A clean and well-organized workplace is more than just visually pleasing — it’s essential to safety, productivity, and employee well-being. Workplace housekeeping refers to the ongoing process of maintaining a neat, orderly, and hazard-free work environment. Good housekeeping practices are fundamental to every organization’s health and safety program, whether it’s an office, a warehouse, or a construction site.
In this guide, you’ll learn about the importance of workplace housekeeping, the common hazards caused by poor practices, the different types of housekeeping by area, and the key elements that make up an effective housekeeping program.
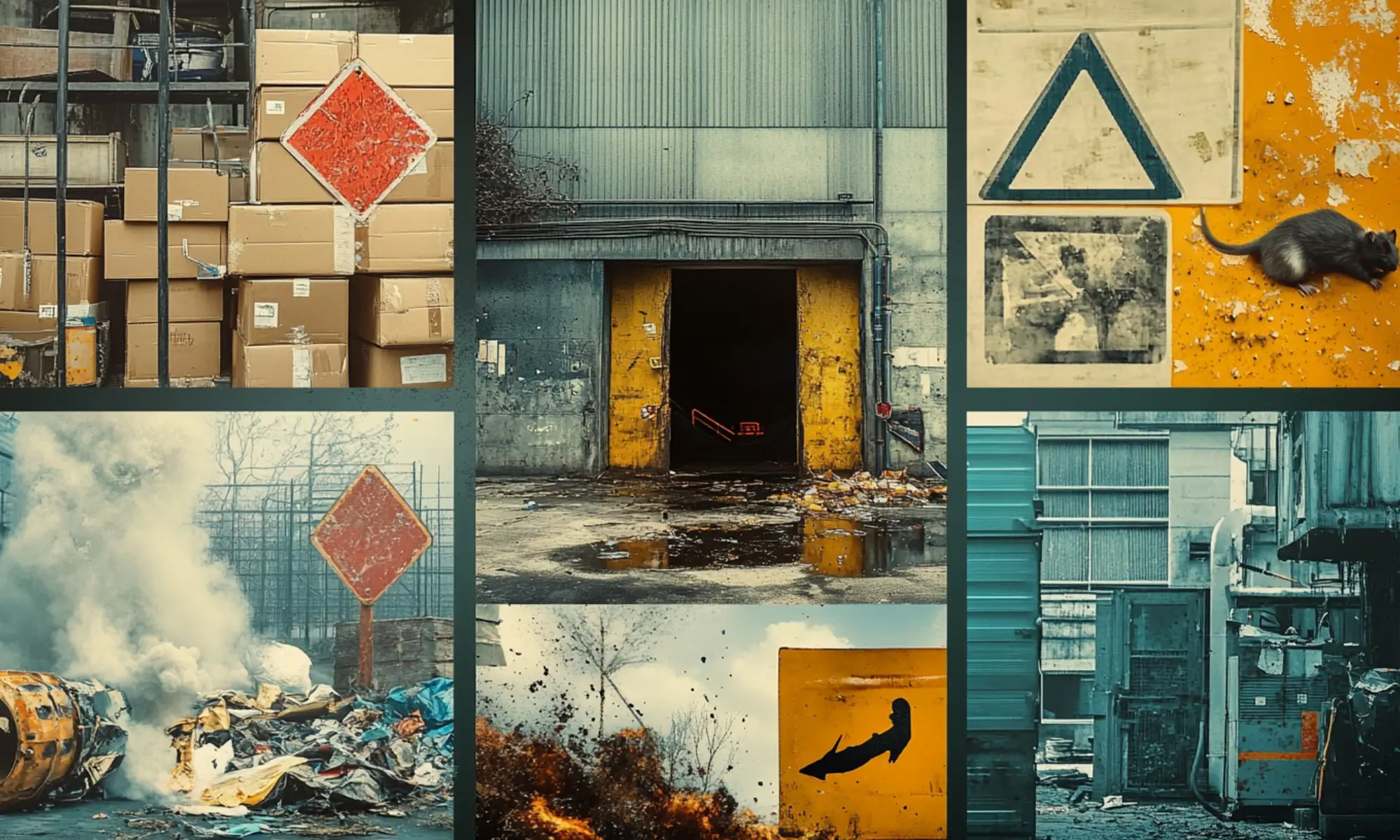
What’s Workplace Housekeeping?
Workplace housekeeping is the continuous process of keeping a work environment clean, organized, and free of hazards to ensure safety, efficiency, and well-being. It goes beyond simple cleaning—it includes the maintenance of floors and surfaces, proper storage of materials, waste disposal, clear marking of walkways, inspection of equipment, and control of hazards such as spills, dust, and clutter.
