In any successful organization, consistency isn’t just helpful—it’s essential. Whether you’re running a manufacturing line, managing a hospital, or operating a small business, ensuring that tasks are performed the same way every time can mean the difference between efficiency and chaos. That’s where SOPs come in.
SOP, or Standard Operating Procedure, is more than just a checklist—it’s a comprehensive guide that defines how specific tasks should be done to maintain quality, safety, and compliance. From onboarding employees to handling hazardous materials, SOPs are the unsung heroes behind smooth operations across industries.
In this detailed guide, we’ll explore what an SOP really is, why it’s so important, and how to write one that actually works. You’ll also discover the different types of SOPs, key components that make them effective, and real-world examples that bring everything together. Whether you’re creating your first SOP or refining an existing one, this resource will help you create procedures that are clear, compliant, and easy to follow.
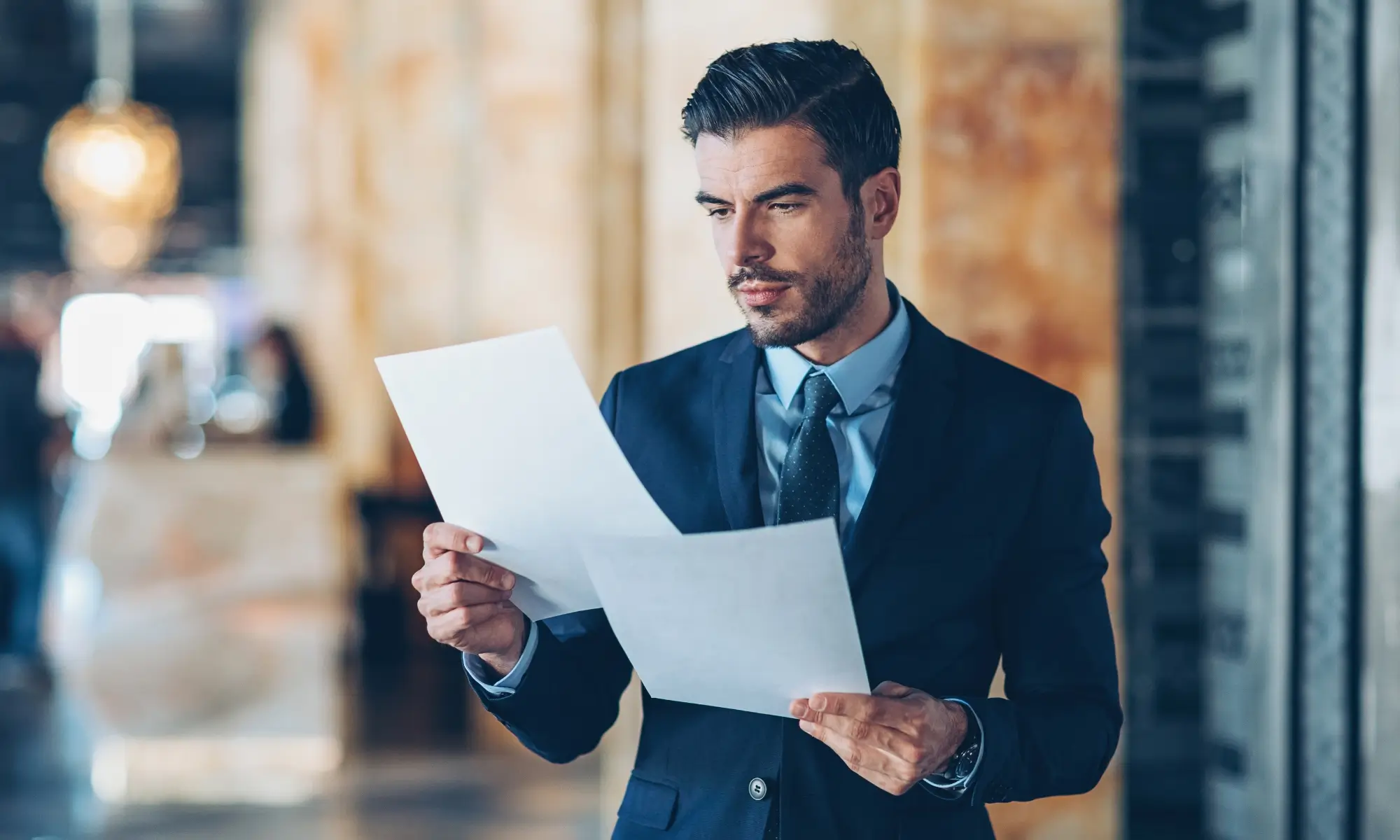
What is an SOP?
