No matter how skilled, experienced, or careful a person may be, mistakes are a natural part of human behavior. From a misplaced keystroke to a critical decision based on faulty assumptions, human error is one of the most common and costly contributors to accidents, failures, and safety incidents, especially in high-risk industries like aviation, healthcare, construction, and manufacturing.
But human error is rarely about carelessness or incompetence. It often results from poor system design, unclear procedures, fatigue, or overwhelming work conditions. That’s why understanding human error, why it happens, and how to prevent it is crucial for creating safer, more resilient workplaces.
In this blog, you’ll learn:
- What does human error really mean
- The different types of human error and how they occur
- Real-world examples from various industries
- Common causes and contributing factors
- Proven strategies to reduce or manage errors effectively
Whether you’re a safety professional, team leader, system designer, or simply interested in human factors, this article will equip you with practical insights to improve safety, performance, and reliability. Let’s dive in.
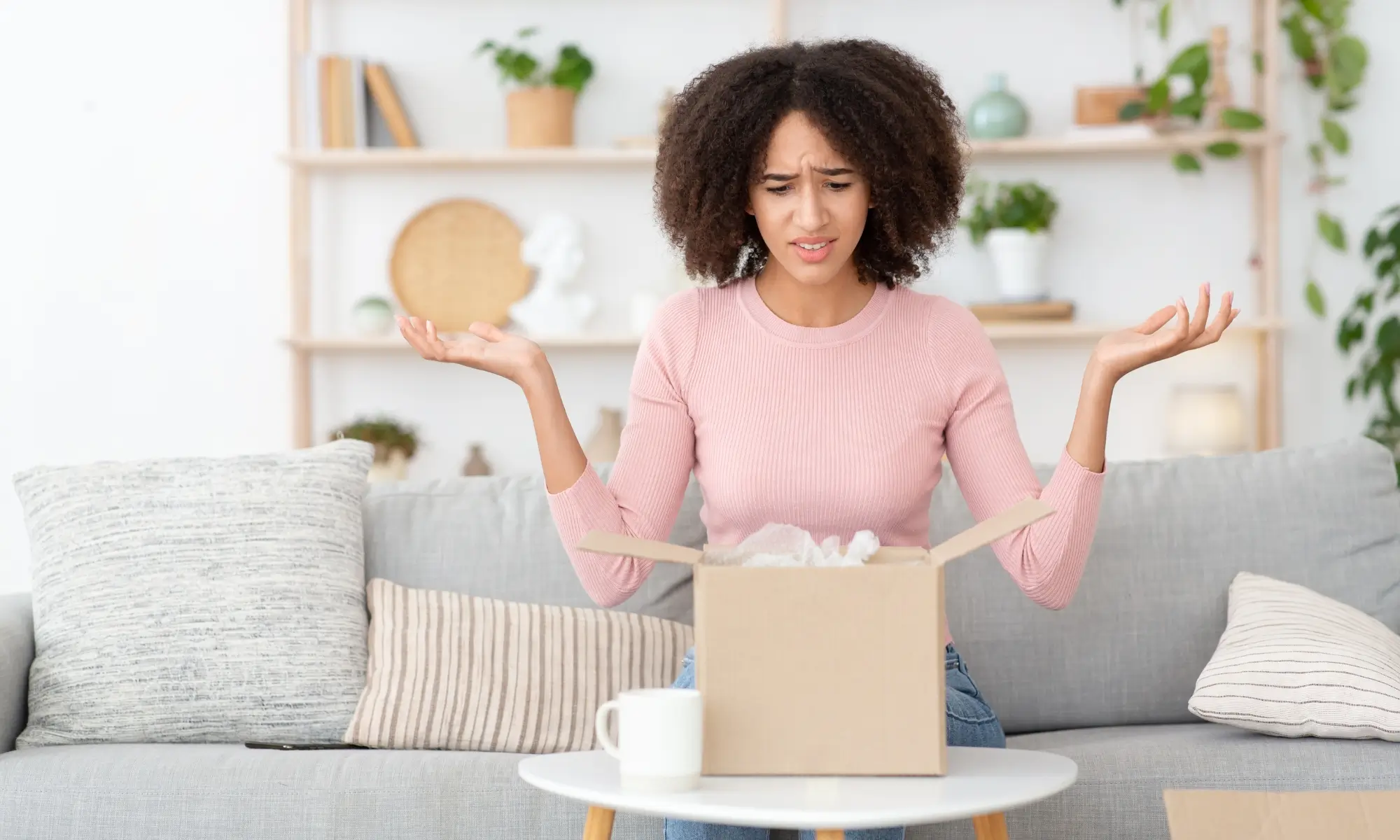
What Is Human Error?