Workplace housekeeping is a proactive safety practice that helps prevent accidents, supports regulatory compliance, improves morale, and boosts overall productivity. It is a shared responsibility that should be embedded in an organization’s safety culture and operational routines.
Why Workplace Housekeeping Matters
According to OSHA, workplaces must be kept “clean, orderly, and sanitary” to reduce the risk of injuries, illnesses, and environmental hazards. Housekeeping affects everything from employee morale to legal compliance.
When neglected, clutter, spills, and disorganization can lead to:
- Slips, trips, and falls
- Fire outbreaks due to flammable materials
- Injuries from falling or protruding objects
- Exposure to hazardous substances
- Infestations and poor hygiene conditions
But effective housekeeping isn’t just about cleanliness — it’s about proactively preventing hazards and maintaining a safety culture.
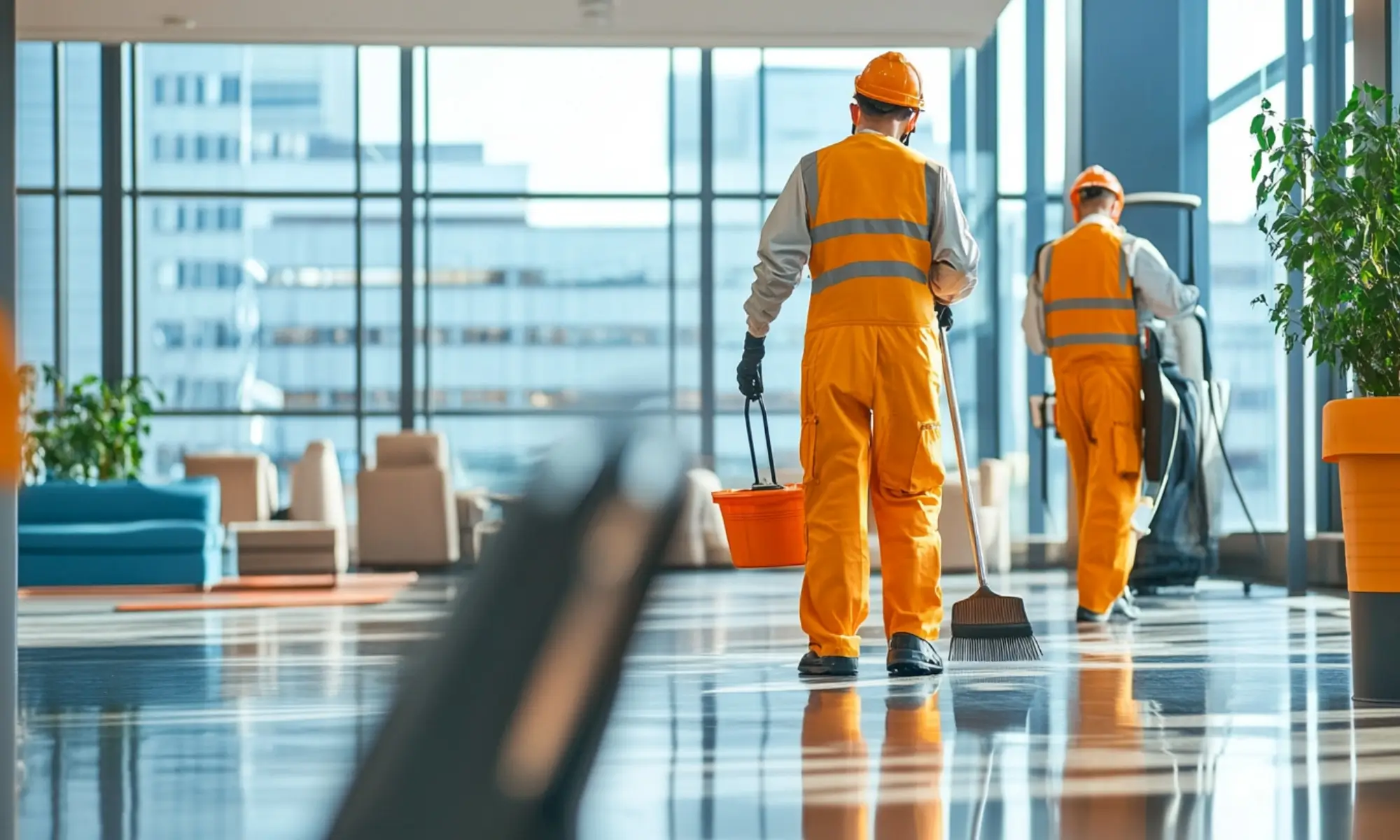
Common Hazards Caused by Poor Housekeeping
Poor workplace housekeeping creates an environment where preventable accidents and health risks can thrive. When walkways are blocked, materials are stored carelessly, and spills or debris are ignored, the potential for injury increases significantly. Below are some of the most common hazards linked to poor housekeeping:
1. Slips, Trips, and Falls
Cluttered aisles, wet floors, loose cables, and uneven surfaces are frequent results of inadequate housekeeping. These can cause employees to slip on spills, trip over misplaced items, or fall due to obstructed paths.
