In industrial settings where heavy machinery and rapid mechanical movements are part of daily operations, worker safety must be a top priority. One of the most effective and reliable methods of protecting machine operators is the use of two-hand control systems. These systems are designed to ensure that an operator’s hands are safely positioned away from hazardous areas during machine cycles, dramatically reducing the risk of serious injuries like amputations and crush incidents.
This comprehensive guide will walk you through everything you need to know about two-hand controls — from how they work, where they are used, and why they are crucial for workplace safety to the components, design considerations, standards, and even common misconceptions.
By the end, you’ll understand why two-hand controls are not just another safety feature but an essential safeguard that can save lives and maintain productivity.
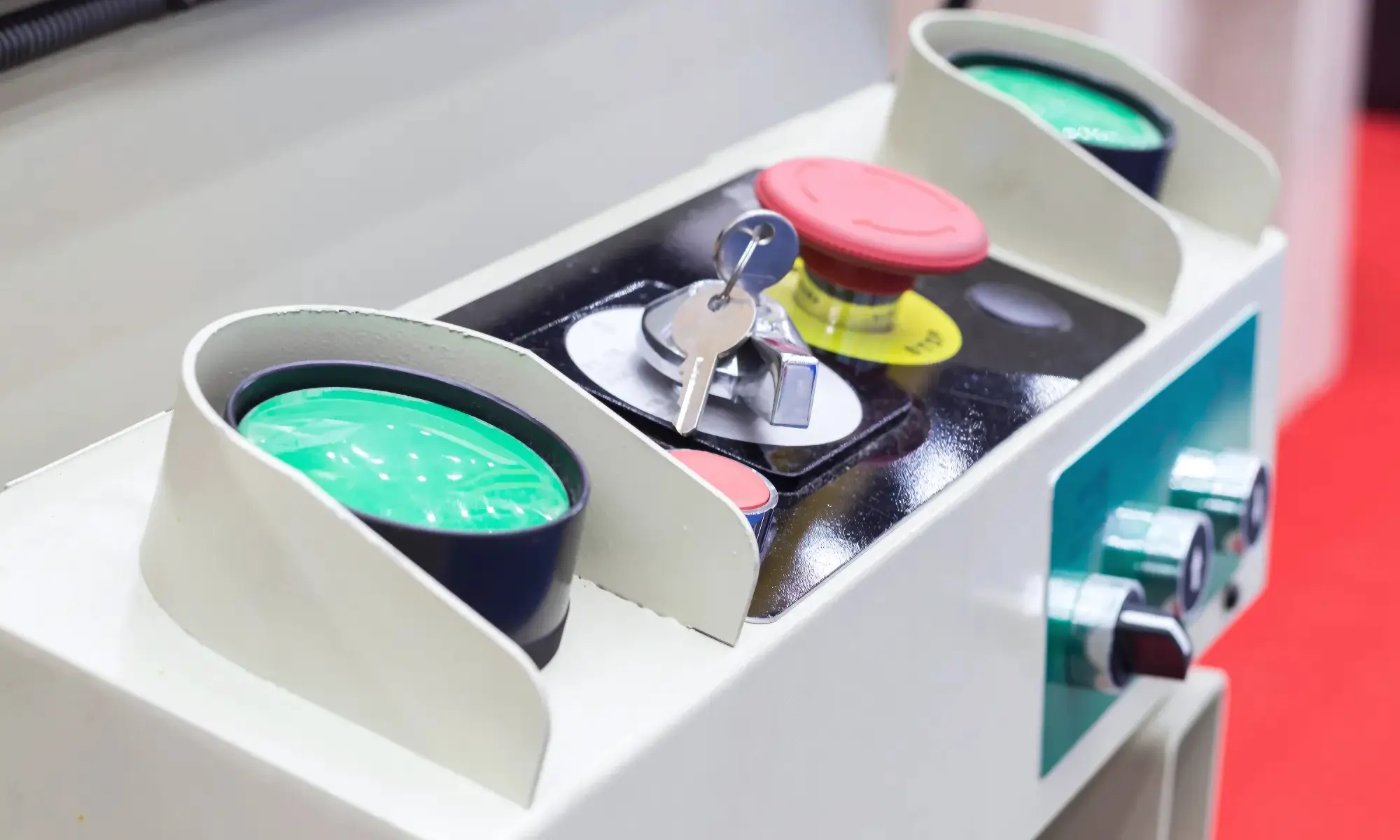
What Are Two-Hand Controls?
