Working near overhead power lines is one of the most common yet underestimated hazards on construction sites, farms, and industrial work zones. While these lines may seem harmless from a distance, they carry extremely high voltage that can cause severe injuries, permanent disability, or even death upon contact—or sometimes even when you’re simply too close.
Unfortunately, many workers and supervisors overlook the invisible dangers of electrical arcs, induced voltage, or energized equipment until it’s too late. The good news? Most incidents involving overhead power lines are entirely preventable with proper awareness, training, and preventive planning.
In this comprehensive guide, we’ll walk you through the top hazards of working near overhead power lines and the 10 most effective safety measures you can implement to protect yourself and your team. Whether you’re a safety officer, construction manager, or field worker, this article will provide practical, real-world insights to reduce risk, stay compliant with OSHA standards, and—most importantly—save lives.
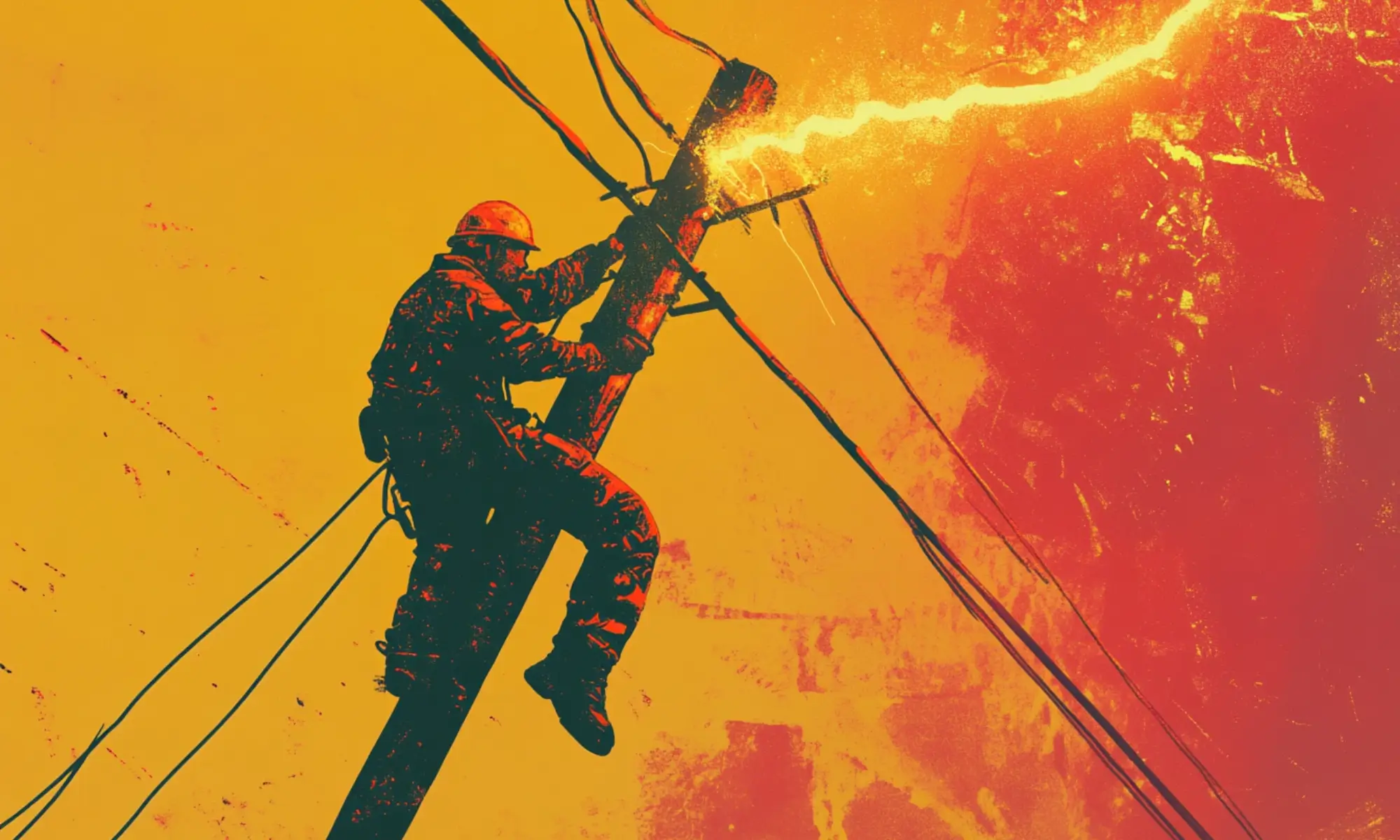
Hazards of Working Near Overhead Power Lines
Overhead power lines pose several hazards, particularly to individuals working near them. Understanding these hazards is crucial to maintaining safety. Some of the main dangers associated with overhead power lines include:
- Electrocution: Direct or indirect contact with a live wire can instantly stop the heart. This is the most immediate and severe hazard.
