Electrical safety is paramount in all industries that deal with electricity. This includes construction sites, manufacturing plants, offices, and even homes. The importance of electrical safety cannot be overstated, as electrical accidents can cause serious injury or even death. In this blog, we will discuss the principles of electrical safety and why they are so important.
Whether you are an electrician, an engineer, or just someone who wants to stay safe around electricity, this blog will provide you with valuable information to help you avoid electrical accidents and stay safe.
Why Is Electrical Safety Important?
Electrical safety is important because it protects individuals and property from the hazards of electricity. These hazards can result in severe injuries, fatalities, and extensive damage if proper precautions are not taken. Here are key reasons why electrical safety is vital:
- Prevents Injuries and Fatalities: Reduces risks of electric shock, burns, and electrocution that can cause severe harm or death.
- Avoids Fires and Explosions: It prevents electrical faults, such as short circuits, from causing sparks, overheating, and property damage.
- Reduces Downtime and Costs: Minimizes system failures and expensive repairs, ensuring uninterrupted operations.
- Ensures Regulatory Compliance: Adheres to safety standards and avoids legal penalties or fines.
- Enhances Workplace Safety: Creates a safer environment, boosting employee morale and productivity.
- Protects Equipment: Safeguard systems from power surges, overloads, and improper handling.
- Promotes Awareness: Educates individuals to recognize hazards and respond effectively to emergencies.
By emphasizing electrical safety, individuals and organizations can prevent accidents, protect lives, and ensure the reliable operation of electrical systems in homes, workplaces, and public spaces. Proper use of electrical safety signs plays a key role in alerting people to potential hazards and reinforcing safety protocols.
Electrical Safety Principles
Electrical safety is crucial to prevent accidents, injuries, and property damage caused by electrical hazards. Here are some key principles of electrical safety:
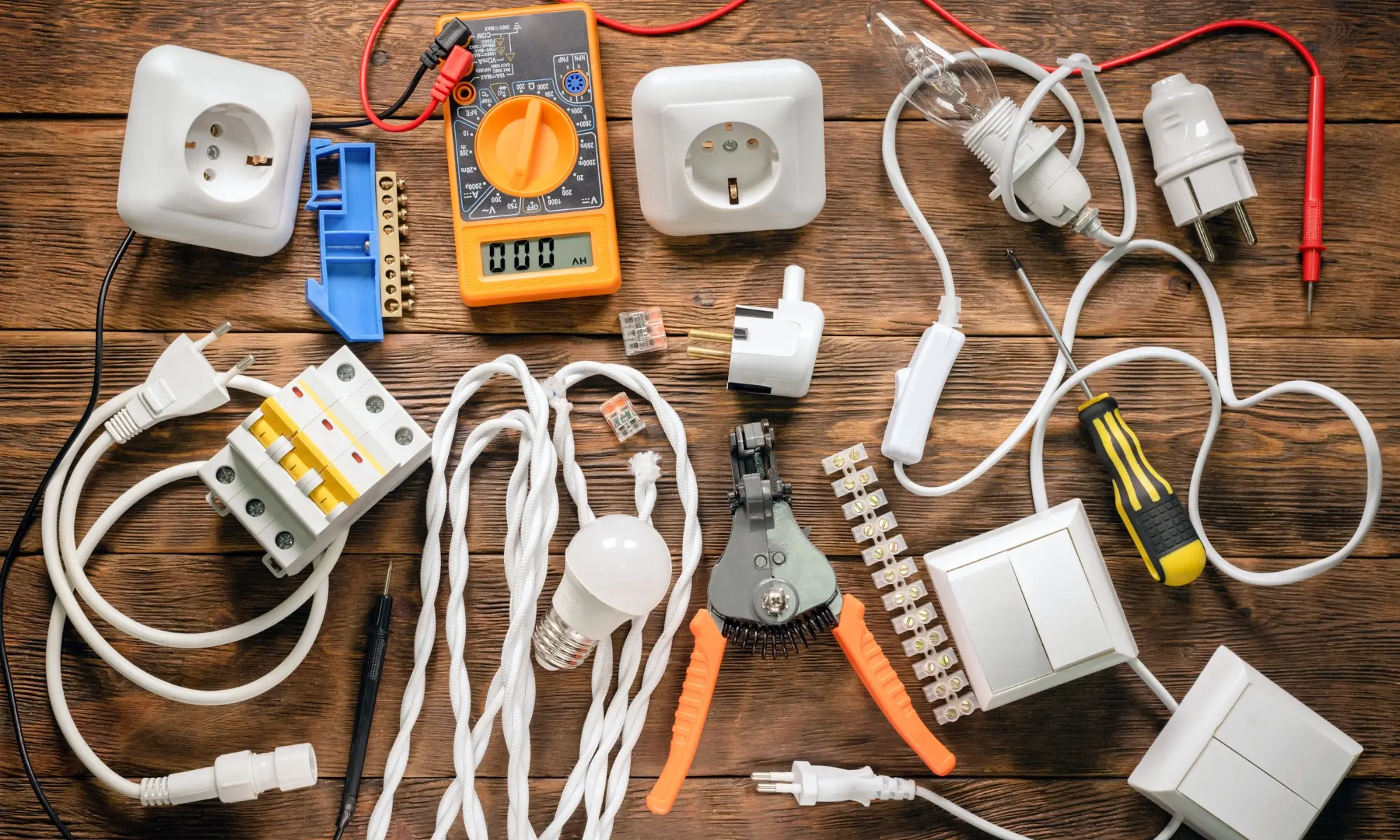
1. Understand The Basics Of Electricity
Understanding the basics of electricity is a crucial first step in ensuring electrical safety. By being knowledgeable about the fundamental concepts of electricity, individuals can better identify potential hazards and take appropriate safety measures to prevent accidents and injuries.
Key concepts include:
- Voltage: Voltage, also known as electric potential difference, is the force that pushes electric charge through a conductor. It is measured in volts (V) and often compared to pipe water pressure. Higher voltage means a higher potential for electrical hazards.
- Current: Electric current is the flow of electric charge through a conductor, such as a wire. It is measured in amperes (A) and can be compared to the flow of water through a pipe. Higher currents can generate more heat and pose a greater risk of electrocution or fire.
- Resistance: Resistance is a property of materials that opposes the flow of electric current. It is measured in ohms (Ω) and can be compared to the narrowing of a water pipe, restricting the flow of water. Materials with high resistance, like insulators, impede the flow of electric current, while materials with low resistance, like conductors, allow the flow of electric current.
- Electrical circuits: An electrical circuit is a closed loop through which electric current flows. It consists of a power source (e.g., a battery or generator), conductors (wires), a load (an electrical device, such as a light bulb or motor), and a return path to the power source. Circuits can be designed in series, parallel, or a combination of both.
By comprehending these basic concepts, individuals can better understand how electrical systems work, recognize potential hazards, and apply appropriate safety measures to reduce the risk of electrical accidents.