SOP stands for Standard Operating Procedure. It is a formal document that provides detailed, written instructions on how to perform specific tasks or operations within an organization. SOPs are designed to ensure that every process is carried out consistently, efficiently, and safely, regardless of who performs it.
They act as a blueprint for employees, guiding them step-by-step to complete a task the right way, every time. SOPs are widely used in industries like manufacturing, healthcare, education, IT, logistics, food safety, and more.
Importance of SOPs
- Consistency and Quality Control: SOPs ensure tasks are performed uniformly across the organization, reducing variability and maintaining product or service quality.
- Efficiency and Time Saving: With clear instructions, employees can execute tasks faster and with fewer errors, boosting productivity.
- Training and Onboarding: SOPs serve as effective training tools for new employees, helping them learn procedures without constant supervision.
- Compliance and Safety: SOPs help organizations meet industry regulations and safety standards, reducing legal risks and improving workplace safety.
- Accountability and Responsibility: SOPs define who is responsible for each task, making it easier to track performance and manage accountability.
- Business Continuity: If key personnel are absent, others can rely on SOPs to ensure the work continues without interruption.
- Improved Communication: SOPs eliminate ambiguity by documenting exactly how tasks should be done, reducing misunderstandings between teams.
In short, an SOP isn’t just a piece of paper—it’s a strategic tool that helps organizations run smarter, safer, and more successfully.
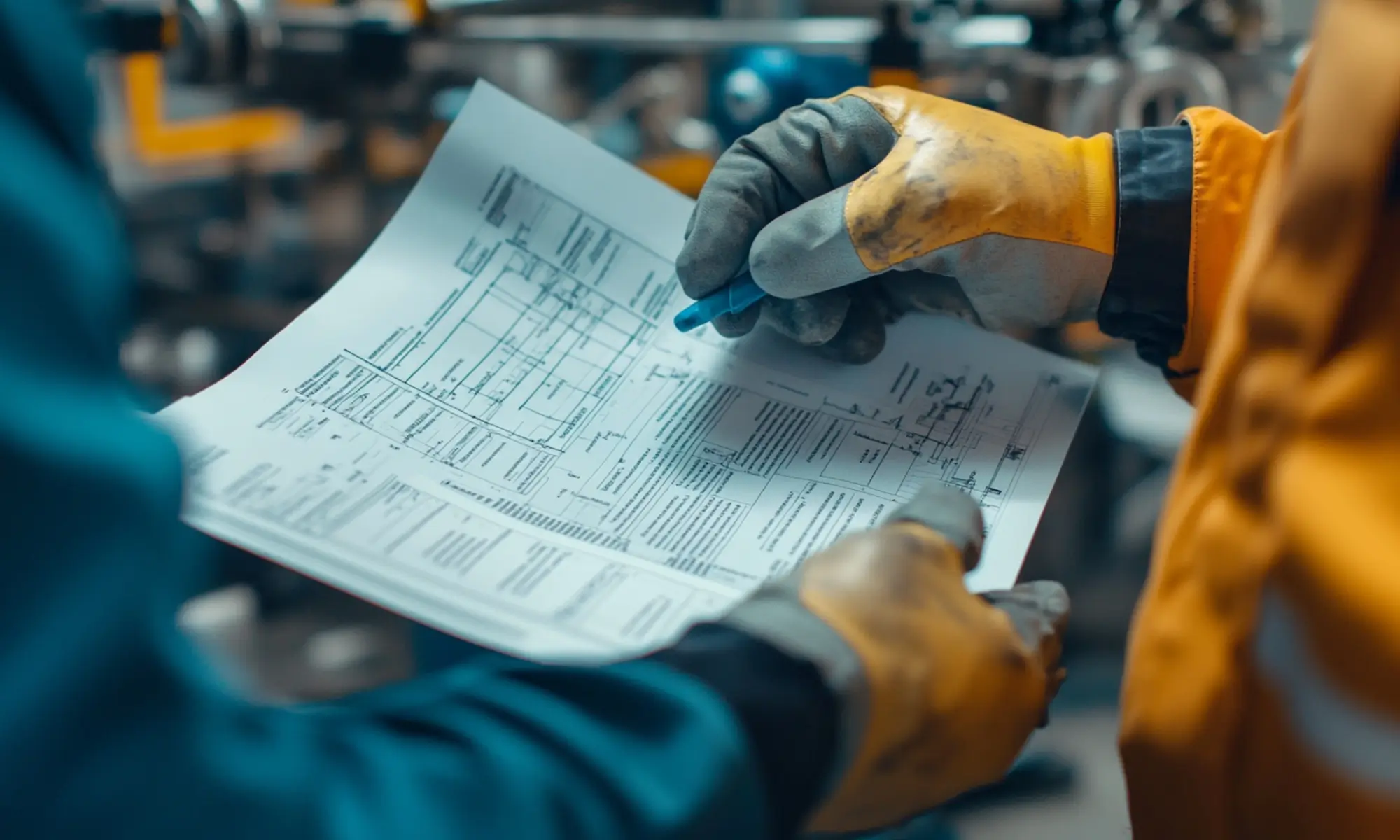
Key Components of an Effective SOP
Creating a helpful and usable SOP means including the right elements. Here’s what every good SOP should contain:
1. Title Page
The title page is like a cover sheet that provides essential document control information. It ensures that everyone is using the correct and most recent version of the SOP. It also identifies the responsible parties, which adds transparency and accountability for the procedure’s content and updates.
