In engineering and material handling, understanding key terms like Safe Working Load (SWL) and Working Load Limit (WLL) is essential to ensure safety, efficiency, and compliance with best practices. Whether you’re a seasoned engineer, a safety officer, or new to the industry, getting a firm grasp on these concepts will greatly contribute to a safer working environment.
SWL and WLL are not just industry jargon; they define the maximum load lifting equipment can safely handle. Over time, the usage of these terms has evolved, and their interpretation varies across different international standards. In this blog post, we aim to clarify these crucial terms, delving into their definitions, calculations, and implications and highlighting their differences.
What exactly do SWL and WLL mean? How are they calculated? What distinguishes them from each other, and are they interchangeable? This post will answer all these questions and more. So, let’s unpack these terms and understand how a subtle change in terminology can significantly influence the interpretation and application of safety standards.
What is Safe Working Load (SWL)?
Safe Working Load (SWL), sometimes also referred to as Normal Working Load (NWL), is the maximum force or load that a piece of lifting equipment, such as a crane, winch, hoist, or an accessory, can safely handle without the risk of failure or breaking.
SWL is determined by the equipment manufacturer and is calculated based on the Minimum Breaking Strength (MBS) or Minimum Breaking Load (MBL), which is the lowest load that would cause the piece of equipment to fail or break under force. This MBS is then divided by a safety factor to determine the SWL.
The safety factor is a number that’s typically between 4 to 6 and is chosen based on the type of equipment, its intended use, and the potential risks associated with equipment failure. In some cases where the risk of equipment failure could harm people, the safety factor may be as high as 10.
In the formula form:
SWL = MBS / Safety Factor
SWL aims to ensure safety in operations that involve lifting heavy objects. It provides a guideline for operators, helping them understand the limits of their equipment and preventing situations where the equipment is overloaded, which could lead to equipment failure and potentially serious accidents or damage.
Please note that it’s crucial not to exceed the SWL of a piece of lifting equipment. Even if the equipment seems to be handling a load heavier than its SWL, that does not mean it’s safe or advisable to continue operating in that way. Overloading equipment can cause wear and tear, reduce the lifespan of the equipment, and increase the risk of unexpected failure.
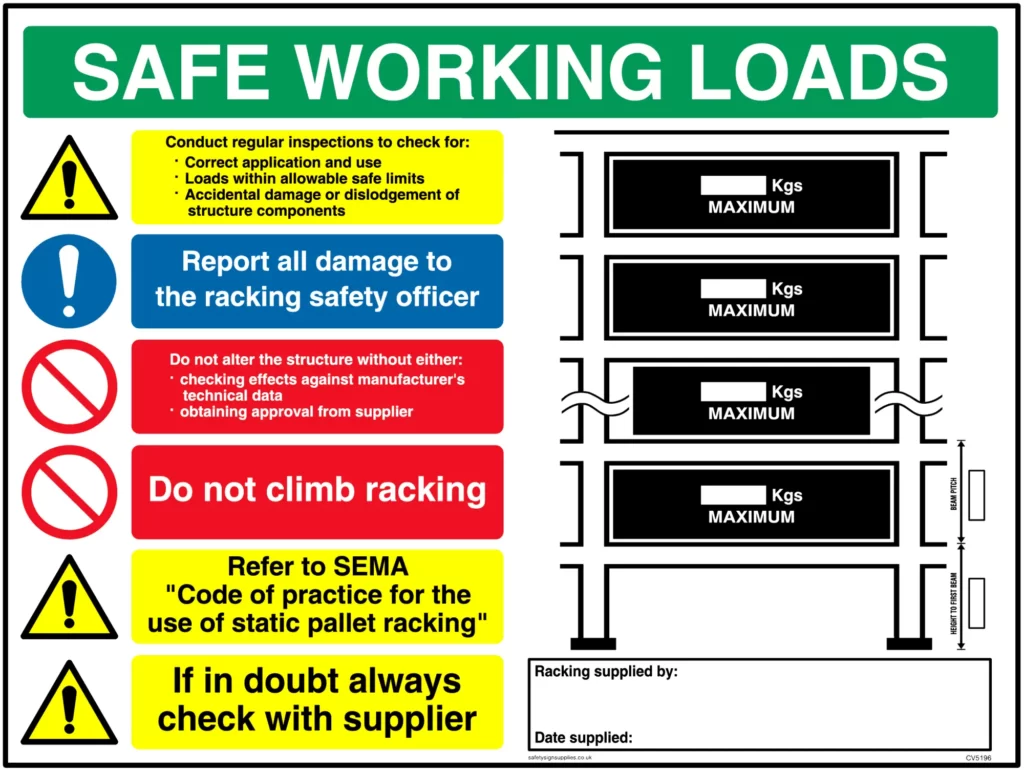
What is Working Load Limit (WLL)?