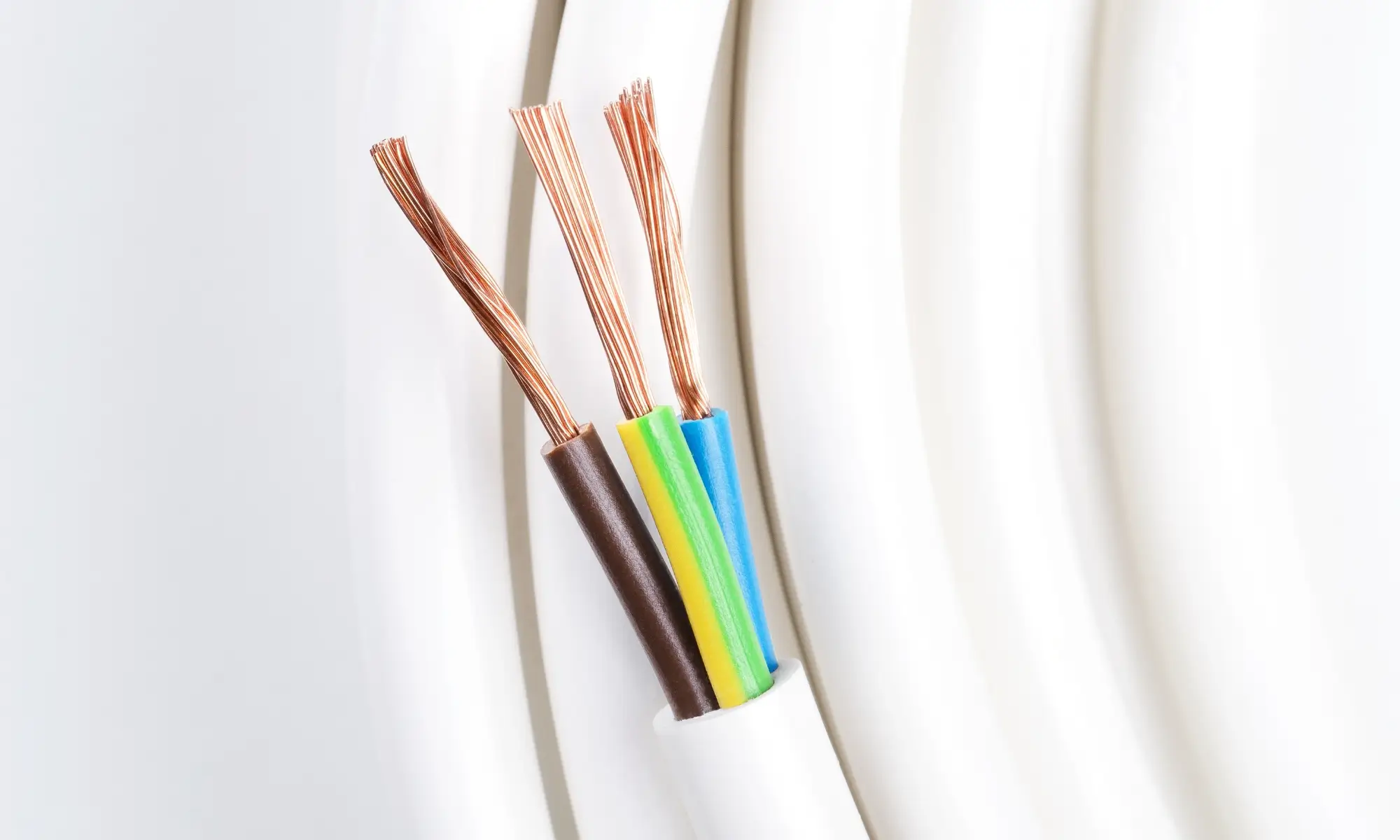
2. Insulate Conductors
Insulating conductors is a critical principle of electrical safety. It helps prevent accidental contact with live wires, reducing the risk of electrical shock, burns, and short circuits. Proper insulation ensures that electrical current is contained within the conductors, minimizing the potential for accidents and injuries.
Key considerations for insulating conductors include:
- Select appropriate insulation materials: Insulation materials should be non-conductive, such as plastic, rubber, or other similar materials. These materials prevent the flow of electrical current, ensuring that the live conductors remain isolated from surrounding objects and people.
- Inspect insulation regularly: Insulation can deteriorate over time, becoming less effective or even exposing live conductors. Regularly inspect the insulation on electrical wires and equipment for signs of wear or damage, and replace it as necessary.
- Use insulated tools: When working with electrical equipment, use insulated tools with non-conductive handles to reduce the risk of accidental contact with live conductors.
- Guard against environmental factors: Insulation should be chosen based on the specific environment in which the conductor will be used. For example, outdoor conductors should have insulation that can withstand exposure to sunlight, moisture, and temperature fluctuations, while conductors in industrial settings may require insulation resistant to chemicals or other harsh conditions.
- Comply with regulations and standards: Ensure that the insulation used on conductors complies with local regulations and industry standards, such as the National Electrical Code (NEC) or the International Electrotechnical Commission (IEC) standards.
Properly insulating conductors can significantly reduce the risk of electrical accidents and injuries, creating a safer environment for both workers and equipment.
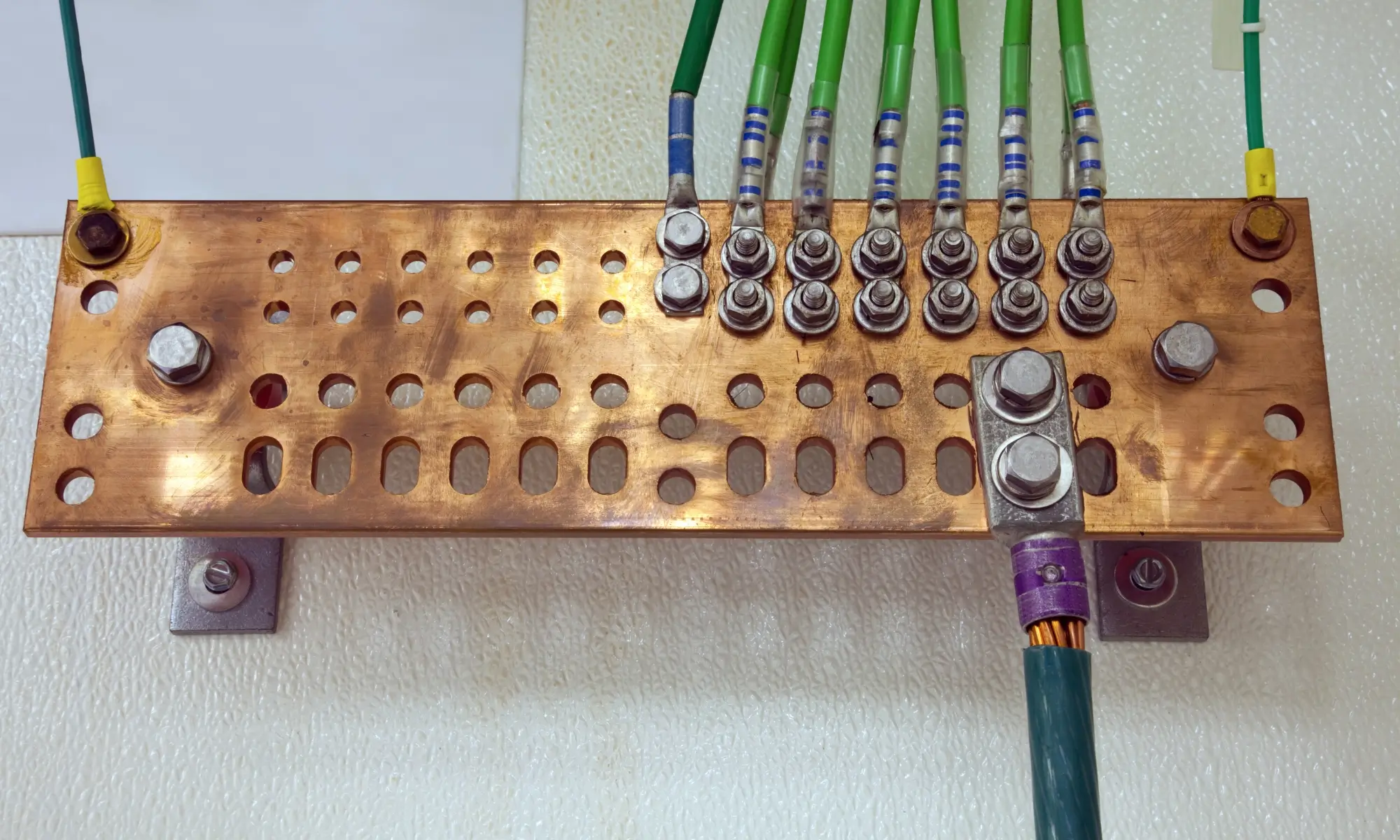
3. Proper Grounding
Proper grounding is a fundamental principle of electrical safety, as it helps protect people and equipment from electrical faults and provides a safe path for current to flow in the event of a fault. Grounding minimizes the risk of electrical shock, equipment damage, and fires by directing excess current away from people and sensitive components.