What it includes:
- The full title of the SOP (e.g., “Machine Maintenance Procedure”)
- A unique identification or reference number
- The department or unit responsible for the SOP
- Date of creation and latest revision
- Names and signatures of the individuals who prepared, reviewed, and approved the SOP
2. Purpose
The purpose section sets the stage by explaining the “why” behind the procedure. It gives the reader context and helps them understand the value and intent of the SOP. Without this, employees may not grasp the significance of following the procedure properly.
What it includes:
- A concise description of why the SOP is necessary
- The main objectives the SOP is designed to achieve
3. Scope
The scope outlines the boundaries of the SOP. It makes clear who must follow it and under what circumstances. This prevents confusion or incorrect application of the procedure, especially in large organizations with multiple departments.
What it includes:
- Details on which locations, departments, processes, or roles the SOP applies to
- Any limitations or exclusions
4. Roles and Responsibilities
Clearly defined responsibilities ensure that everyone knows their part. It improves coordination, avoids duplication of effort, and reinforces accountability. This section is particularly useful during training or audits.
What it includes:
- Specific individuals, teams, or job titles responsible for executing or overseeing each part of the procedure
- Any approvals, sign-offs, or verifications required
5. Definitions
This section makes the SOP accessible to everyone, including new hires or team members unfamiliar with certain terms. By reducing confusion, it improves compliance and the effectiveness of the procedure.
What it includes:
- Clarifications of industry-specific terms, technical jargon, acronyms, or abbreviations used in the SOP
6. Materials and Equipment
This section ensures that users are fully prepared before beginning the procedure. It prevents delays, mistakes, or safety risks caused by missing or incompatible equipment. Having everything ready upfront also improves efficiency.
What it includes:
- A list of all tools, devices, software, materials, or protective gear required to perform the task successfully.
7. Procedure Steps
This is the heart of the SOP. Clear and precise steps help employees follow the correct process every time, reducing errors, saving time, and ensuring quality. Visual aids can make complex procedures easier to understand, especially for hands-on tasks.
What it includes:
- A detailed, chronological list of steps to complete the task
- May include visuals like flowcharts, images, or screenshots to improve clarity
- Action words and specific instructions for each step
8. Safety and Compliance Information
This section is crucial for employee safety and legal compliance. It helps prevent accidents, ensures adherence to health and safety standards, and protects the organization from liability in case of audits or incidents.
What it includes:
- Warnings about potential hazards
- Required Personal Protective Equipment (PPE)
- References to safety regulations like OSHA, ISO, or local compliance rules
9. References
References provide additional context and support for complex or interconnected tasks. They also allow users to dig deeper into related processes without duplicating information, keeping the SOP focused and concise.
What it includes:
- Links or citations to other SOPs, operation manuals, external standards, or company policies that relate to the current procedure
10. Revision History
Maintains control over document updates and versioning. This helps organizations track changes over time, ensure outdated procedures aren’t used, and stay compliant during audits or quality reviews.