2. Fire Hazards
Allowing combustible materials like paper, cardboard, oily rags, or chemical residues to accumulate increases the risk of fires. Blocked fire exits and improperly stored flammable substances further worsen the danger.
3. Falling Objects
Improperly stacked boxes, tools left on elevated surfaces, or unsecured items on shelves can fall and injure workers below. Poor storage planning often leads to unstable stacks or overloading shelves.
4. Exposure to Hazardous Substances
Dust buildup, leaking chemicals, and poorly ventilated spaces can expose workers to airborne particles, toxic fumes, or skin irritants. This can lead to respiratory issues, allergic reactions, or chemical burns.
5. Cuts and Punctures
Sharp objects like nails, broken glass, metal scraps, or tools left lying around can easily cause cuts or puncture wounds. These are especially dangerous if sanitation is poor and the risk of infection is high.
6. Blocked Emergency Exits and Equipment
When clutter blocks access to fire extinguishers, eyewash stations, first aid kits, or emergency exits, critical response time is delayed in emergencies, putting lives at greater risk.
7. Pest Infestations and Mold Growth
Neglected trash, food waste, and dirty areas attract pests like rodents and insects. Damp conditions can lead to mold, which affects indoor air quality and can cause health issues.
In summary, poor housekeeping not only makes a workplace look unprofessional, but it also actively increases the risk of injury, illness, fire, and legal liability. Effective housekeeping is a key preventive measure and a cornerstone of a strong safety culture.
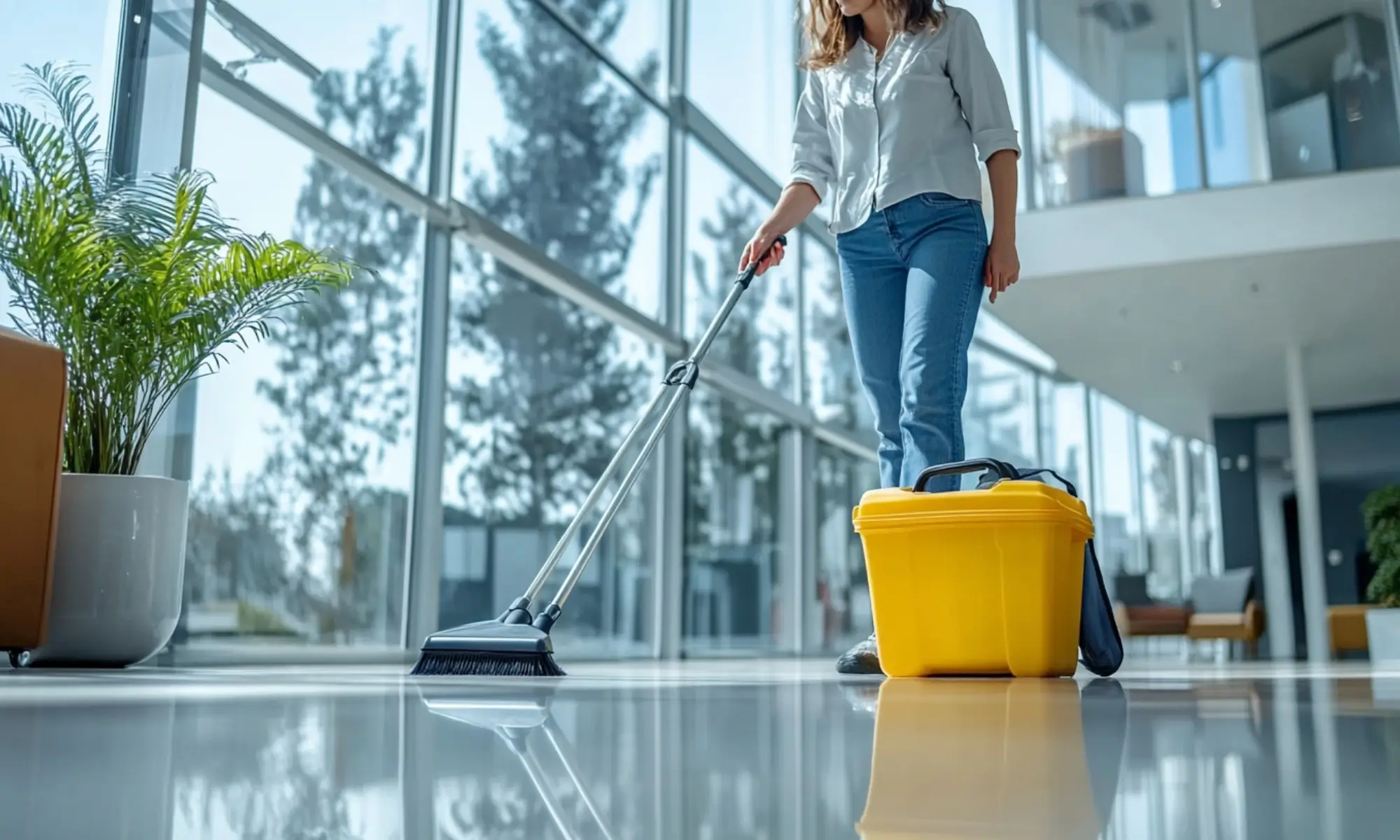
Types of Housekeeping by Work Area
Workplace housekeeping isn’t one-size-fits-all. Each area has unique needs and challenges:
1. Office Spaces
- Clear clutter from desks
- Proper cable management
- Regular trash removal
