Permit to Work (PTW) systems are specialized safety protocols designed for various hazardous work environments. These systems categorize tasks based on their associated risks and provide specific guidelines to ensure worker safety. Examples of PTW systems include hot work permits, electrical permits, confined space permits, and many others. Each type of permit addresses unique hazards and outlines the necessary precautions to mitigate them.
In this blog, we will discuss the different types of Permits to Work and their examples of PTW systems. By understanding the nuances of each system, organizations can make informed decisions about which PTW is best suited for their specific work environment and tasks.
Permit To Work Systems (PTW) and its Purpose
A work permit is a formal written document that authorizes a worker or team to perform a job involving serious hazards. A work permit aims to ensure that workers are fully aware of the risks involved in their jobs and provide them with the necessary precautions and preparation to minimize them.
Work permits are typically required for jobs that involve working in hazardous environments or with hazardous materials. For example, jobs that require employees to enter and work in confined spaces, such as tanks, vessels, and pipes, are considered high-risk and require a work permit. Similarly, jobs that involve repairing, maintaining, or inspecting electrical installations, such as power lines, switchgear, and transformers, also require a work permit.
In addition to these examples, work permits are required for jobs involving large or complex equipment, such as cranes, forklifts, and heavy machinery. These jobs require specialized skills and knowledge; a work permit ensures they are fully prepared and trained to perform the job safely.
A work permit ensures workers’ safety and prevents accidents in hazardous work environments. By requiring a work permit, organizations can ensure that workers are fully aware of the hazards associated with their jobs and the necessary precautions to mitigate them, ultimately reducing the risk of accidents and injuries.
Different Types Of Permit To Work Systems
Several permits may be required depending on the job or task. Some of the most common types of permits include:
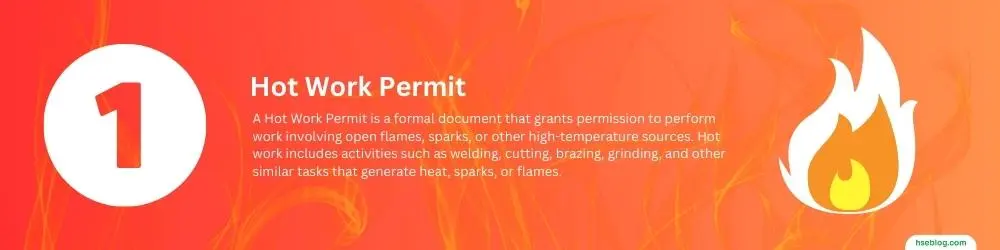
1. Hot Work Permit
A Hot Work Permit is a formal document that grants permission to perform work involving open flames, sparks, or other high-temperature sources. Hot work includes activities such as welding, cutting, brazing, grinding, and other similar tasks that generate heat, sparks, or flames. These activities can present significant fire and explosion hazards, leading to serious injury or damage to property if not properly managed.
The main objectives of a Hot Work Permit are to:
- Identify and assess potential fire and explosion hazards associated with the hot work activity.
- Ensure that the individuals involved in the hot work activity are adequately trained and competent to perform the work safely.
- Establish appropriate safety measures, including fire prevention and control, ventilation, and personal protective equipment (PPE).
- Verify that the work area is free of flammable materials and that proper safeguards, such as fire blankets or extinguishers, are in place.
- Maintain a record of all hot work activities for future reference and regulatory compliance.
Here are some examples of tasks that may require a Hot Work Permit:
- Welding or cutting metal structures or equipment involves using an open flame or arc to join or cut metal parts or structures. A hot work permit ensures proper fire prevention measures, such as removing flammable materials from the work area and using fire blankets to contain sparks.
- Grinding or sanding of metal surfaces: Grinding or sanding metal surfaces generates heat and sparks, which can ignite flammable materials in the work area. A hot work permit ensures proper ventilation, and PPE is used to minimize the risk of fire or explosion.