Two-hand controls are safety devices designed to require both of an operator’s hands to simultaneously activate and maintain the operation of a machine. This simple but highly effective mechanism ensures that the operator’s hands are safely positioned away from hazardous areas during machine activity, minimizing the risk of serious injuries such as amputations, crush injuries, and lacerations.
Unlike other safety measures that might rely on guards or warning signs, two-hand controls directly govern the act of machine operation itself — making it nearly impossible for a user to accidentally or intentionally bypass the system without risking a shutdown.
Why Two-Hand Controls Are Essential for Workplace Safety
Two-hand control systems are not just an optional add-on — they are often mandated by workplace safety regulations for high-risk machinery.
Here’s why they matter:
- Guarantees hand safety: Ensures hands are out of danger when machinery is activated.
- Prevents accidental starts: Reduces incidents of machines starting unintentionally.
- Encourages operator focus: Requires active, conscious engagement with the machine.
- Meets legal standards: Compliance with OSHA, ANSI, and ISO standards often demands safeguarding systems like two-hand controls.
Without two-hand controls, even experienced workers may face life-changing injuries due to simple human error or distraction.
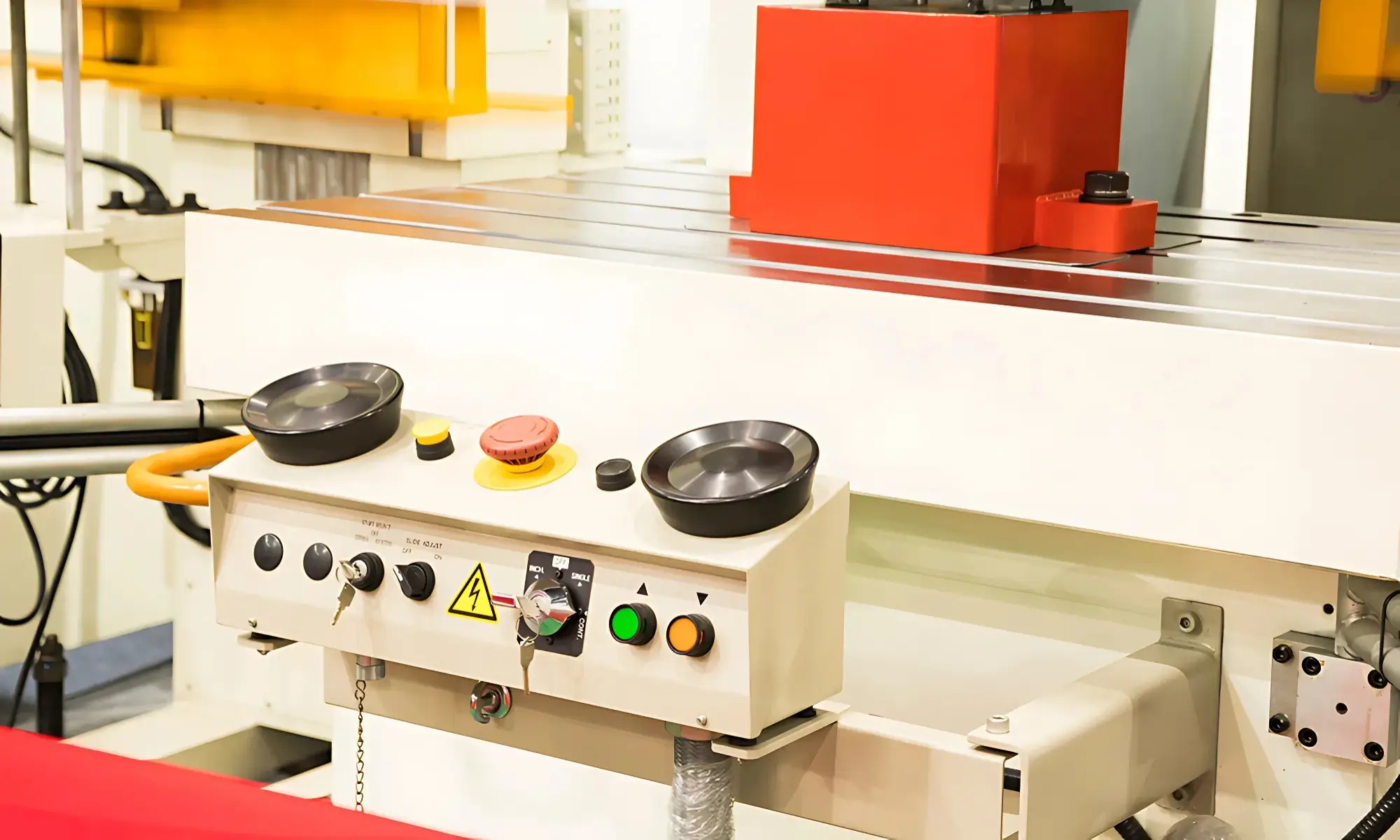
How Do Two-Hand Controls Work?
