Certain roles stand out for their criticality and precision in the intricate world of construction, industrial setups, and various specialized sectors. One such pivotal role is that of a ‘rigger.’ This term may not be commonplace for many, but its importance cannot be understated in numerous industries. Rigging is both an art and a science, demanding keen attention to detail, extensive technical know-how, and a steadfast commitment to safety.
In this comprehensive guide, we delve deep into the realm of rigging, shedding light on the multifaceted responsibilities of a rigger, the prerequisites to stepping into this field, and the stringent safety protocols that are imperative to this profession. Whether considering a career as a rigger or merely wanting to understand its nuances, this blog will serve as your detailed roadmap. Join us as we unravel the intricacies of the rigger’s world.
What Is Rigger? Definition
A rigger is a professional who assembles, installs and maintains cables, pulleys, winches, and other equipment to hoist or move heavy loads. They operate in various industries, including construction, oil and gas, and shipping, where they ensure that the lifting and movement of materials are conducted safely and efficiently. Rigging requires technical knowledge, attention to detail, and adherence to safety procedures to prevent accidents and damage to materials or equipment.
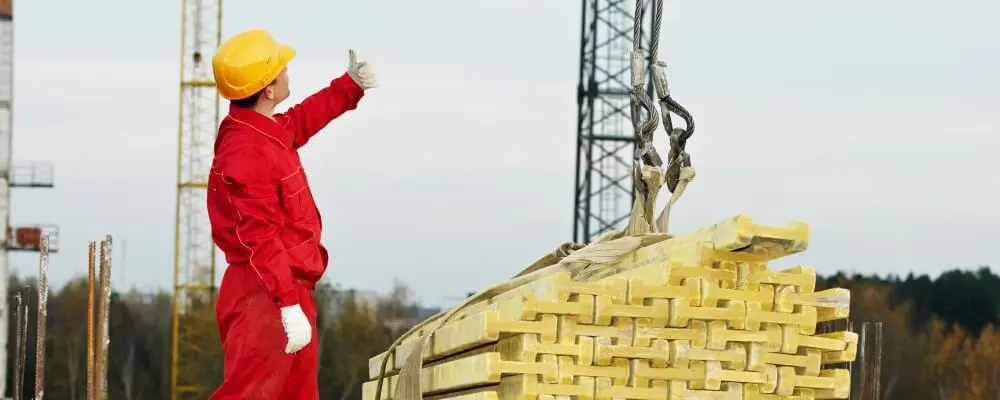
Roles And Responsibilities Of Rigger
The roles and responsibilities of a rigger can vary depending on the specific industry and context in which they work. However, here are some common roles and responsibilities of a rigger:
1. Equipment Handling and Setup
Rigging predominantly revolves around manipulating and utilizing heavy-duty equipment to lift or shift substantial items. This involves intricate knowledge of tools such as pulleys, winches, and cranes. Understanding these devices’ mechanics and operation is crucial for a rigger.
Properly setting up this machinery ensures that the construction or work site operations run without hitches. Any oversight in the setup can lead to inefficiencies, which can sometimes result in severe consequences, including potential damage or safety hazards.
2. Load Assessment and Preparation
Before lifting begins, a rigger meticulously inspects the objects to be moved. This evaluation is not just about weight but also encompasses the load’s shape, balance, and other physical properties. Proper preparation often involves securing the load with ropes, chains, or slings, ensuring no undesirable shift or imbalance during the lifting process.
Proper load assessment is the cornerstone of preventing accidents, as an improperly secured load can become unsteady or fall, posing risks to the personnel and the infrastructure.
3. Equipment Selection
The rigging world has many tools and machinery designed for specific tasks. Depending on the load’s weight, size, and nature, the rigger has to select the most suitable equipment judiciously. This might mean opting for a particular type of cable that has the strength to handle a specific weight or choosing a pulley that’s ideal for the task at hand. Incorrect equipment selection can not only be inefficient but also potentially dangerous.