- Brazing or soldering of pipes or other components: These activities involve using heat to join metal components without melting them. A hot work permit ensures that proper fire prevention measures are in place and that workers use appropriate PPE and ventilation.
- Thawing of frozen pipes: Using heat sources such as torches can create fire hazards due to flammable materials in the work area. A hot work permit ensures proper safety measures, such as heat-resistant shields and PPE, are in place to minimize the risk.
- Roofing work involving torches: Torch-applied roofing involves using open flames to seal and install roofing materials. A hot work permit ensures proper fire prevention and control measures, such as fire-resistant roofing materials, fire extinguishers, and fire watches.
- Demolition work involving cutting or burning of materials: Demolition work involving cutting or burning of materials can generate heat and sparks, which can ignite flammable materials in the work area. A hot work permit ensures proper safety measures, such as removing flammable materials from the work area and using appropriate PPE and ventilation.
- Heating or thawing equipment or pipelines involves using heat to thaw or warm equipment or pipelines, which can pose a fire hazard if proper safety measures are not in place. A hot work permit ensures workers use appropriate PPE and fire prevention measures, such as fire-resistant blankets and fire extinguishers.
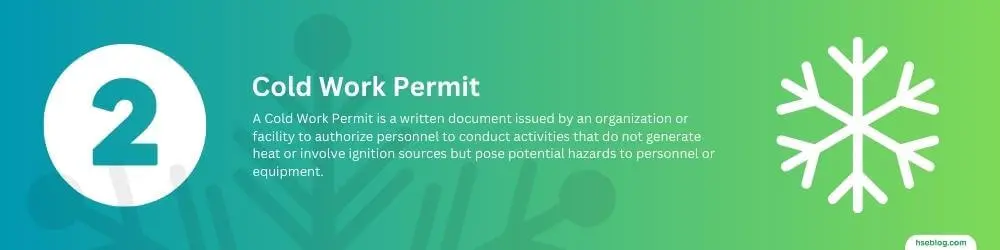
2. Cold Work Permit
A Cold Work Permit is a written document issued by an organization or facility to authorize personnel to conduct activities that do not generate heat or involve ignition sources but pose potential hazards to personnel or equipment. It is a safety measure to ensure that workers know the risks associated with the task and are adequately trained and equipped to complete the job safely.
A cold work permit typically outlines the specific tasks to be performed, the associated hazards, and the precautions that must be taken to mitigate the risks. The permit may also include information on the duration of the work, the personnel involved, and the necessary equipment and tools required to complete the job safely.
Examples of cold work activities that may require a permit include:
- Painting – Painting activities may require a cold work permit to ensure that workers are protected from exposure to hazardous chemicals and that proper ventilation and personal protective equipment (PPE) are used.
- Operating machinery – Operating machinery such as forklifts or cranes can be hazardous if proper safety protocols are not followed. A cold work permit may be required to ensure workers are trained and certified to operate the equipment safely.
- Erecting scaffolding – Scaffolding can be hazardous if not erected properly. A cold work permit may be required to ensure that workers are trained to erect the scaffolding safely and that proper safety equipment is used.
- Using cranes or heavy lifts – Using cranes or heavy lifts can be dangerous if not done properly. A cold work permit may be necessary to ensure that workers are trained to use the equipment safely and that proper safety protocols are followed.
- Handling heavy objects – Handling heavy objects can lead to injuries if not done safely. A cold work permit may be required to ensure that workers are trained to handle heavy objects properly and that proper lifting techniques are used.
