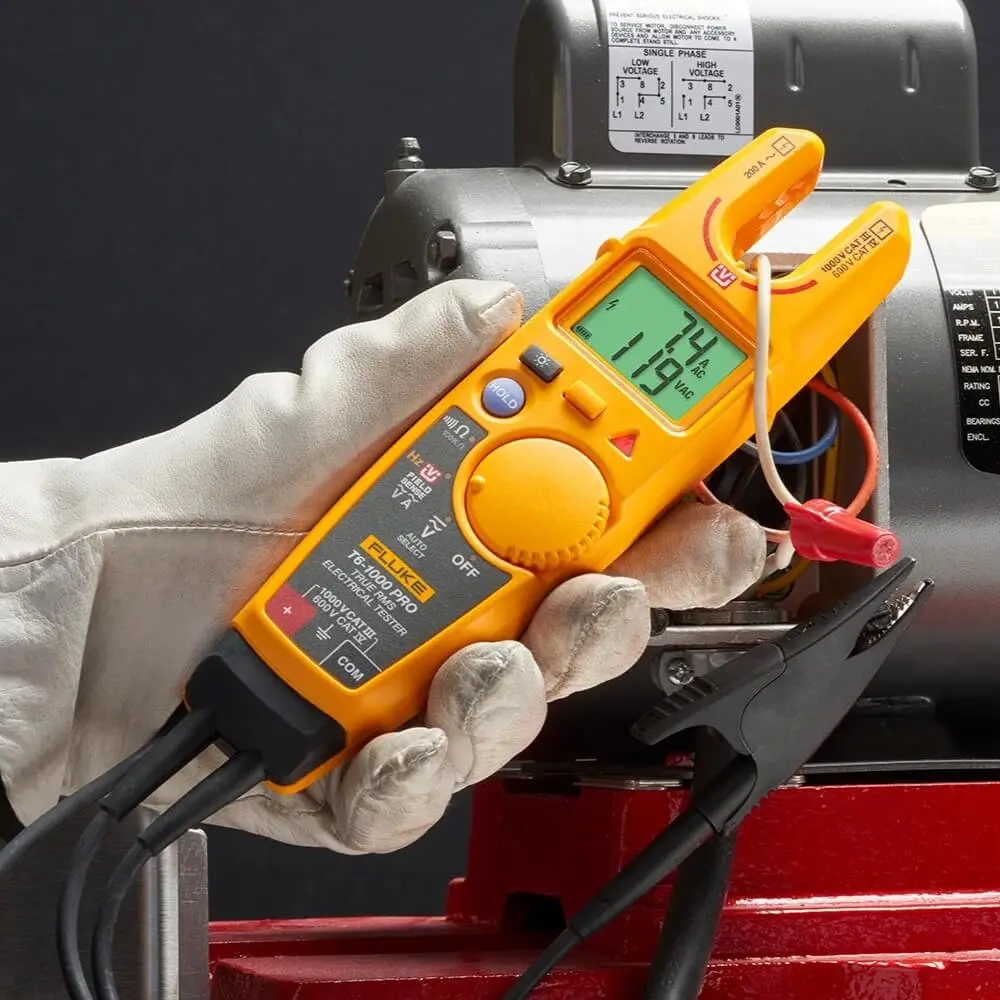
9. Voltage Detector
A non-contact voltage detector, sometimes called a voltage tester or voltage pen, is an essential safety tool in electrical work, even though it’s not a form of “wearable” personal protective equipment (PPE). This compact device is designed to detect the presence of voltage in a wire, cable, circuit, or device without requiring physical contact, hence its name. By bringing the detector close to the object in question, it can identify if an electrical current is present. It typically does this through visual and/or audible signals, such as flashing lights or beeping sounds. This allows workers to establish whether a line or cable is “live” (energized), providing crucial information that can prevent potential electrical shocks or electrocution.
Voltage detectors are rated for different voltage ranges, so it’s important to use a detector suitable for the specific working voltage to ensure accurate detection. While these tools significantly enhance safety, it’s worth noting that they should be used as part of a comprehensive electrical safety strategy that includes other forms of PPE, adhering to safety regulations, and maintaining safe work practices. Additionally, regular testing and maintenance of voltage detectors are vital to ensure they function correctly and accurately.