What it includes:
- A table or log listing previous versions, dates of revisions, what was changed, and who made or approved the updates
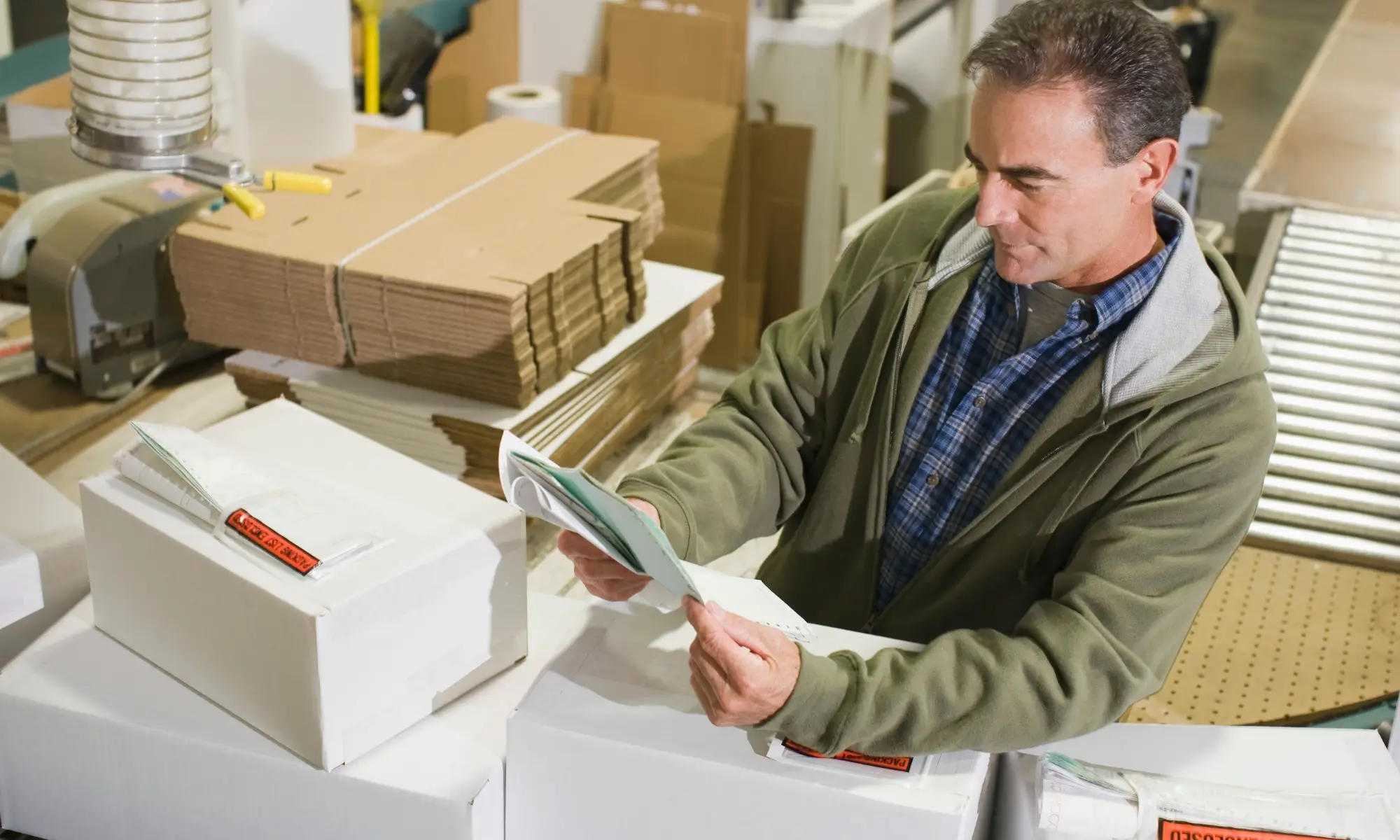
Types of SOPs (Standard Operating Procedures)
SOPs can be classified into different types depending on how they are written, what they are used for, and the complexity of the task they cover. Understanding these types helps in choosing the right format for your organization’s specific needs.
1. Step-by-Step SOP
This is the most common and straightforward type of SOP. It provides a linear list of instructions, usually numbered or bulleted, that employees can follow in sequence.
Best For:
- Simple, repetitive tasks
- Single-user operations
- Routine procedures like logging in to a system, cleaning equipment, or preparing reports
Advantages:
- Easy to follow
- Minimizes confusion
- Great for onboarding and training
2. Hierarchical SOP
A hierarchical SOP breaks the process into main steps and sub-steps. It is more detailed than the basic step-by-step version and is useful for tasks with decision points or variations.