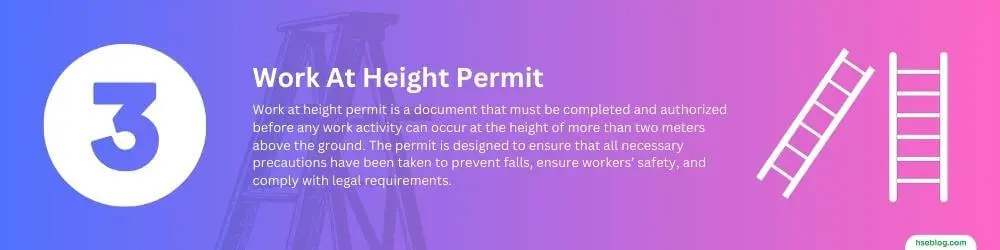
3. Work At Height Permit
Work at height permit is a document that must be completed and authorized before any work activity can occur at the height of more than two meters above the ground. The permit is designed to ensure that all necessary precautions have been taken to prevent falls, ensure workers’ safety, and comply with legal requirements.
Examples of work that requires a height work permit include, but are not limited to:
- Working on ladders: Ladders are commonly used to access high places like roofs or shelves. Any work carried out on a ladder more than two meters above the ground will require a height work permit.
- Working on scaffolding: Scaffolding is commonly used in construction work to provide a stable platform for workers to access high areas. Any work carried out on scaffolding over two meters above the ground requires a height work permit.
- Working on Mobile Elevated Work Platforms (MEWPs): MEWPs are commonly used in construction, maintenance, and cleaning work to provide access to high areas. Any work carried out on a MEWP more than two meters above the ground will require a height work permit.
- Working on roofs: Any work carried out on a roof over two meters above the ground will require a height work permit.
- Working near edges or openings: Work carried out near edges or openings more than two meters above the ground, such as balconies, windows, or open floors, will require a height work permit.
- Using access equipment: Any use of access equipment, such as cherry pickers or hoists, to carry out work more than two meters above the ground will require a height work permit.
In summary, any work activity that takes place at the height of more than two meters above the ground will require a height work permit to ensure the safety of workers and comply with legal requirements.

4. Confined Spaces Work Permit
A Confined Space Permit is a formal document granting permission to work within a confined space. Confined spaces are areas that are large enough for a person to enter and perform work but have limited means of entry and exit and are not designed for continuous occupancy. These spaces can present a variety of hazards, such as toxic atmospheres, oxygen deficiency, engulfment, or entrapment, which can lead to serious injury or fatality if not properly managed.
The main objectives of a Confined Space Permit are to:
- Identify and assess potential hazards associated with the confined space.
- Establish appropriate safety measures, including ventilation, gas monitoring, and rescue procedures.
- Verify that the individuals involved in the work are adequately trained and competent to work in confined spaces safely.
- Ensure proper communication and coordination among workers, supervisors, and rescue personnel.
- Maintain a record of all confined space work activities for future reference and regulatory compliance.
Some examples of tasks that may require a Confined Space Permit include the following:
- Cleaning or maintenance of tanks, vessels, or silos: These confined spaces may contain hazardous chemical residues or lack adequate ventilation, leading to dangerous atmospheres. A confined space permit ensures that all safety protocols are followed, such as purging and isolating the space, ventilating the area, and using gas monitors to detect hazardous atmospheres.
- Inspection, repair, or maintenance of sewers or underground utility vaults: These spaces can present risks such as engulfment, oxygen deficiency, or toxic gases. A confined space permit ensures workers know the hazards, wear appropriate PPE, use gas monitors, and follow proper entry and exit procedures.
- Working inside pipelines, ducts, or tunnels: These confined spaces can have limited access and egress, making it difficult for workers to escape in an emergency. A confined space permit ensures that proper communication and rescue procedures are in place and that workers are trained to work safely in these environments.