The basic principle is straightforward:
- The operator must press two separate control buttons (or levers) at the same time.
- Both controls must be continuously pressed during the dangerous phase of machine operation.
- If one or both controls are released, the machine immediately stops or enters a safe state.
This system forces the operator’s hands to stay occupied, reducing the chance that one hand might accidentally drift into a hazardous zone.
Advanced two-hand controls often include:
- Anti-tie-down functionality (to prevent users from taping or jamming one control in place),
- Anti-repeat features (requiring both controls to reset before the next cycle),
- Timing constraints (both buttons must be pressed within a small window, such as 0.5 seconds).
Example: In a metal stamping press, the operator must press both hand controls to lower the press. Removing one hand stops the machine instantly, ensuring the operator’s hands cannot be trapped beneath the stamp.
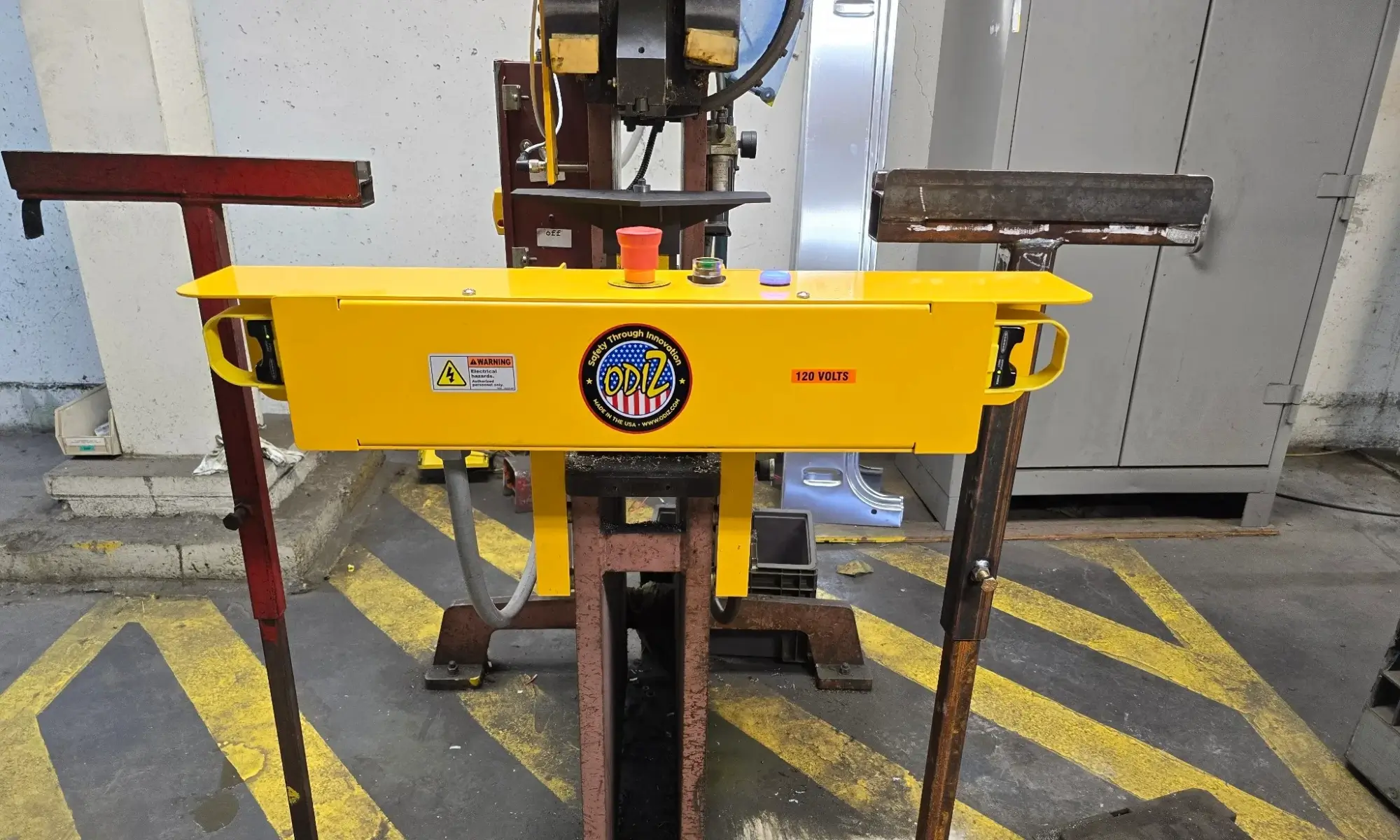
Two-Hand Control Components
A two-hand control system is more than just two buttons — it’s a thoughtfully engineered combination of components that work together to protect the operator and control the machine safely.