Human error refers to an action or decision that was not intended or desired by a set of rules or observers or that led the task or system beyond its acceptable limits.
Human error occurs when someone does something they didn’t mean to do, forgets to do something important, or makes a poor decision due to misunderstanding or misjudgment.
Importantly, not all failures are human errors. The outcome may not qualify as an error if there was no intention or plan to achieve a particular result.
Why Human Error Matters
Human error is a leading cause of workplace accidents, system failures, and safety incidents. According to the UK’s Health and Safety Executive (HSE), human error is often the underlying cause in the majority of workplace accidents. However, errors are not just a result of individual carelessness—they usually stem from deeper issues in system design, training, or work conditions.
Even a small error can trigger cascading failures in complex systems. Designing systems anticipating and tolerating human error can dramatically reduce risks and improve outcomes.
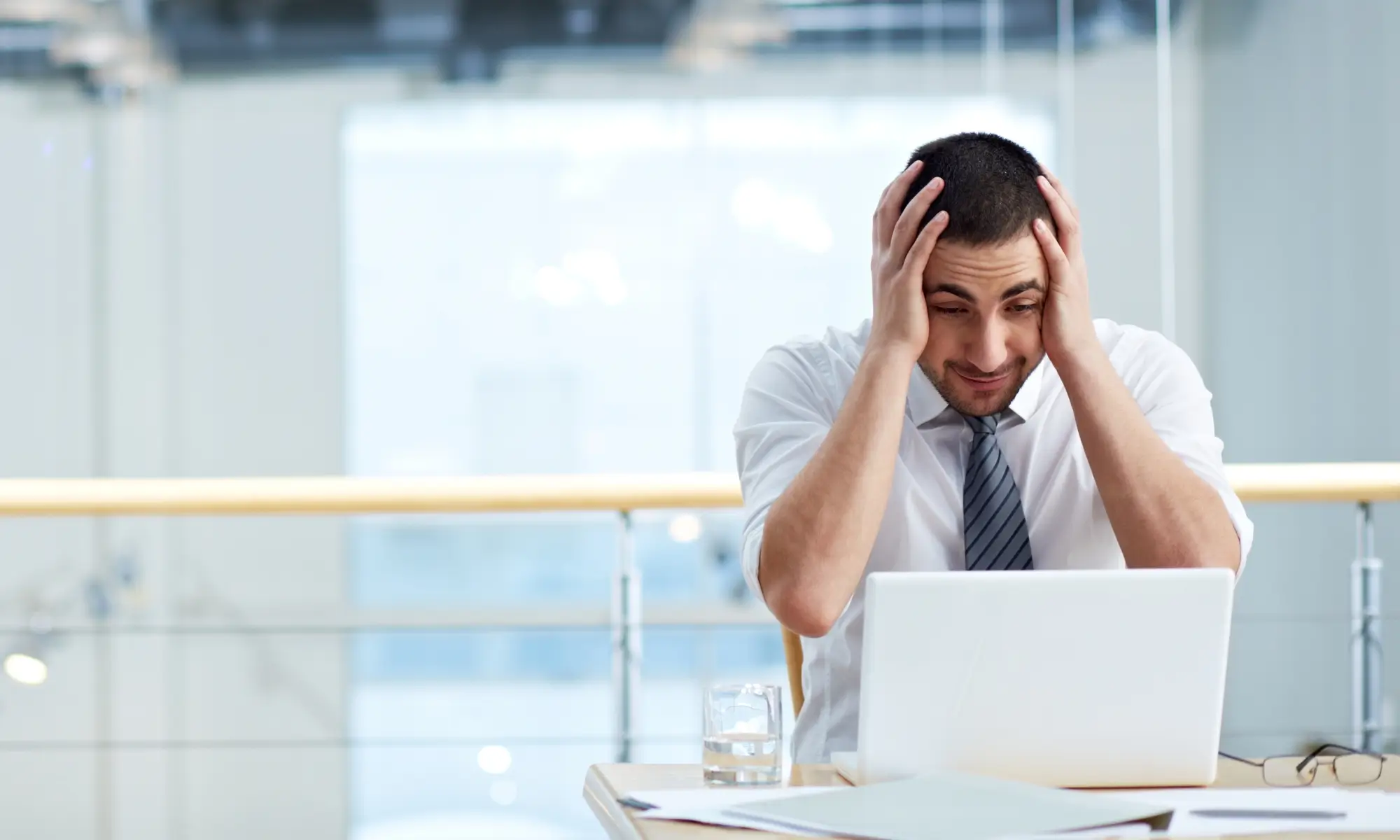
Types of Human Errors
Experts like James Reason, Don Norman, and Erik Hollnagel have categorized human errors into three main types: slips, lapses, and mistakes. Each relates to a different part of the human cognitive process.