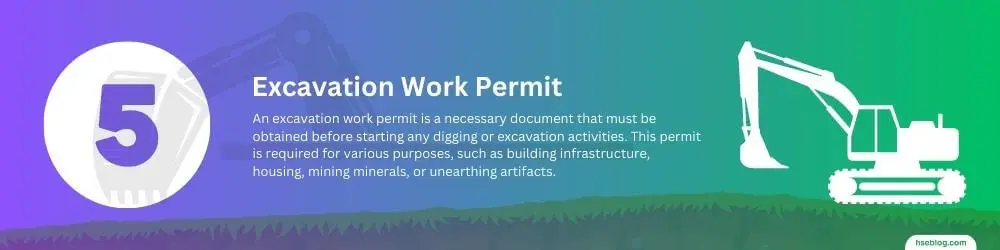
5. Excavation Work Permit
An excavation work permit is a necessary document that must be obtained before starting any digging or excavation activities. This permit is required for various purposes, such as building infrastructure, housing, mining minerals, or unearthing artefacts. The main goal of obtaining an excavation work permit is to ensure the safety of the workers and the surrounding environment by minimizing the potential risks associated with excavation activities.
Some common risks involved in excavation work include:
- Falling into the excavation site.
- Being trapped or engulfed by collapsing soil or materials.
- Accidental explosions are caused by striking underground utilities or improperly stored explosives.
- Exposure to hazardous airborne contaminants, such as dust, asbestos, or other harmful substances.
- Accidents result from the failure of temporary supports or battering.
Here are some examples of excavation permits:
- Trenching permit: This permit is required when excavating a narrow excavation below the ground’s surface. Trenching permits are typically required for utility installation, sewer line repair, and other similar activities.
- Excavation permits for foundations: This permit is required when excavating for a foundation of a building or structure. It is important to ensure that the foundation is constructed on solid ground and that the excavation work is done in a safe and controlled manner.
- Excavation permit for landscaping: This permit is required when excavating for landscaping projects, such as creating a garden bed or installing a pond. Excavation work for landscaping projects should be done carefully to avoid damaging existing plants or trees and to prevent erosion or soil instability.
- Excavation permits for underground storage tanks: This permit is required when excavating to install or remove an underground storage tank, such as for petroleum products or hazardous waste. Excavation work for underground storage tanks should be done cautiously to prevent spills or leaks.
- Excavation permits for archaeological sites are required when excavating areas containing archaeological artefacts or sites. Excavation work for archaeological sites should be done carefully to preserve any artefacts that may be discovered and to comply with laws protecting historical and cultural resources.
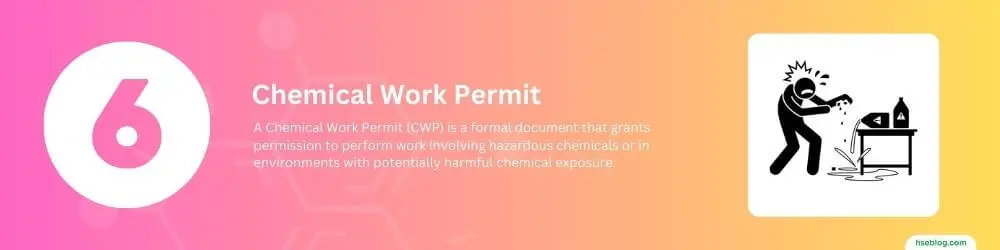
6. Chemical Work Permit
A Chemical Work Permit is a formal document that grants permission to perform work involving hazardous chemicals or in environments with potentially harmful chemical exposure. This permit system is implemented to ensure the safety of workers, the environment, and the surrounding community by minimizing the risk of chemical-related accidents and incidents. Chemical work permits are usually required in industries such as chemical manufacturing, pharmaceuticals, petrochemicals, and research laboratories where hazardous chemicals are handled, stored, or processed.
The main objectives of a Chemical Work Permit are to:
- Establish a systematic process for identifying and assessing chemical-related hazards associated with a particular task.
- Ensure that appropriate safety measures, including engineering controls, personal protective equipment (PPE), and standard operating procedures (SOPs), are in place to mitigate the risks.
- Verify that the individuals involved are trained and competent to safely handle hazardous chemicals.
- Record all chemical-related work activities for future reference and regulatory compliance, including hazard assessments, safety measures, and worker training.