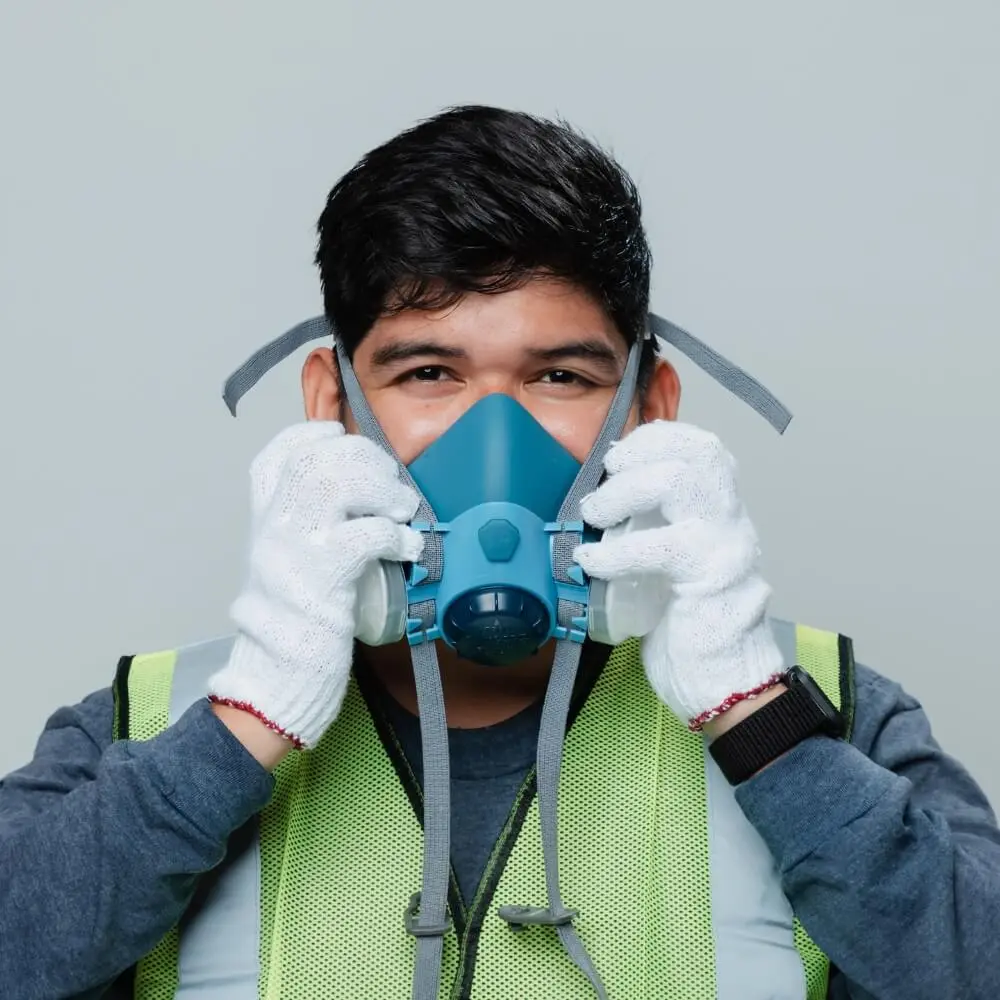
10. Respirator/Dust Mask
A respirator or dust mask is a crucial piece of safety equipment in electrical work scenarios where there is a potential for air contamination due to smoke, dust, or dangerous fumes. This can occur in various situations, such as soldering, releasing metal fumes and gases, or working near or with insulation materials that disintegrate into fine particulates. These masks work by filtering out harmful particles, preventing them from being inhaled into the respiratory system, which can cause serious health issues like lung disease.
There are several types of respirators, including disposable dust masks, half-face respirators, and full-face respirators. The selection depends on the level and type of contaminants in the working environment. For instance, a simple dust mask might be adequate for filtering out non-toxic dust particles, while a more advanced respirator with specific filters would be required when working with toxic gases or fumes. It’s crucial to ensure that the respirator fits well to provide maximum protection, and many designs incorporate adjustable straps for a secure fit.
Respirators and dust masks must meet specific safety standards to ensure their effectiveness. Like all PPE, they need to be regularly checked for damage and replaced when necessary. Despite their protective function, respirators and dust masks are not substitutes for proper ventilation and other safety measures when working in environments with potential air contaminants.