1. Slips (Execution Errors)
A slip happens when a person intends to perform the correct action but fails to execute it properly. The plan is sound, but the movement, operation, or interaction doesn’t align with it.
Cause:
- Distractions (e.g., noise, interruptions)
- Loss of focus or divided attention
- Perceptual errors (e.g., misreading a label)
Nature:
- Slips are observable.
- They often result in immediate feedback that something went wrong.
- Users usually recognize the error right away.
Examples:
- A factory operator means to press the “Start” button on a machine but accidentally presses the “Stop” button due to button placement.
- A user means to email “John” but clicks “Joan” by mistake due to autocomplete suggestions.
- A driver signals left but turns right because of distraction.
Design Implications:
Design systems with error-tolerant features that help users:
- Undo actions (e.g., “Undo Send” in email)
- Confirm critical operations (e.g., “Are you sure you want to delete this file?”)
- Visually distinguish similar functions or inputs (e.g., color coding, spacing)
2. Lapses (Memory Failures)
A lapse occurs when a person forgets to carry out a planned action or loses track of part of the task. Unlike slips, the error lies in memory, not execution.
Cause:
- Fatigue
- Cognitive overload or multitasking
- Stress or interruptions
- Routine tasks leading to autopilot behavior
Nature:
- Internal and less visible to others.
- Often goes unnoticed until consequences emerge.
- May involve forgetting steps, losing place, or missing cues.
Examples:
- An engineer forgets to close a valve after equipment testing.
- A worker omits a step in a safety inspection checklist.
- A surgeon skips a final instrument count because of an emergency distraction.
Design Implications:
To support memory and prevent lapses:
- Use checklists and step-by-step procedures.
- Implement task reminders or alerts.
- Automate repetitive steps where appropriate.
- Design interfaces that help users keep track of progress (e.g., progress bars, step indicators).
3. Mistakes (Planning Errors)
A mistake happens when a person executes a plan correctly, but the plan itself is flawed. It’s not an issue of memory or attention—it’s a misjudgment or misunderstanding.
Cause:
- Incomplete or incorrect knowledge
- Flawed assumptions or mental models
- Inexperience or insufficient training
- Misinterpretation of available information
Nature:
- Intentional actions that are appropriate for the person’s goal—but based on faulty reasoning.
- Can be harder to detect, especially if the result appears reasonable at first.
Examples:
- A nurse administers the wrong dosage of medication due to misreading the chart.
- A team evacuates to the wrong zone during a drill because they misread the site map.
- An IT technician follows an outdated procedure, leading to a system crash.
Design Implications:
To reduce planning errors:
- Provide accurate, real-time information to support decisions.
- Offer guidance, training, and contextual help.
- Use clear labels, consistent logic, and intuitive layouts.
- Enable simulation or training environments to build correct mental models.
Type | What Goes Wrong | Cause | Visibility | Prevention |
---|---|---|---|---|
Slip | Action | Execution error | High | Safeguards, undo, confirmation dialogs |
Lapse | Memory | Forgetting or omitting | Low | Checklists, reminders, automation |
Mistake | Planning | Misjudgment or knowledge gap | Medium | Training, clear info, intuitive systems |
Understanding these types of errors helps designers, supervisors, and safety professionals anticipate failure points and build error-resilient systems that protect users, workers, and the public.
Additional Error Types
Some frameworks also include:
- Violations – Deliberate deviations from rules or procedures (not necessarily malicious; often well-intentioned shortcuts).
- Latent Errors – Hidden system-level flaws that lie dormant until triggered.
- Knowledge-Based Errors – Errors made due to a lack of understanding in unfamiliar situations.
- Rule-Based Errors – Misapplying a rule to the wrong situation.