The Working Load Limit (WLL) is the maximum load a piece of lifting equipment, such as a crane, hoist, sling, chain, or any other lifting device, can handle under normal service conditions. This limit is set by the manufacturer based on rigorous testing and should not be exceeded to ensure the safe operation of the equipment.
Like the Safe Working Load (SWL), the WLL is derived from the Minimum Breaking Strength (MBS) or Minimum Breaking Load (MBL) of the equipment, divided by a safety factor. The safety factor varies depending on the type of equipment and its intended use, but generally ranges between 4 to 6, and can go up to 10 in cases where the failure of the equipment could pose a risk to human life.
In simple mathematical terms:
WLL = MBS / Safety Factor
WLL is crucial in construction, shipping, and any industry where lifting and moving heavy loads is a regular part of operations. It ensures the safe use of lifting equipment, helping to prevent equipment failure, accidents, and potential injuries.
It’s important to note that the WLL can change based on the configuration of the lifting equipment. For example, the angle at which a sling or chain can affect its WLL. Therefore, all components in a lifting configuration, including hooks, shackles, and slings, should have a WLL suitable for the lift load.
In many regions, it’s a legal requirement to clearly mark the WLL on lifting equipment, and it’s also recommended that regular inspections are carried out to ensure equipment is in good condition and safe to use.
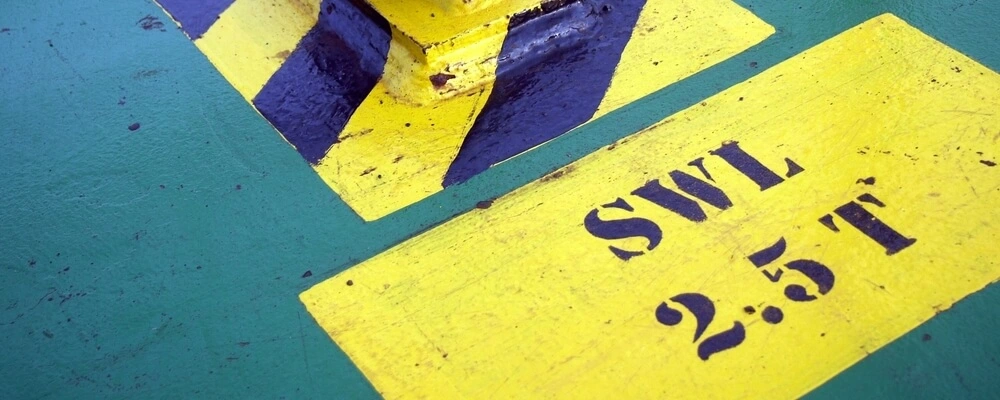
Difference Between Safe Working Load (SWL) and Working Load Limit (WLL)
Safe Working Load (SWL) and Working Load Limit (WLL) are used in engineering and material handling fields to denote the maximum capacity equipment or hardware can safely handle. While they have been used interchangeably in some contexts, they have distinct meanings in different regions and standards. Here’s a brief explanation of the differences:
- SWL, or Safe Working Load, is an older term that indicates the maximum weight or force that equipment or machinery could safely handle. The maximum load can be applied to a component or equipment without causing deformation or failure. The term is calculated as the Minimum Breaking Load (MBL) or Minimum Breaking Strength (MBS) divided by a safety factor, which typically ranges from 4 to 6.
- WLL, or Working Load Limit, is a term that has largely replaced SWL in the United States, European, and ISO standards due to the more specific and legally clear nature of its definition. The WLL is the maximum mass or force a product can support in general service when the pull is applied inline.
In terms of practical usage, both define the same concept — the maximum safe load a piece of lifting equipment can handle. However, the shift from SWL to WLL has been due to an attempt to provide more specificity and clarity in safety regulations and to avoid potential legal implications associated with the term “safe.”
It’s important to note that these terms provide a guideline for safe operation, and loads should not exceed these limits. Proper training, inspection, and maintenance of lifting equipment are essential in ensuring safe operations.