- Accessible fire exits and walkways
2. Warehouses and Industrial Facilities
- Regularly sweep and mop floors
- Mark pathways and aisles clearly
- Store heavy items on lower shelves
- Keep fire exits, sprinklers, and panels unobstructed
3. Construction Sites
- Remove debris and materials daily
- Secure tools and equipment
- Mark hazardous zones clearly
- Regularly inspect scaffolding and ladders
4. Laboratories and Chemical Storage Areas
- Label and segregate chemicals
- Maintain spill control kits
- Provide proper PPE and hygiene facilities
- Use appropriate ventilation and exhaust systems
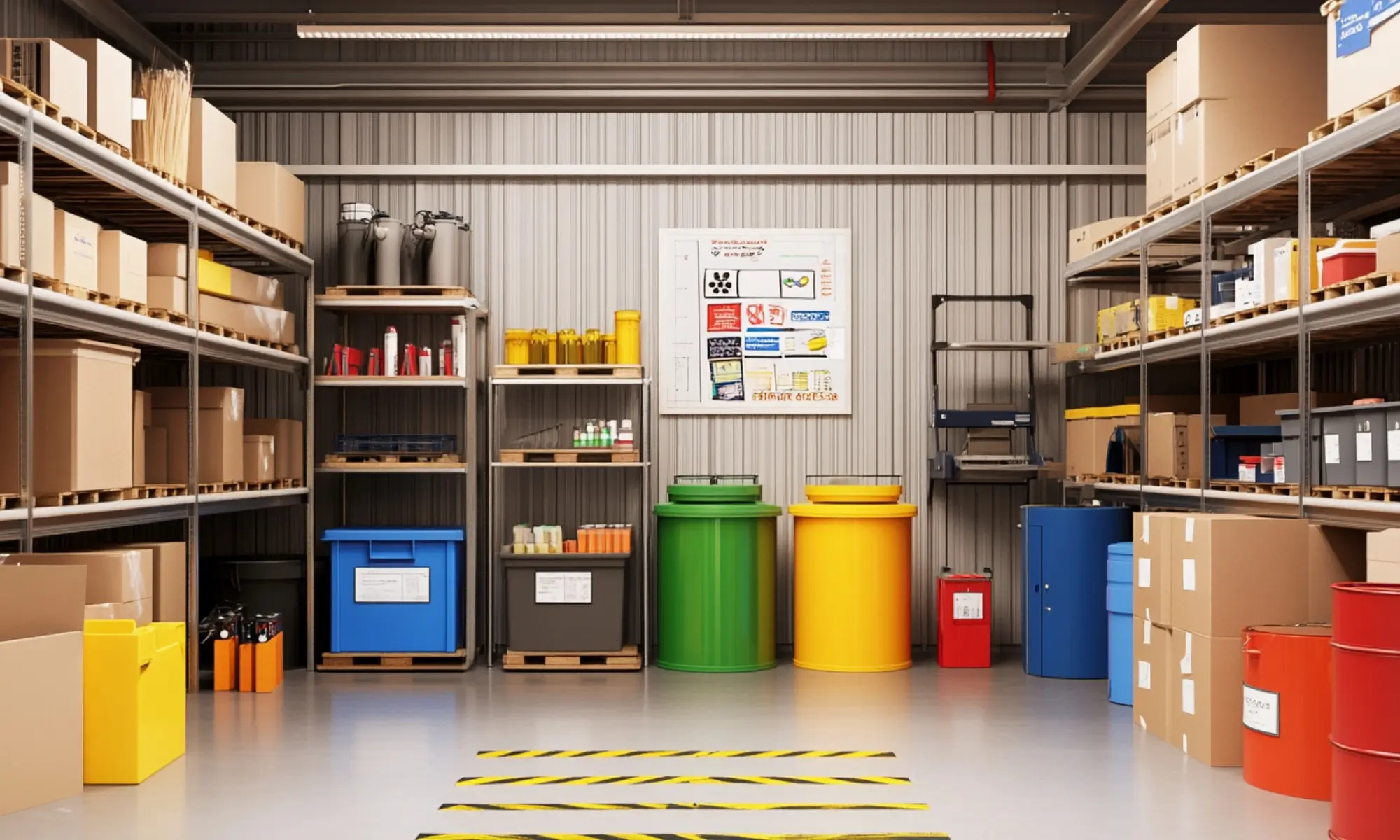
Key Elements of an Effective Housekeeping Program
Housekeeping is more than just cleaning up—it’s a structured, strategic process to prevent hazards, improve efficiency, and foster a strong safety culture. A well-executed housekeeping program should be planned, consistent, and integrated into daily operations across all departments. Here’s a breakdown of each key element:
1. Maintenance of Buildings and Equipment
A clean environment isn’t safe if equipment and facilities are in disrepair. Broken flooring, malfunctioning machinery, or damaged lighting pose immediate safety threats.
Best practices:
- Schedule regular inspections of the physical structure (walls, ceilings, windows, floors).
- Repair damaged floors, stairs, handrails, doors, and plumbing promptly.
- Ensure that safety-critical systems like alarms, lighting, ventilation, and fire suppression are operational.
- Implement preventive maintenance for machinery and tools to reduce breakdowns and hazards.
2. Dust and Dirt Control
Accumulated dust is more than a cleanliness issue—it can contribute to respiratory hazards, product contamination, and even combustible dust explosions in certain industries.
Best practices:
- Use industrial vacuum systems, especially HEPA-filter models, for fine dust and hazardous particles.