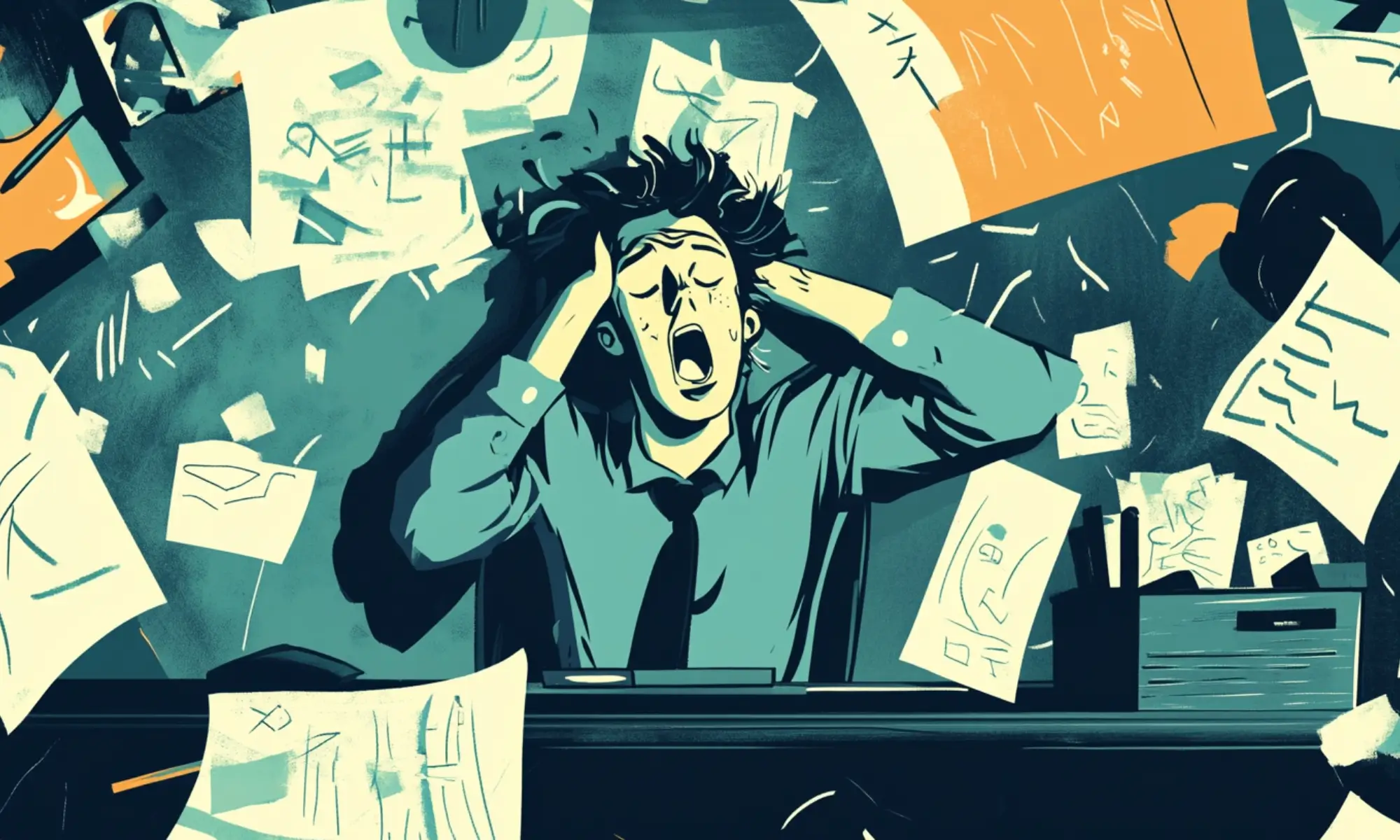
Causes of Human Error
Human error doesn’t happen randomly—it usually stems from cognitive, environmental, organizational, and individual factors. Understanding these causes helps organizations reduce risks, improve safety, and build more error-resistant systems. Here are the key causes of human error:
1. Inadequate Training or Knowledge
When individuals lack the proper knowledge or skills to perform a task, they’re more likely to make planning or rule-based mistakes.
Examples:
- Misinterpreting a procedure due to insufficient onboarding.
- Applying the wrong rule to a situation due to a lack of training.
Solution: Regular, hands-on training tailored to job roles and complexity.
2. Poorly Designed Systems or Interfaces
Complex, inconsistent, or unintuitive system design increases the chance of slips and mistakes.