Key aspects of proper grounding include:
- Grounding conductors: Electrical systems should have a grounding conductor connected to a grounding electrode, such as a metal water pipe or a ground rod. This conductor creates a low-resistance path for fault current to flow safely to the earth, preventing hazardous voltage levels on equipment and reducing the risk of electrical shock.
- Grounded outlets: Use grounded (three-prong) outlets for all electrical devices, especially those with metal casings or high power consumption. The third prong connects to the grounding conductor, providing additional protection against electrical faults.
- Ground-fault circuit interrupters (GFCIs): Install GFCIs in areas where water and electricity are in close proximity, such as bathrooms, kitchens, and outdoor outlets. GFCIs monitor the current flow and quickly trip the circuit if they detect a ground fault, reducing the risk of electrical shock.
- Equipment grounding: Ensure that all metal parts of electrical equipment are properly grounded. This includes the metal enclosures of devices, such as motors, transformers, and control panels, and any conductive materials that could become energized during a fault.
- Regular inspections and maintenance: Periodically inspect your grounding system for proper connections, corrosion, or other signs of damage. Regular maintenance helps ensure that the grounding system remains effective in protecting against electrical hazards.
- Compliance with regulations and standards: For proper grounding practices and requirements, follow local regulations and industry standards, such as the National Electrical Code (NEC) or International Electrotechnical Commission (IEC) standards.
By implementing proper grounding techniques and regularly inspecting and maintaining your grounding system, you can significantly reduce the risk of electrical accidents, protect valuable equipment, and ensure a safer environment for both workers and equipment.

4. Circuit Protection
Circuit protection is a vital principle of electrical safety. It safeguards electrical systems from damage caused by overloads, short circuits, and ground faults. By implementing appropriate circuit protection devices, you can prevent equipment damage, minimize fire risks, and reduce the potential for electrical shock.
Key aspects of circuit protection include:
- Fuses: Fuses are designed to protect electrical circuits by melting a metal filament when the current exceeds a specified rating. Once the fuse is blown, it must be replaced to restore the electrical circuit. Fuses come in various types and ratings, depending on the specific application.
- Circuit breakers: Circuit breakers are automatic switches that detect an overload or short circuit and interrupt the current flow by tripping the switch. Unlike fuses, circuit breakers can be reset after the fault has been corrected, making them a reusable protection method. Circuit breakers come in different types, such as thermal, magnetic, or a combination of both.
- Ground-fault circuit interrupters (GFCIs): GFCIs are specialized devices designed to protect against ground faults by constantly monitoring the current flow in a circuit. If the GFCI detects an imbalance in the current flow, indicating a potential ground fault, it quickly trips the circuit, cutting off the power supply. GFCIs are commonly used in areas with increased risk of electric shock, such as bathrooms, kitchens, and outdoor outlets.
- Arc-fault circuit interrupters (AFCIs): AFCIs protect against arc faults, which can occur when damaged or worn wiring creates a high-temperature electrical discharge. Arc faults can lead to fires, so AFCIs are designed to detect these events and interrupt the circuit, preventing potential hazards.
- Proper sizing and selection: Choose the appropriate circuit protection devices based on the specific electrical system and equipment requirements. Ensure that the devices are rated according to the system’s voltage and current specifications and follow local regulations and industry standards for proper installation.
By incorporating effective circuit protection measures, you can enhance electrical safety, protect valuable equipment, and reduce the likelihood of electrical accidents and fires.
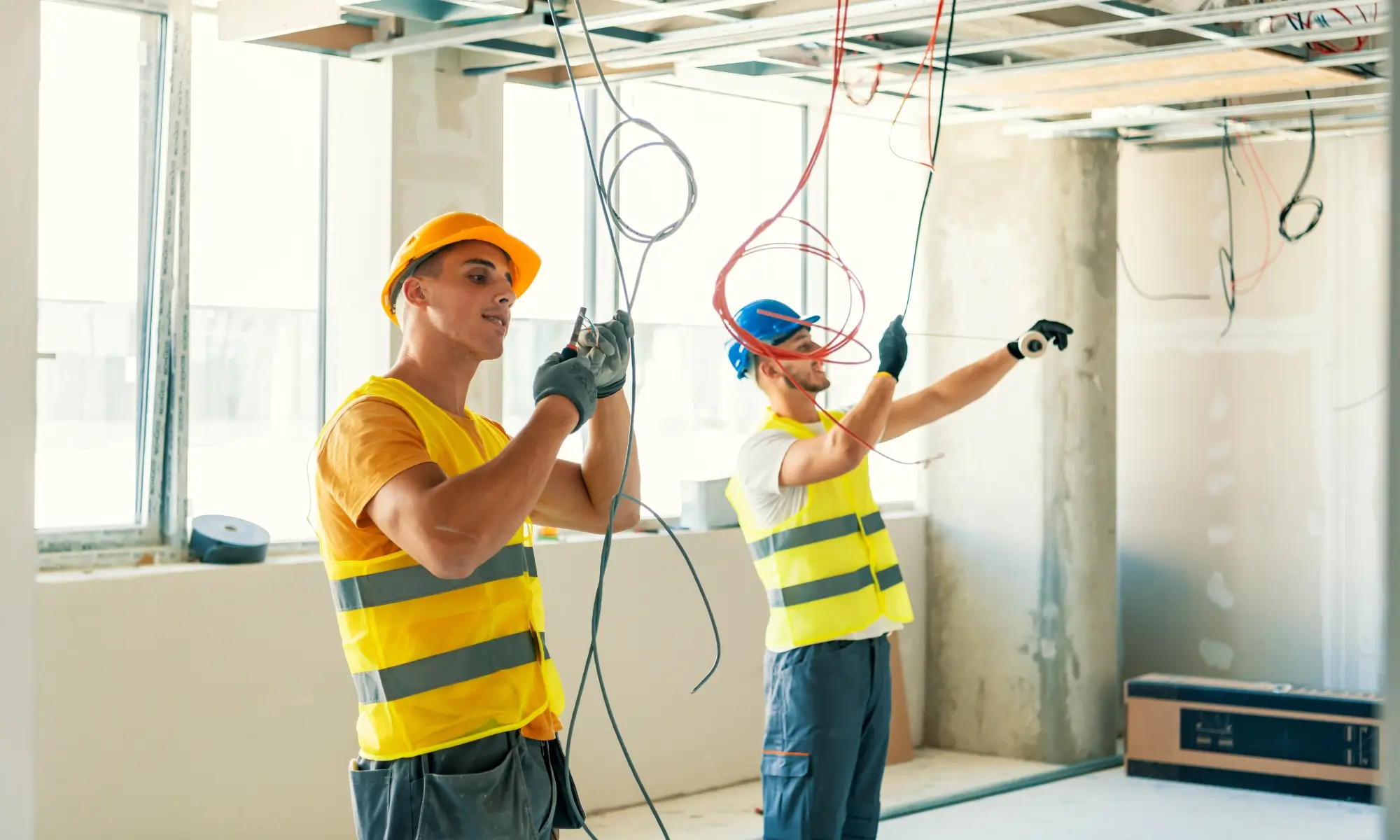
5. Maintain Safe Distances
Maintaining safe distances is a key principle of electrical safety. It helps prevent accidental contact with live conductors, electrical equipment, and energized systems. Individuals can reduce the risk of electrical shock, arc flash incidents, and other accidents by keeping an appropriate distance from electrical hazards.