4. Risk Assessment
The environments where riggers operate, like construction sites or shipping docks, are replete with potential hazards, especially when dealing with heavy machinery and loads. There’s an art and science to gauging the risks associated with each task.
For instance, moving a large piece of equipment through a confined space demands extensive planning. Riggers must anticipate challenges, from environmental factors to equipment limitations, and craft strategies to navigate these risks effectively.
5. Adherence to Safety Procedures
The rigging profession places a premium on safety. Ensuring the well-being of everyone on-site is paramount. Rigging operations often need to adhere to a stringent set of safety guidelines, which might be mandated by local or state laws or set internally by the company.
Riggers undergo training to familiarize themselves with these protocols, ensuring every operation, from the simplest to the most complex, adheres to these safety standards.
6. Team Collaboration
The role of a rigger is intrinsically collaborative. They seldom work in isolation. Instead, they are part of a larger operational framework, often collaborating with construction crews, engineers, and other specialists. Seamless communication and coordination with these teams ensure that lifting and moving operations integrate smoothly with other concurrent tasks. This synergy is vital to prevent mishaps and ensure timely project completion.
7. Equipment Maintenance and Storage
The post-operation phase in rigging is as crucial as the setup and operation phases. Once a task is complete, the rigger ensures all equipment returns to its pristine state. This involves cleaning to remove any operational residues, checking for wear and tear, and performing necessary repairs.
Proper maintenance ensures the longevity of the equipment, saving costs in the long run. Additionally, safely storing equipment ensures it’s readily available and in optimal condition for future tasks.
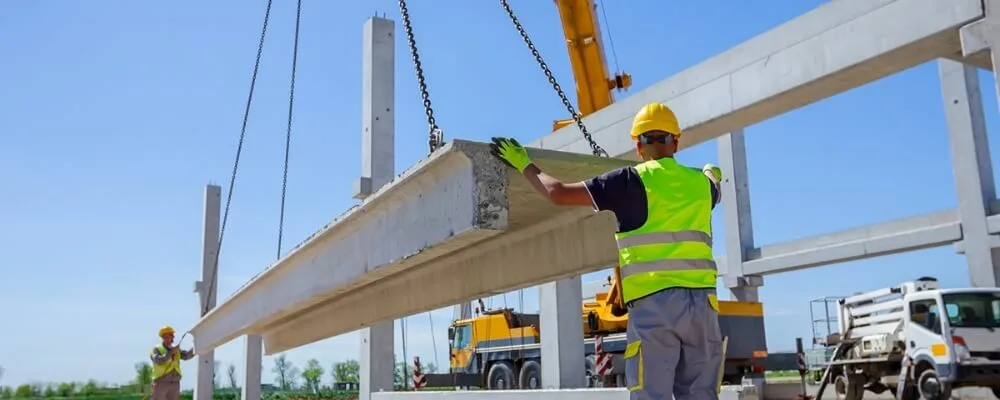
Requirements to Become a Rigger
Becoming a rigger typically involves a combination of formal education, training, and practical experience. The specific requirements can vary depending on the industry and location, but here are some general steps and requirements to become a rigger:
1. Educational Foundation
Starting with a basic educational background, such as completing Class 8 or Class 10, provides an aspirant with foundational knowledge. While not always mandatory, this education level offers benefits in understanding basic concepts and can serve as a stepping stone for advanced courses and training.
2. Industry Selection
Deciding on a specific industry can greatly influence a rigger’s career trajectory. Industries like construction, manufacturing, oil, and mining have varied demands and challenges. It’s essential to understand the nuances of the chosen field, including its physical demands and specific skills required. For instance, the physical robustness needed for a construction site might differ from that required on an oil rig.
3. Vocational Training
Vocational training is pivotal to bridging the gap between basic education and the specialized skills required in rigging. Institutions like the Industrial Training Institute (ITI) offer courses tailored for aspiring riggers. These courses, often provided by the Ministry of Skill Development And Entrepreneurship in countries like India, arm individuals with practical knowledge in sectors ranging from construction to electronics. Such training provides theoretical understanding and hands-on experience, making transitioning into a full-time rigging job easier.