Examples:
- Similar-looking buttons are placed close together.
- Lack of visual cues or confirmation messages for critical actions.
Solution: Apply human-centered design principles; test systems for usability.
3. Fatigue and Overwork
Physical and mental fatigue impairs attention, memory, and decision-making, leading to lapses, slips, or delayed reactions.
Examples:
- Forgetting a safety step due to long shifts.
- Falling asleep during monotonous monitoring tasks.
Solution: Enforce work-hour limits, schedule breaks, and rotate tasks.
4. Distractions and Interruptions
Interruptions shift focus away from the task, increasing the likelihood of execution errors or forgetting crucial steps.
Examples:
- Answering a phone call in the middle of data entry.
- Pausing a procedure due to a question, then skipping a step.
Solution: Minimize workplace distractions; encourage “focus zones” for critical tasks.
5. Time Pressure and Unrealistic Deadlines
Under pressure, individuals may rush or cut corners, which leads to slips, lapses, or even violations (intentional rule-breaking).
Examples:
- Skipping equipment checks to meet a delivery deadline.
- Ignoring a safety rule to speed up production.
Solution: Set achievable goals and promote a “safety over speed” culture.
6. Repetitive or Monotonous Tasks
Performing the same tasks repeatedly can lead to autopilot behavior, increasing the chance of lapses or complacency.
Examples:
- Forgetting to inspect a component that’s always “fine.”
- Overlooking warning signs because they’re always visible.
Solution: Rotate responsibilities and maintain engagement through variation.
7. Poor Communication
Misunderstandings between team members or unclear instructions can lead to planning mistakes or coordination errors.
Examples:
- Misreading a shift change handover note.
- Confusion over who is responsible for a task.
Solution: Standardize communication protocols and confirm critical information.
8. Stress and Personal Issues
Emotional stress, health problems, or substance use can impair focus, memory, and judgment.
Examples:
- A stressed worker forgets steps in a safety procedure.
- Someone experiencing personal issues may become distracted or error-prone.
Solution: Provide mental health support, flexible work policies, and employee wellness programs.
9. Organizational and Cultural Factors
A company’s safety culture, leadership, and policies influence employees’ performance and response to potential errors.
Examples:
- A culture that punishes errors discourages reporting and learning.
- Inconsistent procedures across departments increase confusion.
Solution: Promote a just culture, prioritize safety, and encourage continuous improvement.
Human error is often a symptom of deeper system issues, not just individual failure. By identifying and addressing the root causes—like poor design, fatigue, distractions, or weak training—organizations can create environments where people are less likely to make errors and more likely to recover from them safely.