Best For:
- Complex or technical procedures
- Multistage processes
- Procedures requiring decisions or checks along the way
Advantages:
- More detailed without being overwhelming
- Helps clarify complex processes
3. Flowchart SOP
A visual type of SOP using flowcharts or decision trees to map out the process. It shows actions, decisions, and paths users may follow based on different outcomes.
Best For:
- Troubleshooting
- Multi-outcome processes
- Customer service scenarios, tech support, or emergency response
Advantages:
- Easy to understand visually
- Ideal for conditional procedures
- Helps users make decisions quickly
4. Checklist SOP
A checklist SOP presents a to-do list of items or actions. It’s ideal for experienced employees who don’t need detailed instructions but need to ensure nothing is missed.
Best For:
- Audits and inspections
- Safety checks
- Pre-operation or shutdown procedures
Advantages:
- Simple and quick
- Effective for routine checks
- Reduces oversight
5. Work Instruction SOP
Work instructions are granular, highly detailed SOPs that cover specific tasks in depth. They are often part of larger SOP documents.
Best For:
- Technical manufacturing processes
- Quality assurance tasks
- Any process where precision is critical
Advantages:
- Precision and control
- Ideal for training or certification
- Supports quality standards like ISO 9001
6. Hybrid SOP
A combination of two or more types, such as step-by-step with flowcharts, or checklists with decision points.
Best For:
- Cross-departmental processes
- Situations requiring both structure and flexibility
- SOPs used by both new and experienced staff
Advantages:
- Customizable for real-world complexity
- Balances detail with usability
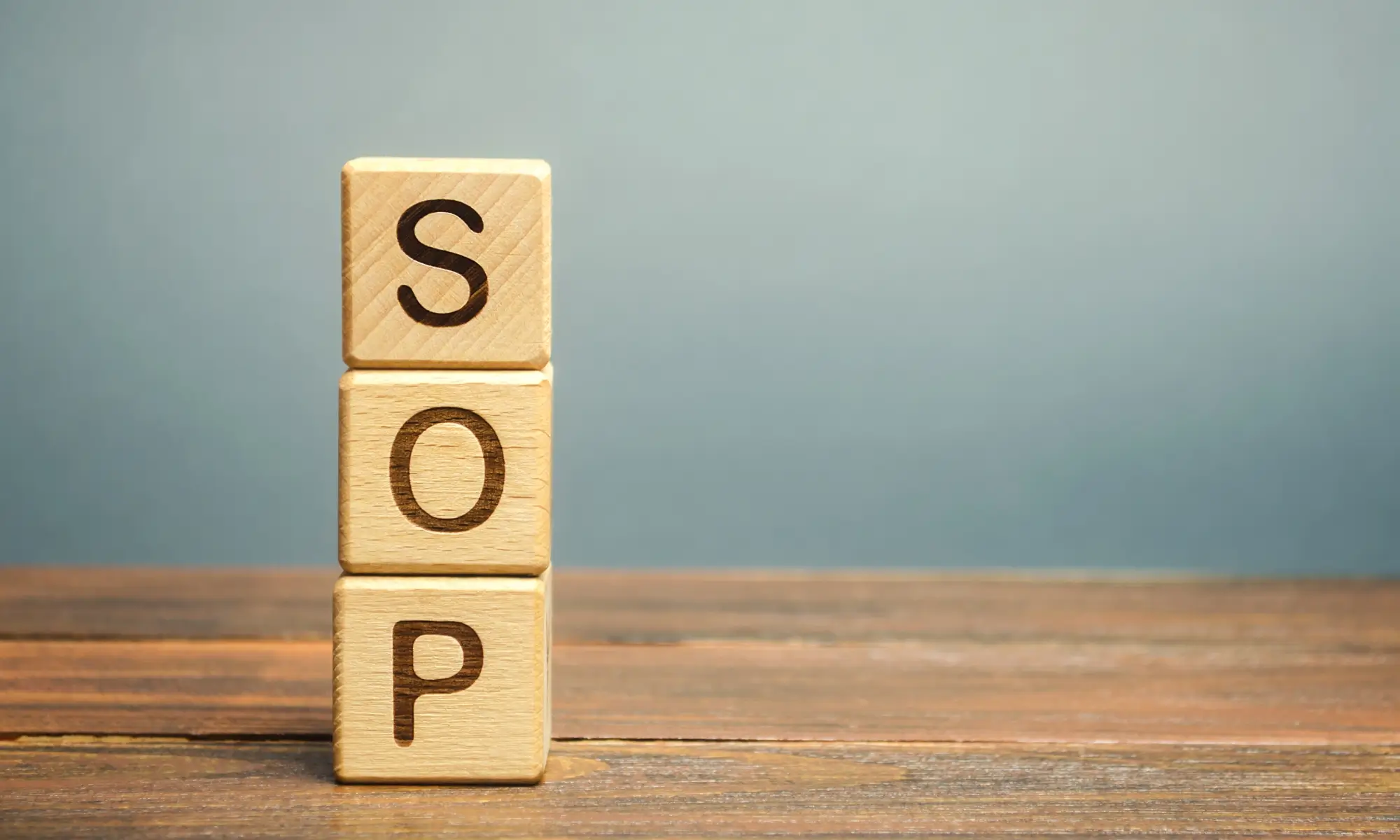
Real-World Examples of SOPs
To better understand SOPs, let’s explore how they function in different settings:
1. Manufacturing SOP – Machine Maintenance
Title: Routine Maintenance for CNC Machines
Purpose: To ensure the machine operates safely and efficiently
Procedure Highlights:
- Turn off power supply
- Inspect for wear and tear on belts and gears
- Clean filters and lubrication points
- Restart machine and conduct a test run
Why It Matters: Prevents unexpected downtime, extends equipment life, and improves worker safety.