Each part plays a specific role in ensuring the system is reliable, tamper-proof, and effective.
Here’s a breakdown of the key components you’ll typically find in a two-hand control setup:
1. Actuator Devices (Buttons, Levers, or Switches)
These are the physical controls the operator interacts with — usually two push buttons.
They must be:
- Durable enough for industrial environments,
- Easy to operate without excessive force,
- Positioned ergonomically for simultaneous, comfortable use.
Tip: Many designs use mushroom-style push buttons because they are large, easy to hit quickly, and reduce the chance of accidental slips.
2. Control Logic Circuit (Safety Relay or Safety PLC)
At the heart of the system is the logic controller.
It monitors both actuators and verifies:
- Both buttons were pressed within a set time window,
- Both buttons remain pressed during the hazardous operation,
- No tampering (such as holding one button permanently) occurs.
If any safety condition is violated, the control logic immediately sends a stop command to the machine.
Tip: Safety relays or safety-rated programmable logic controllers (PLCs) are typically used to meet regulatory safety requirements (such as ISO 13849-1).
3. Anti-Tie-Down and Anti-Repeat Circuits
Built into the control logic, these features ensure:
- Both buttons must be released and pressed anew for every machine cycle (anti-repeat),
- The operator cannot “tie down” one button while operating the machine with only one hand (anti-tie-down).
Without these circuits, the system would be vulnerable to misuse, defeating the safety purpose.
4. Output Devices (Machine Actuation Controls)
When the two-hand control system confirms all safety conditions are met, it sends a signal to start the machine’s hazardous motion — usually through a contactor, motor starter, or hydraulic valve.
If the operator releases either button, the system instantly stops the hazardous motion by opening the output circuit.
Tip: The output devices must be fast-acting and fail-safe to ensure immediate machine stoppage when needed.
5. Monitoring and Diagnostic Indicators
Many two-hand control systems feature built-in status lights or indicators to show:
- Both buttons are pressed correctly,
- The system is ready,
- Faults or errors are detected.
These indicators help operators and maintenance staff quickly recognize system status and address any issues before restarting operations.
Tip: Some modern systems include diagnostic outputs that can connect to maintenance dashboards for proactive fault detection.
6. Enclosure and Mounting Hardware
Finally, all components — especially the actuators and logic units — must be enclosed in rugged, tamper-proof housings rated for the operating environment (dustproof, waterproof, and vibration-resistant).
The controls must also be securely mounted at a safe and calculated distance from the hazardous area to prevent an operator from reaching into danger while pressing the buttons.
A reliable two-hand control system consists of actuators, safety logic, anti-tamper circuits, machine actuation outputs, status indicators, and durable enclosures — all working together to ensure that machine operations cannot occur unless the operator is fully engaged and hands are safely out of harm’s way.