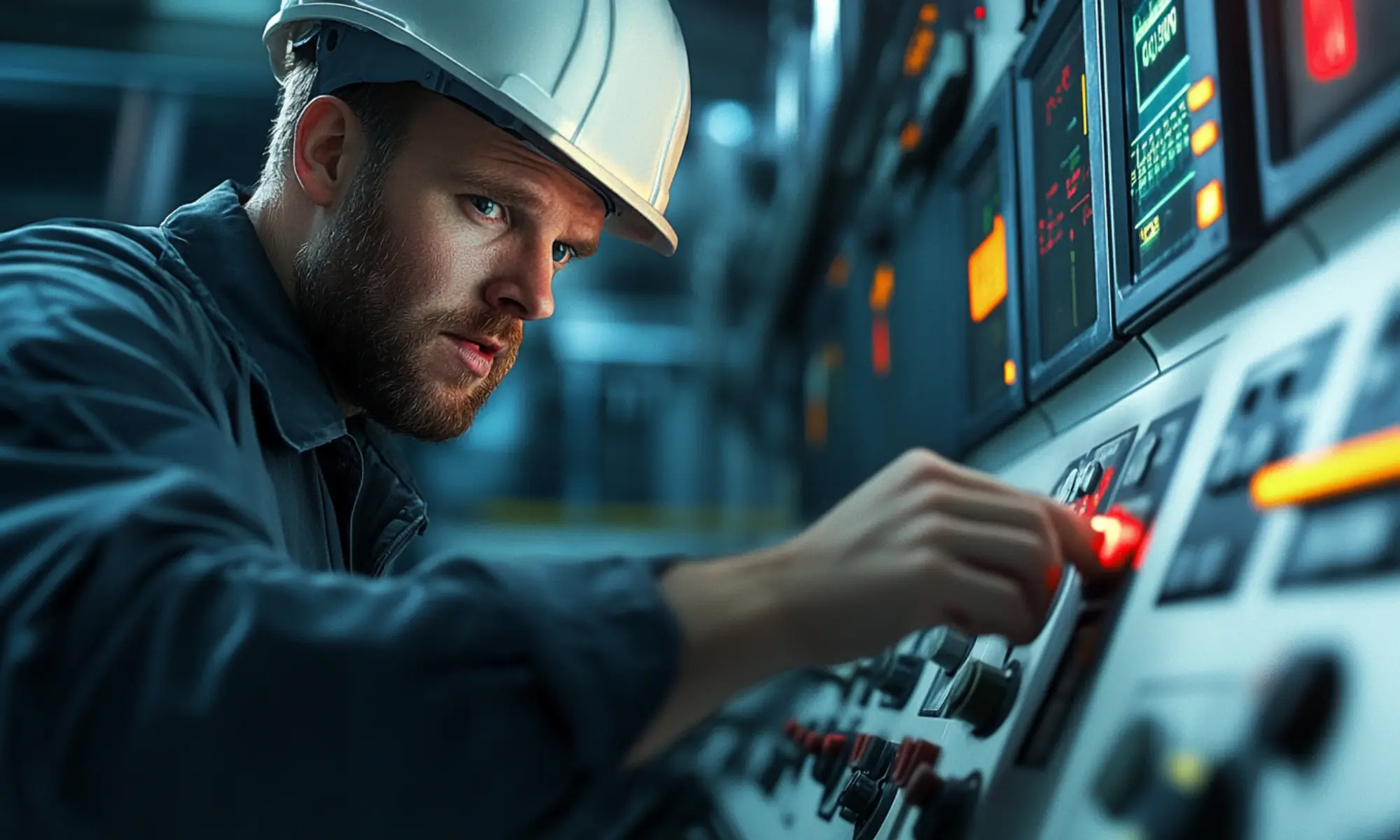
Real-World Examples of Human Error
Understanding how human error occurs in real-life situations helps organizations design better systems and prevent similar failures in the future. These examples span aviation, healthcare, manufacturing, construction, and everyday digital interactions.
1. Aviation: Distraction Leads to Catastrophic Descent
Scenario: During a routine flight, the crew is distracted by troubleshooting a minor technical issue—a faulty warning light. While focusing on that, they fail to monitor the plane’s altitude. The aircraft descends unnoticed and crashes into the terrain.
Type of Error: Slip + Lapse
Cause:
- Attention diverted from critical flight monitoring
- Memory lapse in altitude checks
Lesson:
- Cockpit systems must include better alerting mechanisms.
- Crew resource management (CRM) training is crucial for prioritizing tasks under pressure.
2. Healthcare: Medication Administration Error
Scenario: A nurse administers the wrong dose of medication due to misreading the doctor’s handwriting or misinterpreting dosage guidelines. The patient suffers adverse effects.
Type of Error: Mistake
Cause:
- Misjudgment caused by poor handwriting or ambiguous instructions
- Lack of electronic prescribing systems
Lesson:
- Standardizing prescriptions through digital systems reduces ambiguity.
- Cross-checking medications can prevent administration mistakes.
3. Manufacturing: Incorrect Machine Operation
Scenario: A machine operator intends to press the “Start” button but accidentally hits the adjacent “Emergency Stop” button due to their proximity and similar appearance.
Type of Error: Slip
Cause:
- Poor interface design
- Muscle memory acting on autopilot
Lesson:
- Controls should be color-coded and spaced out to prevent slips.
- Protective covers or confirmation prompts can reduce accidental activations.
4. Construction: Forgotten Safety Lockout
Scenario: A maintenance worker forgets to apply a lockout device before servicing equipment. Another worker, unaware, powers the machine, causing injury.
Type of Error: Lapse
Cause:
- Fatigue and routine familiarity
- Distraction due to nearby activity
Lesson:
- Checklists and step-by-step protocols should be mandatory.
- Visual indicators (e.g., lockout tags) help others recognize a hazard.
5. Space Exploration: Challenger Disaster (1986)
Scenario: Engineers knew about O-ring problems in cold weather, but management misunderstood the risk and proceeded with the launch. The shuttle exploded shortly after takeoff.
Type of Error: Mistake + Latent Error
Cause:
- Planning failure at the organizational level
- Latent errors in safety culture and communication
Lesson:
- Encourage open communication of safety concerns.