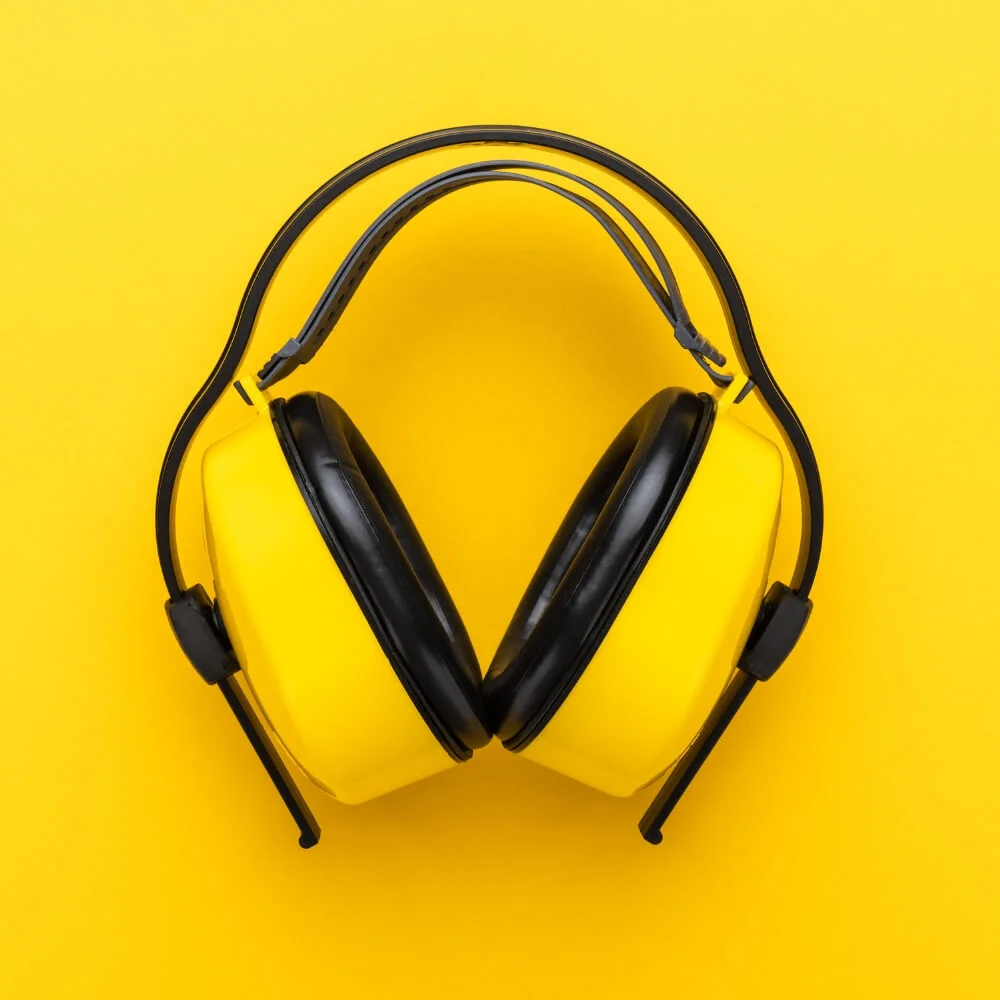
11. Hearing protection
Hearing protection is a critical safety measure in environments where there’s potential for high-intensity noise, such as during an arc flash incident. An arc flash is a type of electrical explosion that generates intense heat and light and creates a blast wave that can produce a sound pressure level exceeding 140 decibels, which is well beyond the threshold of pain and can cause immediate and permanent hearing damage.
Hearing protection for these scenarios typically comes in earplugs or earmuffs. Earplugs are small inserts that fit into the outer ear canal, and they are usually made from soft materials that can conform to the shape of the ear for a comfortable fit. Earmuffs fit over the outer ear and form a seal that reduces the noise level that can reach the eardrums. Both earplugs and earmuffs come in various models offering different levels of noise reduction, and they should be selected based on the specific noise levels that workers could potentially be exposed to.
In addition to protecting against high-intensity noise, hearing protection can also help reduce fatigue from constant exposure to lower noise levels, improving worker comfort and productivity. Like all PPE, hearing protection devices should be regularly inspected for any wear or damage that could reduce their effectiveness and replaced if necessary.
Remember, appropriate training on the use and maintenance of PPE is critical. Also, PPE should always be used with proper safety practices and not as a substitute for them. It’s important to note that the level of PPE required can vary depending on the specific job and the potential electrical hazards present.
Conclusion
To conclude, personal protective equipment (PPE) is indispensable in ensuring the safety of those working in electrical environments. Each piece of PPE, be it insulated gloves, hard hats, or respirators, serves a specific purpose in shielding workers from the various hazards associated with electrical work. As we’ve explored in our guide, understanding these protective tools and their correct usage can literally be a lifesaver. However, remember that PPE is the last line of defense and should be used with safe work practices, comprehensive training, and a well-maintained work environment. Safety should never be taken for granted, and it’s our collective responsibility to ensure that the safety culture is emphasized and upheld in all aspects of electrical work.