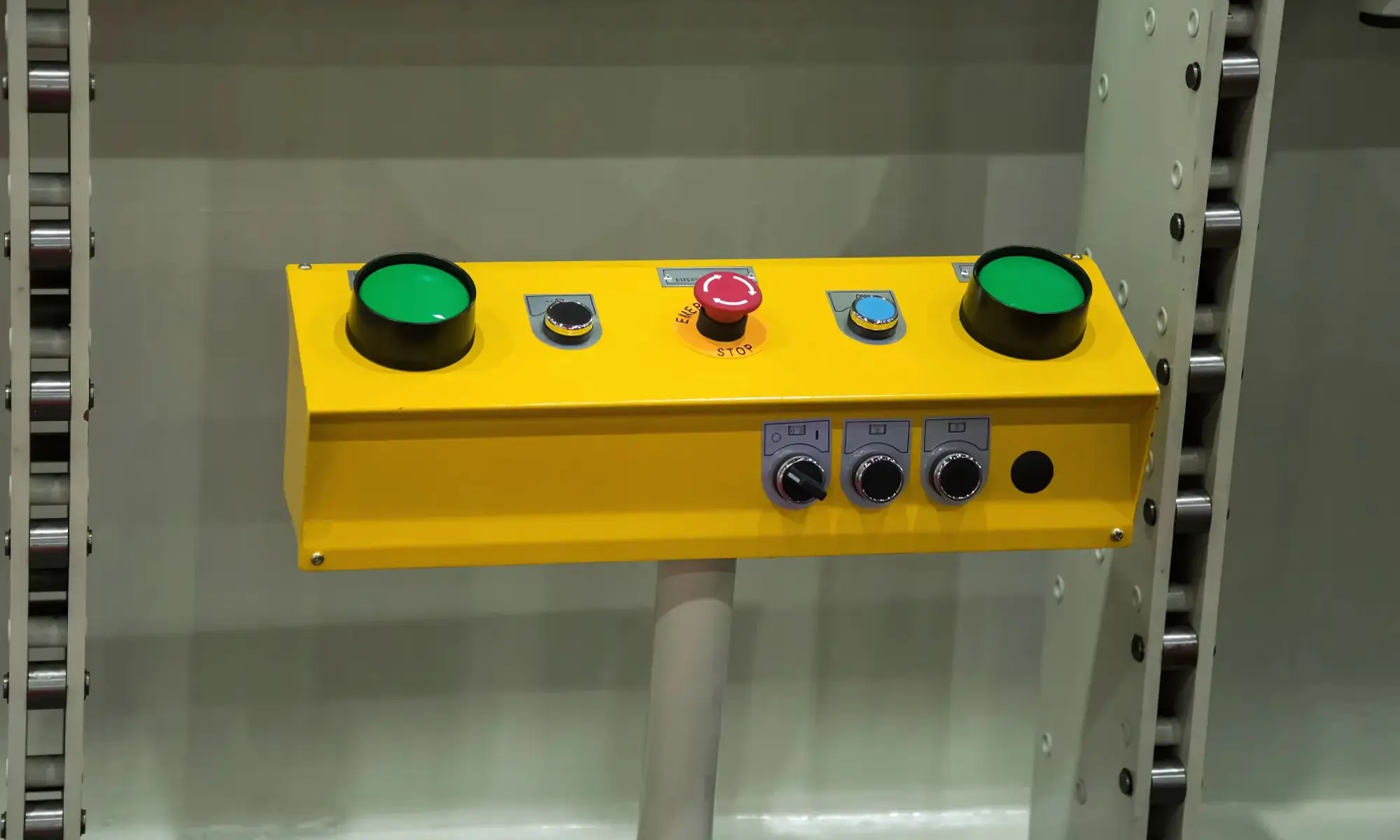
Applications of Two-Hand Controls
Two-hand controls are widely used across industries where machinery poses a significant risk to the operator’s hands during operation. Their primary role is to safeguard workers by ensuring both hands are occupied away from hazardous areas when a machine is running. Here’s where you’ll commonly find two-hand control systems:
1. Mechanical Power Presses
Mechanical power presses used in metalworking — for tasks like stamping, forming, and punching — often involve fast, forceful downward motion that can cause severe hand injuries.
Two-hand controls ensure that the operator’s hands are away from the die area during each cycle, greatly reducing the chance of accidental amputation or crushing.
2. Hydraulic Presses
In industries like automotive manufacturing and heavy equipment production, hydraulic presses are used to bend, shape, or compress materials.
Here, two-hand controls are critical because the tremendous pressure exerted by these machines leaves no margin for error.
3. Plastic Molding Machines
Plastic injection molding and compression molding machines involve large, moving molds that can trap or crush hands if safety measures fail.
Two-hand controls make sure the operator must engage both hands simultaneously, preventing accidental hand placement between moving molds.
4. Die Cutting and Punching Machines
These machines are used in making parts from sheet metal, plastics, rubber, and even textiles.
Since they often have sharp dies moving at high speed, two-hand controls protect operators by making it impossible to reach into the cutting zone during operation.
5. Press Brakes
Press brakes are used for bending metal sheets. Operators must often handle large, flexible materials, which increases the risk of hands entering danger zones.
Two-hand controls, combined with proper guarding, ensure that operators cannot inadvertently move hands into hazardous areas during the bend cycle.
6. Robotic and Automated Systems
In some robotic work cells, two-hand controls are used as a manual override or maintenance tool.
Operators must safely position themselves before starting or reactivating the robot, especially during manual interventions.
In Short, Whenever a machine’s operation could crush, cut, or injure hands due to sudden movements, two-hand controls are applied to enforce safe hand positioning and prevent accidents.