Some examples of tasks that may require a Chemical Work Permit include the following:
- Handling, mixing, or transferring hazardous chemicals: This includes working with chemicals that are toxic, corrosive, flammable, or reactive. A chemical work permit ensures that the workers know the hazards and use the proper safety precautions, such as wearing appropriate PPE, using safety equipment, and following the correct handling procedures.
- Cleaning or maintaining chemical storage or process equipment involves working with equipment that may contain hazardous chemical residues or working in confined spaces with a risk of chemical exposure. A chemical work permit is necessary to ensure that all safety protocols are followed, such as purging and isolating the equipment, ventilating the area, and using the proper PPE.
- Chemical spill response or emergency situations: In a chemical spill or other emergency involving hazardous chemicals, a chemical work permit helps coordinate the response by outlining the roles and responsibilities of the emergency response team and the necessary safety measures and procedures to follow.
- Disposal of hazardous chemical waste: Proper disposal of hazardous waste is essential to prevent environmental contamination and harm to human health. A chemical work permit ensures that the waste is handled, stored, and disposed of according to regulatory requirements and best practices.
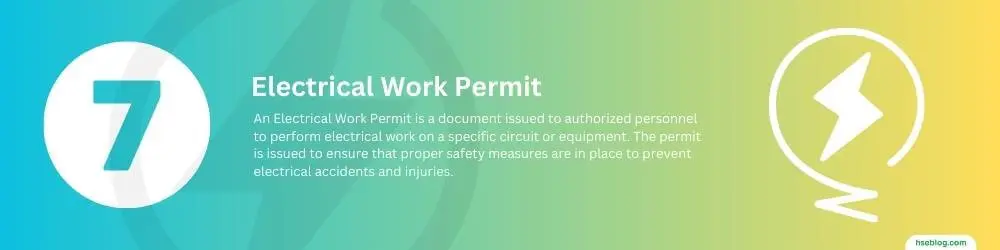
7. Electrical Work Permit
An Electrical Work Permit is a document issued to authorized personnel to perform electrical work on a specific circuit or equipment. The permit is issued to ensure that proper safety measures are in place to prevent electrical accidents and injuries.
Examples of electrical work that may require an Electrical Work Permit include:
- Installing or repairing electrical equipment may include installing or repairing motors, generators, transformers, switchgear, or control panels. A permit ensures that proper safety measures, such as locking and tagging out the equipment, are in place to prevent accidental contact with live electrical parts.
- Electrical maintenance may include cleaning, lubricating, testing, or adjusting electrical equipment. A permit ensures that proper safety measures, such as wearing appropriate PPE and using proper tools, are in place to prevent electrical shocks and burns.
- Troubleshooting electrical problems may involve testing or measuring electrical circuits or equipment to diagnose problems. A permit ensures that proper safety measures, such as de-energizing the equipment and using proper test equipment, are in place to prevent electrical accidents.
- Modifying electrical systems may include adding or removing electrical circuits, changing wiring, or upgrading equipment. A permit ensures proper safety measures, such as disconnecting and isolating the equipment, are in place to prevent electrical hazards.
- Testing and commissioning electrical systems may involve testing newly installed equipment or systems to ensure they function properly. A permit ensures proper safety measures, such as using proper test equipment and following testing procedures, are in place to prevent electrical accidents.
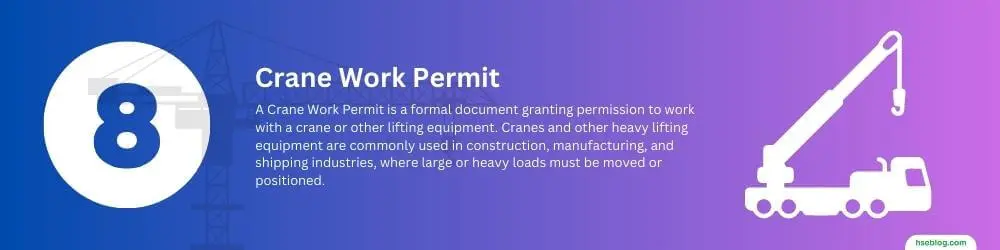
8. Crane Work Permit
A Crane Work Permit is a formal document granting permission to work with a crane or other lifting equipment. Cranes and other heavy lifting equipment are commonly used in construction, manufacturing, and shipping industries, where large or heavy loads must be moved or positioned. Operating cranes and lifting equipment can present significant hazards, including the risk of loads falling, equipment failure, or structural collapse, leading to serious injury or fatality if not properly managed.
