In industries where handling hazardous materials is a reality, safeguarding the environment, ensuring worker safety, and complying with regulations are paramount concerns. This blog will provide a comprehensive overview of spill containment berms – versatile structures designed to effectively manage and control the potential risks associated with spills of hazardous liquids, chemicals, and other substances.
This article will explore the different types of spill containment berms available, exploring their unique features and applications. We’ll also uncover the myriad benefits of incorporating these innovative solutions into your operational practices, from environmental protection and regulatory compliance to cost savings and emergency response capabilities.
But how exactly do spill containment berms work? Fear not, as we’ll guide you through the mechanics behind these ingenious structures. From their material composition to their deployment process, you’ll understand how spill containment berms prevent the spread of harmful substances, mitigate potential disasters, and maintain a safer and cleaner working environment.
So, join us on this informative journey as we explore spill containment berms in-depth if you’re an industry professional seeking to enhance spill management strategies or simply someone intrigued by the technology that safeguards our planet and communities. Let’s dive into the world of spill containment, exploring its types, benefits, and mechanics that make it an indispensable tool in modern industry.
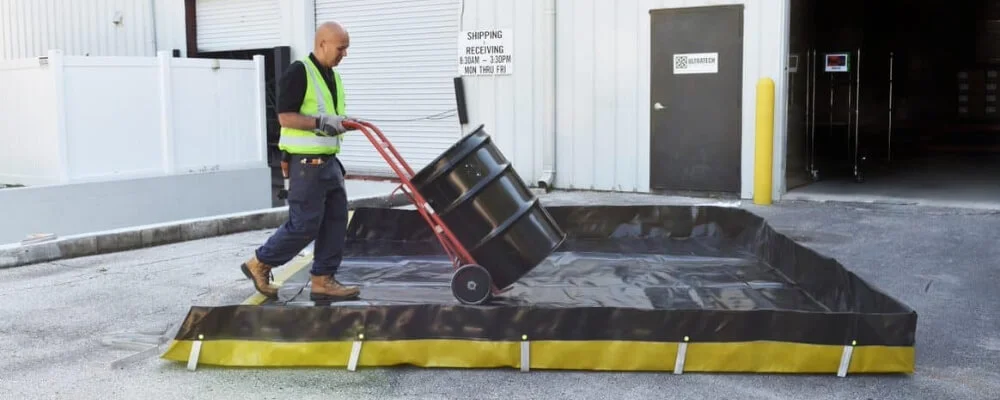
What is Spill Containment Berms?
Spill containment berms, also known as spill containment barriers or containment bunds, are engineered structures designed to prevent the spread of hazardous liquids, chemicals, oils, or other potentially harmful substances in the event of a spill. They function as temporary containment basins by creating a physical barrier that confines the spilled material within a designated area, preventing it from reaching the environment or causing harm to people, wildlife, and property.
Spill containment berms come in various forms, sizes, and materials, tailored to different applications and scenarios. They are commonly used in industrial settings, construction sites, transportation hubs, and areas where the risk of spills is present. The primary purposes of spill containment berms include:
- Environmental Protection: Berms are designed to contain spills and leaks, preventing hazardous substances from contaminating soil, water bodies, and ecosystems. This helps mitigate the environmental impact of the spilled materials.
- Safety: By confining spilled liquids, berms reduce the risk of exposure to toxic, flammable, or harmful substances, thus protecting the health and safety of workers, responders, and the general public.
- Compliance: Many industries are subject to regulations and laws that require containment measures to prevent spills and leaks. Spill containment berms help businesses comply with these regulations and avoid penalties.
- Emergency Response: Berms provide a rapid and effective solution to containing spills during emergencies, helping to minimize the potential consequences of accidents or unforeseen incidents.
- Containment of Equipment and Storage: Berms can also hold spill containment pallets, equipment, storage tanks, or drums containing hazardous materials, adding an extra layer of protection against leaks or drips.
Spill containment berms are designed to withstand the pressures exerted by the contained material, and they often have features such as reinforced walls, welded seams, or foam-filled sections to maintain their structural integrity. Depending on the type of berm, they can be portable, collapsible, or permanent installations, making them versatile tools for various spill containment needs.