- Avoid dry sweeping, which can stir up particles—opt for damp mops or sweeping compounds.
- Regularly clean surfaces that are often neglected (ceilings, light fixtures, shelves).
- Maintain and clean air filters, ductwork, and exhaust systems to prevent buildup.
3. Spill Control
Slips, chemical exposure, and environmental damage can all result from unmanaged spills.
Best practices:
- Clean spills immediately using appropriate absorbent materials or spill kits.
- Post warning signs around wet areas to prevent slip incidents.
- Place drip pans or containment trays under machinery prone to leaking.
- Train employees on how to report and clean up spills safely.
4. Organized Storage
Improper storage leads to falls, injuries from falling objects, blocked emergency exits, and inefficiencies in workflow.
Best practices:
- Store items in designated areas with clear labeling.
- Keep heavy materials on lower shelves to prevent strain or tip-overs.
- Avoid stacking materials near sprinklers or blocking fire exits.
- Secure items on shelves and ensure that materials are cross-tied or braced if needed.
5. Waste Disposal
Accumulated waste can lead to fires, pest infestations, injuries, and reduced morale.
Best practices:
- Use clearly labeled containers for general waste, recyclables, and hazardous materials.
- Place bins near workstations to encourage regular use.
- Empty trash regularly to prevent overflow or fire risk.
- Segregate combustible, chemical, and sharps waste following local regulations.
6. Clear Walkways and Aisles
Obstructed walkways are a leading cause of trips, falls, and delays during emergencies.
Best practices:
- Keep floors and passageways free of tools, cords, debris, and loose materials.
- Mark pedestrian walkways, vehicle lanes, and restricted zones with high-visibility striping.
- Use mirrors or signs in blind spots.