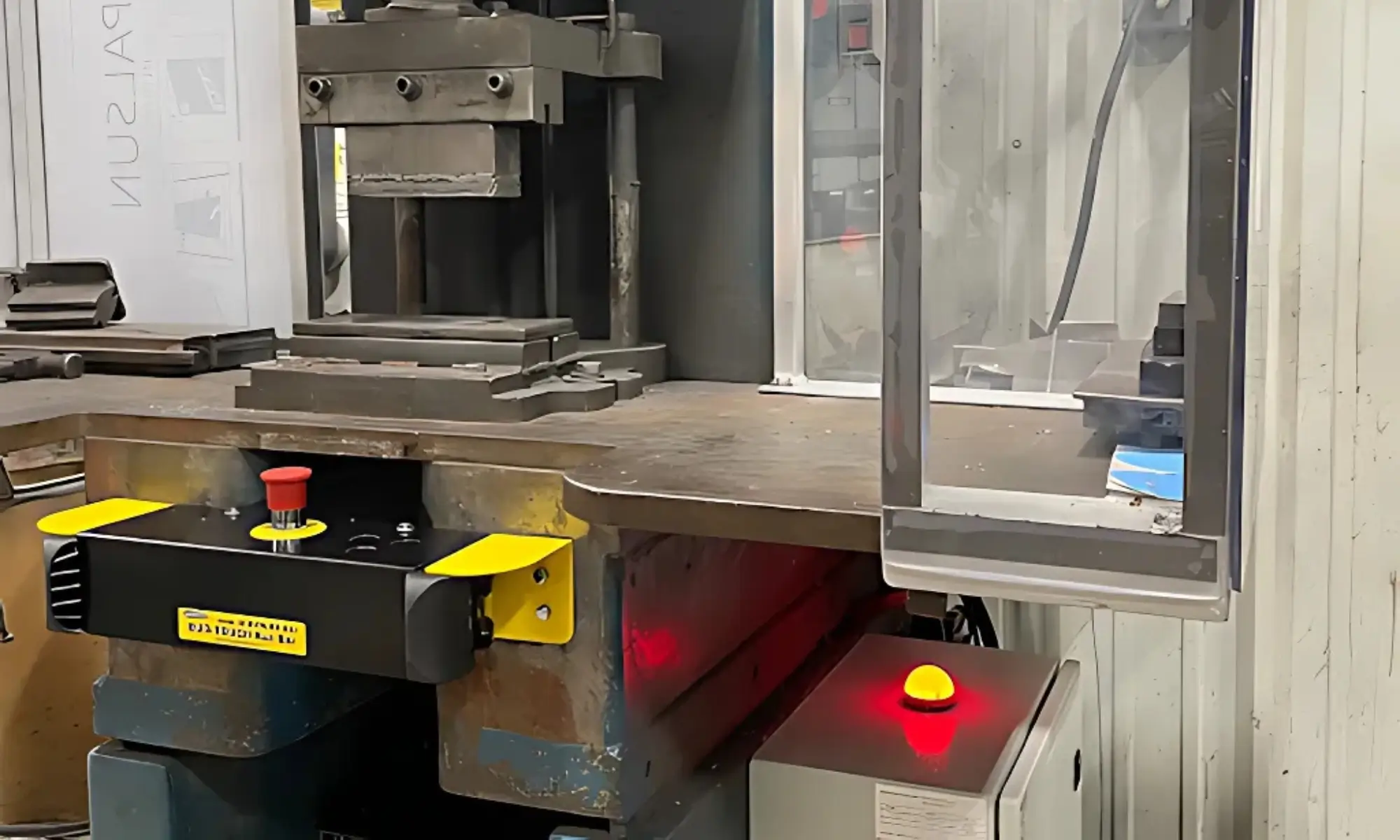
Important Design Considerations for Two-Hand Controls
Designing two-hand control systems isn’t just about placing two buttons on a machine. For these systems to be effective, they must be carefully engineered to match safety standards, worker ergonomics, and the specific hazards of the machine they’re safeguarding. Poorly designed controls can introduce new risks or fail to protect operators properly. Here are the key considerations every designer, engineer, or safety manager must focus on:
1. Control Positioning and Safety Distance
Two-hand controls must be placed far enough away from the machine’s point of operation so that the operator cannot reach hazardous areas while keeping both buttons pressed.
This “safety distance” ensures that even if the operator stretches or leans, their hands remain safely outside the danger zone.
Tip: Follow OSHA or ISO guidelines for calculating minimum safety distances based on machine speed and worker reach.
2. Simultaneous Activation Timing
Both controls must be activated at the same time — usually within a very small window (for example, 0.5 seconds).
This prevents “cheating” the system by pressing one button and then the other later, which could defeat the purpose of hand safety.