Overall, spill containment berms play a critical role in safeguarding the environment, human health, and regulatory compliance by containing and controlling hazardous material spills, thereby preventing potential disasters and pollution.
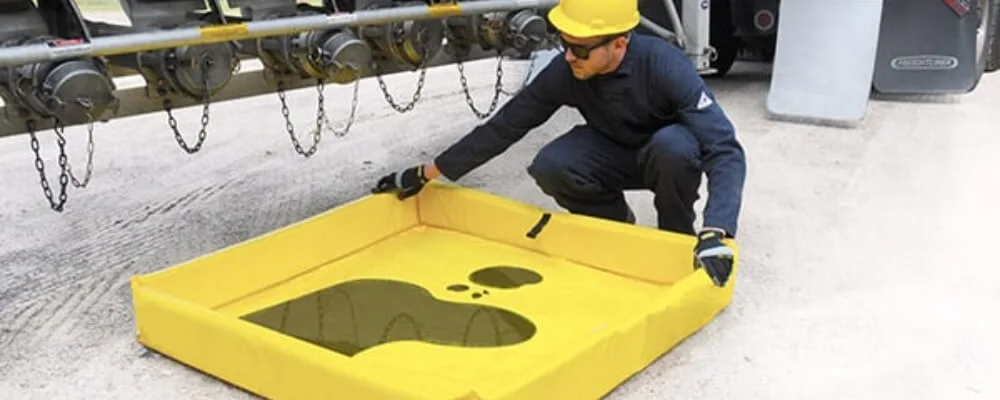
Benefits Of Using Spill Containment Berms
Using spill containment berms offers a range of benefits for businesses, industries, and environments with a potential risk of hazardous material spills. Here are some key advantages of using spill containment berms:
- Environmental Protection: One of the primary benefits is preventing the spread of hazardous materials into the environment. Spill containment berms confine spills within a designated area, preventing soil and water contamination and damaging ecosystems, wildlife, and aquatic habitats.
- Regulatory Compliance: Many industries are subject to strict regulations and laws regarding spill prevention and containment. Spill containment berms help businesses comply with these regulations, avoiding legal penalties and reputational damage.
- Health and Safety: Berms contribute to the safety of workers, responders, and nearby populations by reducing exposure to toxic, flammable, or harmful substances. This is crucial for maintaining a safe working environment and preventing accidents.
- Cost Savings: The potential costs associated with cleaning up a spill, environmental remediation, legal fines, and medical expenses far exceed the investment in spill containment berms. Using berms can help mitigate these financial risks.
- Prevention of Business Interruption: A significant spill can lead to disruptions, production halts, and costly downtime. Berms minimize the impact of spills, allowing businesses to resume operations more quickly.
- Emergency Response: Spill containment berms provide an immediate solution for containing spills during emergencies. They can help prevent the escalation of an incident and provide responders with a controlled environment for cleanup.
- Versatility: Spill containment berms come in various types and sizes to suit different applications. They can be portable and easily transported to different locations, making them versatile tools for different scenarios.
- Ease of Deployment: Many spill containment berms are designed for quick and easy deployment. Some types can be set up rapidly, ensuring timely spill containment and minimizing the potential consequences.
- Customization: Some berms can be tailored to fit specific equipment, areas, or containment requirements. This adaptability enhances their effectiveness in various situations.
- Maintenance and Reusability: Most spill containment berms are relatively easy to clean and maintain. After a spill is contained, the berm can be cleaned and reused, reducing long-term costs.
- Protection of Infrastructure: Berms can safeguard infrastructure such as floors, pavements, and drains by preventing corrosive or harmful liquids from coming into contact with them.
- Risk Reduction: By effectively containing spills, berms reduce the risk of accidental releases and potentially catastrophic events, enhancing overall operational safety.
Using a spill containment berm is a proactive approach to managing the risks associated with handling hazardous materials. They offer a cost-effective and reliable way to protect the environment, maintain regulatory compliance, ensure worker safety, and preserve the reputation of businesses and industries.