Important aspects of maintaining safe distances include:
- Approach boundaries: Understand and adhere to the defined approach boundaries for electrical systems, which may include limited, restricted, and prohibited approach boundaries. These boundaries are established based on the voltage level and potential hazards associated with the electrical equipment.
- Clearance distances: Observe the minimum clearance distances specified for electrical installations, such as overhead power lines or electrical substations. These distances are designed to prevent accidental contact with energized conductors and reduce the risk of electrical shock or electrocution.
- Arc flash boundaries: Be aware of arc flash boundaries, which indicate the distance at which an arc flash can cause severe burns or injuries. Workers should avoid crossing these boundaries without proper personal protective equipment (PPE) and training.
- Safe work practices: When working around electrical equipment, follow safe work practices, such as maintaining a safe distance from energized components, using insulated tools, and avoiding contact with conductive materials.
- Exclusion zones: Establish and enforce exclusion zones around electrical work areas, where only qualified personnel with the necessary PPE and training can enter. This helps minimize the risk of untrained individuals coming into contact with electrical hazards.
- Use of barriers and warning signs: Install physical barriers, such as guardrails or covers, and post warning signs to indicate the presence of electrical hazards and remind individuals to maintain a safe distance.
- Training and awareness: Ensure that all workers are adequately trained in electrical safety, including the importance of maintaining safe distances from electrical hazards and the appropriate approach boundaries for specific tasks and equipment.
By maintaining safe distances from electrical hazards and following established approach boundaries, individuals can significantly reduce the risk of electrical accidents and create a safer environment for both workers and equipment.
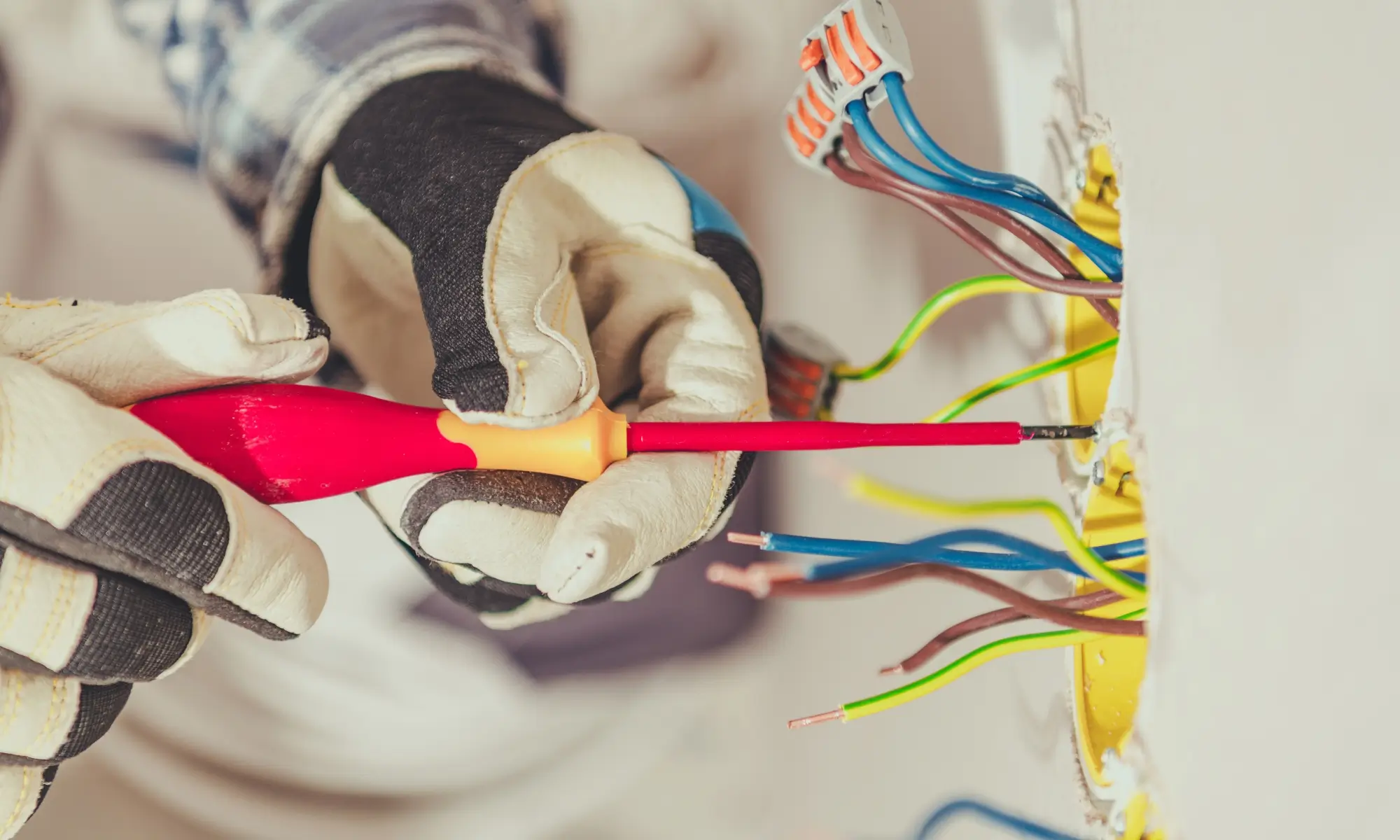
6. Use Appropriate Personal Protective Equipment (PPE)
Using appropriate personal protective equipment (PPE) is also a key principle of electrical safety, as it provides a crucial line of defense for individuals working with or around electricity. By wearing suitable PPE, workers can minimize the risk of injury from electrical hazards such as shocks, burns, and arc flashes.
Essential PPE for electrical safety includes:
- Insulated gloves: Insulated gloves, made from materials like rubber, provide protection against electrical shock by creating a barrier between the worker and live conductors. These gloves should be rated for the specific voltage level being worked on and should be inspected regularly for signs of wear or damage.
- Safety glasses or goggles: Eye protection is essential when working with electricity, as it helps prevent injuries from flying debris, sparks, or intense light produced during electrical work. Safety glasses or goggles should always be worn when working on or near electrical equipment.
- Face shields: Face shields protect the face from burns and other injuries caused by electrical arcs, explosions, or flash hazards. They should be used in conjunction with safety glasses or goggles for complete eye and face protection.
