In the realm of electrical safety, the role of insulation cannot be overstated. It forms the protective barrier that guards against potential accidents, making it a critical component in designing and operating electrical systems. However, the implications can be far-reaching and devastating when this insulation becomes defective or damaged.
This article thoroughly examines the risks posed by faulty insulation and presents preventive strategies and control measures. By shedding light on these hazards and their solutions, we highlight the importance of meticulous maintenance and monitoring, ultimately contributing to safer and more efficient electrical systems.
Damaged Insulation Or Defective Insulation
Damaged or defective insulation refers to the deterioration or failure of the insulating material used in an electrical system. This insulation is designed to act as a protective barrier that prevents electrical current from leaving the wires or components and coming into contact with other conductors or individuals.
“Damaged Insulation” typically refers to the physical harm the insulation has suffered. This could be due to several factors, such as mechanical stress (bending or pulling the wires), exposure to high temperatures, or being gnawed on by pests like rats or squirrels. Damage could also occur during installation if the insulation is not handled correctly.
“Defective insulation,” on the other hand, often refers to faulty insulation from the beginning due to manufacturing or design errors. It could also refer to insulation that has become ineffective over time. This could be due to aging, exposure to harsh environmental conditions, or loads or voltages beyond its capacity. Certain chemical reactions, moisture, or the presence of corrosive substances could also degrade the insulation over time.
Both damaged and defective insulation poses significant risks, as they can allow electricity to escape, leading to potential electrical shock, fire hazards, and other safety issues. Hence, regular inspection and maintenance of electrical systems are essential to detect and rectify any insulation faults as early as possible.
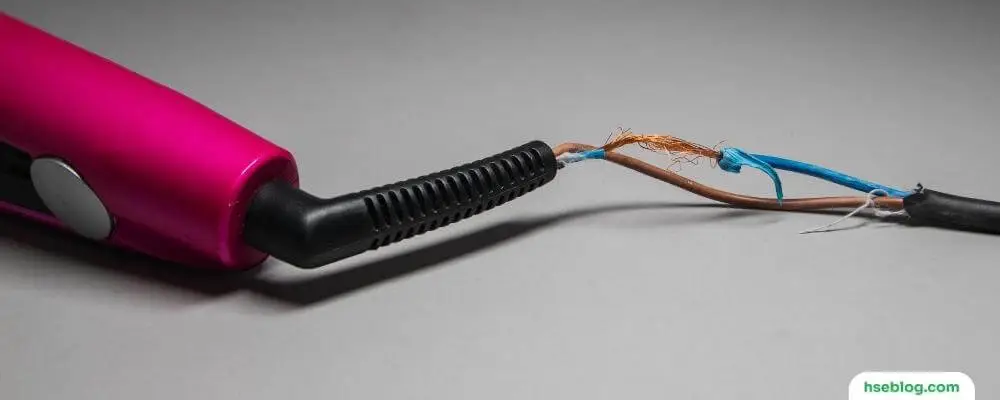
Defective Insulation Hazards and Control Measures
Defective insulation can pose various hazards, depending on the type of insulation and its location. Here are some common hazards associated with defective insulation and the control measures to mitigate those risks:
1. The threat of Electrical Shock
Defective insulation creates a severe hazard for electrical shock. An electrical shock occurs when an individual comes into contact with an exposed, live electrical wire or component, allowing the electrical current to pass through the body. The consequences can range from minor discomfort to severe injuries or even death, depending on the intensity of the current. Defective insulation can expose these wires or parts, greatly increasing the risk of a shock.
Proper insulation is a barrier, preventing the current from leaving the system. Hence, high-quality insulation must be used during the installation and maintenance of electrical systems. Moreover, even if a part of the system is not readily visible, regular inspections should be conducted to identify any signs of wear or tear or damage to the insulation, which could potentially expose live parts.