Tip: Timing circuits should reject the start signal if one button is pressed before the other outside the allowed window.
3. Anti-Tie-Down and Anti-Repeat Features
Operators must not be able to “tie down” one button using tape, weights, or mechanical fixtures.
Anti-tie-down circuits detect if one button remains pressed too long without a cycle reset and block the machine from starting.
Similarly, anti-repeat features ensure the operator must release both buttons before beginning a new cycle — preventing automatic restarting without active engagement.
4. Ergonomic Design
The control devices must be easy and comfortable to operate, even during long shifts.
Controls that require excessive force, awkward body positioning, or repetitive strain can cause operator fatigue, leading to reduced productivity and increased injury risk.
Tip: Controls should be reachable without leaning or straining and should fit naturally within an operator’s normal arm reach zone.
5. Mechanical and Electrical Reliability
Two-hand controls must be rugged enough to withstand industrial environments: vibration, dust, moisture, oil, and temperature extremes.
Additionally, the system must be fail-safe: if a fault occurs (e.g., a button sticks or wiring is damaged), it must default to a safe, non-operational state.
Tip: Use components rated for the environment (e.g., IP65 enclosures for wet areas).
6. Visibility and Marking
The two-hand control devices must be clearly marked and visible to the operator. Color coding (such as green for start and red for stop) and labeling help reduce confusion, especially in multi-operator or multilingual work environments.
Tip: Install proper signage explaining how the controls function and why they are essential.
7. Regular Testing and Maintenance
A two-hand control system is only as good as its maintenance.
Regular inspections must verify that controls are responsive, tamper-proof, and in good working order. Any wear, sticking, or electronic faults must be corrected immediately.
Tip: Integrate two-hand control testing into your machine’s standard pre-shift safety checklist.
In Short, A properly designed two-hand control system prioritizes safe placement, ergonomic operation, tamper-proof circuits, and regular testing to deliver true hand protection without interfering with productivity.
Standards Governing Two-Hand Controls
Several international safety standards provide specific guidelines for designing and implementing two-hand controls:
- OSHA (Occupational Safety and Health Administration): Particularly in mechanical power presses (29 CFR 1910.217), OSHA outlines detailed requirements for two-hand control devices.
- ANSI B11.1: Covers the safety of mechanical power presses, including the use of two-hand trip devices.
- ISO 13851: Defines the requirements for the design, construction, and selection of two-hand control devices for safeguarding machinery.
Following these standards ensures that the two-hand system isn’t just functional — it’s reliable and verifiably safe under real-world conditions.
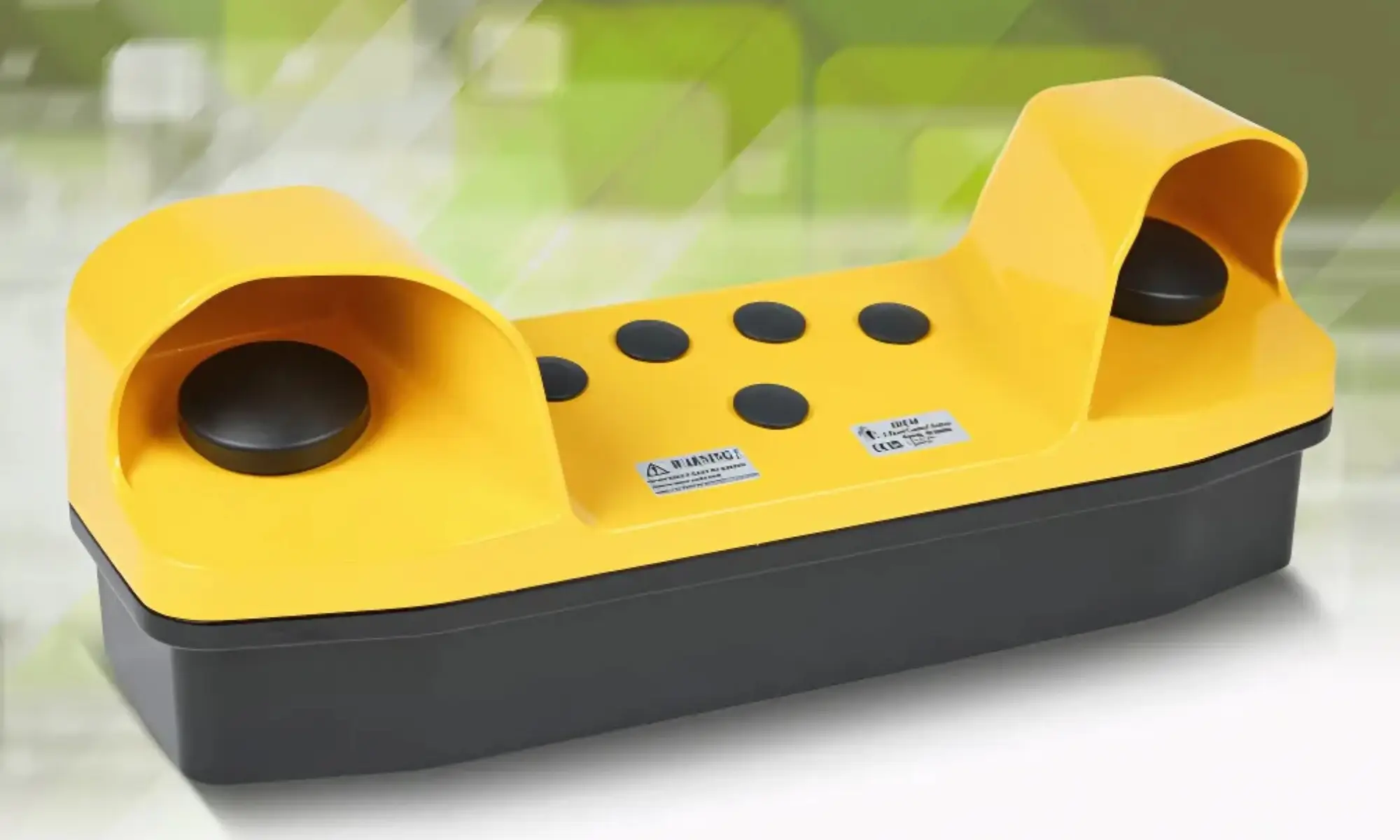
Common Misconceptions About Two-Hand Controls