- Flame-resistant clothing: Flame-resistant (FR) clothing is designed to resist ignition and minimize the spread of flames, providing protection against burns caused by arc flashes or electrical fires. Workers should wear FR clothing that meets industry standards, such as those established by the National Fire Protection Association (NFPA).
- Insulated footwear: Insulated footwear, made from non-conductive materials, can help protect workers from electrical shock by reducing the flow of current through the body. Electrical hazard (EH) rated shoes or boots are recommended for those working in environments with potential electrical hazards.
- Dielectric hard hats: Dielectric hard hats, made from non-conductive materials, protect the head from electrical shock and falling objects. They should meet relevant safety standards and be used in conjunction with other PPE to ensure complete protection.
- Protective hearing equipment: Electrical work may involve loud noises that can damage hearing. Workers should wear earplugs or earmuffs to protect their hearing when working in high-noise environments.
By selecting and using appropriate PPE, workers can significantly reduce the risk of injury from electrical hazards and ensure a safer working environment. Remember to inspect, maintain, and replace PPE as needed to ensure its effectiveness.
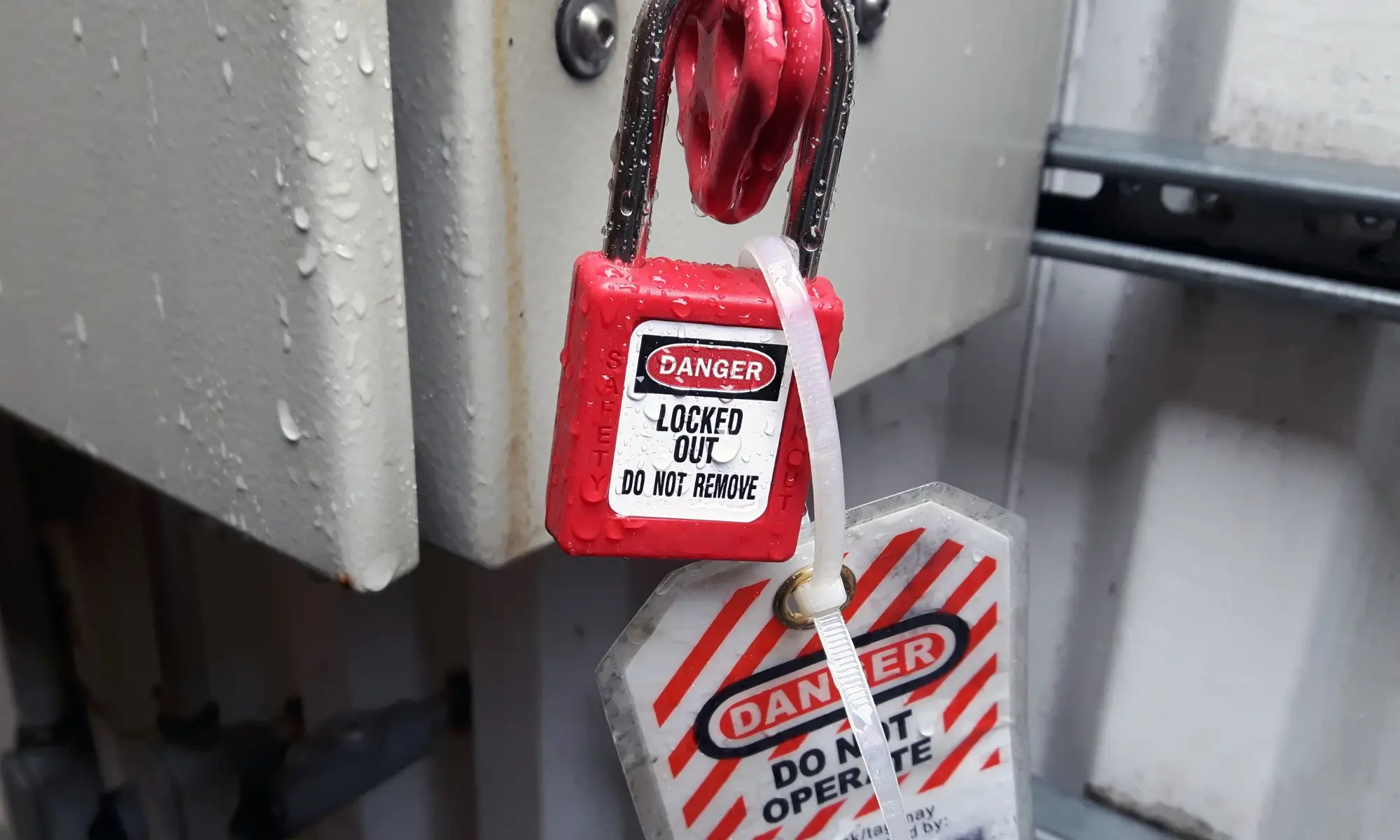
7. Follow Lockout/Tagout Procedures
Following Lockout/Tagout procedures is an essential principle of electrical safety, as it ensures that electrical equipment and systems are de-energized and cannot be accidentally re-energized during maintenance, repair, or other work activities. This practice helps prevent injuries and fatalities caused by unexpected energization, the release of stored energy, or equipment start-up.
Key elements of Lockout/Tagout procedures include:
- Develop a Lockout/Tagout program: Establish a comprehensive Lockout/Tagout program within your organization, outlining specific procedures, responsibilities, and requirements for equipment and personnel.
- Identify energy sources: Before working on electrical equipment, identify all energy sources, such as electrical, mechanical, hydraulic, pneumatic, and stored energy, and ensure they are properly isolated and controlled.
- Shut down equipment: Using the established shutdown procedure, typically switching off the power and disconnecting the equipment from the energy source.
- Isolate energy sources: Physically isolate the energy sources by disconnecting, blocking, or otherwise preventing energy flow to the equipment. This may involve unplugging devices, opening circuit breakers, or closing valves.
- Apply Lockout/Tagout devices: Attach lockout devices, such as padlocks, to the energy-isolating mechanisms to prevent the equipment from being re-energized. Attach warning tags to inform others that the equipment is locked out and should not be operated.
- Verify de-energization: Test the equipment to ensure it has been successfully de-energized and that there is no residual or stored energy. Use appropriate testing instruments, such as voltage testers, to confirm the absence of electrical energy.
- Perform the required work: Once the equipment is de-energized and locked out, perform maintenance, repair, or other work activities.
- Restore equipment to service: After completing the work, follow established procedures for removing Lockout/Tagout devices, re-energizing the equipment, and returning it to service. This process should involve verifying that all workers are clear of the equipment and that all tools and materials have been removed.
By adhering to proper Lockout/Tagout procedures, you can significantly reduce the risk of accidents and injuries related to unexpected equipment energization and ensure a safer work environment for all personnel involved.