4. On-the-Job Experience
Entering the field and gaining hands-on experience is a crucial step. Once initial training is complete, seeking internships or entry-level positions allows individuals to learn the intricacies of rigging under the guidance of seasoned professionals. This phase is essential for mastering the trade, understanding safety protocols, and becoming familiar with the equipment used in the industry.
5. Career Advancement
With experience comes the opportunity for growth. As riggers spend more time in the field, they can pursue advanced roles. Positions like a master rigger or rigging equipment inspector become attainable. These roles often come with added responsibilities, including supervising operations, ensuring adherence to quality standards, and training newcomers to the field.
In summary, to become a rigger, one should start with a foundational education, choose an industry, undergo vocational training, gain practical experience, and seek career advancement opportunities. Each step equips them with the necessary skills and expertise to excel in rigging.
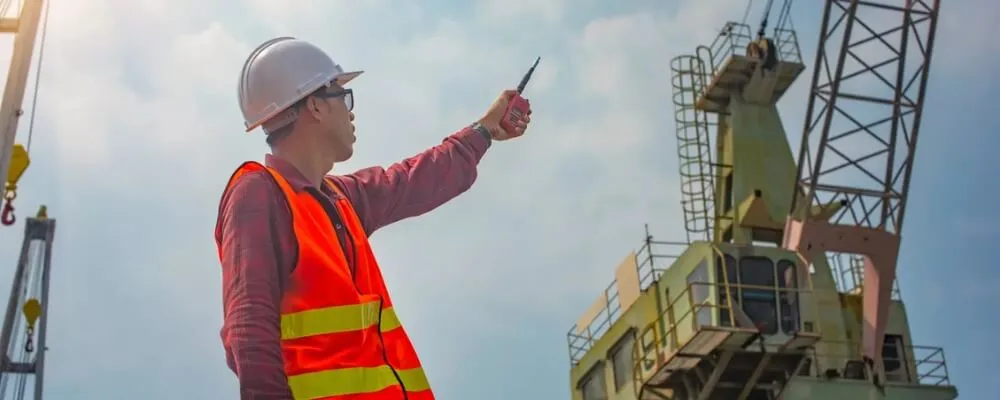
Skills Requirements Of A Rigger
Becoming a skilled rigger requires a combination of technical expertise, practical knowledge, and a strong commitment to safety. Here are some of the essential skill requirements for a rigger:
1. Communication Proficiency
Rigging operations demand clear and concise communication. Given the potential dangers of lifting heavy materials, riggers must be adept at providing explicit instructions and ensuring all team members are on the same page. This is crucial for coordinating operations and ensuring safety.
2. Equipment Maintenance Knowledge
Rigging machinery and tools require regular upkeep to function optimally. Riggers should be proficient in understanding the machinery’s intricacies, recognizing when maintenance is due, and performing necessary upkeep to prevent malfunctions during critical operations.
3. Reading and Writing Competence
Riggers often interact with labels, charts, and operation manuals. Thus, they must be able to read, comprehend, and sometimes document information. This might also involve drafting incident reports or jotting down key operational details, ensuring clarity for all stakeholders.
4. Technical Expertise
The essence of rigging lies in manipulating heavy machinery and equipment. Riggers need a robust understanding of machinery design, usage, repair, and maintenance. Additionally, interpreting plans, blueprints, and models is essential for executing tasks accurately.
5. Attention to Detail
Precision is paramount in rigging. The slightest oversight can lead to significant consequences, from equipment damage to safety hazards. Riggers should possess a keen eye for detail, ensuring that every aspect of the operation—from equipment setup to the actual lifting process—is carried out meticulously.
6. Risk Assessment Ability
Every rigging operation comes with its set of potential risks. Rigging professionals must identify these risks, understand their implications, and devise strategies to mitigate them effectively.