- Ensure aisles are wide enough for both foot and vehicle traffic, especially in warehouses.
7. Clean and Functional Employee Facilities
Sanitary facilities reduce the spread of illness and improve overall workplace hygiene and morale.
Best practices:
- Clean restrooms, break rooms, and locker areas at least once per shift.
- Provide hygiene supplies like soap, paper towels, and hand sanitizer.
- In environments with hazardous materials, ensure showers and changing areas are available and maintained.
- Separate eating areas from work zones, especially where chemicals or biological hazards are present.
8. PPE and Tool Management
Damaged or missing PPE and poorly maintained tools can result in accidents and non-compliance with safety regulations.
Best practices:
- Assign storage locations for tools with labels or outlines.
- Inspect tools regularly for damage or wear and take faulty items out of service.
- Clean PPE after use and store it in a sanitary location.
- Replace worn or expired PPE promptly and keep backup stock.
9. Employee Training and Engagement
Housekeeping is a team effort. Everyone must understand their role in maintaining cleanliness and safety.
Best practices:
- Train all staff on housekeeping standards during onboarding and refresher sessions.
- Assign housekeeping tasks by department, role, or shift.
- Encourage a “clean as you go” culture to prevent accumulation.
- Empower employees to report unsafe conditions or violations without fear of reprisal.
10. Monitoring, Inspections, and Continuous Improvement
Without regular checks, even the best housekeeping plans can fall apart. Inspections reveal gaps and areas for improvement.
Best practices:
- Use area-specific inspection checklists for consistency.
- Schedule daily or weekly walkthroughs by supervisors.
- Record findings, take corrective actions, and track trends over time.
- Set clear goals (e.g., 100% clear emergency exits, zero slip hazards) and audit performance against them.
An effective housekeeping program is not an occasional clean-up—it’s a core operational strategy. When well-executed, it boosts morale, prevents injuries, enhances compliance, and promotes a safety culture across the organization.
Employers should integrate housekeeping into their overall health and safety management system and ensure all employees are involved, accountable, and empowered to contribute.