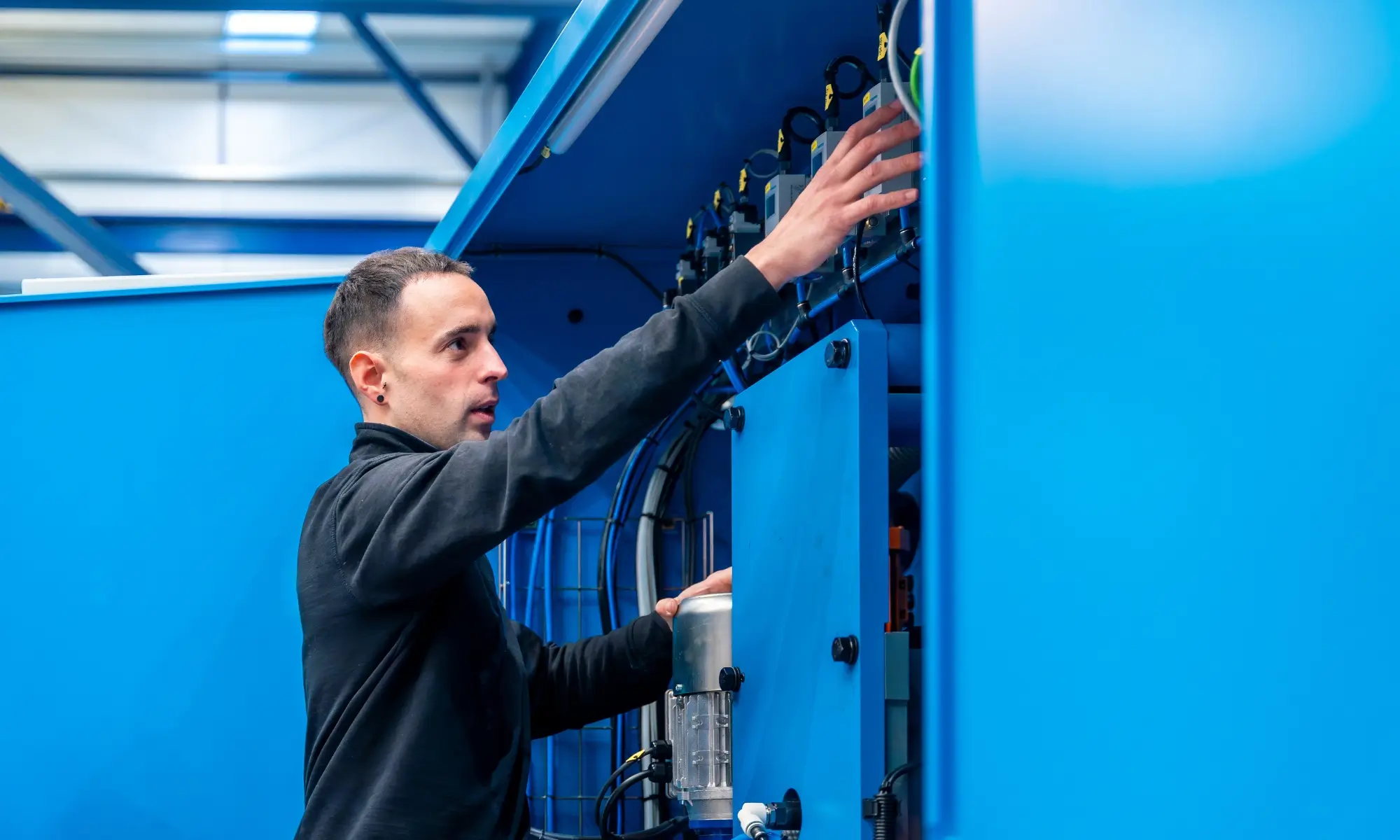
8. Properly Maintain Electrical Equipment
Properly maintaining electrical equipment is also an essential principle of electrical safety, as it ensures that devices and systems operate safely and efficiently. Regular maintenance can help prevent electrical hazards, such as short circuits, overloads, and fires, by identifying and addressing potential issues before they escalate.
Key aspects of properly maintaining electrical equipment include:
- Scheduled maintenance: Develop a schedule for all electrical equipment, including inspections, testing, and servicing. Regular maintenance schedules can help identify issues early and prevent unexpected equipment failure or hazards.
- Visual inspections: Conduct regular visual inspections of electrical equipment, looking for signs of wear, damage, or overheating. Check for loose connections, frayed or damaged wiring, and any signs of corrosion.
- Testing and calibration: Periodically test and calibrate electrical equipment to ensure it functions correctly and within specified tolerances. This may include testing circuit breakers, GFCIs, and other protective devices to ensure they operate as intended.
- Cleaning and servicing: Clean electrical equipment to remove dust, dirt, and debris, which can cause overheating or reduced performance. Perform routine servicing tasks, such as lubricating moving parts or replacing worn components, as needed.
- Repair and replacement: Promptly repair or replace damaged electrical equipment to prevent further deterioration or hazards. Always use the correct replacement parts and follow the manufacturer’s repair guidelines.
- Recordkeeping: Maintain accurate records of all maintenance activities, including inspections, testing, repairs, and replacements. This documentation can help track the performance and condition of electrical equipment over time and support effective maintenance planning.
- Training and awareness: Ensure that individuals responsible for maintaining electrical equipment are adequately trained and aware of the potential hazards, best practices, and relevant regulations and standards related to electrical safety.
By properly maintaining electrical equipment and regularly inspecting and servicing devices, you can minimize the risk of electrical accidents, improve equipment performance, and extend the life of your electrical systems.
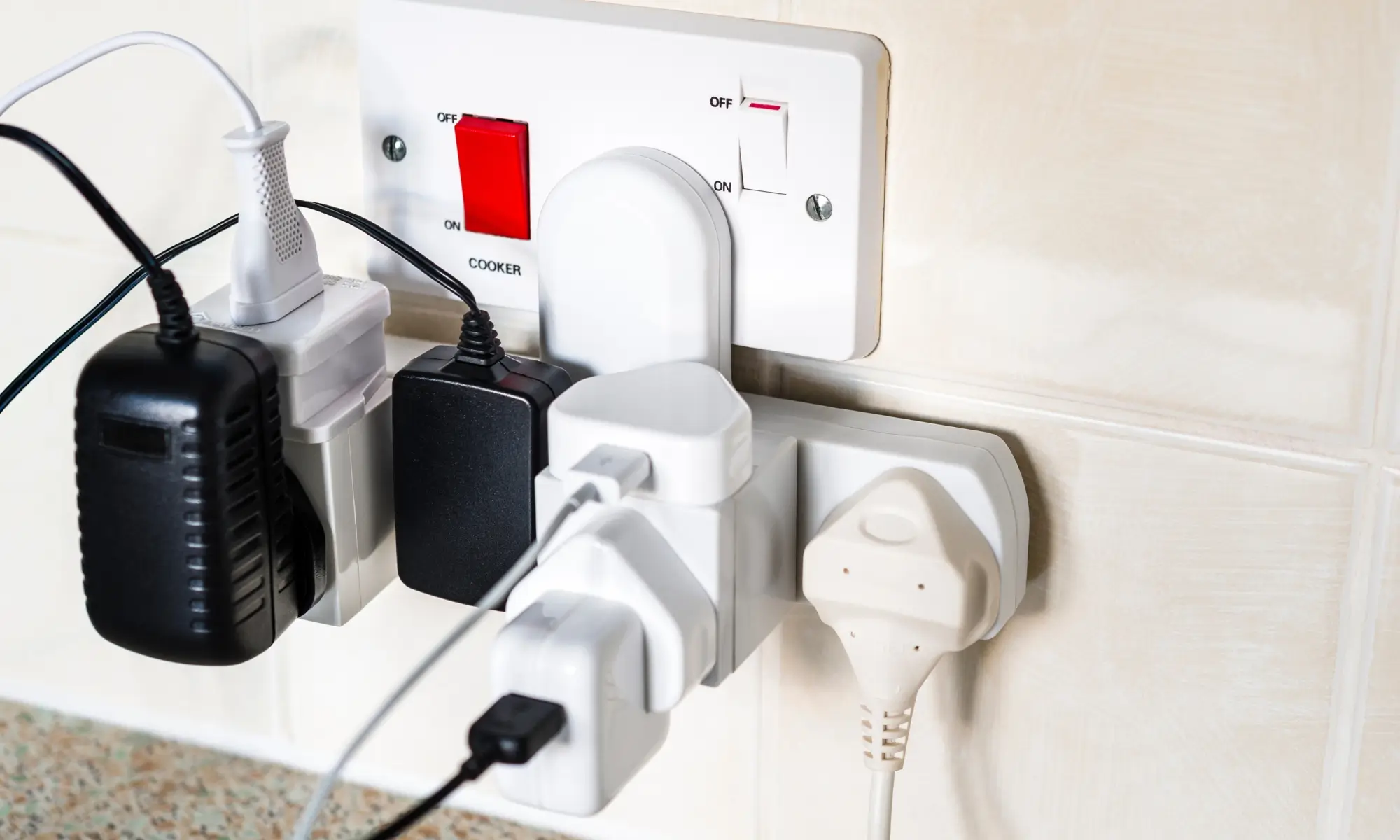
9. Avoid Overloading Circuits
Avoiding circuit overloads is also a crucial principle of electrical safety. Overloads can cause excessive heat, damage to electrical equipment, and even fires. By ensuring that electrical circuits are not overloaded, you can maintain a safe environment and minimize the risk of electrical accidents.