7. Physical Fitness
Rigging often demands physical exertion, from handling equipment to performing manual tasks. As such, riggers should be in good physical condition, ensuring they can manage the job’s demands without compromising their well-being.
8. Teamwork and Collaboration
Rigging is seldom a solitary endeavor. Riggers often work in teams, collaborating with other professionals, such as crane operators, construction workers, and engineers. Being a good team player and understanding how to coordinate effectively with others is crucial for the job’s success.
9. Problem-Solving Skills
Unforeseen challenges are a given in the rigging world. Riggers should be adept problem solvers, able to think on their feet and devise solutions when faced with unexpected issues, ensuring operations remain smooth and safe.
A rigger’s role is multifaceted, demanding a blend of technical knowledge, physical prowess, and soft skills. Mastery of these skills ensures not only the efficient execution of tasks but also the safety and well-being of all involved.
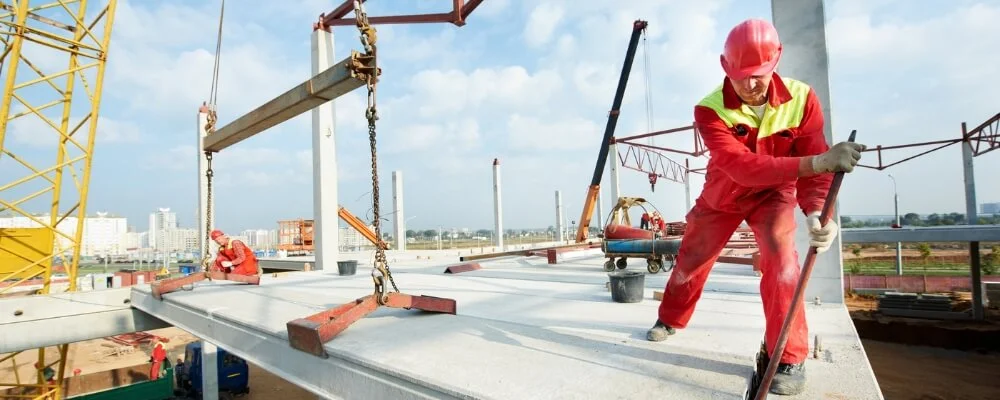
Safety Rules A Rigger Should Follow At Work
Proper Training: Before undertaking any rigging task, ensure you have undergone the appropriate training for the equipment and procedures involved. Knowledge is the first step to safety.
- Equipment Inspection: Before use, always inspect rigging equipment for any signs of wear, damage, or malfunction. This includes ropes, slings, hooks, and other hardware.
- Use Appropriate Gear: Wear the necessary personal protective equipment for the task, such as helmets, gloves, safety boots, and high-visibility vests.
- Clear Communication: Always maintain clear lines of communication with all team members. Standard hand signals, radios, or other communication tools can help prevent misunderstandings and accidents.
- Load Weight Verification: Ensure the load’s weight and the rigging equipment’s capacity match. Never exceed the weight limit of any piece of rigging equipment.
- Stable Footing: Always ensure a stable footing, especially when working at heights or on unstable surfaces. This might mean using non-slip shoes or setting up platforms.
- Secure the Load: Ensure the load is balanced and securely fastened before lifting. It’s essential to prevent load shifts during movement.
- Maintain a Safe Distance: Keep unnecessary personnel away from the lifting area. When lifting is in progress, ensure a clear zone where the load travels.
- Avoid Working Under Loads: Never stand or walk under suspended loads. Even with precautions, there’s always a risk of the load falling.
- Stay Updated with Weather Conditions: Outdoor rigging operations can be affected by weather conditions. High winds, rain, or lightning can make rigging operations dangerous. Always be aware and consider halting operations in adverse conditions.
- Regularly Maintain Equipment: Periodic checks and equipment maintenance ensure that wear and tear do not lead to malfunctions. Replace any gear that shows signs of degradation.
- Plan for Emergencies: Have an emergency response plan in place. This should include procedures for accidents, equipment failures, or other unforeseen events.