The main objectives of a Crane Work Permit are to:
- Identify and assess potential hazards associated with the crane operation, such as equipment malfunction, load instability, or nearby obstacles.
- Ensure that the crane operator and other personnel involved in the lifting operation are adequately trained and competent to perform the work safely.
- Establish appropriate safety measures, including load calculations, rigging inspections, and communication protocols.
- Verify that the crane and lifting equipment is properly maintained, inspected, and certified as required by regulations and manufacturer recommendations.
- Maintain a record of all crane work activities for future reference and regulatory compliance.
Some examples of tasks that may require a Crane Work Permit include:
- Lifting heavy equipment or materials could involve lifting and positioning large machinery, structural components, or other heavy loads at a construction site or manufacturing facility. A crane work permit ensures that the operator knows the load’s weight, the center of gravity, and other factors that may affect its stability during the lift.
- Working near power lines or other overhead obstacles: Crane operations near power lines or other overhead obstacles present the risk of contact, which can result in electrocution or equipment damage. A crane work permit ensures that appropriate safety measures, such as maintaining minimum clearance distances and using signal persons or warning devices, are in place to minimize the risk.
- Lifting personnel using a crane or hoisting equipment: When personnel is lifted using a crane or other hoisting equipment, there is an increased risk of injury due to falls or equipment failure. A crane work permit ensures proper safety measures, such as using approved personnel lifting devices and following manufacturer guidelines for personnel lifting, are in place.
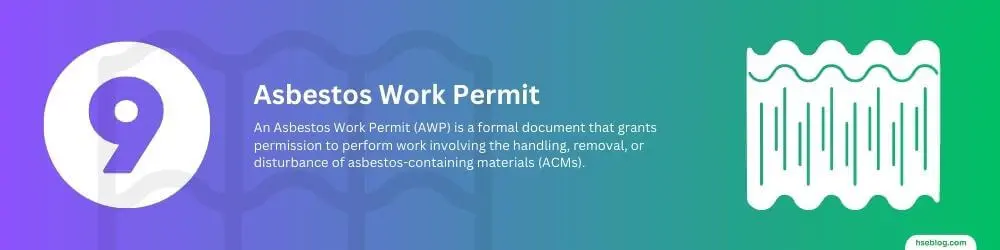
9. Asbestos Work Permit
An Asbestos Work Permit is a formal document granting permission to perform work involving handling, removing, or disturbing asbestos-containing materials (ACMs). Asbestos is a naturally occurring fibrous mineral widely used in construction, insulation, and other applications due to its heat-resistant and insulating properties. However, inhaling asbestos fibers can cause severe health issues, such as asbestosis, lung cancer, and mesothelioma. As a result, strict regulations and safety protocols have been implemented to protect workers and the public from exposure to asbestos fibers.
The main objectives of an Asbestos Work Permit are to:
- Identify and assess potential hazards associated with asbestos-related work, such as the release of asbestos fibers or the spread of contamination.
- Ensure that workers involved in asbestos-related work are adequately trained and competent to perform the tasks safely and comply with relevant regulations.
- Establish appropriate safety measures, including containment, ventilation, wet methods, and personal protective equipment (PPE), to minimize the risk of asbestos exposure.
- Verify that proper procedures for the disposal of asbestos waste are followed to prevent environmental contamination and protect public health.
- Maintain a record of all asbestos work activities for future reference and regulatory compliance.