2. Possibility of Fire Outbreak
The threat of fire is another critical concern associated with faulty insulation. When electrical wires or parts are exposed, there’s a higher chance of electrical arcs, essentially electrical currents, that pass through the air from one conductor to another. These arcs can produce extreme temperatures and sparks, igniting nearby flammable materials and leading to fires, resulting in extensive property damage and potential loss of life.
Therefore, to mitigate this risk, any wiring not enclosed in insulation should be routinely checked for any deterioration or damage. Furthermore, regular inspections of outlets and appliances should be carried out to verify that proper insulation is employed, reducing the risk of arcing.
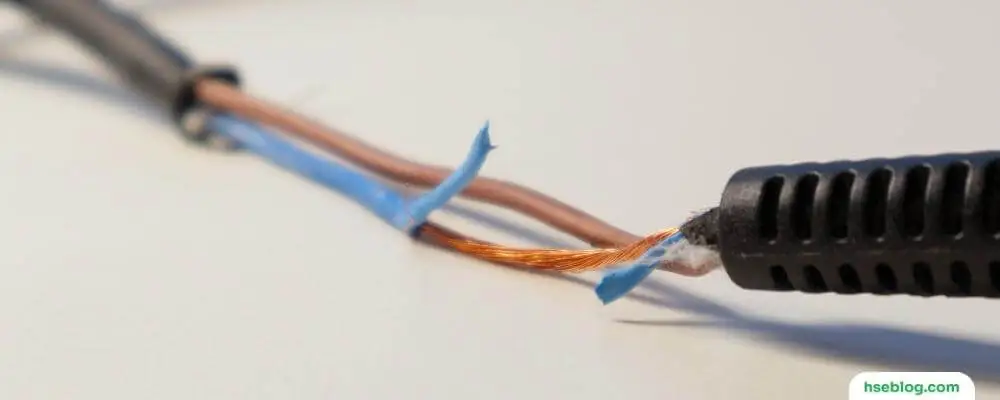
3. Threat to Equipment Integrity
Defective insulation can damage equipment, primarily caused by increased resistance and current leakage. These leaks can lead to an electrical system overload, overheating and potential damage to the electronic components. This not only disrupts the operation of the device but also poses a fire hazard.
It is crucial, therefore, to use proper insulation when installing and maintaining electrical systems to maintain the integrity and longevity of the equipment. Regular checks for any wear or damage that could lead to current leakage are also important, even in system parts that might not be immediately visible or accessible.
4. Risks of Arcing and Short-Circuiting
Defective insulation can also lead to arcing and short-circuiting, both detrimental to the safe operation of electrical systems. As mentioned earlier, arcing occurs when an electrical current jumps through the air from one conductor to another, creating a spark that can generate heat, potentially damage nearby objects, or even cause a fire.
On the other hand, short-circuiting is an electrical malfunction where two wires connect directly, allowing an uncontrolled flow of current from one wire to another. This can lead to various problems, including equipment damage, electrical shocks, and fires. To prevent these issues, it is necessary to ensure that all wiring is properly insulated and checked regularly for signs of wear and damage, reducing the chances of these dangerous events occurring.
5. Deterioration of Insulation Material
Insulation material can degrade over time due to various factors such as temperature fluctuations, humidity, corrosive substances, and mechanical stress. This degradation can lead to a loss of insulation properties, increasing the risk of electrical shock, equipment damage, and fire hazards. Control measures should include using high-quality insulation material suitable for specific environmental conditions. Regular inspections should be conducted to check for any signs of degradation or damage. If any insulation is deteriorating, it should be replaced promptly to maintain the electrical system’s safety.