Key guidelines for avoiding circuit overloads include:
- Know the circuit’s capacity: Familiarize yourself with the capacity of each circuit in your home or workplace. The circuit’s capacity, typically expressed in amperes (A), determines the maximum amount of electrical current it can safely handle.
- Calculate the load: Add up the total electrical load of all devices connected to a single circuit, taking into account their wattage (W) and voltage (V). Ensure that the total load does not exceed the circuit’s capacity.
- Use the 80% rule: As a safety measure, avoiding exceeding 80% of the circuit’s capacity is recommended. This helps account for potential variations in electrical demand and provides a margin of safety against overloads.
- Distribute the load: To prevent overloading, avoid plugging too many devices into a single outlet or circuit. Distribute high-power appliances and devices across multiple circuits.
- Avoid extension cord overuse: While extension cords can be useful in certain situations, overusing them can contribute to circuit overload. Do not plug multiple high-power devices into a single extension cord; avoid connecting multiple extension cords.
- Use surge protectors: Surge protectors can help protect your devices from voltage spikes and overloads. Choose a surge protector with an appropriate capacity for your connecting devices, and ensure it’s properly grounded.
- Regular maintenance and inspection: Inspect your electrical system, including wiring, outlets, and circuit breakers, for signs of wear or damage. Regular maintenance can help identify potential issues before they lead to overloads or other hazards.
By following these guidelines and being mindful of the electrical load on your circuits, you can effectively avoid overloading and reduce the risk of electrical accidents and fires.
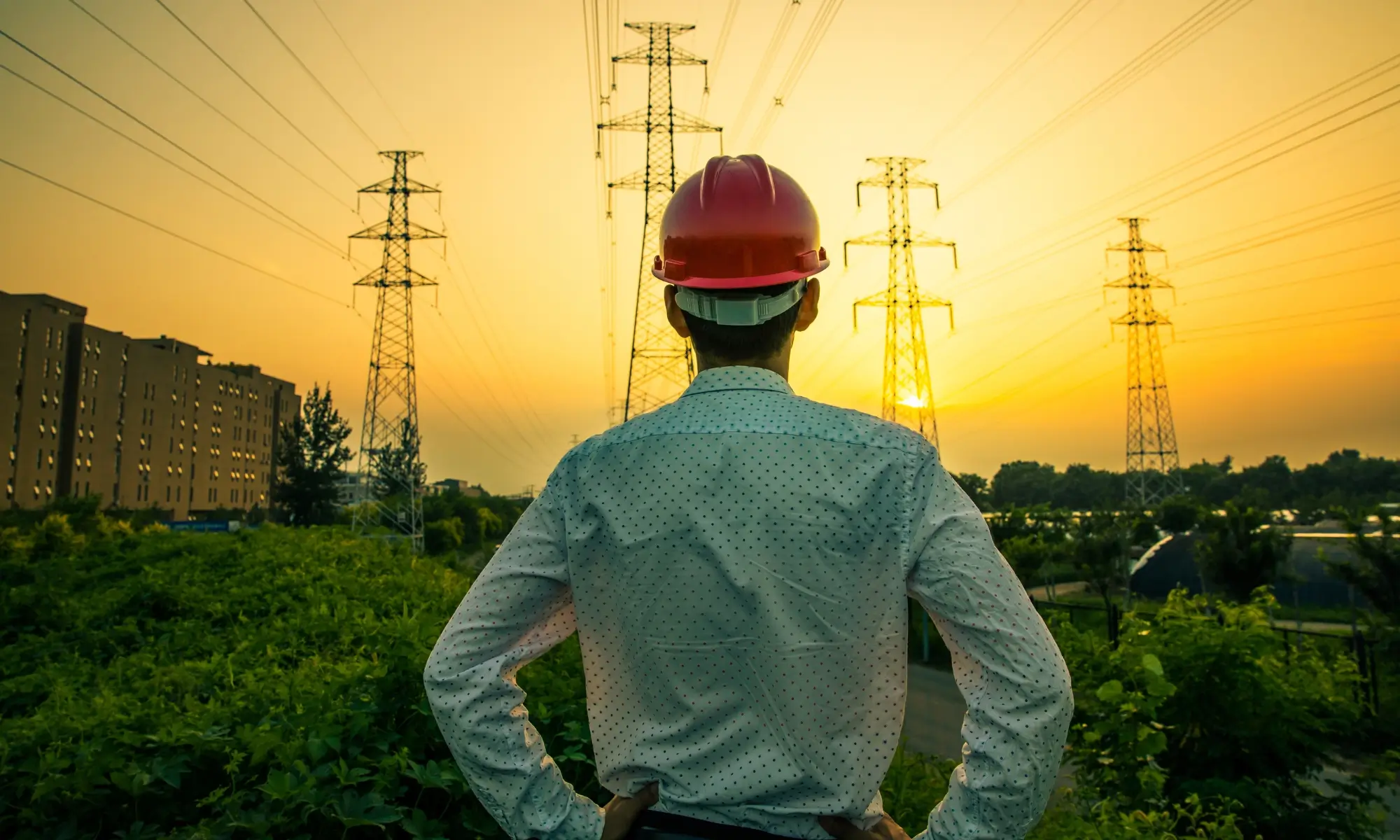
10. Be Aware Of Environmental Factors
Being aware of environmental factors is also a critical principle of electrical safety, as certain conditions can increase the risk of electrical hazards or affect the performance of electrical equipment. By understanding how environmental factors influence electrical safety, individuals can take appropriate precautions and maintain a safer work environment.
Key environmental factors to consider include:
- Moisture and humidity: Moisture and high humidity can increase the risk of electrical shock, as water is a conductor of electricity. Always exercise caution when working near water or damp environments, and use GFCIs to protect against ground faults. Additionally, ensure that electrical equipment is rated for wet or damp locations.