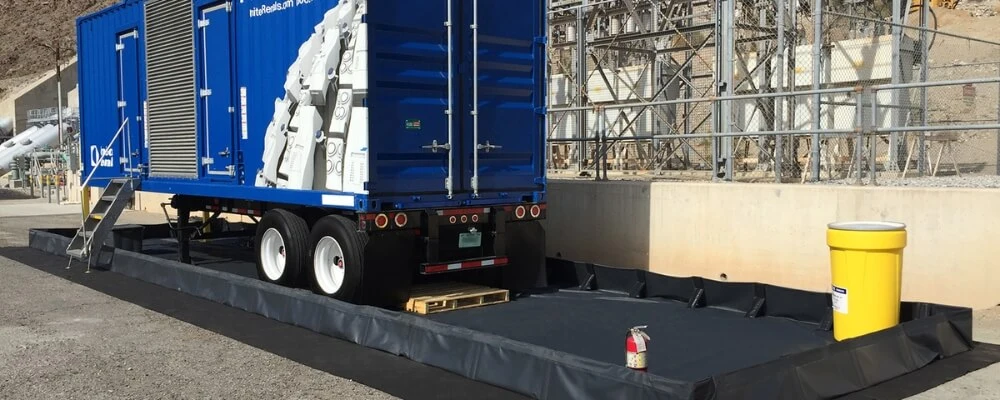
Types Of Spill Containment Berms
Spill containment berms are structures designed to contain and control the spread of hazardous liquids, chemicals, and other materials in the event of a spill. They come in various types and designs to suit different applications and environments. Here are some common types of spill containment berms:
- Portable Berms: These are collapsible or foldable berms that are easily transportable and can be set up quickly. They are often used for temporary spill containment at remote locations, during maintenance, or for emergency response.
- Drive-Through Berms: These berms are designed to allow vehicles to drive over them, making them suitable for areas where vehicles need to cross over while maintaining spill containment integrity.
- Foam Wall Berms: These berms have foam-filled walls that provide structure and stability. The foam walls can be quickly inflated during deployment to create a barrier against spills.
- Welded Seam Berms: These are constructed from materials with welded seams to ensure a watertight and leak-resistant containment area. They are often used to contain hazardous materials over an extended period.
- L-Bracket Berms: These berms have L-shaped brackets or supports along the walls, providing additional rigidity and helping to maintain the shape of the berm even when empty.
- Self-Rising Berms: Also known as “pop-up” berms, these berms have walls that automatically spring into an upright position as the berm is unfurled, simplifying and speeding up deployment.
- Customizable Berms: Some manufacturers offer customizable berms tailored to fit specific equipment or areas. This is especially useful in situations where standard-sized berms may not work effectively.
- Spill Pallet Berms: These berms are designed to hold spill pallets, which can hold containers or drums. The berms provide additional containment for potential leaks or spills from the containers on the pallets.
- Modular Berms: Modular berms consist of individual sections that can be connected to create larger containment areas. They are versatile and can be expanded or contracted based on the situation’s needs.
- Berm Liners: These can be placed inside existing containment structures to provide additional protection against leaks or spills.
- Rapid Deployment Berms: Designed for quick response to spills, these berms can be rapidly deployed and inflated, creating an immediate emergency containment area.
When selecting a spill containment berm, it’s important to consider factors such as the type of liquid or material being contained, the size of the area, the level of potential risk, ease of deployment, and any specific requirements for your application. Always follow the manufacturer’s guidelines for installing, maintaining, and properly using spill containment berms.