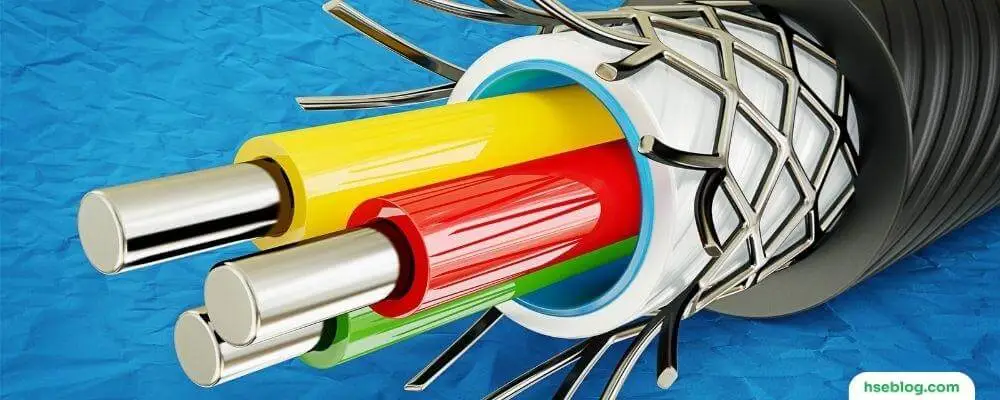
6. Impact on Energy Efficiency
Defective insulation can also lead to increased energy consumption. Electrical systems with defective insulation are less energy efficient because of the current loss due to leakage. This contributes to higher energy bills and hurts the environment due to increased carbon emissions. Implementing energy audits and regular maintenance checks can help identify and rectify defective insulation. Using energy-efficient materials and practices during installation can also help mitigate this risk.
7. Health Hazards from Defective Insulation
If damaged or improperly handled, certain insulation materials can pose health risks. For example, once widely used for its fire-resistant and insulating properties, asbestos can cause serious health problems if its fibers are inhaled. Properly handling, replacing, and disposing of these materials is crucial. It is also advisable to use safer insulation materials where possible. Protective gear should be worn when dealing with potentially harmful insulation materials, and all related work should be done according to safety regulations and guidelines.
8. Unintended Electromagnetic Interference
Insulation defects can lead to the creation of electromagnetic fields around faulty equipment. These fields can interfere with the functioning of other sensitive electronic devices in the vicinity. Control measures should include regular inspections and maintenance to ensure the insulation is in good condition. Shielding or moving sensitive devices away from sources of interference might also be necessary.
These are just some of the dangers associated with defective electrical insulation. Taking the necessary steps to protect yourself and your property from these hazards is important. Inspecting and maintaining electrical systems can help ensure they remain safe and reliable for years.
By following these simple tips, you can ensure that your electrical insulation is always in good condition, keeping you safe and your system running smoothly. Contact a qualified electrician in your area for more information on electrical insulation. They will be able to provide valuable insights into the safety of your electrical systems.
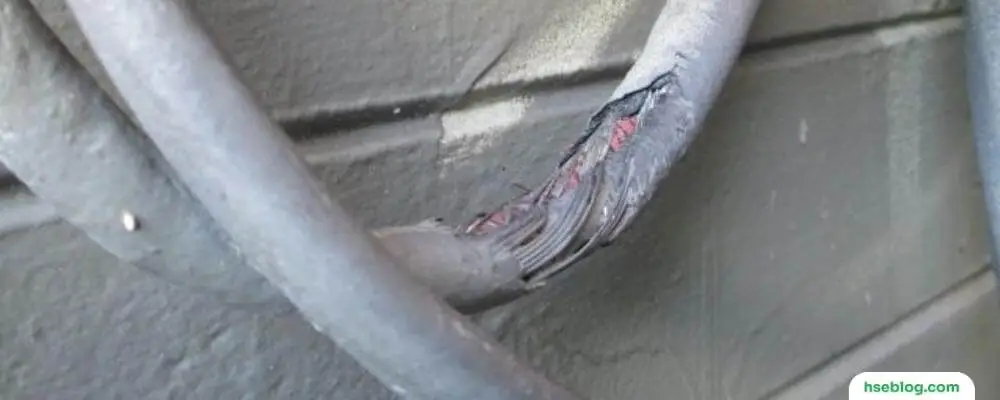
Additional Control Measures
Workers and employers must comply with OSHA Standard 29 CFR 1910 Subpart S – Electrical. Electricity is used daily, and if uncontrolled or misused, it can severely burn, injure, kill you, or cause fires with devastating results. However, most electrical faults can be seen by visual inspection.