- Electric Shock: Even if it doesn’t kill, a strong electric shock can cause long-term damage to muscles, nerves, and organs.
- Arc Flashes: Electric arcs can jump through the air to nearby workers or equipment, causing serious burns without any physical contact.
- Thermal Burns: Arcing or fault currents can cause explosive heat, resulting in deep tissue burns.
- Falls from Height: A sudden shock while working on ladders or platforms can lead to dangerous falls.
- Tool or Equipment Contact: Metal ladders, cranes, and boom lifts can become energized if they get too close to overhead lines.
- Downed Lines: Power lines that fall due to storms or equipment contact may remain energized, posing hidden risks.
- Conductor Clashing: High winds or improper work near lines can cause wires to touch, creating sparks or fires.
- Induced Voltage: Nearby equipment or metal objects can become energized through electromagnetic induction, even without touching the lines.
- Lack of Visibility: Power lines often blend into the background, especially during early mornings or foggy conditions, increasing the risk of accidental contact.
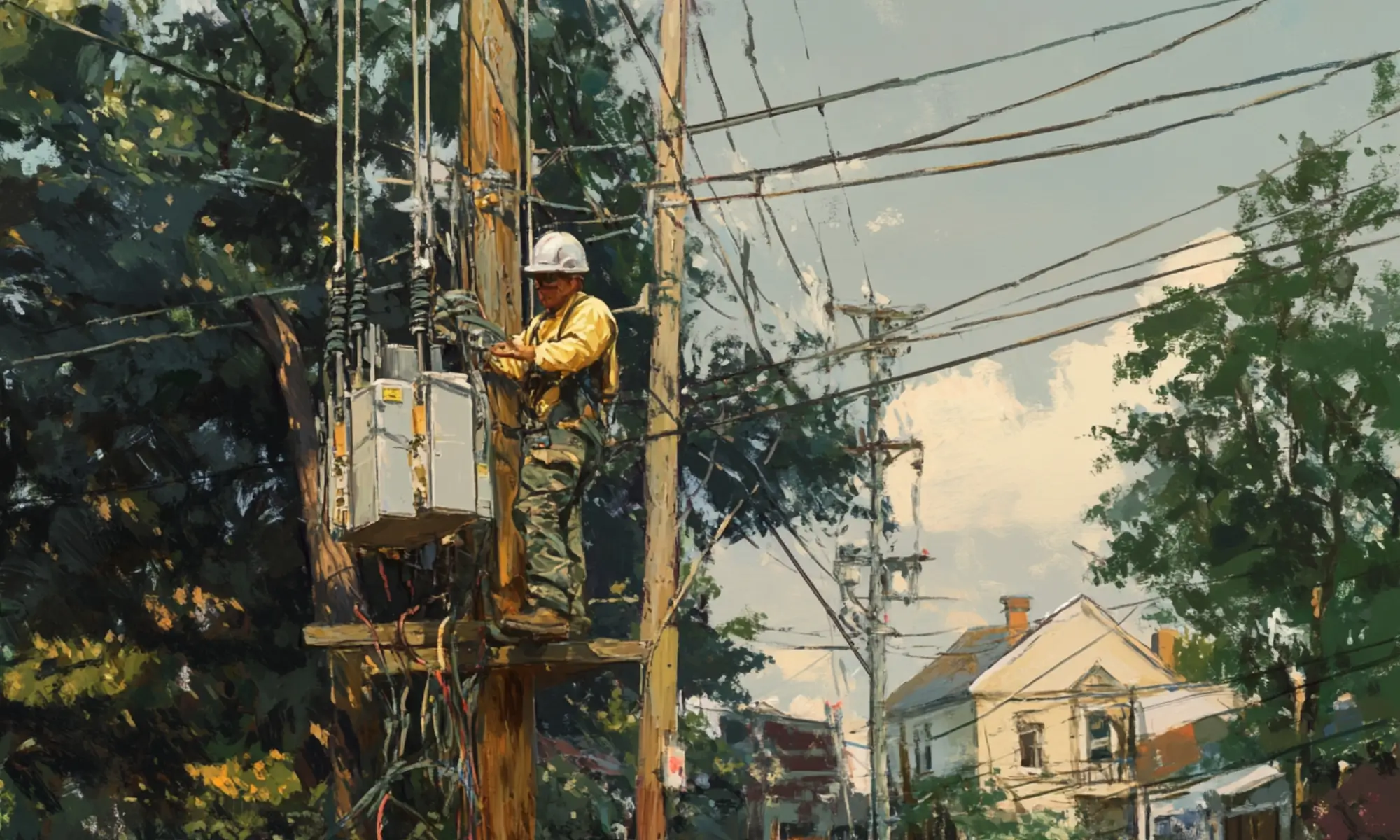
Preventive Measures to Work Safely Near Power Lines
To reduce the risk of these hazards, implement the following preventive strategies:
1. Maintain Safe Clearance
Keeping a minimum distance from power lines is essential. OSHA mandates a minimum of 10 feet (3 meters) from lines carrying up to 50 kV. For higher voltages, greater clearances are required, and safety calculations should be site-specific.
Electricity can arc through the air, causing severe injury or death without direct contact. Adequate clearance protects against this invisible danger.
Key Points:
- Keep at least 10 feet (3 meters) away from power lines (up to 50kV).
- Increase distance for higher voltages.
- Avoid working beneath power lines unless absolutely necessary.
- Never assume lines are de-energized without confirmation.
2. De-Energize and Ground Lines
Before starting work, coordinate with utility providers to de-energize the lines and properly ground them to prevent accidental electrocution.
Even indirect contact with energized lines can be fatal. Grounding and de-energizing eliminate the primary risk.
Key Points:
- Contact the utility company for temporary shutdowns.
- Confirm grounding has been applied by trained personnel.
- Never begin work until a safety clearance has been issued.
- Use lockout/tagout (LOTO) procedures if applicable.
3. Use Non-Conductive Tools
Use fiberglass or treated wood tools instead of metal ones to avoid conduction. This includes ladders, poles, and hand tools used around energized lines.
Metal conducts electricity efficiently. Using non-conductive tools breaks the path that electricity needs to reach the worker.
Key Points:
- Avoid aluminum or steel ladders near power lines.
- Use non-conductive alternatives (e.g., fiberglass).
- Regularly inspect tools for cracks or wear.
- Store non-conductive tools properly to maintain integrity.
4. Inspect the Job Site
Before any task, conduct a site-specific hazard assessment. Identify all power lines, mark them clearly, and assess machinery locations and access points.
Most incidents occur due to unawareness. A thorough inspection helps plan work routes and establish exclusion zones.
Key Points:
- Perform a walk-through before each shift.
- Identify and map all overhead power lines.
- Use warning signs, flagging tape, or barriers.