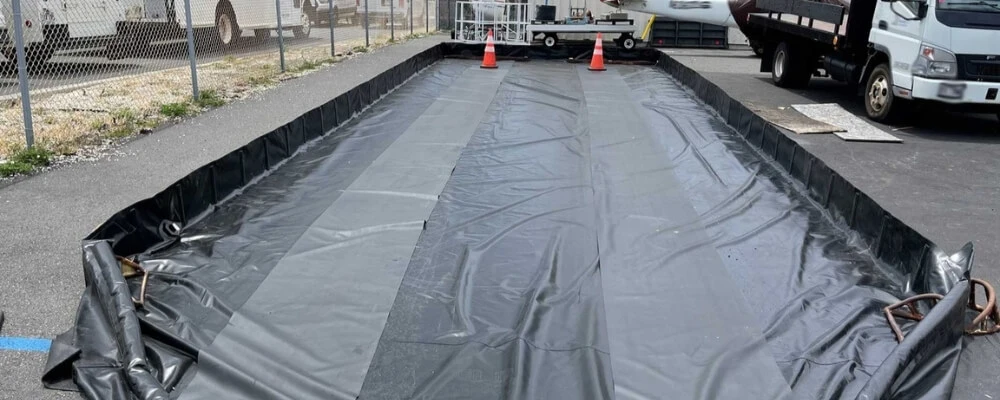
How Do Spill Containment Berms Work?
Spill containment berms are engineered structures designed to effectively control and contain spills of hazardous liquids, chemicals, or other materials. Their primary function is to prevent these substances from spreading and causing environmental damage or posing risks to human health. Here’s how to spill containment berms work:
- Containment: The fundamental purpose of a spill containment berm is to create a barrier that prevents spilled liquids from escaping the designated area. The berm forms a raised perimeter around the spill, creating a temporary basin or containment area. This containment prevents the hazardous substance from seeping into the soil, water bodies, or other sensitive areas.
- Material Selection: Spill containment berms are constructed from various materials, such as high-strength fabrics, coated textiles, or PVC. The choice of material depends on factors like the type of material being contained, the anticipated volume of the spill, and the environment in which the berm will be deployed. The selected material should resist the spilled substance and effectively prevent leakage.
- Structural Integrity: Berms are designed with structural integrity to maintain their shape and effectiveness even when empty. This prevents the walls of the berm from collapsing and losing containment capacity.
- Deployability: Depending on the type of berm, they can be either portable and easily transported to different locations or permanently installed. Portable berms can be quickly deployed by unrolling or unfolding them, and some even come with mechanisms that automatically inflate the walls for immediate containment.
- Walls and Seals: The berm walls are crucial in containing spills. They are usually raised to a certain height to create a barrier against escaping liquids. Some berms have foam or air-filled walls that provide buoyancy and structural support. Welded seams or other leak-resistant mechanisms ensure no weak points where the spilled material can escape.
- Integration with Equipment: In industrial settings, spill containment berms are often used with spill pallets, drums, or equipment that may hold hazardous materials. Berms with specific features, such as spill pallet berms, are designed to hold these items while providing an additional layer of containment against leaks or spills.
- Maintenance and Cleanup: Spill containment berms are designed to be relatively easy to clean and maintain. After a spill is contained, the hazardous material can be properly disposed of, and the berm can be cleaned or decontaminated as necessary.
- Adaptability: Berms are available in various sizes and designs to accommodate different spill scenarios. Some berms can be connected to create larger containment areas, while others can be adjusted to fit specific equipment or locations.
Overall, spill containment berms work by creating a physical barrier that contains spilled liquids and prevents them from spreading into the environment. The specific design and effectiveness of a spill containment berm depend on factors such as its type, material, construction, and the nature of the spilled substance. Proper selection, installation, and maintenance are essential to ensure the effectiveness of spill containment berms in preventing environmental damage and safeguarding human health.