- Ensure electrical equipment is suitable for the working environment (especially if it is or could be wet, corrosive, flammable, or subject to impact damage).
- Connect all equipment to fixed sockets, where possible.
- Ensure that all socket circuits are protected by a Residual Current Device (RCD).
- Test the RCD regularly.
- Avoid the use of extension leads and multiple adaptors.
- Never swap equipment leads between devices.
- Have a recorded inspection and maintenance program for all electrical equipment.
- Train staff to inspect visually for damage (such as exposed wires and scorching on plugs, leads, and cables) and report faults.
- Take faulty equipment out of use immediately until repaired. Clearly label it as faulty or remove the plug to prevent use.
- Never clean or adjust appliances when the power is switched on.
- Never touch light switches or appliances with wet hands.
Wear and Tear
Normal and regular use of electrical equipment can cause wear and tear, resulting in insulation breaks, short circuits, and exposed wires. Essential safety requirements include:
- All electrical cords should have enough insulation to prevent direct contact with wires. Checking all cords before each use is particularly important since corrosive chemicals or solvents may erode the insulation.
- Damaged cords should be repaired or removed, especially in wet environments such as cold rooms and near water baths.
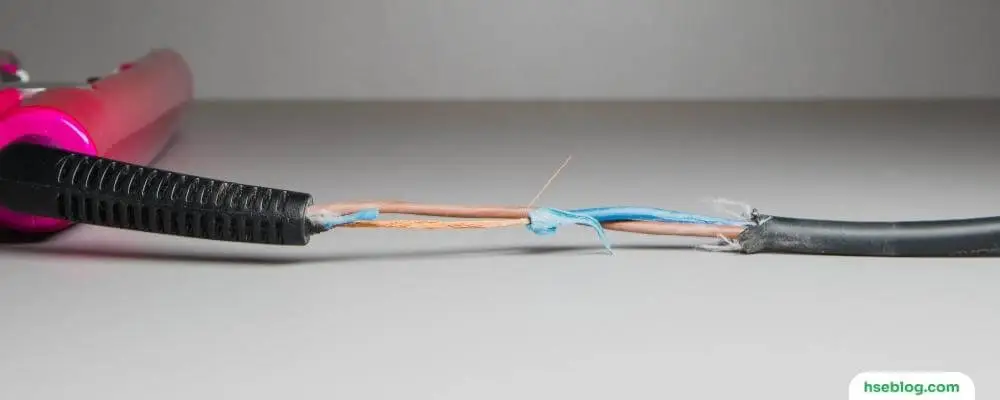
Taking Equipment Out of Service
Any of the following circumstances require that the user immediately take the equipment out of service:
- Experiencing shocks, even mild shocks, upon contact
- Abnormal heat generation
- Arcing, sparking, or smoking from the equipment
Workers must label the equipment “Do Not Use” and should arrange for equipment repair either through the equipment manufacturer or through their department support as appropriate.
Having the right boots is essential if you work outdoors in extreme weather. Electrically insulated boots protect your feet from electrical shock and provide extra warmth. Look for boots designed to keep your feet warm in cold temperatures while protecting them from electric shocks. Boots for extreme weather should also be waterproof and provide good insulation against cold and moisture. Ensure your boots have a slip-resistant sole to keep you safe on slick surfaces. With these features in your boots, you will be able to confidently tackle any job in extreme weather conditions, knowing that your feet are protected.
Conclusion
In conclusion, the potential hazards of defective electrical system insulation vary significantly. They include severe threats like electrical shocks, fire outbreaks, equipment damage, energy inefficiency, and health risks. It’s imperative for everyone involved in the design, installation, and maintenance of electrical systems to be aware of these hazards and actively implement measures to control them.
These measures include using high-quality insulation material, conducting regular inspections and maintenance, ensuring energy-efficient practices, and adhering to safety regulations and guidelines. Proactive management and preventive measures can significantly reduce the risks associated with defective insulation, fostering safer and more reliable electrical systems.