- Leadership must make data-informed decisions and respect engineering input.
Human error is not always the result of negligence—it’s often a byproduct of normal human limitations combined with poor system design, inadequate training, or environmental factors. By analyzing these real-world examples:
- We see how slips, lapses, and mistakes play out in practical settings.
- Organizations can develop better training, interface design, process controls, and error-recovery mechanisms.
Ultimately, minimizing human error involves designing systems that support human strengths and compensate for limitations.
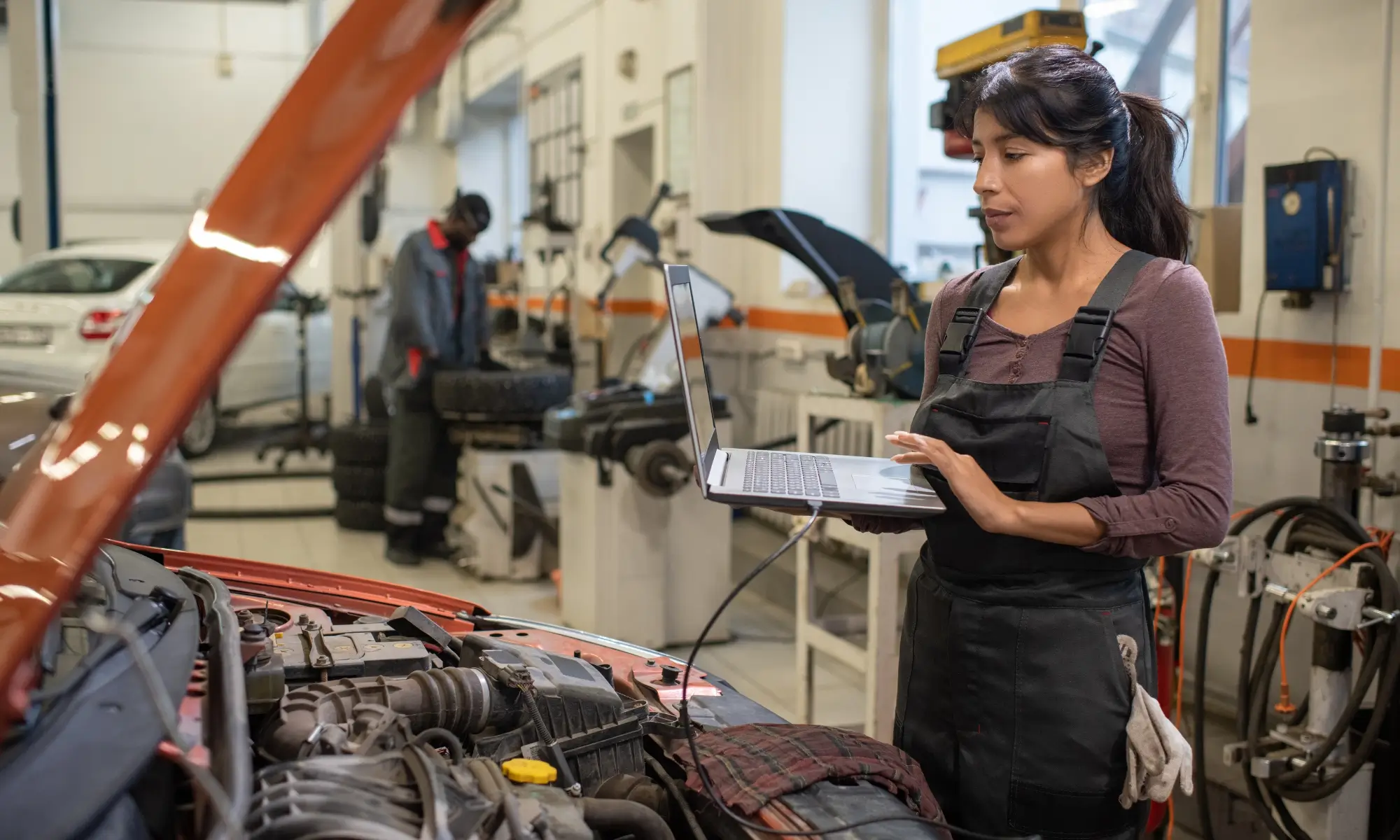
How to Avoid Human Errors
While it’s impossible to eliminate human error completely—because to err is human—we can significantly reduce its frequency and impact through proactive design, smart procedures, and supportive workplace culture. The goal is to design for human limitations and support human strengths. Below are effective strategies to help prevent human error:
1. Improve Training and Knowledge
Proper training is the foundation for safe and correct performance.