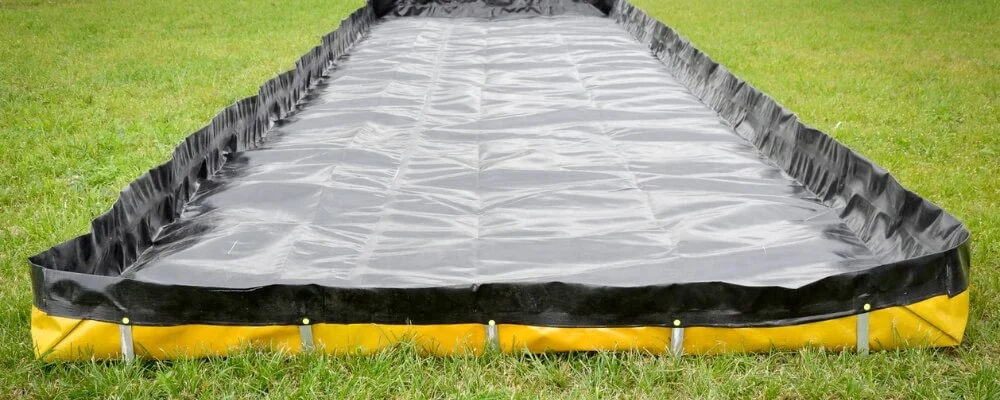
How To Use Spill Containment Berms
Using spill containment berms effectively involves proper selection, deployment, maintenance, and response procedures. Here’s a step-by-step guide on how to use spill containment berms:
1. Selection
- Assess the type of hazardous materials you’ll be dealing with, including their volume and potential risks.
- Choose a spill containment berm compatible with the spilled material and appropriate for the anticipated spill scenario.
2. Preparation
- Identify the area where you’ll be deploying the berm. Ensure it is clear of obstacles and debris that could hinder deployment.
- Ensure workers using the Berm are familiar with its features and deployment process.
3. Deployment
- Lay the spill containment berm in the desired location, properly oriented and aligned.
- If the berm is collapsible or foldable, carefully unfold or expand it to its full size.
- If the berm has foam walls or automatic inflation mechanisms, ensure they are properly activated.
- For drive-through berms, ensure they are properly aligned with the path of vehicles.
4. Containment
- Position the berm to create a raised perimeter around the potential spill area.
- Ensure that the walls of the berm are raised to a sufficient height to contain the spilled material.
- Place equipment, storage containers, or spill pallets within the berm if applicable.
5. Response to Spills
- In the event of a spill, immediately contain it within the spill containment berm.
- Use appropriate spill response materials (absorbents, booms, etc.) to manage the spill within the containment area.
6. Maintenance and Cleanup
- After the spill is under control, begin the cleanup process, following proper hazardous material cleanup and disposal procedures.
- If the berm becomes contaminated, ensure it is properly cleaned and decontaminated before storing or reusing it.
7. Disposal of Contaminated Materials
- Follow local regulations and guidelines for properly disposing of contaminated materials, such as absorbents or hazardous liquids.
8. Inspection and Maintenance
- Regularly inspect the spill containment berm for signs of damage, wear, or deterioration.
- Repair or replace any damaged components to ensure the berm’s effectiveness.
9. Training and Familiarization
- Train workers on the proper deployment, use, and maintenance of spill containment berms.
- Conduct drills or simulations to ensure that workers are familiar with the procedures in case of an actual spill.
10. Documentation
- Keep records of berm inspections, maintenance, and any spill incidents. This documentation can be useful for compliance and reporting purposes.
Remember that the specific steps for using spill containment berms may vary depending on the type of berm and the materials you are working with. Always refer to the manufacturer’s guidelines and follow industry best practices to ensure the safe and effective use of spill containment berms in your particular environment.
Conclusion
In conclusion, spill containment berms are a testament to human innovation and our commitment to environmental stewardship and workplace safety. The diverse range of spill containment berms available underscores the adaptability of these structures to a multitude of scenarios, from routine operations to emergencies. Spill containment berms empower industries to tailor their spill prevention strategies to their specific needs by offering portable, drive-through, foam-walled, and modular designs.
The benefits of integrating spill containment berm into operational practices are profound and far-reaching. The advantages extend to businesses, communities, and our planet, from ensuring compliance with stringent regulations to safeguarding delicate ecosystems and minimizing financial liabilities. Spill containment berms prevent the immediate spread of hazardous materials and contribute to a safer working environment, greater operational efficiency, and enhanced emergency response capabilities.
By understanding the mechanics behind spill containment berms, we gain insight into their role as proactive solutions. From material selection to proper deployment and maintenance, these structures epitomize preparedness. The ability to effectively contain and control spills become an integral part of risk management, fostering a culture of responsibility and care.