Some examples of tasks that may require an Asbestos Work Permit include the following:
- Removal or abatement of asbestos-containing materials: This involves the removal of asbestos-containing insulation, tiles, or other materials during building renovations, demolition, or maintenance. An asbestos work permit ensures that workers follow proper removal procedures, such as using wet methods to suppress dust and wearing appropriate PPE, including respirators and protective clothing.
- Repair or encapsulation of damaged asbestos-containing materials: In some cases, asbestos-containing materials may be repaired or encapsulated to prevent the release of asbestos fibers. An asbestos work permit ensures that workers follow proper repair or encapsulation procedures and take necessary precautions to prevent exposure to asbestos fibers.
- Inspection or sampling of suspected asbestos-containing materials: Inspections and sampling of materials to determine the presence of asbestos may involve disturbing the material and releasing asbestos fibers. An asbestos work permit ensures that workers conducting these activities are trained in proper sampling techniques and follow necessary safety precautions to minimize the risk of exposure.
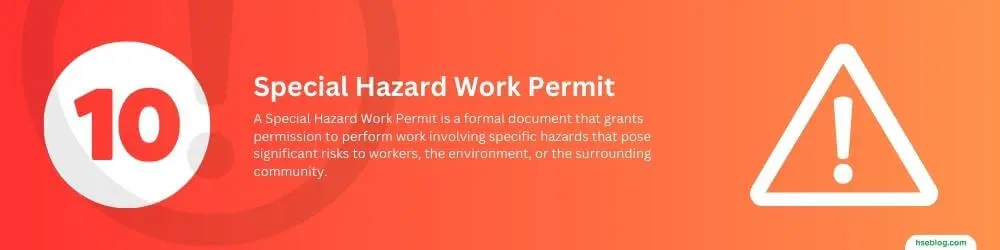
10. Special Hazard Work Permit
A Special Hazard Work Permit is a formal document that grants permission to perform work involving specific hazards that pose significant risks to workers, the environment, or the surrounding community. These permits help ensure proper safety measures, training, and procedures are in place to minimize the risk associated with these hazards. Special hazard work permits are commonly required in construction, utilities, nuclear power, and chemical manufacturing industries.
Some examples of tasks that may require a Special Hazard Work Permit include:
- Extremely hazardous conditions could involve working in environments with extreme temperatures, high noise levels, or other physical hazards. A particular hazard work permit ensures that workers are adequately trained and equipped with appropriate personal protective equipment (PPE) and follow established safety protocols to minimize the risk of injury or illness.
- Radioactive materials: Handling, storing, or disposing of radioactive materials requires specialized training and safety measures to protect workers and the environment from exposure to ionizing radiation. A particular hazard work permit ensures that workers handling radioactive materials are properly trained and follow specific safety procedures, such as using radiation monitors, wearing dosimeters, and employing shielding techniques.
- Dangerous chemicals: As previously mentioned, handling, storing, or working with hazardous chemicals may require a Chemical Work Permit. In some cases, a Special Hazard Work Permit might be used instead or in addition to a Chemical Work Permit, mainly if the chemicals involved are highly toxic, reactive, or pose a significant risk to human health or the environment.
- Power supplies: Working with high-voltage electrical systems, such as power lines or electrical panels, poses a risk of electrocution or arc flash incidents. A particular hazard work permit for electrical work ensures that workers are qualified and trained in electrical safety, follow lockout/tagout procedures, use appropriate PPE, and adhere to established safety protocols for working around live electrical systems.
Conclusion
Permit-to-work systems are essential safety management tools used to control high-risk activities in the workplace. These systems ensure that all necessary safety measures are in place before work begins and that workers are adequately trained and competent to perform the work safely. Several types of permit-to-work systems are designed to address specific hazards and risks associated with different work activities.
From confined space permits to crane work permits, chemical work permits, and hot work permits, each permit has a unique set of requirements and safety protocols that must be followed to ensure the safe and efficient completion of the work.