- Dust and debris: Accumulating dust and debris on or around electrical equipment can cause overheating, reduced performance, or even fires. Regularly clean electrical equipment and enclosures to prevent buildup, and consider using dust-tight enclosures in particularly dusty environments.
- Temperature extremes: Extreme temperatures, both hot and cold, can affect the performance and lifespan of electrical equipment. Ensure that equipment is rated for the specific environmental conditions it will be exposed to, and consider using temperature controls or insulation to maintain safe operating conditions.
- Corrosive or hazardous environments: Certain environments, such as those with high levels of corrosive gases, chemicals, or airborne particles, can damage electrical equipment and increase the risk of electrical hazards. Use equipment rated for use in hazardous or corrosive environments and follow proper maintenance procedures to minimize potential risks.
- Space constraints: Limited space around electrical equipment can restrict proper airflow, leading to overheating and reduced performance. Ensure that equipment has adequate clearance for cooling and is not obstructed by other objects or materials.
- Vibration and mechanical stress: Excessive vibration or mechanical stress can cause damage to electrical equipment, such as loose connections or component failures. Ensure that equipment is securely mounted and protected from excessive vibration or stress.
- Lightning and surge protection: Voltage surges caused by lightning strikes or other power disturbances can damage electrical equipment. Implement appropriate surge protection measures, such as surge protectors or lightning arresters, to protect equipment and minimize the risk of damage.
By being aware of environmental factors and taking appropriate precautions, individuals can effectively manage the risks associated with various conditions and maintain a safer work environment when dealing with electrical equipment and systems.
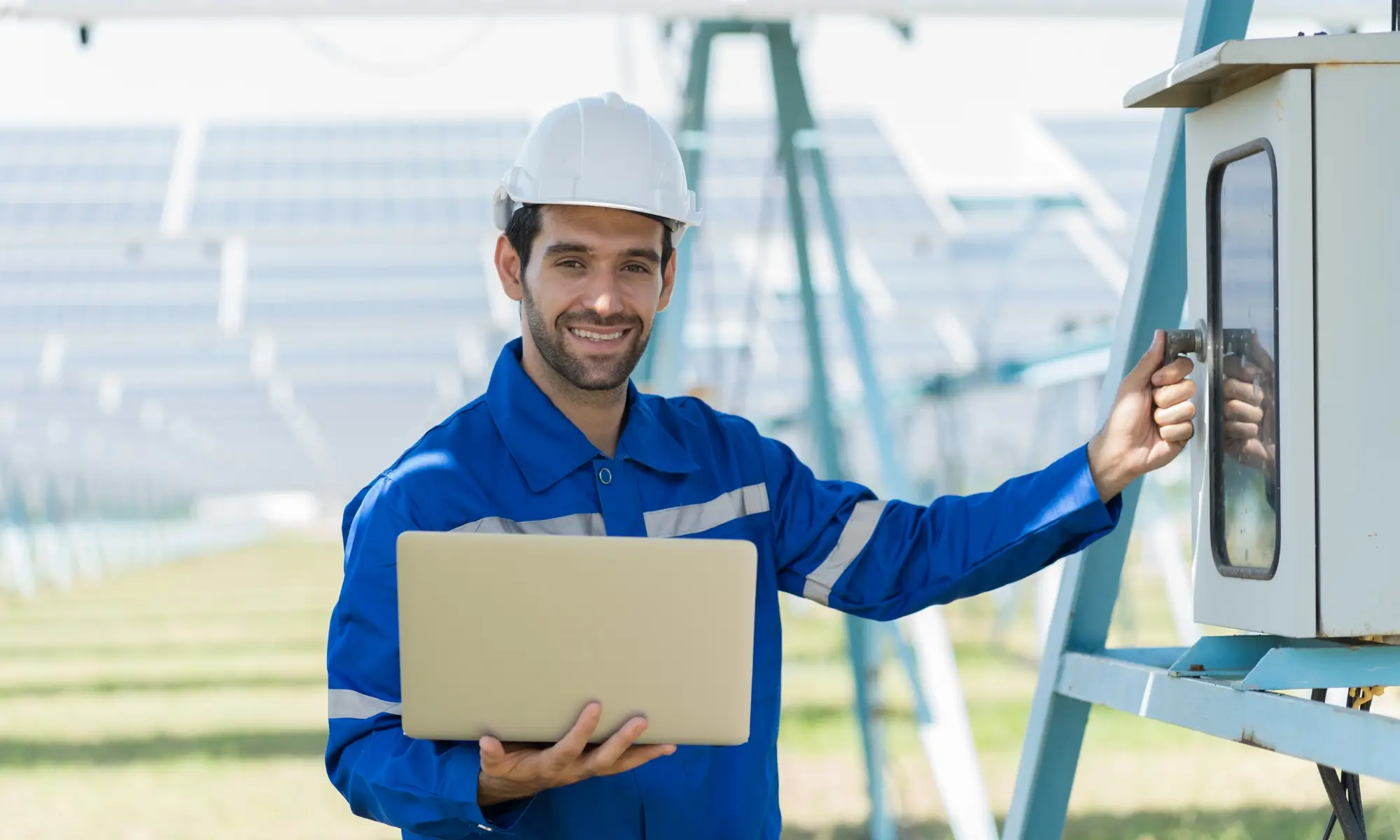
11. Training And Awareness
Effective health and safety training and awareness are essential components of electrical safety, as they equip individuals with the necessary knowledge and skills to work safely with or around electricity. This principle emphasizes the importance of proper education in identifying potential hazards, understanding best practices, and avoiding accidents.
Key aspects of training and awareness include:
- Safety training: Workers who interact with electrical equipment, systems, or devices should receive comprehensive safety training that covers relevant topics, such as the basics of electricity, hazard identification, risk assessment, safe work practices, and personal protective equipment (PPE).
- Regular updates and refreshers: To maintain a high level of electrical safety awareness, training should be updated regularly, and refresher courses provided to ensure workers know the latest safety standards, best practices, and technological advancements.
- Safety culture: Promoting a strong safety culture within an organization encourages employees to prioritize safety, adhere to established procedures, and proactively identify and report potential hazards. This mindset helps create an environment where electrical safety is ingrained in the daily work routine.
- Hazard communication: Clear and effective communication is crucial for electrical safety. This includes the proper labeling of electrical equipment, the use of warning signs, and the sharing of information about potential hazards among team members.
- Emergency response: Training should also cover emergency response procedures in an electrical incident, such as administering first aid, using fire extinguishers, and evacuating the area. This knowledge can be vital in mitigating the consequences of an accident and ensuring the safety of all individuals involved.
By prioritizing training and awareness, organizations can ensure that employees are well-equipped to work safely with electricity, minimize risks, and prevent accidents, thus contributing to a safer work environment.
Conclusion
Understanding and implementing the important principles of electrical safety is essential for ensuring a secure and hazard-free environment when working with or around electricity. By focusing on these key principles, including understanding the basics of electricity, adhering to proper installation and maintenance practices, using appropriate personal protective equipment, and being aware of environmental factors, individuals can significantly reduce the risk of electrical accidents, injuries, and equipment damage.
Creating a culture of electrical safety within your organization requires ongoing training, awareness, and a commitment to best practices. Both employers and employees must take these principles seriously and prioritize safety above all else. By doing so, you can create a safer work environment for everyone involved, protect valuable equipment, and minimize the likelihood of costly and dangerous electrical incidents. Electrical safety is not just a one-time effort but an ongoing responsibility that requires diligence, knowledge, and a proactive approach.