- Conduct task-specific training: Ensure employees are trained on what to do and why it matters.
- Use hands-on simulations: Training in realistic scenarios can help solidify correct actions, especially for critical tasks.
- Refresh regularly: Offer periodic re-training to keep knowledge current and reinforce standards.
Example: Flight crews train on simulators to practice emergency protocols before facing real incidents.
2. Design User-Friendly Systems and Tools
Bad design causes good people to make avoidable errors.
- Simplify interfaces: Avoid clutter, and make controls intuitive.
- Use visual cues and feedback: Buttons, labels, icons, and error messages should guide users clearly.
- Enable error recovery: Provide undo options, confirmation prompts, and safe defaults.
Example: Software with a “Confirm Delete” pop-up prevents accidental file loss due to slips.
3. Use Checklists and Standard Operating Procedures (SOPs)
Checklists reduce memory lapses, especially during complex or high-pressure tasks.
- Step-by-step guidance: Ensure all critical steps are documented.
- Easy to access and use: Keep checklists visible and simple.
- Update frequently: Reflect any changes in equipment or procedures.
Example: Surgeons use a “surgical safety checklist” to avoid leaving instruments inside patients.
4. Minimize Fatigue and Distraction
Cognitive overload and tiredness are major causes of slips and lapses.
- Enforce regular breaks, especially for tasks requiring sustained focus.
- Rotate repetitive tasks: To avoid monotony and fatigue.
- Limit multitasking: Let workers concentrate on one task at a time when safety is critical.
Example: Air traffic controllers work in shifts with mandatory breaks to maintain alertness.
5. Encourage a Just Culture
A blame-free environment supports learning from mistakes.
- Report near misses and errors without fear: Encourage early detection and system improvement.
- Focus on system issues, not just individuals.
- Use errors as learning tools: Share case studies and real examples to prevent recurrence.
Example: Hospitals conduct “morbidity and mortality” meetings to learn from errors openly and respectfully.
6. Implement Error-Proofing (Poka-Yoke)
Poka-Yoke is a lean manufacturing concept that designs out the possibility of error.
- Physical constraints: Make incorrect actions physically impossible (e.g., a plug that only fits one way).
- Automation: Use sensors or systems that detect errors before they cause harm.
- Color coding: Differentiate tools or pathways to avoid mix-ups.
Example: A microwave that doesn’t start unless the door is closed properly.
7. Improve Communication and Coordination
Human errors often arise from misunderstandings or missing information.
- Standardize communication: Use structured handovers and check-back techniques.
- Clarify responsibilities: Everyone should know who does what and when.
- Visual aids: Diagrams, floor maps, or signage can prevent navigation and process errors.
Example: Pilots use “readback/hearback” to confirm air traffic instructions in aviation.
8. Maintain and Calibrate Equipment Regularly
Even skilled users make mistakes if tools or systems are unreliable.
- Schedule inspections and servicing.
- Replace outdated equipment.
- Calibrate instruments to ensure accuracy.
Example: A misreading from a faulty gauge could cause a technician to apply incorrect pressure or dosage.
9. Set Realistic Expectations and Deadlines
Time pressure leads to stress, shortcuts, and risk-taking.
- Avoid overloading employees.
- Allow time for thoroughness.
- Balance productivity with safety.
Example: Rushed factory workers may skip final quality checks to meet production quotas, leading to costly recalls.
A well-designed process, smart training, regular feedback, and supportive culture can greatly reduce the risk and impact of human errors.
Conclusion
To err is human, but failing to design systems that account for human error is an avoidable risk. As we’ve explored in this guide, human errors—slips, lapses, or mistakes—are predictable and often symptoms of deeper issues like poor design, unclear procedures, or overwhelming work conditions.
Rather than solely blaming individuals, the focus should be on creating systems, environments, and cultures that support human performance and make it easier to do the right thing—and harder to do the wrong one.
By understanding the types, causes, and real-world consequences of human error, and implementing strategies such as better training, smarter design, and supportive workplace policies, organizations can dramatically reduce the frequency and impact of errors.
Ultimately, managing human error isn’t about striving for perfection—it’s about building resilient systems that recognize human limitations and work with them, not against them.