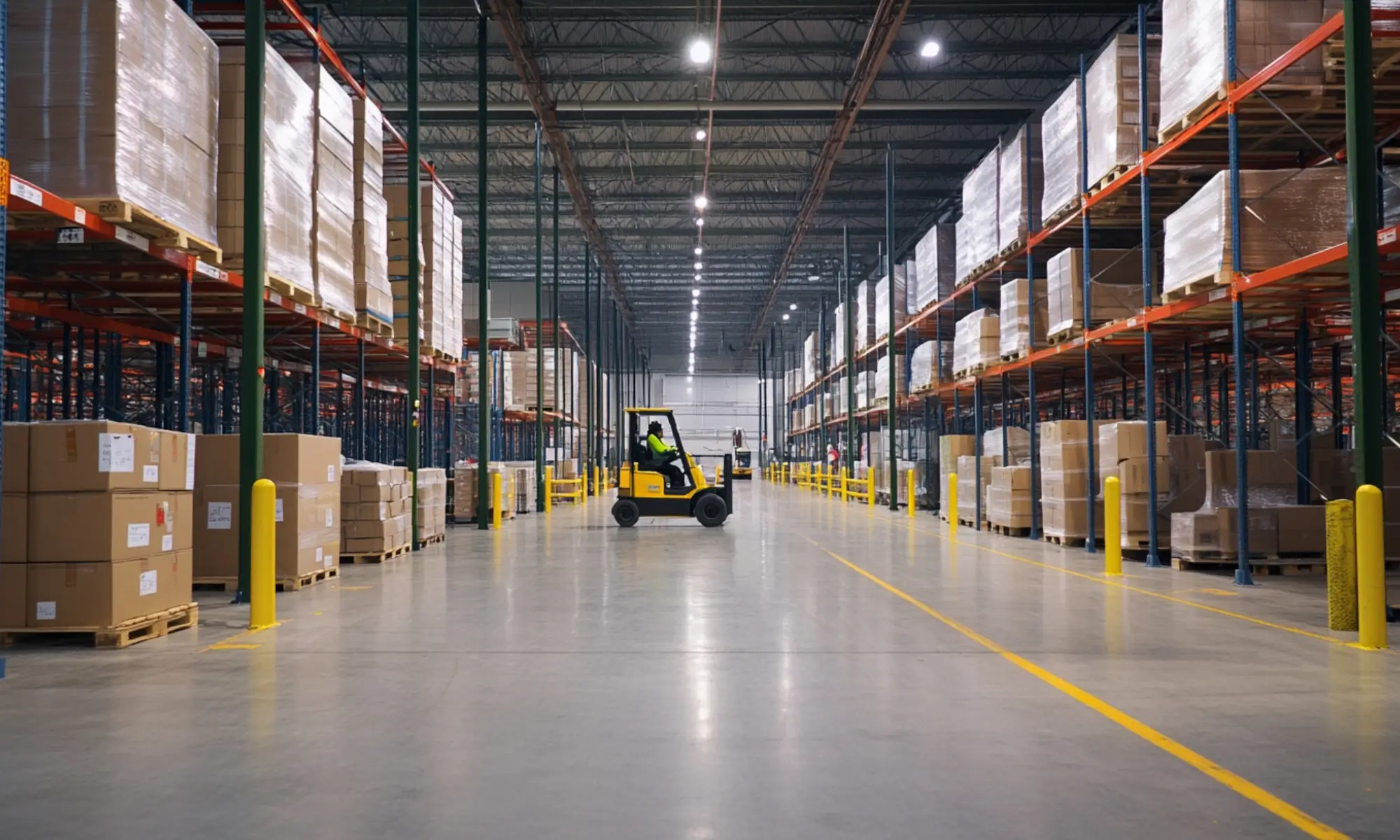
Best Practices for Sustaining Good Housekeeping
Maintaining a clean and organized workplace isn’t a one-time effort — it requires a proactive and consistent approach. Good housekeeping should be embedded in your company culture and integrated into daily operations. Here are the best practices for sustaining long-term workplace housekeeping:
- Clean as You Go Policy: Encourage employees to tidy their workstations immediately after completing tasks to prevent the accumulation of clutter and hazards.
- Assign Clear Responsibilities: Each team or department should have designated housekeeping duties with specific individuals accountable for regular cleaning tasks.
- Set a Cleaning Schedule: Daily – empty bins, wipe down surfaces, clean spills; Weekly – organize storage, inspect tools; Monthly – deep clean machinery and ventilation.
- Conduct Regular Inspections: Use a housekeeping checklist for daily or weekly audits. Note any issues, assign follow-ups, and track corrective actions to closure.
- Provide Adequate Storage: Ensure there are enough labeled shelves, racks, and bins to keep materials and tools off the floor and in their proper places.
- Train Employees on Housekeeping: Include housekeeping expectations in onboarding. Offer refresher training and toolbox talks focusing on common problems like spill response or tool misplacement.
- Encourage Hazard Reporting: Provide a simple way for employees to report unsafe conditions, such as blocked exits, broken lights, or unattended spills.
- Use Visual Aids and Signage: Mark aisles, storage zones, and hazardous areas with bright tape and signs. Post reminders near spill kits, PPE stations, and waste bins.
- Monitor and Improve: Keep records of inspections and improvements. Set housekeeping goals and review them regularly during safety meetings.
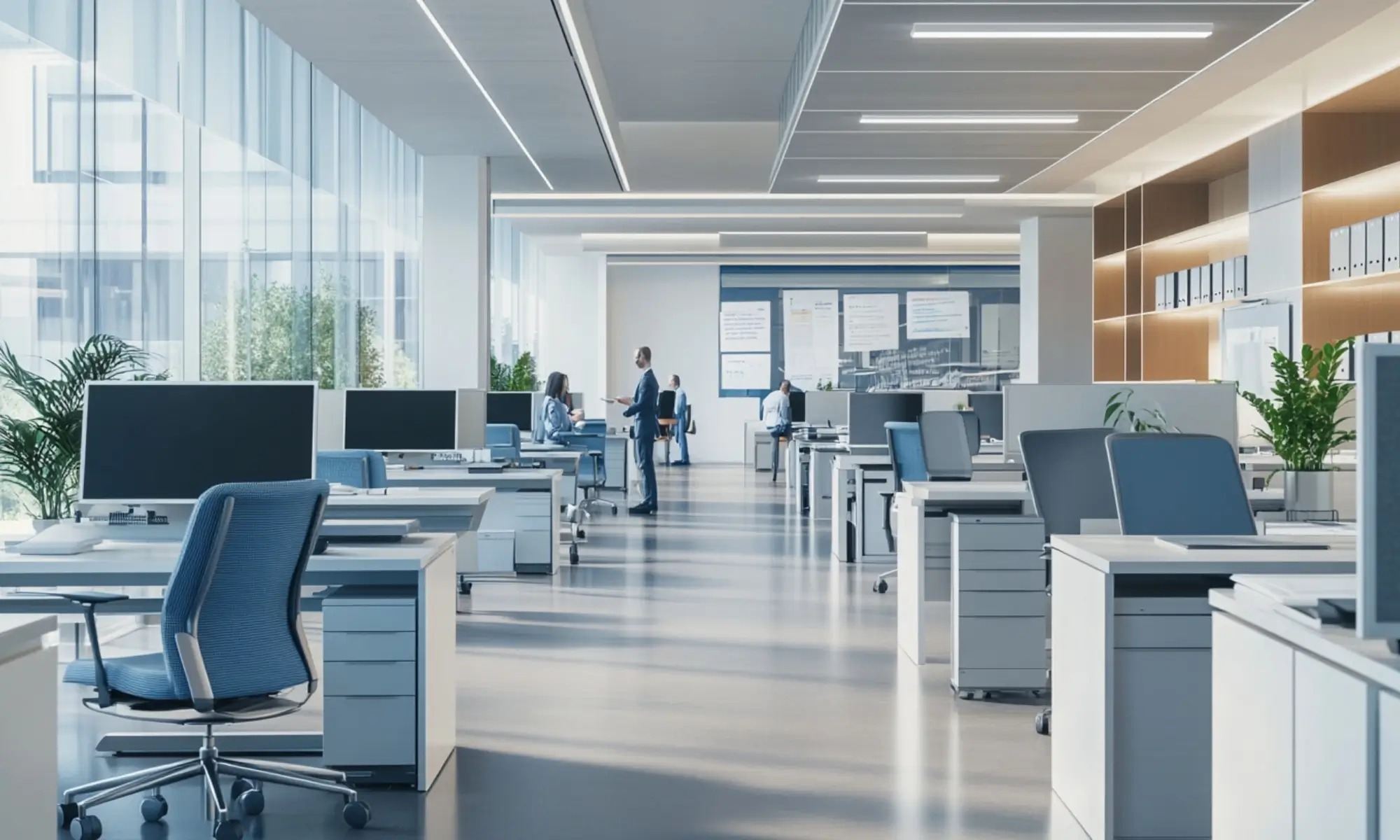
Legal Compliance and Safety Culture in Workplace Housekeeping
Workplace housekeeping isn’t just a matter of cleanliness—it’s a legal requirement and reflects an organization’s commitment to safety. Effective housekeeping supports regulatory compliance and a strong safety culture, which are essential for minimizing risks, avoiding fines, and building trust with employees.
Legal Compliance