2. Healthcare SOP – Patient Admission Process
Title: Patient Intake and Admission Procedure
Purpose: To standardize the admission process and maintain accurate records
Procedure Highlights:
- Verify patient identity and insurance
- Collect medical history and allergies
- Assign to a physician and room
- Record information in the EMR system
Why It Matters: Ensures quality care, reduces administrative errors, and maintains legal compliance.
3. Food Industry SOP – Kitchen Hygiene and Sanitation
Title: Daily Kitchen Cleaning Protocol
Purpose: To maintain cleanliness and food safety
Procedure Highlights:
- Sanitize all countertops, cutting boards, and utensils
- Clean floor drains and dispose of waste
- Check and log refrigerator/freezer temperatures
- Wear gloves and hairnets during prep
Why It Matters: Prevents foodborne illness and supports compliance with health codes.
4. Office/Admin SOP – Document Approval Workflow
Title: Internal Document Review and Approval
Purpose: To streamline document approvals and maintain version control
Procedure Highlights:
- Draft submitted to department head
- Review for accuracy and completeness
- Final approval by senior management
- Document logged and archived
Why It Matters: Speeds up communication, reduces miscommunication, and ensures audit readiness.
5. Retail SOP – Product Return Handling
Title: Customer Product Return Process
Purpose: To ensure consistent and fair handling of returns
Procedure Highlights:
- Verify receipt and condition of returned item
- Log return in POS system
- Offer exchange, refund, or store credit
- Restock item or send for inspection
Why It Matters: Improves customer satisfaction and maintains inventory accuracy.
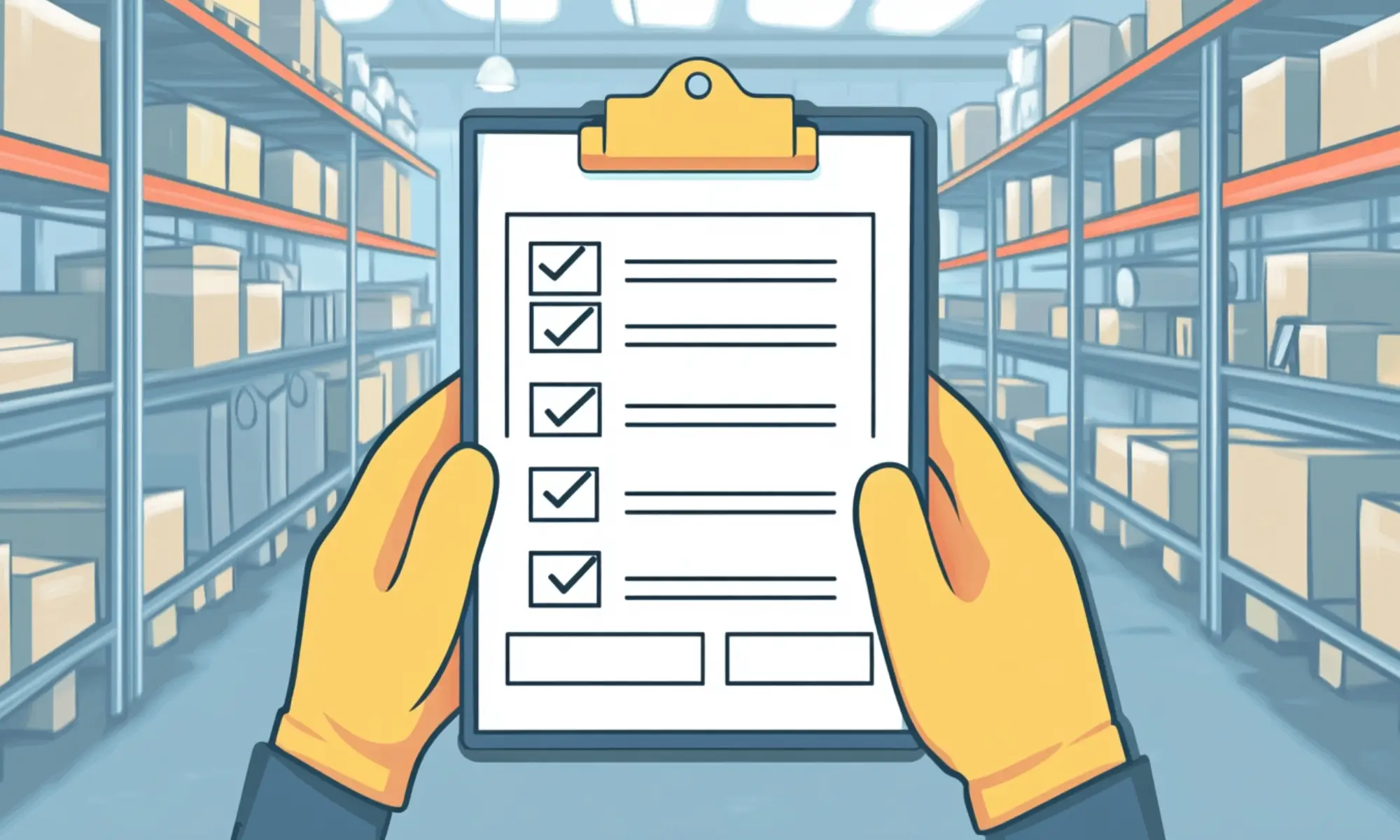
Best Practices for Writing SOPs
Here are the best practices for writing effective Standard Operating Procedures (SOPs) that ensure clarity, usability, and compliance with industry standards:
1. Start with a Clear Purpose
The purpose sets the stage for the SOP. It answers the fundamental question: Why does this document exist? A clearly stated purpose helps the user immediately understand what the procedure is meant to achieve—whether it’s for safety, compliance, quality control, or operational consistency.
How to do it:
Write a brief, direct statement at the beginning of the SOP that outlines:
- What the SOP is about
- Why it’s important
- The outcome it aims to produce
Example: “This SOP outlines the procedure for calibrating laboratory scales to ensure accurate weight measurements and regulatory compliance.”
2. Use Simple and Clear Language
SOPs are used by a wide range of personnel, including new hires and individuals for whom English may not be a first language. Technical jargon, vague language, or overly complex phrasing can lead to misunderstandings and errors.
How to do it:
- Use plain, everyday language
- Write in short, active voice sentences
- Avoid unnecessary technical terms unless they’re defined
- Replace passive constructions with direct commands
Example:
✔️ “Shut off the power switch.”
❌ “The power switch should be turned off.”
3. Be Specific and Action-Oriented
Ambiguous instructions lead to inconsistent results. People interpret vague terms differently, which can result in errors, inefficiency, or safety hazards. Specific instructions help users perform the task exactly as intended.
How to do it:
- Use measurable and quantifiable terms
- Give clear parameters (e.g., time, temperature, volume)
- Be directive with verbs like “Press,” “Check,” “Record,” “Open,” etc.
Example:
✔️ “Set the oven to 180°C and bake for 15 minutes.”
❌ “Heat the oven and bake until done.”
4. Structure It Logically
A clear, logical structure makes it easier for users to follow the SOP from start to finish without missing steps or jumping ahead. Well-organized SOPs are easier to understand, train from, and revise when needed.
How to do it:
Divide the document into standard sections like:
- Purpose
- Scope
- Materials
- Roles
- Procedure
- Safety/Compliance
- References
Present instructions in chronological order. Use headings, subheadings, bullet points, or numbered steps. Consider using a flowchart if the process involves decisions.
Example Structure:
- Prepare materials
- Inspect equipment
- Perform task
- Record results
- Shut down and clean
5. Use Visual Aids When Necessary
Some procedures are too complex to explain through text alone. Visuals help reduce confusion, enhance understanding, and make instructions accessible to visual learners. They’re especially useful in technical or hands-on tasks.