- Update site maps when conditions change.
5. Train All Workers
Provide workers with training on the hazards of working near power lines, emergency response, and safe equipment handling.
Trained workers are more aware of risks, follow procedures more closely, and are better prepared for emergencies.
Key Points:
- Conduct onboarding and refresher safety training.
- Include electrical hazard awareness in toolbox talks.
- Simulate emergency scenarios for preparedness.
- Emphasize individual responsibility for safety.
6. Wear Protective Equipment (PPE)
Use specialized personal protective equipment (PPE) for electrical work to protect against accidental contact or arc flash injuries. Essential PPE includes:
- Rubber insulating gloves and sleeves
- Dielectric safety boots
- Flame-resistant (FR) and arc-rated clothing
- Hard hats with electrical protection ratings (Class E)
While PPE can’t stop contact from happening, it significantly reduces the severity of injuries and can be life-saving in case of an unexpected incident.
Key Points:
- Always wear PPE rated for the voltage level.
- Inspect PPE for damage before every use.
- Replace worn or expired equipment.
- Train workers on proper PPE use and maintenance.
7. Install Proximity Alarms
Equip cranes, aerial lifts, and other heavy machinery with electronic proximity sensors or boom-mounted alarms to warn operators when getting too close to overhead lines. Visual detection can be unreliable, especially in tight or visually obstructed work zones. Proximity alarms offer a real-time safety buffer.
Key Points:
- Use alarms specifically rated for electrical proximity.
- Calibrate alarms to site-specific distances.
- Combine with physical warning barriers for added safety.
- Ensure operators are trained to respond promptly to alerts.
8. Use Spotters
Assign a trained spotter to assist equipment operators by providing guidance and monitoring proximity to overhead lines. Spotters must have a clear view and maintain constant communication.
Even the most skilled operators can miss hazards in blind spots. A spotter acts as an extra layer of oversight and communication, especially near energized lines.
Key Points:
- Spotters must be trained in electrical safety.
- Use radios or hand signals for communication.
- Spotters should never multitask—this is a full-time role during operation.
- Position them to maintain visibility of all moving equipment.
9. Establish Emergency Procedures
Develop a site-specific emergency response plan that clearly outlines steps in case of:
- Contact with an energized power line
- Electrical shock or burns
- Equipment entanglement with power lines
Conduct regular training and drills to reinforce procedures.
Time and preparedness save lives. Knowing what to do during an emergency reduces panic, speeds up response, and limits injury or damage.
Key Points:
- Post emergency numbers and procedures onsite.
- Train workers to never touch a person or equipment that’s in contact with a line.
- Ensure first-aid kits and AEDs are accessible.
- Conduct emergency drills at least quarterly.
10. Regular Equipment Checks
Before and during operations, inspect all machinery, tools, and equipment for:
- Proper electrical insulation
- Intact grounding systems
- Functional mechanical parts
Daily checks help identify wear, damage, or faults before accidents happen.
Equipment in poor condition may fail during operation, increasing the risk of contact with power lines or causing malfunctions that lead to injury.
Key Points:
- Perform daily pre-use inspections.
- Use checklists to ensure consistency.
- Tag and remove defective tools or machines.
- Schedule periodic professional maintenance.
Conclusion
Working near overhead power lines demands more than just caution—it requires a proactive safety mindset backed by training, planning, and the right protective measures. As we’ve outlined, the risks range from electrocution and arc flashes to falls and equipment failures. But with proper hazard awareness and the implementation of preventive strategies—such as maintaining safe distances, using non-conductive tools, deploying proximity alarms, and establishing emergency procedures—these risks can be significantly reduced.
Safety is not just a checklist; it’s a culture. By staying vigilant and ensuring your team is well-informed and well-equipped, you can create a safer work environment where everyone goes home unharmed.
Make these preventive practices a part of your standard operating procedure—and don’t wait for an incident to take safety seriously. The power to prevent accidents lies in your hands.