- Avoid Distractions: Stay focused on the task at hand. Avoid using mobile phones or engaging in unrelated activities while rigging operations are ongoing.
- Respect Load-bearing Points: Ensure that the load’s weight is distributed appropriately. Avoid overloading specific points or using equipment not designed for the load’s weight or nature.
- Continuous Learning: The rigging world is always evolving, with new techniques, equipment, and standards emerging. Stay updated with the latest best practices in the industry.
By adhering to these safety rules, riggers protect themselves and ensure their colleagues’ well-being and the integrity of the equipment and materials they handle. Rigging operations are intricate, and even minor oversights can lead to significant hazards. Therefore, a consistent emphasis on safety is crucial.
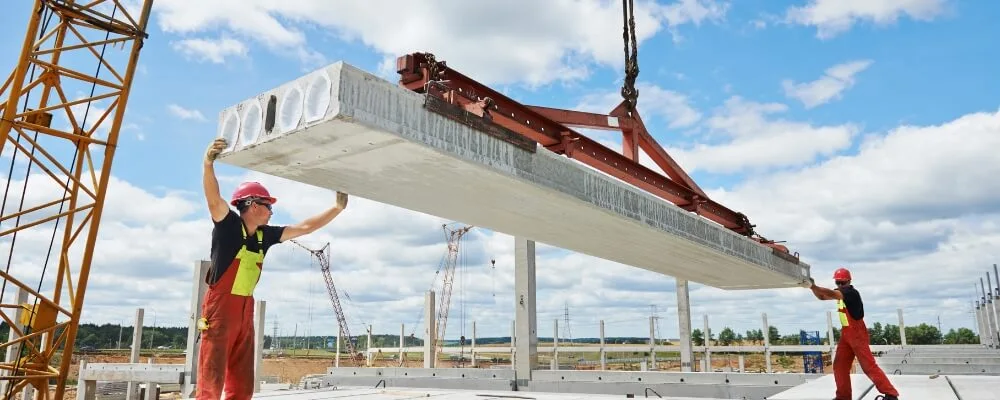
Where Do Riggers Work?
Riggers find themselves in diverse working environments tailored to the specific tasks they are designated to perform. These professionals have various employment avenues, from venturing into self-employment and taking up contractual gigs to securing permanent roles in large industrial establishments. The nature of their job often requires adaptability, with some riggers frequently relocating based on contract work, especially if they collaborate with contractors. In contrast, those associated with industrial factories or established organizations generally enjoy a more stationary work life.
Given the versatility of their skill set, riggers are also in demand in specialized sectors like the oil and mining industries. Riggers play a pivotal role in drilling operations in the oil and gas sector. They are responsible for handling various machinery essential for drilling and continuously monitoring the drilling rig’s functions to ensure optimal performance and safety.
The maritime sector offers another domain where riggers’ expertise is invaluable. Marine riggers specialize in maintaining, installing, and repairing essential maritime equipment. This includes but is not limited to, ropes, cables, winches, and pulleys crucial for ship operations.
In summary, the rigging world offers a dynamic and varied work environment, with opportunities across industries, each demanding unique skills and expertise tailored to the job.
Conclusion
The role of a rigger, often operating behind the scenes, remains an indispensable pillar in numerous industries, from construction to maritime endeavors. As we’ve explored, the rigger’s responsibilities are vast and crucial, ensuring that heavy loads are moved safely and efficiently. While the pathway to becoming a rigger requires specific training and an understanding of industry requirements, the emphasis on safety remains paramount, safeguarding both the rigger and those around them. Ultimately, the rigger epitomizes the fusion of skill, knowledge, and unwavering attention to detail.
As industries continue to evolve and expand, the demand for proficient riggers will persist, emphasizing the enduring importance of their role in shaping our built environment and ensuring the safety of complex operations. Whether you’re an industry professional or intrigued by the mechanics of the world around you, understanding the essence of rigging provides a fresh perspective on the gears that keep our world turning.