How to do it:
- Add flowcharts to show process flow
- Include diagrams to illustrate equipment setup
- Use screenshots for software-based tasks
- Insert labeled photos for step-by-step guidance
Example: In a fire extinguisher inspection SOP, include a photo of a pressure gauge with the correct pressure zone highlighted.
6. Define Roles and Responsibilities
Knowing who is responsible for each step ensures tasks aren’t duplicated, overlooked, or miscommunicated. It also makes accountability and training easier.
How to do it:
- Assign roles using job titles, not individual names
- Clearly state what each role must do at different stages
- If multiple departments are involved, show hand-offs or shared duties
Example:
- “Warehouse Supervisor: Verifies product packaging before shipment.”
- “Quality Control Technician: Records inspection data and signs off final approval.”
7. Include Safety and Compliance Info
Safety and compliance are critical in industries like healthcare, manufacturing, construction, and laboratories. Including clear instructions on hazards, legal requirements, and safety precautions protects employees and ensures your organization complies with regulatory standards (like OSHA, ISO, or FDA).
How to do it:
- Add warning signs or hazard symbols for risky steps
- List required PPE (Personal Protective Equipment) such as gloves, helmets, or goggles
- Reference regulatory standards or internal safety policies
- Include emergency contacts or first-aid instructions if applicable
Example: Wear safety goggles before opening the chemical container (per OSHA 1910.133).
8. Test the SOP in Practice
An SOP might look good on paper but fail in the real world. Testing verifies that instructions are clear, the steps are practical, and nothing has been overlooked. It also exposes gaps or steps that may need further clarification.
How to do it:
- Ask someone unfamiliar with the procedure to perform it using only the SOP
- Observe the process and note where confusion or delays occur
- Adjust the SOP based on real-time feedback
Example: Have a new hire perform a system shutdown using the SOP. If they pause or ask questions, revise the step for clarity.
9. Get Stakeholder Feedback
The best people to review an SOP are the ones who use it daily. Getting feedback from actual users helps ensure that the procedure is both accurate and realistic.
How to do it:
- Share a draft SOP with the employees or teams who will use it
- Ask for feedback on wording, missing steps, or potential improvements
- Involve supervisors and quality or safety officers for compliance validation
Tip: Include a review form or comment section when circulating the draft for feedback.
10. Regularly Review and Update
Procedures evolve due to changes in technology, regulations, staff, or equipment. Outdated SOPs can lead to inefficiencies or non-compliance, especially in regulated industries.
How to do it:
- Set a review cycle (e.g., every 6 months or annually)
- Assign responsibility to a specific person or department
- Use a revision history section to track changes, reasons, and dates
Example: Reviewed annually by the Quality Assurance Manager – next review due: Jan 2026.
11. Make It Accessible
An SOP that’s hard to find might as well not exist. Accessibility ensures that staff can quickly refer to SOPs when needed—during training, inspections, or emergencies.
How to do it:
- Store SOPs in a centralized digital system (like an intranet or cloud platform)
- Provide version-controlled PDFs or web-based formats
- Train employees on where and how to access SOPs
Tip: Use folder hierarchies or search tags (e.g., “Safety > Fire Evacuation” or “HR > Onboarding”) for easy navigation.
12. Ensure Consistency Across SOPs
Consistency in formatting, tone, and structure makes your SOP library look professional and makes it easier for users to navigate and trust the content. Inconsistent documents confuse readers and waste time.
How to do it:
- Create and enforce a standard SOP template
- Use uniform fonts, heading styles, bullet points, and labeling systems
- Keep terminology consistent across all documents (e.g., don’t alternate between “staff” and “team member”)
Tip: Use style guides and assign a document owner or editor for final reviews.
Conclusion
Standard Operating Procedures (SOPs) are far more than internal documents—they’re the foundation of operational excellence. By providing step-by-step guidance, ensuring consistency, enhancing safety, and promoting accountability, SOPs empower teams to perform tasks efficiently and correctly every time.
Whether you’re managing complex workflows in manufacturing, ensuring patient safety in healthcare, or streamlining everyday office operations, having well-written SOPs ensures that your processes are repeatable, reliable, and ready for scaling. Understanding the types, components, and best practices for writing SOPs equips you to create documents that truly support your team and organization.
Investing time in crafting effective SOPs today can save countless hours tomorrow—and contribute to a culture of quality, compliance, and continuous improvement.