Workplace housekeeping is mandated under various safety regulations worldwide. In the U.S., for example, OSHA’s General Industry Standard 1910.22 requires that all places of employment be kept “clean, orderly, and in a sanitary condition.”
Key compliance points include:
- Safe walking and working surfaces must be maintained to prevent slips, trips, and falls.
- Combustible materials must be controlled and disposed of to reduce fire hazards.
- Emergency exits, fire extinguishers, and electrical panels must remain accessible and unobstructed.
- Hazardous substances must be stored, labeled, and disposed of properly to protect workers and the environment.
Failure to comply with these standards can lead to fines, legal action, injury claims, and even criminal liability in severe cases.
Safety Culture
Beyond legal requirements, good housekeeping is a visible and practical way to demonstrate a company’s safety values. It communicates that the organization prioritizes health, order, and the prevention of accidents, not just because the law requires it, but because it genuinely cares about its people.
A strong safety culture benefits the workplace by:
- Improving morale: Workers feel respected and protected in a clean, organized environment.
- Encouraging ownership: Employees are more likely to maintain standards when leadership actively supports safety efforts.
- Reducing incidents: Well-maintained spaces reduce hazards, which lowers the frequency of injuries and near misses.
- Reinforcing accountability: When housekeeping is part of every employee’s responsibility, it fosters shared ownership of workplace safety.
Legal compliance ensures that organizations meet minimum safety requirements. But it’s the integration of housekeeping into the daily routine—and the mindset of both leaders and employees—that builds a true safety culture. Together, they form the foundation of a productive, healthy, and legally compliant work environment.
Final Takeaways
Workplace housekeeping isn’t just about appearance — it’s about preventing injuries, reducing risks, and supporting productivity. Whether you manage a warehouse, office, or job site, a robust housekeeping program can transform your work environment and safety outcomes.
Remember:
- Cluttered workspaces are dangerous workspaces.
- Routine, not reaction, leads to safer environments.
- Housekeeping is everyone’s responsibility.