While two-hand control systems are a proven and effective safety measure, several misunderstandings still exist about their purpose, effectiveness, and implementation. Addressing these misconceptions is critical for improving workplace safety culture and ensuring these systems are correctly used. Here are some of the most common myths — and the reality behind them:
1. “Two-hand controls slow down production.”
Modern two-hand controls are designed for ergonomic efficiency and minimal interference with workflow.
When properly installed, they add only a fraction of a second to each cycle — a tradeoff that is well worth it to protect workers from devastating injuries. In fact, they can increase productivity over time by reducing injury-related downtime and boosting worker confidence.
2. “Experienced workers don’t need two-hand controls.”
Experience does not eliminate the risk of accidents. Even seasoned operators can suffer lapses in focus due to fatigue, stress, or distractions.
Two-hand controls act as a fail-safe that protects everyone — regardless of their experience level — from unpredictable human errors.
3. “Guarding is enough without two-hand controls.”
While physical guards are important, they serve a different purpose. Guards create a barrier; two-hand controls control the operation of hazardous machinery.
In many cases, regulatory standards require both guarding and two-hand controls for comprehensive safety, especially in machines like mechanical power presses.
4. “It’s easy to bypass two-hand controls, so why bother?”
Properly designed two-hand controls include anti-tie-down, anti-repeat, and monitoring circuits to prevent cheating or bypassing.
When systems are installed and maintained correctly and backed by a strong safety culture, they offer a highly reliable layer of protection that is difficult to defeat without obvious tampering — which itself can be detected during regular inspections.
5. “Two-hand controls are outdated with modern technology.”
Two-hand controls remain fundamental to modern industrial safety, often used alongside advanced technologies like light curtains, interlocks, and safety PLCs (Programmable Logic Controllers).
They are a proven, low-cost, and highly effective method of safeguarding that complements — not replaces — more complex systems.
Key Insight: Two-hand controls are not an outdated or inconvenient safety feature. They are an essential, efficient, and legally required safeguard that significantly reduces the risk of serious workplace injuries.
Conclusion
Two-hand control systems embody the best of industrial safety design: simple, intuitive, effective, and mandatory where lives are at stake. They remind us that no machine operation, however routine, should compromise worker safety. Implementing two-hand controls doesn’t just meet regulatory standards — it demonstrates a company’s deep commitment to the well-being of its workforce.
Whether you’re designing a new manufacturing line or upgrading existing equipment, investing in a properly installed and maintained two-hand control system could be one of the smartest safety decisions you can make.
Key Takeaways:
- Two-hand controls keep both hands safe during dangerous machine operations.
- Compliance with OSHA, ANSI, and ISO standards is essential.
- Proper design and maintenance are crucial for their effectiveness.
- They significantly reduce the risk of workplace injuries and costly downtime.